Поверхностное упрочнение.
Материаловедение в машиностроении
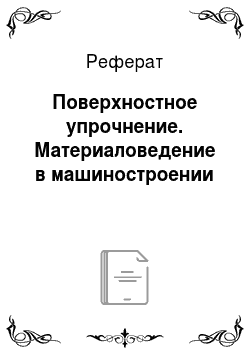
Наиболее часто закалку проводят после медленного охлаждения деталей после цементации до цеховой температуры. Детали вновь нагревают до температур выше точки Acv т. е. до температуры закалки заэвтектоидных сталей, поскольку именно такая структура сформирована в поверхностном слое в процессе цементации. Температура закалки цементованных деталей выбирается равной 820…850 °С, что выше обычно… Читать ещё >
Поверхностное упрочнение. Материаловедение в машиностроении (реферат, курсовая, диплом, контрольная)
Объемная закалка с последующим отпуском не может обеспечить работоспособность детали в условиях повышенного износа в сочетании с ударными нагрузками. Для этого одновременно необходимы высокие и твердость, и ударная вязкость. Однако после объемного упрочнения стали при высокой твердости имеют низкую ударную вязкость, и наоборот (см. рис. 5.24).
В таких случаях используется поверхностное упрочнение. При этом обеспечиваются высокая твердость и износостойкость поверхности детали при вязкой сердцевине, обеспечивающей сопротивление ударным нагрузкам.
Поверхностное упрочнение осуществляется методами химико-термической обработки (ХТО), а также поверхностной закалкой.
В результате ХТО достигается высокая износостойкость детали за счет повышения твердости поверхностного слоя при сохранении вязкой сердцевины. ХТО выполняется также для достижения коррозионной стойкости. В ряде случаев эти задачи могут быть решены одновременно.
Поверхностная закалка осуществляется нагревом на заданную глубину только поверхностного слоя, поэтому при последующем охлаждении закаливается только этот слой, а не все сечение детали. При этом сопротивление ударным нагрузкам обеспечивается вязкой сердцевиной.
Химико-термическая обработка
Химико-термическая обработка представляет собой процесс, сочетающий химическое и тепловое воздействие с целью изменения химического состава, структуры и свойств поверхностного слоя стальных изделий.
Изменение химического состава достигается за счет диффузии в поверхностный слой различных компонентов, которая более интенсивно протекает при высоких температурах. Для этого стальные изделия нагревают в активной среде, содержащей диффундирующий (насыщающий) компонент. Среда может быть твердой, газовой и жидкой. В процессе выдержки в среде при высоких температурах происходит диссоциация (распад) химических соединений с образованием насыщающего компонента в атомарном состоянии; адсорбция (осаждение) активных атомов на поверхности изделия; диффузия (перемещение) атомов вглубь металла с образованием твердых растворов, которая может сопровождаться фазовой перекристаллизацией. На поверхности могут также образовываться химические соединения высокой твердости.
Диссоциация и адсорбция протекают значительно быстрее, чем диффузия, в процессе которой формируются структура и свойства диффузионной зоны. Следовательно, толщина образованного слоя определяется скоростью диффузии, возрастающей с повышением температуры, и зависит также от длительности процесса ХТО. За толщину диффузионного слоя, насыщаемого любым компонентом, обычно принимают эффективную толщину, оцениваемую глубиной слоя с определенными свойствами (например, твердостью) или структурой. При диффузионном насыщении в поверхностном слое возникают, как правило, значительные остаточные напряжения сжатия, что повышает предел выносливости изделий.
В результате химико-термической обработки достигаются повышение твердости и износостойкости, предела выносливости или устойчивости против коррозии. При этом ХТО может использоваться как окончательная или как предварительная технологическая операция с последующей упрочняющей термической обработкой.
Наиболее широкое применение в машиностроении нашли следующие разновидности ХТО: цементация, азотирование и нитроцементация (цианирование).
Цементация — процесс диффузионного насыщения поверхностных слоев деталей углеродом. Цементации подвергают изделия, изготавливаемые из сталей, содержащих до 0,25…0,3% углерода. Такие низкоуглеродистые конструкционные стали называют цементуемыми. Они являются доэвтектоидными и имеют в равновесном (отожженном) состоянии структуру феррита и перлита, в которой доля феррита преобладает. Твердость и прочность этих сталей низкие, а пластичность и ударная вязкость высокие. Из-за низкого содержания углерода они практически не закаливаются (см. 5.5.2, подраздел «Закаливаемость и прокаливаемость»).
Механизм цементации и структура цементованного слоя. Цементацию проводят путем нагрева стальных деталей в активных средах, содержащих углерод, до 900…950 °С, т. е. выше точки Ас3 (в области устойчивого аустенита). Выбор температуры объясняется тем, что растворимость углерода в аустените (до 2,14%) значительно выше, чем в феррите (0,02%). Чем выше температура нагрева, тем больше углерода может раствориться в аустените, но при этом возрастают размеры его зерен. Скорость насыщения составляет примерно 0,1 мм/ч. Таким образом, для получения цементованного слоя глубиной 1 мм требуется не менее 10 ч.
После окончания процесса насыщения поверхности углеродом и медленного охлаждения до цеховой температуры образуется цементованный слой, имеющий переменную концентрацию углерода, убывающую от поверхности к сердцевине. Соответственно изменяется и его микроструктура. Первая зона, прилегающая к поверхности и содержащая в среднем около 1% углерода, имеет структуру перлита и цементита вторичного, характерную для заэвтектоидных сталей. Затем следует зона со структурой перлита (0,8% углерода) и переходная (третья) зона со структурой перлита и феррита (при снижении концентрации углерода менее 0,8%). По мере удаления от поверхности количество феррита в этой зоне возрастает. За эффективную величину цементованного слоя принимают глубину от поверхности до структуры, состоящей примерно из 50% феррита и 50% перлита (до 0,4…0,45% углерода).
Технологии цементации. Применяют твердую и газовую цементацию. Их название определяется первоначальным агрегатным состоянием используемых углеродсодержащих активных сред, которые называют карбюризаторами.
Твердая цементация осуществляется в карбюризаторе, содержащем активированный древесный уголь (70%), порошки BaCOi (25%) для интенсификации процесса и CaCO3 (5%) для предотвращения спекания угольных гранул. Детали укладывают рядами в стальные сварные или чугунные ящики (контейнеры). Дно ящика и каждый ряд деталей засыпают слоем карбюризатора. Ящик закрывают крышкой, кромки которой для обеспечения герметичности замазывают огнеупорной глиной, и помещают в печь. Углерод древесного угля взаимодействует с кислородом воздуха (имеющегося в цементационном ящике) и углекислым барием (), образуя газ СО, который диссоциирует по реакции:

Образующийся атомарный углерод адсорбируется на поверхности стальных деталей и диффундирует вглубь, растворяясь в аустените.
Твердая цементация имеет ряд недостатков:
- — невозможность регулирования степени насыщения поверхности деталей углеродом;
- — повышенные энергетические затраты, связанные с прогревом ящиков с карбюризатором;
- — более низкая скорость цементации по сравнению с газовой цементацией (почти в 2 раза), поскольку к скорости насыщения (0,1 мм/ч) добавляется значительное время, необходимое для прогрева ящиков и протекания химических реакций.
Твердая цементация применяется в условиях единичного и мелкосерийного производства, отличается простотой выполнения, не требует специального оборудования.
Газовая цементация осуществляется при нагреве изделий в среде газов, содержащих углерод. Наиболее часто используется газовый карбюризатор, состоящий из смеси метана CH4 (природный газ) и СО, при диссоцииации которых образуется атомарный углерод:

Далее все протекает так же, как при твердой цементации, но длительность процесса существенно сокращается. Газовая цементация позволяет обеспечить заданную концентрацию углерода в слое, механизацию и автоматизацию процесса.
Цементации может подвергаться не вся поверхность изделия. В этом случае участки, не подлежащие цементации, защищают гальванически омеднением либо специальными обмазками.
Сама по себе цементация не обеспечивает выполнения главной задачи — получения высокой твердости и износостойкости на поверхности деталей при сохранении вязкой сердцевины. Она создает только выгодное распределение углерода по сечению детали. Необходимое упрочнение поверхностного слоя достигается только последующей термической обработкой, которая всегда проводится после цементации.
Термическая обработка цементованных деталей. После цементации детали подвергают закалке для получения высокой твердости в поверхностных слоях и низкому отпуску (160…180 °С). Применяются различные технологии закалки в зависимости от типа производства, требований к прочности поверхностного слоя и сердцевины деталей, необходимости автоматизации процесса.
Наиболее часто закалку проводят после медленного охлаждения деталей после цементации до цеховой температуры. Детали вновь нагревают до температур выше точки Acv т. е. до температуры закалки заэвтектоидных сталей, поскольку именно такая структура сформирована в поверхностном слое в процессе цементации. Температура закалки цементованных деталей выбирается равной 820…850 °С, что выше обычно используемых при закалке заэвтектоидных сталей (780…800 °С). Это обеспечивает не только полную закалку и измельчение зерен в результате перекристаллизации цементованного слоя, но и частичные перекристаллизацию и измельчение зерна в сердцевине. На поверхности образуется структура мслкоигольчатого мартенсита (после последующего низкого отпуска — отпущенного мелкоигольчатого мартенсита), вторичного цементита и остаточного аустенита (5…8%). Структура сердцевины зависит от химического состава стали и размеров изделия. Структура сердцевины деталей из углеродистых сталей — феррит и перлит; легированных — сорбит, троостит или низкоуглеродистый мартенсит.
При крупносерийном и массовом производстве для деталей менее ответственного назначения закалка совмещается с газовой цементацией. Закалочное охлаждение производится непосредственно с температуры цементации или после некоторого подстуживания до 820…850 °С для уменьшения термических напряжений. Такая технология является наиболее экономичной и легко автоматизируется. Однако при закалке сердцевина детали сохраняет крупное зерно, а на поверхности образуется крупнопластинчатый мартенсит и повышенное количество остаточного аустенита. Это объясняется тем, что длительные выдержки при высоких температурах в процессе цементации вызывают значительный рост аустенитного зерна. Поскольку закалка выполняется непосредственно с высокой температуры цементации, структура остается крупнозернистой. Удовлетворительные свойства после такой обработки получаются в природно мелкозернистых сталях при содержании углерода в поверхностном слое, близком к эвтектоидному;
Наиболее ответственные тяжелонагруженные детали, для которых необходимы высокие прочность и ударная вязкость сердцевины, после цементации подвергают двойной закалке. Первая проводится с целью перекристаллизации структуры сердцевины и растворения сетки вторичного цементита в цементованном слое. В сердцевине после цементации сохраняется структура доэвтектоидной стали, поэтому температура нагрева для закалки выбирается выше точки Ас.у В результате структура сердцевины проходит полную перекристаллизацию и становится мелкозернистой. На поверхности вследствие нагрева до высоких температур образуется структура, состоящая из крупнопластинчатого мартенсита, имеющего низкую прочность, и остаточного аустенита.
Вторая закалка выполняется для устранения перегрева цементованного слоя. Температура нагрева выбирается выше точки Act (750…780 °С), поскольку на поверхности после цементации получается структура заэвтектоидной стали. После второй закалки на поверхности образуется мелкоигольчатый мартенсит, остаточный аустенит и небольшое количество зернистого цементита. Структура сердцевины повторно проходит частичную перекристаллизацию и измельчение зерна. Недостатками такой обработки являются сложность технологического процесса, повышенное коробление изделий сложной формы, возможное окисление и обезуглероживание поверхности.
После цементации, закалки и низкого отпуска твердость поверхностного слоя составляет 58…62 HRC, а сердцевины — менее 20 HRC для углеродистых сталей и 25…45 HRC для легированных. Окончательная глубина слоя на деталях обычно назначается в пределах 0,8…1,2 мм.
Цементации с последующей термической обработкой подвергают детали, работающие в условиях повышенного износа и динамических нагрузок (например, зубчатые колеса, червяки, кулачки, распределительные валики и т. п.). Ее целью является получение высокой поверхностной твердости, обеспечивающей хорошую износостойкость, при сохранении вязкой сердцевины.