Применение принципов TPS на современных предприятиях
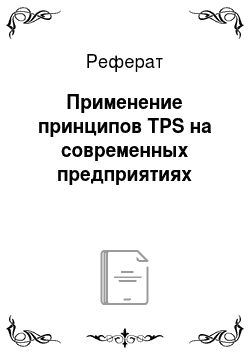
Использовать практические семинары по кайдзен для обучения и осуществления быстрых изменений. Такие мероприятия обычно проводятся с помощью приглашенных консультантов. Как правило, семинары по кайдзен длятся около недели, при этом участники (команда специалистов, занимающаяся осуществлением какого-либо процесса, а также его потребители и поставщики) анализируют. существующую бизнесдеятельность… Читать ещё >
Применение принципов TPS на современных предприятиях (реферат, курсовая, диплом, контрольная)
В настоящий момент многие предприятия используют те или иные методы Toyota, однако компании, сумевшие целиком реализовать на практике концепцию бережливого производства, являются скорее исключением. Объяснение этому факт>' кроется в том, что подход Toyota, в первую очередь, предполагает создание определенной внутриорганизационной философии, что является чрезвычайно сложным, затратным и длительным процессом. Для радикального преобразования производственной культуры могут потребоваться десятилетия, а это подразумевает дальновидность и преемственность руководства предприятия.
Понимание высшим менеджментом сущности подхода Toyota, а также готовность внедрять, поддерживать и постоянно совершенствовать культуру бережливого производства являются основными предпосылками успешного преобразования предприятия на принципах TPS.
Как считает Дж. Лайкер, для создания бережливой обучающейся организации необходим некоторый минимальный уровень заинтересованности топ-менеджмента, определить который можно, ответив на следующие вопросы.
- 1) Придерживается ли высшее руководство долгосрочной концепции создания добавленной ценности для потребителей и общества в целом?
- 2) Готово ли высшее руководство развивать компанию и привлекать к этому процессу ее сотрудников и партнеров?
- 3) Возможна ли преемственность в философии высшего руководства?
Если топ-менеджеров интересуют только краткосрочные финансовые результаты, персонал рассматривается лишь как рабочая сила, поставщики — как источник дешевых деталей, а руководство предприятия сменяется при каждом кризисе, ответ на все перечисленные вопросы будет отрицательным. В этом случае компания может использовать краткосрочные инструменты бережливого производства («5S», ячейки, канбан и т. п.), имея в виду, что они способны повысить эффективность отдельных видов деятельности, поскольку являются лишь одним из многих аспектов философии Toyota.
Однако если компания способна обеспечить преемственность руководства, позиция которого остается неизменной с течением времени, она может приступить к внедрению собственной версии принципов TPS. По мнению Дж. Лайкера, в процессе такого преобразования предприятию следует:
- 1) Начинать с воздействия на техническую систему, а затем сразу же приступать к изменению производственной культуры. Наилучшим путем здесь будет совершенствование основных потоков добавления ценности при поддержке преданных делу лидеров, работающих также и над осуществлением культурных изменений.
- 2) Акцентировать внимание на практическом освоении принципов бережливого производства, не тратя слишком много времени на теоретическую подготовку и инструктаж сотрудников.
- Ъ) Осуществить ряд пилотных проектов по созданию потока добавления ценности, чтобы продемонстрировать персоналу действенность принципов TPS. Это позволяет преодолеть инертность корпоративной культуры, что особенно актуально для производственных подразделений компании.
- 4) Активно использовать карты потока создания ценности для представления текущего и будущего состояния процессов. Составление таких карт, а также плана преобразований конкретного процесса, желательно поручить межфункциональной группе. Она должна состоять из руководителей, которые распоряжаются ключевыми ресурсами, и исполнителей, являющихся составной частью представленной на карте деятельности. Составление карт следует использовать применительно к тем продуктам, процесс создания которых планируется преобразовывать немедленно.
- 5) Использовать практические семинары по кайдзен для обучения и осуществления быстрых изменений. Такие мероприятия обычно проводятся с помощью приглашенных консультантов. Как правило, семинары по кайдзен длятся около недели, при этом участники (команда специалистов, занимающаяся осуществлением какого-либо процесса, а также его потребители и поставщики) анализируют. существующую бизнесдеятельность, учатся рассматривать эту деятельность с точки зрения бережливого производства и, что самое важное, сразу же приступают к реализации своих наработок[1]. Семинары по кайдзен используются как один из инструментов внедрения конкретных усовершенствований, которые позволят реализовать концепцию потока добавления ценности.
- 6) Перестроить организационную структуру в соответствии с потоком создания ценности. В компании должны существовать менеджеры, ответственные не только за отдельные стадии процесса создания ценности, но и за поток в целом.
- 7) Относиться к созданию бережливого производства как к постоянной обязательной работе.
- 8) Привести систему показателей в соответствие с принципами потока создания ценности.
- 9) Привлечь специалистов в области бережливого производства для обучения сотрудников и быстрого получения первых результатов.
В их роли могут выступать либо консультанты из сторонних организаций, либо нанятые специалисты с как минимум пятилетним опытом работы в системе бережливого производства. Их задачей станет техническая помощь в процессе преобразований. Такие специалисты помогут облегчить преобразования, дадут процессу первый импульс, на практике обучая согрудников принципам TPS.
- 10) Чтобы создать обучающееся бережливое предприятие, необходимо накапливать собственные знания и опыт, поэтому следует обучить лидеров в области бережливого производства и позаботиться о преемственности. Лидер должен досконально знать философию ЛИН, верить в нее и жить в соответствии с ней. Кроме того, он обязан до мелочей знать работу предприятия и его корпоративную культуру, а также уметь заинтересовать и привлечь людей к участию в процессе преобразований.
- 11) В процессе изменений опираться на историю и систему ценностей своей компании. Основные составляющие бережливого производства неизменны, однако при их внедрении каждое предприятие должно двигаться по собственному пути, добиваясь органичного сочетания принципов TPS с национальной и корпоративной культурой.
Опора на перечисленные рекомендации повышает вероятность, но не гарантирует построения бережливой обучающейся организации. Препятствовать достижению этой цели могут:
- — сопротивление высшего руководства, которое не разбирается в данном вопросе;
- — неспособность менеджмента довести до конца процесс внедрения ЛИН;
- — коренная реорганизация предприятия, приведшая к замене лидсров-приверженцев бережливого производства на его противников;
- — неблагоприятная ситуация на рынке;
- — смена собственника предприятия;
- — культурные барьеры.
В заключение следует остановиться на практике внедрения принципов ЛИН на отечественных предприятиях.
По данным Института комплексных стратегических исследований, в России наиболее склонными к внедрению бережливого производства являются предприятия машиностроения, а также черной и цветной металлургии[2]. При этом лидируют автомобильная промышленность и цветная металлургия, причиной чего является высокий уровень конкуренции в этих сферах и, в частности, приход на российский рынок иностранных компаний. Кроме того, эффект повышения отдачи от основных фондов, достигаемого за счет использования ЛИН, наиболее важен для тех отраслей, в которых эти фонды дороги, а таковыми как раз и являются металлургия и машиностроение. В процессе внедрения TPS большинство предприятий пока ограничивается применением одного-двух инструментов. Масштабные же проекты реорганизации, затрагивающие различные производственные процессы, ведутся только в 5 процентах компаний (из числа опрошенных ИКСИ). Наибольшую популярность в России получили следующие инструменты ЛИН (в процессе убывания):
- — визуализация рабочего места (система «5S»); система оптимизации запасов «канбан»;
- — составление карт потока создания ценности;
- — система ухода за оборудованием; технология быстрой переналадки оборудования[3].
Самыми популярными являются система «5S» и «канбан», что обусловлено, во-первых, узкими местами, имеющимися в работе большинства предприятий, а во-вторых, относительной простотой освоения и реализации названных инструментов. Таким образом, большинство отечественных организаций акцентирует внимание на инструментальной стороне бережливого производства, добиваясь с помощью методов ЛИН быстрых, но точечных улучшений. Главной причиной такого положения дел является ориентация акционеров, а следовательно, и топ-менеджеров, на получение прибыли в краткосрочной перспективе, что, естественно, не способствует проведению полномасштабных проектов реорганизации.
Основной сложностью при внедрении отдельных инструментов TPS, с нашей точки зрения, является то, что все методы бережливого производства дополняют и поддерживают друг друга, действуя как единая система, и часто бывает невозможно разграничить сферы действия нескольких инструментов. Отсюда — трудности с достижением конкретных целей силами одного-двух методов ЛИН.
Tax, например, когда на одном машиностроительном предприятии, работавшем в четыре смены, начали внедрять один из принципов системы «5S» — рациональное размещение предметов, выяснилось, что каждый из четырех рабочих сборочного поста рационально размещает предметы по-своему. Следовательно, одни и те же операции каждый выполняет тоже по-своему. В Toyota такая проблема не возникла бы в принципе, поскольку компания имеет четкие стандарты на выполнение всех операций. Однако в данном случае, поскольку предприятие внедряло только один метод бережливого производства — систему «5S», — чтобы найти оптимальный способ размещения инсгрументов, рабочим нужно было договориться между собой, и этот процесс занял у них больше месяца.
Однако, как было отмечено, ряд предприятий (среди них, например, АЗ «Урал» и ГАЗ), все же делает попытки комплексной модернизации производства, пытаясь освоить не только инструменты, но и философию TPS. Несмотря на длительность этого процесса, первые результаты реорганизации становятся видны уже через несколько месяцев, значительное же улучшение финансовых показателей достигается через один-два года после начала преобразований.
Так, приступив к внедрению системы бережливого производства, ОАО «Русал Саянал» уже через четыре месяца сократило время переналадки оборудования на 2 часа.
В результате применения принципов бережливого производства на пилотном участке ГАЗа (сборка кабин бортовых «ГАЗелей»), процент кабин, годных с первого предъявления без доработок и исправлений, вырос с 2% (в марте 2003 года) до 80% (в феврале 2004 года). Из 245 наименований дефектов, имевших место в начале проекта, полностью были исключены 206. Реорганизация рабочих мест операторов позволила снизить численность работников с 258 до 196 при одновременном увеличении числа собираемых кабин в смену с 98 до 146. К концу 2004 года с первого предъявления сдавалось 96% автомобилей, число дефектов на 1 автомобиль сократилось более чем в 10 раз. Резко снизились потери от внутреннего брака, сократились расходы на выполнение гарантийного ремонта.
АЗ «Урал», начав внедрять принципы TPS в 2004 году, к 2006 году повысил производительность труда на 25%. В одном из цехов «Урала» освоение методов быстрой перенатадки оборудования позволило сократить время переналадки с 32 до 5 минут. В 2005 году только за счет сокращения наиболее очевидных потерь заводу удалось сэкономить 440 млн. рублей, или 7% выручки.
Основными проблемами, с которыми сталкиваются отечественные предприятия, внедряющие ЛИН, являются:
- 1) невовлеченность менеджмента в процесс изменений, непонимание необходимости внедрения TPS. При этом если высший руководитель в течение определенного времени не склоняется к активному участию в процессе преобразований, собственники вынуждают его уйти из компании. (Правда, так происходит лишь в случае, если владелец предприятия имеет твердую позицию относительно необходимости реорганизации. В противном случае преобразования либо не будут проведены вовсе, либо пройдут поверхностно, не затронув основных внутриорганизационных процессов);
- 2) мировоззрение руководителей, в соответствии с которым считается, что менеджер высокого уровня «знает все». Однако, с точки зрения ЛИН, чтобы многое знать, нужно постоянно видеть производство своими глазами и принимать решения непосредственно на месте, а такой стиль управления чужд российским руководителям. Кроме того, ощущение, что человек «знает все», делает его закрытым для совершенствования и обучения, которые являются еще одной необходимой составляющей философии бережливого производства;
- 3) формировавшаяся годами, а иногда и десятилетиями культура производства.
Например, если, в соответствии с системой «5S», рабочие начинают хранить вещи и инструменты в специальных шкафчиках, то внутри порядок все равно не наводится. Кроме того, шкафчики необходимо запирать, поскольку иначе возникает проблема воровства, ключи же часто теряются. Таким образом, в результате проведенных изменений временные потери отнюдь не устраняются и производительность остается на том же уровне.
Очень сложно бывает также изменить психологию массового производства — рабочие привыкли работать на объем, а не изготавливать строго определенное количество изделий;
- 4) отсутствие доверия в отношениях с поставщиками. Как говорилось, подход Toyota предполагает создание бережливого потока по всей цепочке поставок. Российский же бизнес традиционно непрозрачен, по большей части считает себя вполне самодостаточным, и потому в массе своей не готов к работе с деловыми партнерами в рамках долгосрочных совместных проектов по внедрению ЛИН;
- 5) необходимость разработки и использования новой системы мотивации персонала. Бережливое производство предполагает непосредственную заинтересованность каждого работника в максимальной эффективности всего предприятия, вовлечение персонала в процесс непрерывного совершенствования. Формирование подобной корпоративной культуры невозможно без применения соответствующих форм стимулирования сотрудников — отказа от сдельной оплаты труда, системы участия персонала в доходах команды, использования новых критериев оценки работы и т. п.
Для поддержания инновационного климата компания должна отказаться от идеи наказания сотрудников, которая, к сожалению, является неотъемлемой частью российской бизнес-культуры. На практике внедрение TPS часто происходит директивно: сотрудников обязывают выполнять работу определенным образом, и они попросту стараются угодить начальству. Единственным мотиватором в этом случае является страх наказания. Разумеется, в такой ситуации невозможно говорить о глубинных преобразованиях на уровне каждого сотрудника, необходимых для работы системы непрерывного совершенствования;
6) появление избытка рабочей силы, к выявлению которого приводит оптимизация потоков. С одной стороны, увольнение персонала ухудшает социально-психологический климат в организации и не способствует вовлечению оставшихся сотрудников в процесс дальнейших преобразований. С другой стороны, избыток рабочих мест — это потери, которые увеличивают затраты и не добавляют ценности конечному продукту. Согласно философии TPS, решить названную дилемму можно путем трудоустройства освобождаемых людей на вакантные позиции внутри компании, что и делает ряд отечественных предприятий.
Литература
по теме:
- 1. Вумек Д. П., Джонс Д. Бережливое производство: Как избавиться от потерь и добиться процветания вашей компании. — М.: Альпина Паблишер, 2016. — 472 с.
- 2. Имаи Масааки. Гемба кайдзен: Путь к снижению затрат и повышению качества. — М.: Альпина Паблишер, 2016. — 424 с.
- 3. Лайкер Дж. Дао Toyota: 14 принципов менеджмента ведущей компании мира. — М.: Альпина Паблишер, 2013. — 400 с.
- 4. Лайкер Дж. Практика Дао Toyota: Руководство по внедрению принципов менеджмента Toyota / Дж. Лайкер, Д. Майер. — М.: Альпина Паблишер, 2016. — 586 с.
- 5. Ротер М., Шук Дж. Учитесь видеть бизнес-процессы. Практика построения карт потоков создания ценности. — М.: Альпина Паблишер, 2015. — 144 с.
- 6. Синго Сигео. Быстрая переналадка: Революционная технология оптимизации производства. — М.: Альпина Бизнес-Букс, 2006. — 344 с.
- 7. Тайити Оно. Производственная система Тойоты. Уходя от массового производства. — М.: Институт комплексных стратегических исследований. — 2012. — 208 с.
- 8. Юрасова Т. Пошел ты на гембу муду разгребать // Эксперт. — 2006. — № 30. — С. 30−40.