Производство фенола
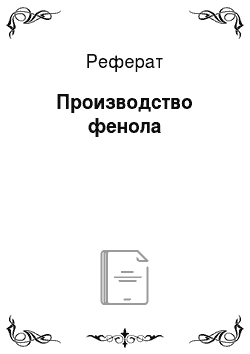
Катализатором разложения служит серная кислота, которая подается во всасывающую линию циркуляционного насоса и вместе с циркуляционной жидкостью поступает в реактор. Реакционная масса из реактора 8 проходит в холодильник 9, так как все тепло реакции в реакторе снять не удается. Охлажденная реакционная масса частично с помощью центробежного насоса снова направляется в реактор, а частично поступает… Читать ещё >
Производство фенола (реферат, курсовая, диплом, контрольная)
1.ПРОИЗВОДСТВО ФЕНОЛА ЧЕРЕЗ БЕНЗОЛСУЛЬФОКИСЛОТУ
2.ПРОИЗВОДСТВО ФЕНОЛА ЧЕРЕЗ ХЛОРБЕНЗОЛ
3.ПРОИЗВОДСТВО ФЕНОЛА ОКИСЛИТЕЛЬНЫМ ХЛОРИРОВАНИЕМ БЕНЗОЛА
4.ПРОИЗВОДСТВО ФЕНОЛА ЧЕРЕЗ ИЗОПРОПИЛБЕНЗОЛ ЛИТЕРАТУРА
Фенол С6Н5ОН—бесцветное кристаллическое вещество со специфическим запахом, температурой плавления 43 °C, температурой кипения 181 °C, удельным весом 1,071.
Фенол применяется в производстве красителей, пластмасс, синтетического волокна—капрона. Поэтому получение фенола только из каменноугольной смолы не могло бы покрыть всех потребностей его в промышленности.
Известны следующие методы получения синтетического фенола.
Метод щелочного плавления наиболее старый, требующий большого расхода серной кислоты на сульфирование бензола и каустика для последующего сплавления бензолсульфонатриевой соли.
Метод получения фенола путем хлорирования бензола и последующего омыления хлорбензола раствором едкого натра возможно осуществить при достаточном количестве дешевой электроэнергии для производства хлора и каустика. Недостатками метода являются применение высокого давления (около 300 атм.) и значительная коррозия аппаратуры.
Метод Рашига не требует расхода других видов сырья, кроме бензола и медно-железного катализатора, но конверсия бензола за проход не превышает 20%. Коррозия аппаратуры значительна.
Разложение гидроперекиси изопропилбензола является более новым методом получения фенола. Схема производства его довольно сложная, так как состоит из производства гидроперекиси путем алкилирования бензола пропиленом с последующим окислением изопропилбензола воздухом и образованием гидроперекиси его. Положительным фактором этого метода является получение одновременно с фенолом другого важного продукта— ацетона.
1. ПРОИЗВОДСТВО ФЕНОЛА ЧЕРЕЗ БЕНЗОЛСУЛЬФОКИСЛОТУ
(Схема 1)
Процесс получения фенола слагается из следующих стадий:
1) сульфирования бензола с получением бензолмоносульфокислоты,
2) нейтрализации сульфурационной массы,
3) щелочного плавления,
4) выделения фенола.
Сырьем для получения бензолмоносульфокислоты является 95%-ный бензол и 96%-ная серная кислота. Серная кислота из мерника 18 поступает в реактор-сульфуратор 3, который нагревается до 150—160°С; бензол из мерника 1—в испаритель-подогреватель 2. Образующиеся в нем пары бензола с температурой 120—125°С направляются в сульфуратор, барботируя через слой кислоты. В сульфураторе протекают реакции:
основная — получение бензолмоносульфокислоты
C6H6+H2S04 > C6H5SO3H + H2O;
побочные реакции:
1) образование сульфонов С6Н5SО3Н+С6Н6 > C6H5SO2C6H6+H2O;
2) образование метадисульфокислоты бензола
C6H5S03H+H2S04 > C6H4(SO3H)2+H2O.
Бензол для сульфирования берется в пятикратном избытке. Пары не-прореагировавшего бензола проходят через брызгоуловитель 19, охлаждаются в холодильнике 20. Конденсат из холодильника 20 поступает в отстойник 21 для отделения бензола от воды, которая уносится из сульфуратора вместе с парами бензола. Бензол обрабатывается в нейтрализаторе 22 едким натром для удаления остатков серной кислоты и из сборника обратного бензола 24 передавливается в мерник для бензола 1. Продукты реакции из сульфуратора 3 периодически спускаются в нейтрализатор 4. Нейтрализация производится 25%-ным раствором сульфита натрия по реакции
2C6H5S03H+Na2S03 > 2C6H5S03Na + S02+H20.
В реакционную жидкость добавляют еще твердого сульфита натрия для повышения концентрации раствора. Образовавшийся раствор бензолсульфоната стекает в сборник 5. Оттуда он подается в плавильный котел 6, в который из котла для плавки каустика 7 направляется расплавленный едкий натр. В плавильном котле при температуре 300 °C протекает реакция
C6H5S03Na + 2NaOH > C6H5ONa + Na2SO3 +H20
Образовавшийся плав выпускают в гаситель 9, залитый холодной водой, для растворения фенолята. Сульфит натрия, вследствие меньшей растворимости, остается большей частью в осадке. Масса из гасителя выдавливается на центрифугу 10. Раствор фенолята поступает в сборник фенолята 11, затем передавливается в кристаллизатор для сульфита 12 , после чего сливается в подкислитель—котел для разложения фенолята 13. Расположение его производится сернистым газом, который поступает из аппарата 4, по реакции:
2C6H5ONa + S02 + Н20 > 2С6Н5ОН + Na2S03
Образующийся сульфит натрия передавливается в сборник раствора сульфита натрия 15, из которого поступает на нейтрализацию сульфурационной массы в нейтрализатор 4.
Фенол передавливается в отстойник для фенола-сырца 16, оттуда стекает в сборник фенола 17 и уходит на перегонку (на схеме не указано).
Основные параметры производства
Температура в сульфураторе 150−160°С Соотношение серной кислоты и бензола при сульфировании 1:5
Температура в нейтрализаторе 100 °C Температура щелочного плавления 350 °C Температура в конце гашения (в апп. 9) 70−80°С Температура подкисления 40−45°С Схема 1. Технологическая схема производства фенола через сульфокислоту Обозначения на схеме 1:
1 — мерник для бензола,
2—испаритель-перегреватель,
3—сульфуратор,
4—нейтрализатор,
5—сборник для бензолсульфоната,
6—плавильный котел,
7— котель для плавления каустика,
8-печь,
9-гаситель,
10—центрифуга,
11—сборник фенолята,
12—кристаллизатор для сульфата,
13—котел для разложения фенолята,
14—ловушка для отходящих газов,
15-сборник для раствора сульфита,
16—отстойник для фенола-сырца,
17—сборник для фенола,
18—мерник для серной кислоты,
19—брызгоуловитель ,
20—холодильник,
21—отстойник,
22—нейтрализатор,
23—мерник для щелочи,
24—сборник обратного бензола.
2.ПРОИЗВОДСТВО ФЕНОЛА ЧЕРЕЗ ХЛОРБЕНЗОЛ
(Схема 2)
Метод производства фенола хлорированием бензола в последующим омылением образовавшегося при этом хлорбензола щелочью достаточно хорошо освоен в области получения хлорбензола. Но омыление хлорбензола вызывает затруднения в аппаратурном оформлении процесса, вследствие применения высокого давлення и коррозии аппаратуры.
Сырьем для производства фенола по описываемой схеме являются хлорбензол, едкий натр, углекислый газ и гидрат окиси кальция.
Необходимый для процесса 15—20%-ный раствор едкого натра готовится и смесителе 2, куда из напорных баков 3 в 7 подается свежий и циркуляционный растворы едкого натра. Хлорбензол в дифенилоксид, поступающие из напорных баков 4 и 6, смешиваются в смесителе 5. Каждый из этих растворов подается насосами высокого давления в подогреватель 7. Поступая в него по одному трубопроводу, растворы при этом хорошо смешиваются. Обогрев трубчатки подогревателя производится дымовыми газами, полученными при сгорании топливного газа. Смесь, нагретая в подогревателе до 350 °C, поступает затем в трубчатый реактор 8 с омедненными внутри трубами во избежание коррозии.
В реакторе протекает основная реакция получения фенола
C6H5Cl+2NaOH > C6H5ONa + NaCl+H20
и побочные реакции образовании дифенилоксида п оксидифенила:
C6H5ONa+C6H5Cl > (C6H5)2O+NaCl;
2C6H5Cl+2NaOH >С6Н5С6Н4ОН+2NaCl+H20
Выход дифенилоксида в равновесном состоянии составляет около 10% от веса исходного хлорбензола. С целью уменьшения расхода хлорбензола на образование дифенилоксида в него добавляют некоторое количество дифенилоксида. Избыток дифенилоксида будет гидролизоваться в фенол по реакции:
NaOН
(С6Н5)2О + Н20 > 2С6Н5ОН
Поэтому вводимый в реакцию хлорбензол более полно будет превращаться в фенолят натрия и расход его на побочные реакции уменьшится.
Реакция хлорбензола с едким натром экзотермична. Тепла, выделяющегося при реакции, достаточно для поддержания необходимой температуры и, при хорошей теплоизоляции, компенсации потерь в окружающее пространство.
Продукты реакции охлаждаются в змеевике испарителя 11, отдавая свое тепло на испарение воды и дифенилоксида, и дросселируются до атмосферного давления, поступая в полость испарителя. Отогнанный дифенилоксид с парами воды конденсируется в конденсаторе 9 в собирается в сборнике 14. После отделения от воды (на схеме не показано) дифенилоксид частично возвращается в напорный бак 6. Остальное количество идет на очистку и выпускается как готовый продукт, используемый в качестве составной части высокотемпературного органического теплоносителя.
Фенолят натрия стекает из испарителя в сборник 15, из которого центробежным насосом подается в скруббер 10.
Вниз этого скруббера вводится углекислый газ для нейтрализации фенолята по реакции:
2C6H5ONa+C02+H20 > 2C6H5OH+Na2C03
Вытекающие из скруббера 10 продукты реакции расслаиваются в разделительном сосуде 12. Фенольный слой нейтрализуется серной кислотой в нейтрализаторе 16 и отбирается на разгонку с целью выделения товарного фенола. Нижний слой, из разделительного сосуда, подфенольная вода, обрабатывается в каустификаторе 17 гидратом окиси кальция. Образующийся при этом по реакции
Na2C03+Ca (OH)2 > CaCO3+2NaOH
углекислый кальций отфильтровывается на фильтрпрессе 18. Фильтрат упаривается в выпарном аппарате 13.
Выпавшая из раствора поваренная соль отфильтровывается на путч-фильтре 19.
Фильтрат, содержащий едкий натр и некоторое количество фенола, перекачивается в напорный бак 1 для регенерированного едкого натра.
Основные параметры производства
Концентрация едкого натра в растворе перед смешением 15—20%
Отношение едкого натра и хлорбензола в молях от 2,3: 1 до 2,5:1
Содержание дифенилоксида в смеси, поступающей в реактор 0—8%
Давление в подогревателе и реакторе 8 200 атм.
Температура в подогревателе и реакторе 350°С
Температура реакционной массы перед дроссельным вентилем у испарителя 150—200°С Давление в испарителе около атмосферного
На 1 г фенола расходуется:
хлорбензола 1,5 т едкого натра 0,61 г
углекислого газа (30%) 1690 м3
серной кислоты 0,07 т Схема 2. Технологическая схема производства фенола через хлорбензол Обозначения на схеме 2:
1, 3, 4, 6 — напорные баки,
2,5 — смесители,
7 — подогреватель,
8 — реактор,
9 — конденсатор,
10 — скруббер,
11 — испаритель,
12 — разделительный сосуд,
13 — выпарной аппарат,
14, 15, 19 — сборники,
16 — нейтрализатор,
17 — каустификатор,
18 — фильтр-пресс.
фенол химический вещество бензол
3. ПРОИЗВОДСТВО ФЕНОЛА ОКИСЛИТЕЛЬНЫМ ХЛОРИРОВАНИЕМ БЕНЗОЛА
(Схема 3)
По описываемой схеме производство синтетического фенола состоит из 2-х стадий:
1) окислительного каталитического хлорирования бензола хлористым водородом;
2) каталитического гидролиза, получающегося на первой стадии хлорбензола водяным паром.
Обе стадии процесса проводятся непрерывно в паровой фазе. Химизм получения фенола на первой стадии процесса выражается уравнениями:
С6Н6+0,5О2+НС1 > C6H5Cl+H2O,
С6Н5С1+Н20 > С6Н5ОН+НС1
Образовавшийся по реакции (2) хлористый водород возвращается на первую стадию процесса; расход его определяется потерями в производстве, тогда как бензол и кислород непосредственно расходуются на получение фенола по суммарной реакции:
С6Н6+0,5О2 > С6Н5ОН Для приготовления исходной реакционной смеси пары бензола, идущие из аппарата 24, поступают в перегреватель паров 36, обогреваемый путем сжигания газообразного топлива. Перегретые пары бензола поступают в среднюю часть смесителя паров 1.
Свежая и обратная соляная кислота из напорного бака 2 поступает в испаритель 27. Образовавшиеся в нем пары соляной кислоты смешиваются в верхней части смесителя 1 с воздухом и в средней части с парами бензола. Получившаяся при этом паро-газовая смесь с температурой около 210 °C поступает на хлорирование в трубчатый контактный аппарат 37, в межтрубном пространстве которого циркулирует высокотемпературный теплоноситель.
При окислительном хлорировании с катализатором, состоящим из окиси алюминия, пропитанной раствором хлорной меди, в контактном аппарате протекают реакции образования хлорбензола:
4НС1+02 >2С12+2Н20,
С6Н6 + С12 > С6Н5С1+НС1
В результате побочных реакций образуется также некоторое количество полихлорбензолов, окиси углерода и углекислого газа.
Реакционная смесь орошается в парциальном конденсаторе 4 бензолом и водой из сборника 39. Сконденсировавшиеся хлорбензол, бензол, полихлориды, хлористый водород и вода спускаются в сепаратор 40. Верхний слой жидкости, состоящий в основном из хлорбензола, подается центробежным насосом вниз нейтрализационной колонны 35, орошаемой 10−12%-ным раствором щелочи из напорного бака 3. Нейтрализованный хлорбензол промывается водой в колонне 6 и стекает в сборник 41. Пары, поднимающиеся из нейтрализационной колонны 35, конденсируются в конденсаторе 5. Газовая фаза сбрасывается через фазоразделитель 7. Отслоившийся бензол уходит сверху сепаратора 8, снизу его вытекает в сборник 39 вода с небольшой примесью бензола.
Из сборника 41 хлорбензол центробежным насосом подается в дистилляционную колонну 9, предварительно нагреваясь в конденсаторе 12. Выходящие из верхней части пары бензола конденсируются в конденсаторе 10, конденсат направляется в сборник обратного бензола. Кубовая жидкость колонны 10 центробежным насосом подается в дистилляционную колонну 11 для отделения от полихлорбензолов. Пары хлорбензола конденсируются в конденсаторе 12. Окончательная конденсация и охлаждение конденсата происходит в конденсаторе-холодильнике 13. Конденсат собирается в сборнике 44, откуда частично подается на орошение колонны 11. Кубовый остаток из колонны 11, состоящий в основном из полихлорбензолов, перекачивается центробежным насосом в колонну 15 для окончательной отгонки хлорбензола от полихлорбензолов. Пары хлорбензола конденсируются в конденсаторе-холодильнике 13; образовавшийся конденсат поступает в сборник 44. Полихлорбензолы выпускаются из кубовой части колонны 15 в сборник 45 и выводятся из системы. Дистилляционные колонны 9, 11 и 15 обогреваются кипятильниками 42, 43 и 46.
Хлорбензол из сборника 44 и кислая вода из сепаратора 40 центробежными насосами подаются на орошение конденсационной башни 18, в которой происходит отмывка хлористого водорода от продуктов пиролиза. Вода и хлорбензол испаряются и вместе с парами, проходящими через башню, поступают для нейтрализации следов соляной кислоты в колонну 32, орошаемую горячим раствором едкого натра. Циркуляция щелочи в колонне идет через сборник 52.
Азеотропная смесь паров воды, хлорбензола, фенола и инертные газы направляются в фенольный скруббер 21, орошаемый горячей водой. Вытекающая из скруббера вода с некоторым содержанием фенола собирается в сборнике 53 и центробежным насосом через холодильник 54 подается в экстракционную колонну 22. Паровая фаза с температурой 90—95°С выходит из скруббера 21 сверху, подогревается в подогревателе 20 и циркуляционным турбокомпрессором через теплообменник 30 нагнетается в перегреватель 36. В перегревателе паровая фаза, представляющая собой азеотропную смесь паров воды и хлорбензола, нагревается до температуры 420 °C и поступает на вторую стадию процесса—каталитический гидролизКонтактный аппарат для гидролиза—трубчатый. Катализатор—комплексная соль диаммоний фосфата и хлорной меди—помещается между перфорированными трубками двух диаметров. В контактном аппарате 28 протекает основная реакция С6Н5С1+Н20 > С6Н5ОН+НС1.
В результате побочных реакций на катализаторе отлагается углерод в виде сажи с примесью смолы, активность катализатора при этом понижается, поэтому требуется его регенерация, заключающаяся в выжигании углерода горячим воздухом. Чтобы избежать периодичности в работе всей стадии гидролиза, устанавливается несколько контактных аппаратов 28 (на схеме показан один аппарат). Реакционная масса из контактного аппарата 28 проходит через теплообменник 30 и поступает в скруббер 31 для улавливания хлористого водорода. Орошается скруббер 5%-ной соляной кислотой из сборника 50, в который она поступает из конденсационной башни 18 после охлаждения в холодильнике 51. Образовавшаяся в скруббере 31 соляная кислота, содержащая некоторое количество фенола, охлаждается в холодильнике 49, стекает в сборник 48 и подается центробежным насосом в напорный бак 14. Из него соляная кислота стекает в экстракционную колонну 16, вниз которой поступает бензол из напорного бака 17. Обесфеноленная соляная кислота собирается в сборник 47. Бензол с содержанием фенола выходит сверху экстрактора и направляется на промывку. Вниз экстракционной колонны 22 поступает бензол из напорного бака 19. Бензольный раствор фенола собирается в сборник 55, из которого центробежным насосом подается в напорный бак 23. Обесфеноленная вода после удаления из нее бензола (на схеме не показано) направляется на орошение скруббера 21. Из напорного бака 23 бензольный раствор фенола поступает в кипятильник 33. Бензол отгоняется в ректификационную колонну 24, орошаемую бензолом, идущим со склада; пары бензола уходят в перегреватель 36. Кубовый остаток из кипятильника и колонны 24, состоящий из сырого бензола, собирается в сборник 56, откуда центробежным насосом направляется в колонну 60 на дистилляцию. В этой колонне пары бензола отбираются сверху, конденсируются в конденсаторе 25, конденсат частично возвращается на колонну в виде флегмы, частично выводится из системы после барометрического затвора. Кубовая жидкость из колонны 60 подается в колонну 26. Пары фенола конденсируются в конденсаторе 29. Через барометрический затвор товарный фенол поступает в сборник 59 и выводится из системы. Орошение дистилляционной колонны 26 производится фенолом, поступающим со склада. Обогрев колонны 60 и 26 осуществляется паром через кипятильники 57 и 58.
Основные параметры производства
Температура паро-газовой смеси перед поступлением в контактный аппарат 37 около 210 °C Температура в контактном аппарате 250 °C Катализатор—хлорная медь на окиси алюминия.
За проход около 7% бензола превращается в хлорбензол.
Температура в парционном конденсаторе 105°С
Температура в контактном аппарате 28 420 °C Катализатор—комплексная соль диаммоний фосфата и хлорной меди.
Цикл работы контактного аппарата 28 4 часа
1) рабочий цикл 3 часа,
2) продувка паром в цикл 10 мин,
3) продувка воздухом 40 мин,
4) продувка паром в атмосферу 10мин.
Концентрация возвратной соляной кислоты 17—18%
Температура паров в аппаратах 3, 8, 21 не менее 90—95°С Схема 3. Технологическая схема производства фенола окислительным хлорированием бензола Обозначения на схеме 3:
1—смеситель паров,
2, 3, 14, 17, 19, 23—напорные баки,
4—парциальный конденсатор,
5, 10, 12, 25, 29—конденсаторы,
6—промывная колонна,
7—фазоразделитель,
8, 40—сепараторы,
9, 11, 15, 26, 60—дистилляционные колонны,
13— конденсатор-холодильник,
16, 29— экстракционные колонны,
18— конденсационная башня,
20—подогреватель,
21—фенольный скруббер,
24 —ректификационная колонна,
27—испаритель,
28, 57—контактные аппараты,
30— теплообменник,
31,35—скрубберы,
32-нейтрализационная колонна,
33, 42, 43, 46, 57, 58— кипятильники,
36— перегреватель,
35—фильтр,
39, 41, 44, 45, 47, 48, 50, 52, 53, 55, 56, 59- сборники,
34, 61 —барометрические затворы,
49, 51, 54—холодильники.
4.ПРОИЗВОДСТВО ФЕНОЛА ЧЕРЕЗ ИЗОПРОПИЛБЕНЗОЛ
(Схема 4)
Описываемый метод производства используется для одновременного получения двух важных технических продуктов: фенола и ацетона. Это производство, состоящее из двух фаз,
1) окисления изопропилбензола,
2) разложения гидроперекиси изопропилбензола осуществляется следующим образом.
Изопропилбензол из сборника 18 вместе с катализатором, идущим во всасывающую линию центробежного насоса, подается через подогреватель 13 в колонну окисления 2. В ней протекает основная реакция получения гидроперекиси изопропилбензола. Реакция окисления изопропилбензола имеет цепной характер.
Суммарно это выражается уравнением:
С6Н5-С3Н7+02 > С6Н6С (СН3)2— О — ОН В реакционной массе, кроме образовавшейся перекиси изопрепилбензола и непрореагировавшего изопропилбензола, присутствуют продукты побочных реакций—дпметилфенилкарбинол, ацетофенон б —метилстирол, метиловый спирт, диметилдифенилбутан и др.
Газовая фаза, содержащая пары изопропилбензола, выводится из колонны 2 сверху. В конденсаторе 1 и холодильнике 7 происходит конденсация паров и охлаждение сконденсировавшегося изопропилбензола, увлеченного газовой фазой. Реакционная масса, выходящая снизу колонны окисления, отдает свое тепло в подогревателе изопропилбензола 13 и поступает в дистилляционную колонну 14, где происходит отделение части непрореагировавшего изопропилбензола, пары которого конденсируются в холодильнике 3. В дистилляционной колонне 15 окончательно отделяется непрореагировавший изопропилбензол, пары его конденсируются в холодильнике 4. Изопропилбензол после холодильников 3 и 4 снова возвращается на окисление, поступая в сборник изопропилбензола 18. Дистилляционные колонны 14 и 15 работают под вакуумом. Гидроперекись изопропилбензола после охлаждения в холодильнике 16 собирается в сборнике 19. Разложение ее осуществляется в реакторе 8 по реакции:
Н2SO4
С6Н5С (СН3)2—О—ОН > C6H6OH + CH3-CO-CH,
Катализатором разложения служит серная кислота, которая подается во всасывающую линию циркуляционного насоса и вместе с циркуляционной жидкостью поступает в реактор. Реакционная масса из реактора 8 проходит в холодильник 9, так как все тепло реакции в реакторе снять не удается. Охлажденная реакционная масса частично с помощью центробежного насоса снова направляется в реактор, а частично поступает в нейтрализатор 20, где нейтрализуется 15%-ным раствором щелочи. Нейтрализованная реакционная масса из сборника 21 центробежным насосом подается в колонну ректификации реакционной массы 5 для отделения ацетона, пары которого конденсируются в дефлегматоре 6. Конденсат частично возвращается в колонну в виде флегмы, частично собирается в сборнике ацетона 10. Из кубовой части колонны 5 вытекает жидкость, состоящая из фенола и продуктов побочных реакций процесса, в собирается в сборнике 22. Центробежным насосом жидкость из него подается на ректификационную колонну 11. Пары б —метилстирола, воды и небольшого количества фенола конденсируются в дефлегматоре 6 и направляются на отделение б —метилстирола (на схеме не показано). Из кубовой части колонны 11 вытекает фенол-сырец, который собирается в сборнике 23. Получение товарного фенола производится в ректификационной колонне 12. Пары фенола отбираются сверху колонны. Полученный в конденсаторе 6 конденсат частью отбирается в сборник 24 как готовый продукт—товарный фенол, частью идет на орошение колонны 12. Кубовый остаток, состоящий из смеси дпметилфенилкарбинола, ацетофенона и других примесей, выводится из системы и направляется на дальнейшее разделение. Обогрев ректификационных колонн 5, 11, 12, работающих под вакуумом, осуществляется с помощью кипятильников 17.
Основные параметры производства
Температура в колонне окисления изопропилбензола 120°С Окисление производится воздухом.
Температура в колонне 14 вверху 38—60°С Температура в колонне 14 в кубе 82 —85°С Температура в колонне дистилляции 15 92—95°С Остаточное давление в колонне дистилляции 10 мм рт. ст.
Катализатор разложения гидроперекиси серная кислота Выход фенола и ацетона—в соотношении 3: 2 (по весу) Схема 4. Технологическая схема производства фенола через изопропилбензол На схеме 4 обозначено:
1—конденсатор,
2—колонна окисления,
3, 4, 7, 9, 16 — холодильники,
5—колонна ректификации реакционной массы,
6—дефлегматор,
8—реактор,
10—сборник ацетона,
11— ректификационная колонна,
12 — колонна ректификации фенола,
13— подогреватель,
14,15 — дистилляционные колонны
17— кипятильник,
18—сборник изопропилбензола,
19-сборник гидроперекиси изопропилбензола,
20-нейтрализатор,
21— сборник нейтрализованной реакционной массы,
22— сборник кубовой жидкости,
23—сборник сырца-фенола.
1. Грибов А. А. и Касаткин Н. М., Основные процессы в производстве полупродуктов, ОНТИ, 1936.
2. Амиантов Н. И., Химия и технология полупродуктов и красителей, ГХИ, 1947
3. Вольфкович С. И., Роговин 3 А., Общая химическая технология, т. 2, ГХИ, 1959.
4. Frank-Vogel, Die Herslellung von Zwischenprodukten und Farbstoffen, Halle. 1955.
5. Воронноп H.H., Основы синтеза промежуточных продуктов и красителей, ГХИ, 1955
6. Кружалов Б. Д., Сергеев П. С, Производство фенола и ацетона, Химическая наука и промышленность, 3, том 1, 1956.
7. Основы технологии нефтехимического синтеза под редакцией А. И. Динцесан, Л. А. Потоловского, Гостоптехиздат, 1960.