Практика выработки решений Ключевые понятия и определения
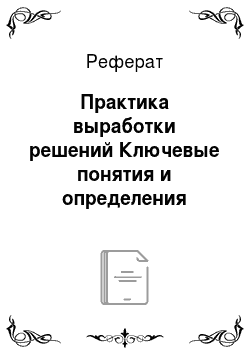
Уместно отметить еще несколько интересных моментов, связанных с решением данной задачи. Полученный нами оптимальный план — это не просто правильный, допустимый план распределения оборудования, по которому можно работать (такими были и оба предыдущих: они обеспечивали как полную загрузку оборудования, так и комплектность продукции). Оптимальный план, помимо того, что он отвечает этим требованиям… Читать ещё >
Практика выработки решений Ключевые понятия и определения (реферат, курсовая, диплом, контрольная)
Задача о станках. Задача о раскрое. Задача директора. Подбор персонала. Оптимальное планирование.
Рассмотрим ряд типовых задач выработки решений менеджером.
о станках
Представим себе три станка, каждый из которых может производить два типа деталей. Назовем их условно деталями, А и Б. Производительность каждого из станков по разным типам деталей, как правило, различна:
- • станок I производит в одну минуту 5 деталей, А или 5 деталей Б;
- • станок 2 производит в одну минуту 6 деталей, А или 2 детали Б;
- • станок 3 производит в одну минуту 5 деталей, А или 3 детали Б.
Задача осложняется тем, что требуется выполнить два важных условия, или, как говорят в математике, учесть два ограничения: 1) ни один из станков не должен простаивать; 2) продукция должна быть комплектна, т. е. количество произведенных деталей, А должно равняться количеству деталей Б (это, например, могут быть гайки и болты).
Несмотря на кажущуюся простоту задачи, ни одним из традиционных методов она не решается. Убедимся в этом на примере (в котором не рассматриваются некоторые несущественные подробности).
Возьмем вариант, при котором в течение рабочего времени станок I производит летать А, станки 2 и 3 также загрузим на все время работы, но деталь Б. (Все расчеты будем производить, исходя из общей продолжительности времени работы в 6 часов = 360 минут. Результат такого решения изобразим следующим образом (табл. 6.2): слева покажем продолжительность работы станков по различным деталям, а справа — соответствующее количество произведенной продукции (произведение времени работы на минутную производительность).
Таблица 6.2.
План распределения 1.
Станок. | Продолжительность работы станка, мин. | Производительность станка (количество деталей за время работы). | ||
А. | Б. | А. | Б. | |
Итого: |
Такое решение вроде бы отвечает поставленным условиям: во-первых, все станки полностью загружены в течение рабочего времени; во-вторых, количество произведенных деталей, А равно количеству деталей Б. Остается, однако, открытым главный вопрос планирования: является ли наше решение наилучшим в данных условиях? Нельзя ли составить другой план распределения станков, который отличался бы наибольшей производительностью?
Общее количество выпушенной продукции 1800+1800 = 3600 деталей Суть метода удобнее всего выразить с мощью наглядного геометрического представления, графика, изображенного на рис. 6.1.
Здесь показан построенный по правилам науки пятиугольник ОАВСЭ (заштрихован). Много соответствует условиям нашей задачи и представляет собой область допустимых планов распределения времени работы станков 2 и 3 над деталью А. (В своих расчетах мы вполне можем обойтись двумя станками и одной деталью так как по этим данным нетрудно рассчитать остальные). По соответствующим осям отмечена продолжительность работы этих станков.
Любая точка заштрихованной области допустимых планов, как видно из ее названия, даст нам какой-либо один возможный азан, отвечающий обоим принятым условиям-ограничениям. Так, например, точка 0 соответствует нашему первоначальному расчету: время работы над деталью, А на станках 2 и 3 равно нулю.

Рис. 6.1. Графическое изображение плана распределения.
Посмотрим, какой план распределения станков дает другие точки области. Вот, скажем, точка В. Как видно из графика, этой точке соответствует время работы над деталью, А станка 2, равное 90 минутам, станка 3 — 360 минутам. По этим данным нетрудно составить второй план распределения станков, причем время, отводимое на производство детали Б станками 2 и 3, получится как дополнение до 360 минут времени, снятогос графика,—станки не должны простаивать. Что касается станка 1, то его время работы подбирается таким, чтобы общее количество деталей, А и Б совпадало.
Второе решение, следовательно, будет выглядеть таким образом (табл. 6.3).
Вот гак результат! Мы сразу же. можно сказать бесплатно, на том же оборудовании увеличили производительность на 1080 деталей, т. е. на целых 30%.
Однако возникает законный вопрос — добились ли мы уже самого лучшего, оптимального решения, или нет? Стоит ли дальше пытаться улучшить план?
Наука убедительно доказывает, что оптимальному решению соответствует одна из вершин пятиугольника допустимых планов, а именно та, для которой обшая производительность окажется максимальной. В нашем случае это вершина С.
Таблица 6.3.
План распределения 2.
Станок. | Продолжительность работы станка, мин. | Производительность станка (количестводеталей за время работы). | ||
А. | К. | А. | К. | |
Итого: |
Общее количество выпущенной продукции 2340+2340 = 4680 деталей. Действительно, рассчитывая известным «уже нам путем план распределения станков для этой точки, получим следующее решение (табл. 6.4).
Таблица 6.4.
План распределения 2.
Станок. | Продолжительность работы станка, мин. | Производительность станка (количество деталей за время работы). | ||
А. | К. | А. | К. | |
Итого: |
Общее количество выпущенной продукции 2610+2610 = 5220 деталей.
Мы получили план почти наполовину (на 45%) лучше, чем первый. И этот существенный прирост, подобно и предыдущему улучшению, ничего (если не считать умственных усилий на планирование) не стоит. Никакого дополнительного расхода каких-либо ресурсов не потребовалось. Те же станки, те же детали, те же станочники работают то же время. Не меняются и производительности станков. Эффект здесь чисто интеллектуальный, умственный — за счет рационального распределения ресурсов оборудования (кстати, латинское слово «рационалио означает разумный). Умное, обоснованное решение сделало чудо, в которое даже трудно поверить. Подобный «чудесный» результат, как мы уже понимаем, характерен для всех решений, принимаемых с помощью научных методов.
Может возникнуть, правда, вопрос: а нельзя ли обойтись в подобных задачах без какого-либо специального математического аппарата, идя путем простого перебора всех возможных вариантов решения. Этот соблазн следует тут же отмести. Расчет показывает, что перебор всех возможных вариантов решений подобных задач не под силу даже самому большому коллективу вычислителей.
Уместно отметить еще несколько интересных моментов, связанных с решением данной задачи. Полученный нами оптимальный план — это не просто правильный, допустимый план распределения оборудования, по которому можно работать (такими были и оба предыдущих: они обеспечивали как полную загрузку оборудования, так и комплектность продукции). Оптимальный план, помимо того, что он отвечает этим требованиям, должен быть еще обязательно самым эффективным. В данном случае это означает требование максимума деталей. Действительно, как уже отмечалось, оптимизация обязательно должна предусматривать обращение одного из показателей в максимум (или минимум). Но только одного показателя. Нельзя вести оптимизацию по нескольким показателям одновременно.
И еще один важный вывод, к которому подводит станковая задача: оптимизация возможна лишь по верхнему уровню управления для всей производственной системы в целом. В данном случае это означает, что мы получили оптимальный план лишь для всех трех станков вместе. А для каждого в отдельности? Туг оптимальности может и не быть. Так, в нашей задаче оптимальный план явно не понравится станочнику, работающему на станке 3: при большей производительности — 5 деталей в минуту — план предлагает ему работать всего 90 минут, а при меньшей — 3 детали в минуту — целых 270. Но тут уж ничего не поделаешь: чтобы получить оптимальный, сбалансированный план предприятия, кому-то на нижнем уровне приходится работать в неоптимальном режиме. Но значительнодешевле компенсировать издержки «внизу», чем лишиться огромного эффекта оптимизации работы целого предприятия.
Методы, подобные рассмотренному, находят широкое применение для обоснования оптимальных решений в самых различных областях человеческой деятельности: при планировании перевозок и в торговле, для правильной организации труда, в управлении транспортом и строительством.