Улучшение качества отделки поверхности холоднокатаного проката при использовании хромированного инструмента
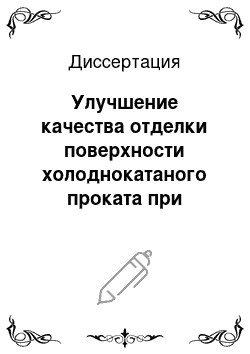
Диссертация
Максимально, с использованием хромированных валков, удалось обработать 7935 т металла практически одной ширины (1250 — 1270 мм), что в 8,8 раза превышает существующий регламент перевалок важов без покрытия. Реально увеличить длительность межперевалочного срока эксплуатации можно до 5000 т обработанного металла, т. е. в 5,5 раз, что снизит расход важов. Уменьшение шероховатости не превышает 30… Читать ещё >
Список литературы
- Качайлов А. П., Савелов Ю. Н. Пригодность автомобильного листа и пригодность его для изготовления лицевых деталей кузова легкового автомобиля. // В сб.: Листопрокатное производство (ИЧМ). Вып. № 1. М.: Металлургия. 1972. -С. 104 — 106.
- Shin Ujihara, Tomohiko Hisatsune, Yuji Hishida, Macoto Imanaka, Hideo Abe. Application of laser-textured steel sheets for autobody panels // Iron and Steel Engineer. 1991. V. 68. № 8. -P. 52 56.
- Качайлов А. П., Бойков В. Г. Современный технологический процесс непрерывной холодной прокатки и некоторые особенности прокатного оборудования. // В кн.: Листопрокатное производство (МЧМ СССР). № 4. М.: Металлургия. 1975. -С. 6−13.
- Белянский А. Д., Кузнецов Л. А., Франценюк И. В. Тонколистовая прокатка. Технология и оборудование. М.: Металлургия. 1994. -380 с.
- Зеленский В. Е., Норка С. П., Будников В. И. Совершенствование оборудования и технологии холодной прокатки листа. // Сталь. № 2. 1997. -С. 61 -63.
- Ксензук Ф. А., Трощенков Н. А., Чекмарев А. П., Сафьян М. М. Прокатка автолистовой стали. М.: Металлургия. 1969. -269 с.
- Тюрин Н. Ф., Коваленко В. С., Шанина М. М. и др. Исследование поверхностного дефекта подката типа мазковая окалина. // Металлургическая и горнорудная промышленность. 1983. № 4. -С. 17−18.
- Северденко В. П., Макушок Е. М., Равин А. Н. Окалина при горячей обработке металлов давлением. М.: Металлургия. 1977. -208 с.
- Ксензук Ф. А., Котькорло В. М., Демченко В. И. Причины образования окалины на горячекатаных полосах малоуглеродистых сталей. //Сталь. 1978. № 2. -С. 158 161.
- Ванников В. А., Столяренко Д. А., Греков Е. А., Бочков Н. Г., Бутылкина JI. И. Взаимосвязь технологических параметров выплавки стали и качества металлопродукции. М.:Металлургия. 1979. -232 с.
- Ройзман С. Е. Пути повышения качества листовой стали на широкополосных станах горячей прокатки за рубежом. // Черная металлургия. Бюллетень НТИ. 1978. № 2. -С. 3 24.
- Губинский В. И., Минаев А. Н., Гончаров Ю. В. Уменьшение окалинообразования при производстве проката. К.: Техника. 1984. -135 с.
- Ковынев М. В., Миллер В. В. Производство листового металла. М.: Металлургия. 1976. -224 с.
- Липухин Ю. В., Пименов А. Ф., Бутылкина Л. И. и др. Качество поверхности глянцевых листов для полиграфической промышленности. //Сталь. 1981. № 11. -С. 54- 57.
- Добронравов А. И. Повышение качества горячекатаных полос низкоуглеродистой стали. // В кн.: Технология производства широкополосной стали. М.: Металлургия. 1983. -С. 50 55.
- Добронравов А. И., Файзуллин В. X., Караганов Г. Г., Файзуллина Р. В. Уменьшение пораженности листового металла дефектом «вкатаная окалина». // Сталь. 1982. № 9. -С. 57 58.
- Беняковский М. А., Сергеев Е. П. Дефекты поверхности автомобильного листа (альбом). -2-е изд. М.: Металлургия. 1974. -72 с.
- Мазур В. Л., Добронравов А. И., Чернов П. П. Предупреждение дефектов листового проката. К.: Техника. 1986. -141 с.
- Мазур В. Л. Производство листа с высококачественной поверхностью. Киев.: Техника. 1982. -165 с.
- Мелешко В. И., Чекмарев А. П., Мазур В. Л., Качайлов А. П. Отделка поверхности листа. М.: Металлургия. 1975. -272 с.
- Гольдфарб Э. М., Мазур В. Л., Бойков В. Г. и др. Роль шероховатости поверхности в предупреждении сваривания при отжиге и загрязненности холоднокатаного листа // Сталь. 1971. № 6. -С. 532 533.
- Беняковский М. А. Качество поверхности автомобильного листа. М.: Металлургия. 1969. 152 с.
- Чернов П. П., Сосулин В. П., Лялько Н. А. и др. Уменьшение изломов на холоднокатаном металле. // Черная металлургия. Бюл. Ин-та Черметинформация. 1979. № 9. -С. 34 35.
- Мелешко В. И., Качайлов А. П., Ксензук Ф. А., и др. Уменьшение изломов полосы при рулонной дрессировке. // Сталь. 1969. № 6. -С. 537 540.
- Мелешко В. И., Качайлов А. П., Кудин Д. П. Поперечные изломы на предварительно изогнутой растягиваемой полосе. // В кн.: Прокатное производство (ИЧМ). М.: Металлургия. 1971. Том XXXV. -С. 70 75.
- Чернов П. П. Исследование устойчивости холоднокатаных рулонов. // В кн.: Производство горячекатаной и холоднокатаной листовой стали. М.'.Металлургия. 1983. -С. 34 38.
- Чернов П. П., Мазур В. Л., Мелешко В. И. Совершенствование режимов намоточно размоточных операций при производстве холоднокатаных полос. // Сталь. 1983. № 2. -С. 34 — 38.
- Мазур В. Л. Режимы намотки горячекатаных и холоднокатаных полос. //Сталь. 1980. № 7. -С. 591 596.
- Злов В. Е., Будаков А. П., Кочнева Т. М. и др. Исследование образования дефекта «излом» при смотке полосы. // Сталь. 1991. № 3. -С. 45 47.
- Сорокин С. А., Сафьян А. М., Качайлов А. П. Влияние холодной прокатки и дрессировки на величину дефекта «локальная неплоскостность» // В кн.: Теория и практика тонколистовой прокатки. Воронеж: ВорПИ. 1986. -С. 100- 104.
- Сорокин С. А. Расчет допустимой величины местных утолщений профиля подката, применяемого для холодной прокатки тонких полос. // Институт черной металлургии. Днепропетровск. 1987. 15 с. (Рукопись депонирована в Черметинформации № 3914-чм87).
- Полухин П. И., Заугольников Д. И., Тылкин М. А. Качество листа и режимы непрерывной прокатки. Алма-Ата: Наука. 1974. 339 с.
- Файнберг JI. Б., Радюкевич JI. В., Колов М. И., и др. Уменьшение дефекта «излом» при рулонном способе производства холоднокатаного автолиста // Металлург. 1971. № 4. -С. 25 26.
- Беняковский М. А., Мазур В. JL, Мелешко В. И. Производство автомобильного листа. М.: Металлургия. 1979. 256 с.
- Стринжа С. В., Горелик П. Б., Добромилов В. А., Антонов В. Ю. Анализ причин образования излома на переделах для цехов холодной прокатки. // Сталь. 1994. № 11. -С. 49 50.
- Паргамонов Е. А. Влияние условий холодной прокатки на сваривание листового проката при отжиге. // В кн.: Производство горячекатаной и холоднокатаной листовой стали. М.: Металлургия. 1983. -С. 43−48.
- Коцарь С. JI., Белянский А. Д., Мухин Ю. А. Технология листопрокатного производства. М.: Металлургия. 1997. 272с.
- Кунце Г., Коттман К. Возникновение волнистости при холодной прокатке тонкой широкой полосы. // Черные металлы. 1969. № 3. -С. 44 47.
- Смирнов П. Н., Девятченко JI. Д., Елесин П. 3. и др. Уменьшение изломов отожженной полосы при размотке рулонов. // Черная металлургия: Бюл. НТИ. 1978. № 21 (833). -С. 37.
- Павельски О., Расп В., Мартин Г. Дефекты, возникающие в результате сваривания витков рулонов холоднокатаной полосы при отжиге в колпаковых печах. // Черные металлы. 1989. № 4. -С. 12 20.
- Сорокин С. А. // Технологические процессы при производстве тонколистового проката: Сборник трудов ИЧМ. М.: Металлургия. 1990. -С. 43 48.
- Пискунов А. Г., Воробьев В. В., Плахтин В. Д. Совершенствование схемы подачи полосы от непрерывного стана холодной прокатки к моталкам. // Сталь. № 1. 1997. -С. 37 38.
- Кляпицын В. А., Мухин Ю. А., Колпаков С. С. и др. Влияние технологических факторов на качество поверхности холоднокатаной автолистовой стали. // Сталь. № 6. 1993. -С. 48 52.
- Белов В. С., Грузнов А. К., Бояршинов О. А. Формирование микрорельефа полос при бесконечной холодной прокатке конструкционной стали. // В кн.: Теория и практика тонколистовой прокатки. Воронеж: ВорПИ. 1986. -С. 64 67.
- Кузнецов Л. А., Мамышев А. В. Теоретическая модель управления шероховатостью поверхности полосы при холодной прокатке. // Известия вузов. Черная металлургия. 1991. № 11. -С. 45 47.
- Кузнецов Л. А., Мамышев А. В. Теоретическое определение коэффициента отпечатываемости микрорельефа валков на полосе при холодной прокатке. // Известия вузов. Черная металлургия. № 6. 1989. -С. 38−41.
- Настич В. П., Блюмин С. Л., Божков А. И., Гуляев Н. И. Исследование влияния технологических факторов процесса холоднойпрокатай на образование дефекта «излом» // В кн.: Теория и практика тонколистовой прокатки. Воронеж: ВорПИ. 1986. -С. 119 128.
- Божков А. И., Гуляев Н. И., Белов В. С., Бояршинов О. А. Влияние некоторых технологических факторов на плоскостность холоднокатаных полос. // В кн.: Тонколистовая прокатка. Воронеж: ВПИ. 1983.-С. 109−115.
- Бендер Е. А., Чернов П. П., Зиновьев Е. Г., Виноградов В. И. Влияние конструкции роликовых пресс-столов станов холодной прокатки на качество тонких полос. // В кн.: Повышение качества тонколистовой стали. МЧМ СССР. М.: Металлургия. 1986. -С. 7 12.
- Грудев А. П., Машкин JI. Ф., Ханин М. И. Технология прокатного производства М.: Металлургия. 1994. -656 с.
- Третьяков А. В., Бочаров В. Ф., Локшин Б. Е. и др. Исследование эффективности механического разрушения окалины перед травлением полос. // В кн.: Точная прокатка. Донецк. 1973. -С. 229 238.
- Ледков В. Г. Непрерывные травильные линии. М.: Металлургиздат. 1961. -206 с.
- Мазур В. Л., Шевченко Л. А., Колесниченко Б. П. и др. Оптимальные условия дрессировки горячекатаных полос перед их травлением. // В кн.: Листопрокатное производство. 1972. № 1. -С. 16 20.
- Гуренко В. Д., Фанштейн В. М. Травление полос и листов в соляной кислоте. М.: Металлургия. 1971. -126 с.
- Смирнов П. Н., Девятченко Л. Д., Файнберг Л. Б., Плетнев Ю. М. Работа четырехвалковых дрессировочных клетей 2500 в линиях непрерывного травления // Сталь. 1979. № 7. -С. 513 516.
- Чернов П. П., Сафин Г. Г., Коваленко Н. Е. Исследование эффективности окалиноломателя при солянокислотном травлении // В кн.: Теория и практика производства широкополосной стали. М.: Металлургия. 1979. -С. 76 77.
- Разработка и реализация мероприятий по предупреждению дефекта «излом» на поверхности холоднокатаной листовой стали. Отчет о НИР. Руководитель работы Акишин В. В. ИЧМ. Днепропетровск. № госрегистрации 1 870 003 657. 1989. -123 с.
- Пастрняк 3. И., Пивода П. А. Современные тенденции в производстве стальной полосы. // Обзор по системе Информсталь. Ин т Черметинформация. 1987. Вып. 10 (286). -29 с.
- Мелешко В. И., Качайлов А. П., Мазур В. JI. Прогрессивные методы прокатки и отделки листовой стали. М.: Металлургия. 1980. -192 с.
- Hudd R. С. Some aspects of the annealing of low carbon strip steel // Metals and Materials. 1987. Y3. № 2. -P. 71 76.
- Locher H. Erfahrungen beim Gluhen von Kaltbreitband im Hochkonvektions Haubenafen // Zachberichte, Huttcnpraxis, Metallweiterverarbeiting. 1986. Bol. 24. № 10. -P. 1032 — 1040.
- Schweiger G., Schwar W., Locher H., Erfahrungen bein Gliihen von Kaltbreitband im Hochkonvektions Haubenafen // Berg — und Huttenmannische Monatshefte. 1986. Bol. 131. № 9. -P. 336 — 342.
- Мазур В. П., Костяков В. В., Тимошенко П. В. Современные способы ускоренного охлаждения полосы в рулонах. Обзорн. информ. Ин т Черметинформация. Серия: Прокатное производство. 1987. Вып. 1 (276). -20 с.
- Белоусова Т. И., Бендер Е. А., Бармин Г. Ю. и др. Оптимизация микрогеометрии стальной основы для улучшения эксплуатационных свойств жести. // Сталь. 1990. № 7. -С. 61 64.
- Мелешко В. И., Качайлов А. П., Мазур В. М. и др. Производство и потребление шероховатых листов за рубежом. Сб. МЧМ СССР Прокатное производство. Серия 7. Вып. № 1. 1972. -12 с.
- Чекмарев А. П., Мелешко В. И. Шероховатость поверхности листа для глубокой вытяжки. // Сталь. № 12. 1969. -С. 1217 1219.
- Бойко Г. И., Фурсов Б. Т. Исследование процесса дрессировки аватолистовой стали в лабораторных и промышленных условиях. // В кн.: Теория и практика тонколистовой прокатки. Воронеж. ВорПИ. 1986. -С. 150- 152.
- Файзулин В. X., Антипанов В. Г., Пономарев В. Я. Оптимизация режимов обжатий при дрессировке нестареющей стали. // Бюллетень ЦНИИчермет. 1975. № 11. -40 с.
- Панкнин В., Краненберг Г. Шероховатость поверхности рабочих важов и ее перенос на полосу при дрессировке. // Черные металлы. 1968. № 3.-С. 12−19.
- Бутылкина JI. И., Начаев С. А., Рыжов В. В. Шероховатость поверхности холоднокатаных полос. // Сталь. 1970. № 2. -С. 144 146.
- Беняковский М. А., Ширинская С. А., Фирсов П. А. Микрогеометрия важов и холоднокатаной полосы. // Металлург. 1969. № 9. -С. 31−32.
- Илюкович Б. М., Самохвал В. М. К учету шероховатости при прокатке с технологическими смазками. Днепр о Дзержинский индустриальный институт. Днепродзержинск. 1987. -9 с. (Рукопись деп. в УкрНИИНТИ № 2650-Ук87).
- Бутыжина JI. И., Нагаев С. А. и др. Шероховатость поверхности холоднокатаных полос. // Сталь. 1970. № 2. -С. 144 146.
- Раимбеков А. М., Рубцова С. П., Левин В. В. и др. Влияние режимов дрессировки жести на микрогеометрию ее поверхности. // Сталь. 1993. № 1.-С. 42−44.
- Колесниченко Б. П., Мазур В. JL, Качайлов А. П. Отпечатываемость шероховатости валков на полосе при холодной прокатке и дрессировке. // В сб.: Листопрокатное производство (ИЧМ). вып. 1. М.: Металлургия. 1972. -С. 76 80.
- Боровик Л. И., Мешков Б. И., Гурин С. М. Исследование влияния шероховатости подката и валков на шероховатость поверхности холоднокатаных полос и коэффициент отпечатываемое&trade-. // В кн.: Тонколистовая прокатка. Воронеж: ВПИ. 1977. -С. 91 95.
- Репина Н. И., Мазур В. Л., Колесниченко Б. П. Влияние дробеструйной обработки на структуру поверхностного слоя важа. // Листопрокатное производство (МЧМ СССР). Сборник № 4. М.: Металлургия. 1975. -С. 90 93.
- Pesek Z. Predepisovani drsnosti povrchu hlubokotaznych plechu podle stredni сагу profilu. // Strojirenstvi. 1971. 21. № 1. -C. 46 47.
- Jacques A. Defourny, Vincent M. Leroy, Paul E. Nilles. Update of developments in Lasertex technology // Iron and Steel Engineer. 1991. v. 68. № 8. -P. 39−46.
- Keiji Nishimura, Naohiko Soeda, Shin Ujihara, Masahide Nagaoka. Development of high image clarity steel sheet by laser texturing // Iron and Steel Engineer. 1991. v. 68. № 8. -P. 46−51.
- Fawzy EI-Menshavy, Brian Snaith. Advances in electro-discharge texturing (EDT) for cold mill work rolls // Iron and Steel Engineer. 1991. v. 68. № 8. -P. 57 59.
- Андреев В. И., Деревянко В. И., Беда Н. И. и др. Новая технология получения микрорельефа повышенной маслоемкости. // Сталь. 1979. № 10. -С. 780−781.
- Франценюк Л. И., Колпаков С. С., Настич В. П. и др. Эффективный способ создания шероховатости рабочих важов листопрокатных станов. // Сталь. 1994. № 12. -С. 38 40.
- Jurgen Dolves. Electron beam texturing of rolls. // Iron and Steel Engineer. 1991. v. 68. № 8. -P. 33 38.
- Gewollte Rauhigkeit. // Produktion. 1988. № 4. -P. 5 7.
- Трейгер E. И., Комановский A. 3. Повышение стойкости прокатных валков. Киев: Техника. 1984. -146 с.
- Трейгер Е. И., Приходько В. П. Повышение качества и эксплуатационной стойкости валков листовых станов. М.: Металлургия. 1982.-192 с.
- Новиков В. Н., Белосевич В. К. и др. Валки листовых станов холодной прокатки. М.: Металлургия. 1970. -336 с.
- А. Д. Филатов, В. П. Долгов и др. Исследование стойкости рабочих валков непрерывных станов холодной прокатки. // Черметинформация. Бюл. НТИ. 1972. № 3. -С. 55 56.
- Трейгер Е. И. Изменение твердости рабочих валков станов холодной прокатки в процессе эксплуатации. // Черметинформация. Бюл. НТИ. 1972. № 9. -С. 48 -49.
- Полухин П. И., Николаев В. А., Полухин В. П., Зиновьев А. В., Косаримов Е. Н. Контактное взаимодействие металла и инструмента при прокатке. М.: Металлургия. 1974. -200 с.
- Николаев В. А., Пилипенко С. С., Васильев А. Г. и др. Влияние исходной шероховатости валков и полосы на интенсивность износа поверхности валков. // Известия вузов. Черная металлургия. № 11. 1991. -С. 56 58.
- Gerald L. Nessler, James F. Cory. Cause and solution of fifth octave backup roll chatter on 4-h cold mills and temper mills. / Iron and Steel Engineer. 1989. v. 68. № 12.-P. 33 37.
- Колпаков С. С., Пименов В. А., Цуканов А. А., Рубанов В. П. Исследование вибраций на пятиклетьевом стане 2030. // Сталь. 1993. № 1. -С. 47 52.
- Пименов В. А. О причинах нарушения устойчивости холодной прокатки. // Известия вузов. Черная металлургия. 1990. № 8. -С. 36 38.
- Раимбеков А. М., Голкин Ю. Е., Захаров JI. А. и др. Причины нарушения стабильности прокатки в последней клети стана 1400. // Сталь. 1996. № 12. -С. 41 -43.
- Mori Toshikaru. // Curr. Adv. Mater and Proc. 1991. № 2. -C. 567 569.
- Kobayashi Macoto // Curr. Adv. Mater and Proc. 1991. № 2. -C. 470−473.
- Понизовский В. M., Спелков Г. П. Определение прочности сцепления хромовых покрытий со стальной основой. // Заводская лаборатория. 1974. Т. 40. № 1. -С. 107 109.
- Дасоян М. Д., Полымская М. А., Сахорова Е. В. Технология электролитических покрытий. Д.: Машиностроение. 1989. -391 с.
- Вайнер Я. В., Дасоян М. А. Технология электрохимических покрытий. Изд 2-е. Д.: Машиностроение. 1972. -464 с.
- Анохин Ф. Ф. и др. Гальванические покрытия в машиностроении. Справочник в двух томах. М.: Машиностроение. 1985. -Т.2. -248 с.
- Мельников П. С. Справочник по гальванопокрытиям в машиностроении. 2-е изд. М.: Машиностроение. 1991. -380 с.
- Левинзон А. М. Электролитическое осаждение металлов подгруппы железа. Д.: Машиностроение. 1983. -96 с.
- Ямпольский А. М., Ильин В. А. Краткий справочник гальванотехника. 3-е изд. Д.: Машиностроение. 1981. 269 с.
- Игнатьева В. И. и др. Гальванические покрытия в машиностроении. Под ред. Шлугера М. А. Справочник в двух томах. М.: Машиностроение. 1985. Т.1. -240 с.
- Лобанов С. А. Практические советы гальванику. Л.: Машиностроение. 1983. -248 с.
- Богорад Л. Я. Хромирование. Л.: Машиностроение. 1984. -97 с.
- Черкез М. Б. Хромирование. Л.: Машиностроение. 1971. -112 с.
- Плетнев Д. В., Брусенцова В. Н. Основы технологии износостойких и антифрикционных покрытий. М.: Машиностроение. 1968. -272 с.
- Kuwamoto Hirochi, Jwadoh Schuichi, Lzushi Tomoya, Nakayama Teiji. // Jron and Steel Eng. 1989. № 2. -P. 25 27.
- Турин С. M., Пименов А. Ф., Шварцман 3. М. Хромирование стальных рабочих валков станов холодной прокатки. // Сталь. 1965. № 10. -С. 917−919.
- Ар кулис Г. Э., Шварцман 3. М., Файзулин В. К., Пономарев Г. И. Продольные полосы на поверхности жести и борьба с ними. // В кн.: Листопрокатное производство. № 4. М.: Металлургия. 1975 (МЧМ СССР). -С. 109−112.
- Беняковский М. А., Ананьевский М. Г., Бутылкина Л. И. и др. // Сталь. 1973. № 12. -С. 1105 1107.
- Хара Кэндзи, Мацумото Йосакори, Итахаси Масаки. Заявка 63 144 808 Япония, МКИ В 21 В 27/00, В 21 В 1/22.
- Кавано Хироюки, Оно Macao, Такэда Якиёси, Минабэ Йосио. Заявка 62−137 111, Япония, МКИ В 21 В 27/00, В 21 В 1/22.
- Tanaka Sumihiko, Okura Mineki, Tanaka Shohei и др. // Kobe Steel Eng. Repts. 1989. № 3. -P. 81 84.
- Слоним A. 3., Сонин А. Л. Правка листового и сортового проката. М.: Металлургия. 1981. -232 с.
- Слоним А. 3., Сонин А. Л. Машины для правки листового и сортового материала. М.: Машиностроение. 1975. -208 с.
- Лысов М. И. Теория и расчет процессов изготовления деталей методами гибки. М.: Машиностроение. 1966. -236 с.
- Мошнин Е. Н. Гибка и правка на ротационных машинах. Технология и оборудование. 2-е изд.. М.: Машиностроение. 1967. -272 с.
- Гнусин Н. П., Коварский Н. Я. Шероховатость электроосажденных поверхностей. Новосибирск: Наука. Сиб. отделение. 1970. -235 с.
- Целиков А. И., Томленов А. Д., Зюзин В. И. и др. Теория прокатки. Справочник. М.: Металлургия. 1982. -335 с.
- Железнов Ю. Д., Черный В. А., Кошка А. П., Кузнецов Л. А., Кляпицын В. А. Совершенствование производства холоднокатаной лостовой стали. М.: Металлургия. 1982. -232 с.
- Гнусин Н. П., Коварский Н. Я. Шероховатость электроосажденных поверхностей. Новосибирск. «Наука». Сиб. отделение. 1970. -235 с.
- Коновалов Ю. В., Остапенко А. Л., Пономарева В. И. Расчет параметров листовой прокатки. Справочник. М.: Металлургия. 1986. -430 с.