Технология восстановления плунжерных пар топливного насоса высокого давления методом электрохимикомеханической обработки
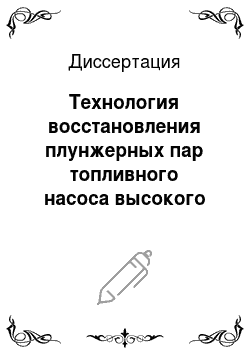
Диссертация
Основной путь повышения долговечности дизелей при ремонтесовершенствование существующих и применение новых технологических процессов восстановления деталей. Необходимо отметить, что ведущим видом изнашивания большинства деталей дизеля является абразивное изнашивание. Это, в первую очередь, относится к плунжерным парам топливной аппаратуры. Трение и износ деталей топливной аппаратуры, происходят… Читать ещё >
Список литературы
- Гусейнов А.Г. Повышение работоспособности деталей машин и аппаратуры путем восстановления и упрочнения диффузионной металлизацией : Дис. д-ра техн. наук: 05.02.08: Москва, 2002 339 с. РГБ ОД, 71:04−5/98-Х
- Болдырев А. И. Комбинированная электрохимикомеханическая обработка деталей авиационно-космической техники.// Известия Самарского научного центра Российской академии наук, т. 13, № 1(2), 2011.-293−296 с.
- Макаренко Н.Г. Электрохимико-механическое повышение эксплуатационных свойств трибосистем.-ОмскЮмский научный вестник, 2 004 254 с.
- Бурумкулов Ф.Х., Гольдина М. Б. Оценка показателей безотказности восстанавливаемых объектов по результатам эксплуатации или испытаний. -М.: Изд-во стандартов, 1977. 36 с.
- Некоторые положения теории надежности и долговечности ремонтируемых машин. Сб. науч. труд, под ред И.Н. Величкина- НАТИ, вып.209. М. — 1970, С.5−32.
- Надежность технических систем. Справочник. Под ред. И. А. Ушакова. М, Радио и связь, 1985, 606 с.
- Погудин Е.В., Георгиевский О. Н., Гаврилов А. Н. Закономерности процесса обеспечения надежности техники на этапах жизненного цикла // Надежность и контроль качества. — 1998. — № 1, С.3−15.
- Решетов Д.Н. и др. Надежность машин / A.C. Иванов., В.З. Фадеев- под ред. Д. Н. Решетова. М.: Выс. школа, 1988. — 238 с.
- К проблеме изнашивания прецизионных деталей. Повышение надежности дизельной топливной аппаратуры. Сб. науч. труд, под ред В.В. Антипова- СИМСХ, вып. 89. Саратов, 1977. — С.3−7.
- Бугаев В.Н. Ремонт форсированных тракторных двигателей. М.: Колос, 1978.-127 с.
- Бугаев В.Н. Эксплуатация и ремонт форсированных тракторных двигателей. М.: Колос, 1981. — 208 с.
- Бугаев В.Н., Гусейнов, А .Г., Павлов В. А., Лемешова Ю. К. Восстановление плунжерных пар топливных насосов // Техника в с.х. — 1987. — № 12.-С. 46−47.
- Бугаев В.Н., Гусейнов А. Г., Павлов В. А., Лемешова Ю. К. Восстановление плунжерных пар топливных насосов // Техника в с.х. 1987. — № 12. — С. 46−47.
- Гусейнов А.Г. Анализ прогиба плунжеров топливного насоса УТН-5 в процессе диффузионной металлизации. // Ремонт и надежность сельскохозяйственной техники. Сб. науч. труд. / МИИСП. М. — 1985. — с.14−15.
- Гусейнов А.Г. Восстановление и упрочнение прецизионных деталей диффузионным борохромоникелированием // Материалы докладов международной научно-технической конференции «Проблемы машиностроения на пороге XXI века» 30−31 мая 200 г. Баку. — 2000, С. 130 132.
- Гусейнов А.Г. Восстановление и упрочнение деталей машин диффузионным титанированием // Вестник машиностроения. 2000. — № 9. — с.43−45.
- Исследовать надежность и долговечность топливных насосов НД-21/2 и НД-21/4 при ускоренных испытаниях и в условиях реальной эксплуатации: Научн. Отчет / ВИСИ. № ГР 1 820 084 743. — Вильнюс, 1983. — 131с.
- Костецкий Б.И., Протопопов Б. В., Шепельский В. А., Кондратюк Ю. А. Износ плунжерных пар насосов // Механизация и электрификация с.-х. — 1973. — № 12.-С. 35−36.
- Бахтияров Н.И., Логинов В. Е. Производство и эксплуатация прецизионных пар. М.: Машиностроение, 1979. — 205 с.
- Петкова Д.Д. Повышение безотказности прецизионных плунжерных пар: Автореф. диссерт. на соиск. канд. техн. наук. Киев, 1978. — 17 с.
- Гусейнов А.Г. Восстановление плунжерных пар топливного насоса УТН-5 парофазным диффузионным хромированием в вакууме с последующей механической обработкой: Диссерт. на соиск. канд. техн. наук. М.: 1987. — 260 с.
- Антипов В. В и др. Ремонт и регулирование топливной аппаратуры двигателей тракторов и комбайнов / В. В. Антипов, Б. А. Гоголев, Б. П. Загородских. — М.: Россельхозиздат, 1978. 126 с.
- Свиридов Ю.Б. Фирменный ремонт топливной аппаратуры (принципы организации, накопленный опыт, перспективы реализации). JL: ЦНИТА, 1981. -11с.
- Прилепин В.А. Повышение надежности поршневых топливоподкачивающих насосов дизелей восстановлением и упрочнением деталей диффузионным хромированием: Автореф. диссерт. на соиск. канд. техн. наук. М.: 1991. — 16 с.
- Вильнюсский завод топливной аппаратуры. Отчет 8/855−86. — ВЗТА. -Вильнюс, 1986. 15 с.
- Елизаветин М.А., Сатель Э. А. Триботехнические способы повышения долговечности машин. -М.: Машиностроение, 1969. 400 с.
- Майоров К.П. Исследование работоспособности топливных пар топливной аппаратуры распределительного типа: Автореф. диссерт. На соиск. канд. техн. наук. Саратов, 1977. — 24 с.
- Нагорских В.Ф. Влияние режимов ускоренной обкатки и смазочной среды на качество приработки и последующую работоспособность топливного насоса: Автореф. диссерт. на соиск. канд. техн. наук. ЧИМЭСХ, 1980. — 18 с.
- Садыхов АИ., Гусейнов А. Г., Мусаев Я. Б. Повышение износостойкости деталей машин диффузионным титанированием // Материалы докладов 43-йнаучно-технической конференции. Баку, 1995. — С.71−73.
- Садыхов А.И., Гусейнов А. Г. Повышение износостойкости деталей плунжерных пар диффузионным хромированием в вакууме // Вестник машиностроения. М.: 1992. — № 8−9. — С.48−52
- Дацко А.И. Исследование влияния конструктивного формирования рабочей поверхности плунжера на работоспособность топливного насоса высокого давления: Автореф. диссерт. на соиск. канд. техн. наук. Л.: 1979. -20 с.
- К проблеме изнашивания прецизионных деталей. Повышение надежности дизельной топливной аппаратуры. Сб. науч. труд, под ред В.В. Антипова- СИМСХ, вып. 89. Саратов, 1977. — С.3−7.
- Хрущев М.М., Бабичев М. А. Абразивное изнашивание. М.: Наука, 1970.-252 с.
- Костецкий Б.И., Колениченко Н. В. Качество поверхности и трение в машинах. Киев: Техника, 1965. — 479 с.
- Костецкий В.Н. Трение, смазка и износ в машинах. Киев: Техника, 1970.-396 с.
- Костецкий В.Н. и др.Надежность и долговечность машин / В. Н. Костецкий, И. Г. Носовский, Л. М. Бершадский, А. К. Караулов. Киев: Техника, 1975.-408 с.
- Гусейнов А.Г. Восстановление и упрочнение прецизионных деталей машин и аппаратуры диффузионной металлизацией. М.: Союз, 1999. — 194 с.
- Галин Л.А. Контактные задачи теории упругости при наличии износа. Прикладная математика и механика. 1976. т.40. — № 6. — С.981−989.
- Дроздов Ю.Н. и др. Трение и износ в экстремальных условиях / Ю. Н. Дроздов, В. Г. Павлов, В. Н. Пучков. М.: Машиностроение, 1986. — 224 с.
- Федотов Г. В., Левин Г. И. Топливные системы тепловозных дизелей. Ремонт, испытание, совершенствование. М.: Транспорт, 1983. — 192 с.
- Филоненко Н.С. Термокинетика фазовых превращений при электромеханической обработке. //Диффузионные процессы в металлах. Тула: ТПИ, 1975. Вып.З. С. 131−135.
- Аскинази Б.М. Упрочнение и восстановление деталей машин электромеханической обработкой. Л.: Машиностроение, 1989. 200 с.
- Петров Ю.Н. Ремонт автотракторных деталей гальваническими покрытиями/Ю.Н.Петров.- Кишинев: Картя молдовеняскэ, 1976−149с.
- Лобанов С.А. Практические советы гальванику/ С. А. Лобанов. — Л. Машиностроение, 1983 .-248 с.
- Молчанов В.Ф. Хромирование в саморегулирующихся электролитах /В.Ф.Молчанов. Киев: Техника, 1972.-155 с.
- Справочник по гальванотехнике/ под ред. В. И. Лайнера .-М.: Металлургия, 1967.-586 с.
- Суслов, А.Г. Направления дальнейшего развития технологии машиностроения / А. Г. Суслов // Справочник. Инженерный журнал. 2010. № 1. С.3−6.
- Смоленцев, В.П. Технология электрических методов обработки / В. П. Смоленцев, A.B. Кузовкин, А. И. Болдырев и др. Воронеж: ВГУ, 2001. 310 с.
- Смоленцев, В. П. Комбинированные методы обработки / В. П. Смоленцев, А. И. Болдырев, A.B. Кузовкин и др. Воронеж: ВГТУ, 1996. 168 с.
- Баширов P.M. и др. Надежность топливной аппаратуры тракторных и комбайновых дизелей / P.M. Баширов, В. Г. Кислов, В. А. Павлов, В. Я. Попов. -М.: Машиностроение. 1978. — 184 с.
- Крагельский И.В. Трение и износ. — 2-е изд. М.: Машиностроение, 1968.-480 с.
- Файнлейб Б. Н. Топливная аппаратура автотракторных дизелей: Справочник. — 2-е изд., перераб. и доп. — Л.: Машиностроение. Ленингр. отд-ние. 1990. — 352 С. ISBN 5−217−911-Х
- Наставление по войсковому ремонту об. 172/Воениздат. М. 1985.
- Термодинамика. Основные понятия. Терминология. Буквенные обозначения величин/ АН СССР, комитет по научно-технический терминологии- отв. редактор выпуска чл.-кор. АН СССР И. И. Новиков. М.: Наука, 1984.-40 с.
- Черепин В.Т., Майфет Ю. П. Локальный анализ концентрационных распределителей элементов в твердых телах методами масс-спектральной микроскопии. Киев: АН УССР, ИМФ, 1971. — 31с.
- Уплотнения и уплотнительная техника: Справочник/ Л. А. Кондаков, А. И. Голубев, В. Б. Овандер и др.- под общ. ред. А. И. Голубева, Л. А. Кондакова. -М.: Машиностроение, 1986. -464 с.
- Орлов П.И. Основы конструирования: Справочно-методическое пособие. Книга 1. -М.: Машиностроение, 1977. 624 с.
- Трение, изнашивание и смазка: Справочник. В 2-х кн.: Кн.2./ Под ред. И. В. Крагельского и В. В. Алисина. М.: Машиностроение, 1979. — 358 с.
- Бурдун Г. Д., Базакуца В. А. Единицы физических величин. Харьков: Вища школа, 1984. — 208 с.
- Костецкий Б.И. Разрушение металлов при трении скольжения в связи с типом их кристаллической решетки / Б. И. Костецкий, Ю. П. Дьяченко, Ю. И. Артемьев // Проблемы трения и изнашивания. Киев: Техника. — 1973. — № 4. — С. 64.
- Владимиров B.C. Уравнения математической физики. М.: Наука, 1971.-512 с.
- Носовский И.Г. Влияние газовой среды на износ металлов. Киев: Техника, 1968.-180 с.
- Макаренко Н.Г., Макаренко А. Н., Доровских Е.В. Технологияформирования поверхностного слоя деталей с заданными свойствами
- Сборник докладов научно-практической конференции «Инновационныепроекты, новые технологии и изобретения». 27 -28 октября 2005 г.
- Экспериментальное кольцо ВНИИЖТ, Щербинка. С. 164−165.
- Гурвич И.Б. Эксплуатационная надежность автомобильных двигателей./И.Б. Гурвич, П. Э. Сыркин.-М.:Транспорт, 1984.-141 с.
- Старосельский А. А. Долговечность трущихся деталей машин./А.А.Старосельский, Д. Н. Гаркунов.-М.:Машиностроение, 1967.394 с.
- В.М. Александров. Контактные задачи теории упругости для неоднородных сред /С.М. Айзикович, В. М. Александров, А. В. Белоконь, Л. И. Кренев, И.С. Трубчих- М.:Физматлит, 2006. 240 е./
- Тененбаум М.М. Износостойкость конструкционных материалов и деталей машин при абразивном изнашивании. М., Машиностроение, 1966,331 с.
- Крагельский И.В., Добычин М. Н., Комбалов B.C. Основы расчетов на трение и износ. М., Машиностроение, 1977, 526 с.
- Андрейкин А.Е., Чернец М. В. Оценка контактного взаимодействия трущихся деталей машин. Киев, Наукова думка, 1991,154 с.
- Brill-Edwards Н., Epner М. «Electrochemical Technology», 1968, v. 6, N 9- 10, p. 299−306.
- Crom-Kohlenstoff- Zeitschrift fur Metallkunde, 1967, v.58, N8, s.560−564
- Крагельский И.В., Михин H.M. Узлы трения машин. Справочник. М., Машиностроение, 1984, 280 с.
- Хрущев М.М., Бабичев М. А. Абразивное изнашивание. М., Наука, 1970, 252 с
- Хрущев М.М., Бабичев М. А. Закономерности царапания и шлифования закрепленными абразивными зернами, при малой скорости. Высокопроизводительное шлифование. М., АН СССР, 1962, с. 18−21.
- Икрамов У.А., Макхамов К. Х. Расчет и прогнозирование абразивного износа. Ташкент, Фан, 1982, 148 с
- ИкрамовУ.А. Расчетные методы абразивного износа. М., Машиностроение, 1978, 287 с.
- Крагельский И В. Трение и износ. М., Машиностроение, 1968, 480 с.
- Крагельский И.В., Михин Н. М. Узлы трения машин. Справочник. М., Машиностроение, 1984, 280 с.
- Мюрретий И., Моттон К. Механизм абразивного изнашивания. Проблемы трения и смазки. М., Машиностроение, 1977, 526 с.
- Галин Л.А., Горячева И. Г. Осесимметричная контактная задача теории упругости при наличии износа. Прикладная математика и механика, 1977, т.41, № 5, с.807−812.
- КрагельскийИ.В., Добычин М. Н., Комбалов В. С. Основы расчетов на трение и износ. М., Машиностроение, 1977, 526 с.
- Галин Л.А. Контактные задачи теории упругости и вязкоупругостью. М., Наука, 1980, 304 с.
- Левина З.М., Решетов Д. Н. Контактная жесткость машин. М., Машиностроение, 1971, 264 с.
- Митрофанов Б.П. Осесимметричная контактная задача для упругого тела с поверхностным слоем. Тезисы докладов Всесоюзного научно-технического семинара по контактной жесткости в машиностроении. Тбилиси, НТО Машпром ГССР, 1974, с.101−103.
- Кутяков В.И. Исследование процесса доводки поверхностей. Автореф. диссерт. на соиск. канд.техн. наук, Одесса, 1971, 19 с.
- Галин JI.A., Горячева И. Г. Осесимметричная контактная задача теории упругости при наличии износа. Прикладная математика и механика, 1977, т.41, № 5, с.807−812.
- Демкин Н.Б. Контактирование шероховатых поверхностей. М., Наука, 1970, 227 с
- Характеристики микрогеометрии, определяющие контактные взаимодействия шероховатых поверхностей (методика определения). М., ИМАШ, 1973, 32 с.
- Демкин Н.Б. Расчет и экспериментальное исследование характеристик контакта шероховатых поверхностей. Контактные задачи и их инженерные приложения. М., НИИ Машиноведение, 1969, с.58−62.
- Хрущев М.М., Бабичев М. А. Абразивное изнашивание. М., Наука, 1970, 252 с.
- Костецкий В.Н. Трение, смазка и износ в машинах. Киев, Техника, 1970, 396 с.
- Трикоми Ф. Интегральные уравнения. М., 1960,299 с.
- Садыхов А.И., Гусейнов А. Г., Мусаев Я. Б. Выбор давления разжима притира при доводке прецизионных деталей восстановленных и упрочненных диффузионной металлизацией. Вестник машиностроения, М., 1992, № 10, с.37−40.
- Ямпольский Г. Я., Крагельский И. В. Исследование абразивного износа элементов пар трения качения. М., Наука, 1973, 64 с.
- Лятипов В В., Гоголев В. А. Ремонт и регулирование ТА двигателей тракторов и комбайнов. М., Россельхозиздат, 1978,126 с.
- Демкин Н.Б. Расчет и экспериментальное исследование характеристик контакта шероховатых поверхностей. Контактные задачи и их инженерные приложения. М., НИИ Машиноведение, 1969, с.58−62.
- Доровских Е.В., Мишин А. И., Слинкин С. А., Махедов В. К., Картавцев И. Г. Установка для увеличения ресурса деталей топливнойаппаратуры с использованием эффекта избирательного переноса.// Отчет о НИР. ЦВНТиТ- Омск, 2005 г. 114 с.
- Джон М.Смит. Математическое и цифровое моделирование для инженеров-исследователей. — М.: Машиностроение. 1980. 272 с.
- Джонсон Н., Лион. Статистика и планирование эксперимента в технике и науке. -М., Мир, 1981. 516 с.
- Диллон Б., Сингх Ч. Инженерные методы обеспечения надежности систем. М.: Мир, 1984. 318 с.
- Рабинович С.Г. Погрешности измерения. Л.: Энергия, 1978. — 261 с.
- Ферстер Г. Единицы, величины, размерности и их практическое использование/ Пер. с нем. — Киев: Вища школа, 1984. 216 с.
- Шенк X. Системный анализ в трибротехнике. М.: Мир, 1982. — 352с.
- Электрохимические процессы при трении и использование их для борьбы с износом. Одесса: ВСНТО, 1973. — 222 с.
- Южогин Ф. Ф и др. Гальванотехника. Справочник--М.:Металлургия, 1987.-736с.
- Черкез М.Б. Хромирование--Л.Машиностроение, 1978.-104 с.
- Баймаков Ю.В. Электролитическое осаждение металлов— Л.: ЛХТИ, 1925.-189 с.
- Молчанов В.Ф. Хромирование в саморегулирующихся электролитах- -Киев: Техника, 1972.-152 с.
- Гурьянов Г. В. Электроосаждение износостойких композиций.- -Кишинев: Машиностроение, 1979.-76 с.
- Вандышев В.А. Восстановление изношенных деталей строительных машин композиционными электролитическими покрытиями на основе хрома с целью повышения их долговечности и надежности -Киев, 1973.-186 с.
- Доровских Е.В., Макаренко Н. Г., Потехин С. М., Аппинг Г. А. Исследование процесса компенсации износа плунжерных пар.// III
- Межрегиональная научно-техническая конференция Броня- 2006.- Омск- 122 с. 30 ноября- 1 декабря 2006 г.
- Доровских Е.В., Мозговой И. В., Макаренко Н. Г. Исследование процесса изнашивания плунжерных пар топливной аппаратуры и реализация метода безразборного восстановления.// «Омский научный вестник"№ 3(93) 2010 г., ОмГТУ, Омск 2010. С 110−112.
- Макаренко Н.Г. Экспериментальная установка для моделирования процессов безразборного восстановления прецизионных деталей / Н. Г. Макаренко, А. П. Демичев, Е. В. Доровских, С. Н. Волошин // Анализ и синтез механических систем. Омск, 2006. С.80−85.
- Крагельский И.В. Об оценке свойств материалов трущихся пар // Заводская лаборатория. 1968. — Т.34. — № 8. — С. 1007−1011.
- Е. В. Доровских, И. В. Мозговой, Н. Г. Макаренко, М. В. Куринной Технология электрохимикомеханической обработки прецизионных пар.// «Омский научный вестник"№ 1 (107) 2012 г., ОмГТУ, Омск 2012.324−327 С., -342 с.
- ОСТ 23.1−363−73 Насосы топливные высокого давления тракторных и комбайновых дизелей. Методы ускоренных испытаний на надежность.-М.:ГОСНИТИ.1974.-18 с.
- ОСТ 23.1.364 81. Методика ускоренных испытаний топливных насосов. ЦНИТА, 1981,16 с.
- Макаренко Н.Г., Доровских Е. В., Волошин С. Н., Демичев А.П. Повышение ресурса топливной аппаратуры дизельных двигателей
- Сборник докладов научно-практической конференции «Инновационные проекты, новые технологии и изобретения». 27 -28 октября 2005 г. Экспериментальное кольцо ВНИИЖТ, Щербинка. С.258−260.
- Пустыльник Е.И. .Статистические методы анализа и обработки наблюдений.-М.:Наука, 1968.-288с.
- Розанов Ю.А. Теория вероятностей, случайные процессы и математическая статистика. М., Наука, 1989, 312 с.