Разработка технологического процесса восстановления вторичного вала коробки передач автомобиля КамАЗ
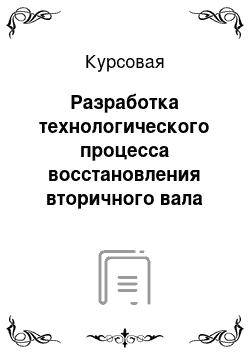
На переднем конце вала посажен подшипник с приставным внутренним кольцом, все шестерни вала установлены на роликовых подшипниках, из которых подшипник шестерни четвертой передачи насыпной, без сепаратора. Шестерни четвертой и третьей передач в осевом направлении закреплены упорным кольцом с внутренними шлицами, которое установлено в выточке вала таким образом, что его шлицы расположены против… Читать ещё >
Разработка технологического процесса восстановления вторичного вала коробки передач автомобиля КамАЗ (реферат, курсовая, диплом, контрольная)
Федеральное агентство по образованию Федеральное государственное образовательное учреждение
Среднего профессионального образования
" ИЖЕВСКИЙ ГОСУДАРСТВЕННЫЙ ПОЛИТЕХНИЧЕСКИЙ КОЛЛЕДЖ"
(ФГОУ СПО «ИГПК»)
ПОЯСНИТЕЛЬНАЯ ЗАПИСКА
по дипломному проекту
на тему: РАЗРАБОТКА ТЕХНОЛОГИЧЕСКОГО ПРОЦЕССА ВОСТАНОВЛЕНИЯ ВТОРИЧНОГО ВАЛА КОРОБКИ ПЕРЕДАЧ АВТОМОБИЛЯ КАМАЗ.
Выполнил: студент гр. ТОРА-56П Музафаров С.Р.
Руководитель: Ижовкин А.П.
ИЖЕВСК 2010 г.
Оглвление
- Введение
- 1.1 Анализ конструкции вторичного вала КП КаМАЗ
- 1.2 Разборка вторичного вала КП КаМАЗ
- 1.3 Сборка вторичного вала КП КаМАЗ
- 2.1 Карта дефектации вторичного вала КП КаМАЗ
- 3.1 Выбор и обоснование способов восстановления вторичного вала КП
- 4.1 План технологических операций по устранению дефектов
- 5.1 Выбор оборудования приспособления и инструмента
- 5.2 Расчет режимов и норм времени по операциям
- 5.3 Расчет технических норм времени
- 6.1 Проектирование и расчет производственного участка
- Расчет количества рабочих
- 6.3 Расчет количества оборудования
- 6.4 Расчет площади
- 6.5 Планировка оборудования и рабочих мест
- 6.6 Организация транспортировки детали
- 6.7 Организация технического контроля
- 7.1 Техника безопасности, противопожарная защита и промышленная санитария
- Заключение
- Литература
- Приложение
- Измерительный инструмент.
Постоянная необеспеченность ремонтного производства запасными частями является серьёзным фактором снижения технической готовности автомобильного парка. Расширение же производства новых запасных частей связано с увеличением материальных и трудовых затрат. Вместе с тем около 75% деталей, выбраковываемых при первом капитальном ремонте автомобилей, являются ремонтопригодными, либо могут быть использованы вообще без восстановления. Поэтому целесообразной альтернативой является вторичное использование изношенных деталей, восстанавливаемых в процессе ремонта автомобилей и его агрегатов. Из ремонтной практики известно, что большинство выбракованных по износу деталей теряют не более 1−2% исходной массы. При этом прочность деталей практически сохраняется. Например, 95% деталей двс выбрасывают при износах, не превышающих 0,3 мм, и большинство из них могут быть вторично использованы после восстановления. С позиции материалоёмкости воспроизводства машин экономическая целесообразность ремонта обусловлена возможностью повторного использования большинства деталей как годных, так и предельно изношенных. Это позволяет осуществлять ремонт в более короткие сроки с меньшими затратами металла и других материалов по сравнению с затратами при изготовлении новых машин. Восстановление деталей стало одним из важнейших показателей хозяйственной деятельности крупных ремонтных, специализированных предприятий. Создана фактически новая отрасль производства — восстановление изношенных деталей. Вторичное потребление деталей значительно больше, чем потребление новых запасных частей. Так, например, восстановленными блоками двигателей пользуются в 2,5 раза больше, чем новыми, коленчатыми валами в 1,9 раза, картерами коробок передач в 2,1 раза. Себестоимость восстановления для большинства восстанавливаемых деталей не превышает 75% стоимости новых, а расход материалов в 15 — 20 раз ниже, чем на их изготовление. Целенаправленная работа заводов — изготовителей по повышению ресурса рам и кабин, доведению его до срока службы автомобиля способствует резкому сокращению сферы применения капитального ремонта (КР) полнокомплектных автомобилей. В последнее время он неуклонно снижается, а для грузовых автомобилей предусмотрен КР только агрегатов. Эта тенденция вызывает изменение функций авторемонтных заводов, которые становятся предприятиями по КР агрегатов. Организационно-техническая перестройка АТП в последние годы ускорилась в связи с изменением социально-экономических условий хозяйствования в нашей стране. Наиболее развитой в нашей стране является фирменная система акционерного общества КамАЗ. Она имеет в своём составе 121 автоцентр и 14 заводов по ремонту агрегатов КамАЗ, из них 9 находятся в Набережных Челнах, 186 субъектов дилерской сети по территории стран СНГ. В период наибольшего развития годовая производственная программа завода по ремонту, достигла 50 тыс. двигателей. На сегодняшний день производственная мощность в год на заводе составляет: 50 тыс. штук грузовых автомобилей, 75 тыс. штук силовых агрегатов. Такая программа позволяет применять высокопроизводительное технологическое оборудование и достигать высокого качества ремонта. Автоцентры в зоне своего действия обеспечивают предприятия запасными частями, производят сбор и доставку ремонтного фонда и отремонтированных изделий, в зависимости от производственных возможностей выполняют централизованное техническое обслуживание и текущий ремонт автомобилей КамАЗ и другие услуги. Дальнейшее эффективное развитие АТП базируется на идеях и принципах, которые создаются в процессе изготовления новой техники заводами-изготовителями, выполняющими услуги по централизованному ТО и ремонту этой техники. За рубежом уделяют большое внимание вопросам технологии и организации восстановления деталей. В высокоразвитых странах — США, Англии, Японии, ФРГ — ремонт в основном осуществляется на предприятиях-изготовителях автомобилей. Восстанавливают дорогостоящие, металлоёмкие, массовые автомобильные детали — коленчатые и распределительные валы, гильзы цилиндров, блоки, шатуны, тормозные барабаны. Ремонтной базой являются моторои агрегаторемонтные предприятия фирм-изготовителей новых машин. Например, в США восстановлением деталей занято около 800 фирм и компаний. Ремонтным фондом служат детали со списанных автомобилей, которые поставляют фирмы-производители, специализирующиеся на переработке негодных к эксплуатации автомобилей. В США удовлетворение потребности автотранспортных средств в запасных частях обеспечивается на 25% в результате восстановления деталей. Автомобильный транспорт, являясь составной частью единой транспортной системы, по сравнению с другими видами транспорта, имеет более высокие темпы развития. В настоящее время ежегодный прирост мирового парка автомобилей равен 10−12 млн. единиц, а его численность более 400 млн. единиц. Каждые четыре из пяти авто. общего мирового парка это легковые и на их долю приходится более 60% пассажиров, перевозимых всеми видами транспорта. Помимо тех неоспоримых удобств, которые легковой автомобиль создаёт в жизни человека, очевидно общественное значение массового пользования личными автомобилями: увеличивается скорость при поездках; сокращается число штатных водителей; облегчается доставка городского населения на работу и т. д. Однако процесс автомобилизации не ограничивается только увеличением парка автомобилей. Быстрые темпы развития автотранспорта обусловили определённые проблемы, для решения которых требуются: научный подход и значительные материальные затраты. Основными из них являются: увеличение пропускной способности улиц, строительство дорог, стоянок, гаражей, восстановление деталей, отработавших свой ресурс, ремонт подвижного состава, обеспечение безопасности движения и охраны окружающей среды, строительство АТП и Сто, складов, АЗС и других предприятий. Эти и другие факторы обусловили создание новой отрасли промышленности — автотехобслуживания. Система «Автотехобслуживания» в настоящее время имеет достаточно мощный производственный потенциал. Дальнейшее укрепление системы должно предусматривать не только ввод в эксплуатацию новых объектов, но и реконструкцию старых объектов, интенсификацию производства, рост производительности труда и фондоотдачи, улучшение качества услуг за счёт широкого внедрения новой техники передовой технологии, рациональных форм и методов организации производства и труда. Важнейшими направлениями совершенствования Т. О и ремонта грузовых и легковых автомобилей являются: применение прогрессивных технологических процессов; совершенствование организации и управления производственной деятельностью; повышение эффективности использования основных производственных фондов и снижение материалои трудоёмкости отрасли; применение новых технологий; повышение качества услуг и разработка материального обеспечения. Авто. транспорт постоянно развивается. Расширяется применение газового оборудования. Это предъявляет повышенные требования к улучшению условий труда, к обеспечению безопасности сотрудников и сохранению их здоровья. Управление деятельностью СТО, улучшению условий труда, повышение эффективности трудозатрат, является одной из задач тех. эксплуатации авто. транспортных средств. В осуществлении указанных задач значительная роль принадлежит автотранспортным предприятиям. Автомобильная промышленность систематически работает над улучшением технологии производства и совершенствованием конструкции подвижного состава, обеспечиванием безотказности, долговечности и ремонтопригодности. Задачи службы технической эксплуатации АТП заключаются в постоянном поддержании высокой технической готовности подвижного состава, обеспечением его работоспособности в течение установленных сроков наработки. Для выполнения поставленных задач необходимо широко использовать средства технической диагностики, максимально механизировать производственные участки и цеха технического обслуживания и текущего ремонта автомобилей, оснащать их подъёмно-транспортными механизмами и контрольно-регулировочными приборами, совершенствовать технологию технического обслуживания и текущего ремонта, создавать требуемые производственно-бытовые и санитарно-гигиенические условия труда ремонтных рабочих.
1.1 Анализ конструкции вторичного вала КП КаМАЗ
Рис.1 Вторичный вал КП автомобиля КаМАЗ
Вторичный вал КПП выполнен из стали 30 ХГТ ГОСТ 4543–71.
Поверхность вала имеет твердость от 45 до 57НRСэ.
Габаритные размеры вала: наибольший диаметр — 65 мм,
длина вала — 493 мм.
Масса вала 2,75 кг.
Вал устанавливается в модели КП различных комплектаций и в отдельные комплектации КП 141. Вал имеет две проточки и разные по толщине шлицы в месте установки синхронизатора 4−5 передачи, что необходимо для предотвращения самовыключения передач. Вал изготавливается на автоматической линии, обеспечивающей выполнение техпроцесса, стабильность размеров, высокую точность и производительность. Использующаяся для изготовления вала сталь обеспечивает работоспособность КП в объеме не менее 350 тыс. км и при увеличении нагрузки от двигателя более чем в 3 раза относительно номинальной.
вторичный вал восстановление инструмент
Рис.2 Вторичный вал в сборе
1 — стопорное кольцо; 2 — передний роликовый подшипник; 3 — синхронизатор четвертой и пятой передач; 4, 15 — упорные шайбы; 5 — ролики подшипника четвертой передачи; 6 — втулка зубчатого колеса четвертой передачи; 7 — зубчатое колесо третьей передачи; 8 — роликовый подшипник; 9 — синхронизатор второй и третьей передач; 10 — зубчатое колесо второй передачи; 11 — зубчатое колесо заднего хода; 12 — муфта включения первой передачи и заднего хода; 13 — втулка зубчатого колеса первой передачи; 14 — зубчатое колесо первой передачи; 16 — вторичный вал; 17 — втулка зубчатого колеса заднего хода; 18 — зубчатое колесо четвертой передачи; 19 — пружина; 20 — втулка зубчатого колеса четвертой передачи; 21 — замковая шпонка
Все зубчатые колеса вала установлены на роликовых подшипниках, из которых подшипник зубчатого колеса четвертой передачи насыпной, без сепаратора.
Зубчатые колеса четвертой 18 и третьей 7 передач в осевом направлении закреплены упорной шайбой 4 с внутренними шлицами, которая установлена в выточке вала так, что ее шлицы расположены против шлицев вала, и застопорена от проворачивания подпружиненной замковой шпонкой 21.
По оси вала просверлен канал для подвода смазочного материала по радиальным отверстиям к подшипникам зубчатых колес. Масло в канал подается маслонагнетающим устройством, расположенным на первичном валу.
На переднем конце вала посажен подшипник с приставным внутренним кольцом, все шестерни вала установлены на роликовых подшипниках, из которых подшипник шестерни четвертой передачи насыпной, без сепаратора. Шестерни четвертой и третьей передач в осевом направлении закреплены упорным кольцом с внутренними шлицами, которое установлено в выточке вала таким образом, что его шлицы расположены против шлицев вала, и застопорено от проворачивания подпружиненной замковой шпонкой. По оси вала просверлен канал для подвода смазки по радиальным отверстиям к подшипникам шестерен. Масло в канал подается маслонагнетающим устройством, расположенным на ведущем валу.
Для безударного переключения второй, третьей, четвертой и пятой передач имеется два пальчиковых синхронизатора инерционного типа.
Химический состав стали 30ХГТ
Химический элемент: %
Кремний (Si) 0.17−0.37
Марганец (Mn) 0.80−1.10
Медь (Cu), не более 0.30
Никель (Ni), не более 0.30
Сера (S), не более 0.035
Титан (Ti) 0.03−0.09
Углерод (C) 0.24−0.32
Фосфор (P), не более 0.035
Хром (Cr) 1.00−1.30
Физические свойства стали 30ХГТ:
Температура испытания,°С20 100 200 300 400 500 600 700 800 900
Модуль нормальной упругости, Е, ГПа212 202 195 189 174 169 157 138 132
Модуль упругости при сдвиге кручением G, ГПа 8379 76 74 67 66 61 53 51
Коэффициент теплопроводности Вт/ (м ?°С) 36 37 36 34 33 31 29 28 28
Температура испытания,°С20 — 10 020 — 20 020 — 30 020 — 40 020 — 50 020 — 60 020 — 70 020 — 80 020 — 90 020 — 1000
Коэффициент линейного расширения (a, 10−6 1/°С) 10.512.012.7 13.3 13.8 14.0
Удельная теплоемкость (С, Дж/ (кг ?°С)) 495 508 525 537 567 621 251 072
Технологические свойства стали 30ХГТ:
Температура ковки — начала 1220, конца 800. Сечения до 200 мм охлаждаются в зольниках, более 200 мм — в печах.
Свариваемость — ограниченно свариваемая. Способы сварки: РДС, КТС. Рекомендуется подогрев и последующая термообработка.
Обрабатываемость резанием — после нормализации при НВ 364 и sB = 860 МПа Ku тв. спл. = 0.45, Ku б. ст. = 0.25.
Склонность к отпускной способности — склонна
Флокеночувствительность — не чувствительна
1.2 Разборка вторичного вала КП КаМАЗ
Рис.3 Разборка вторичного вала
1. Зажмите вторичный вал в тисках со стороны выходного вала Используйте алюминиевые «щечки» .
Рекомендация при сборке и разборке: позиционирование и вращение вала производите только при помощи специального
Инструмента. Предварительно вытолкните трубку для масла.
2. Снимите упорное кольцо (1) и разборное кольцо (2).
3. Инструмент захват заведите во внутреннее кольцо подшипника (3) и укрепите до плотной посадки на роликах подшипника при помощи рифленого кольца. Теперь привинтите основной инструмент и снимите внутреннее кольцо подшипника.
4. Снимите осевую шайбочку (4).
5. Зажмите вторичный вал в тисках в цапфах подшипника со стороны первичного вала. Применяйте алюминиевые «щечки» .
6. Снимите прижимную шайбу (5).
УКАЗАНИЕ: при прямозубом исполнении прижимной шайбы (5) нет.
7. Выньте из кольцевого паза упорное кольцо (6).
8. Косозубую шестерню для заднего хода (7) подхватить двух — или трехзахватным съемником и снять вместе с внутренним кольцом
роликоподшипника (8); используйте проставку.
9. Снимите комплект игольчатых роликов (9).
10. Косозубую шестерню 1-ой передачи (10) подхватите двух — или трехзахватным съемником и снимите вместе с втулкой- (11) и зубчатой муфтой (12) (используйте проставку).
11. Снимите игольчатый роликоподшипник (13).
Рис.4 Разборка вторичного вала
12. Снимите дисковую зубчатую муфту (14) спаренного конического синхронизатора 1-ой или 5-ой передачи.
13. Снимите внутреннее кольцо (15).
14. Снимите промежуточное кольцо (16).
15. Снимите наружное кольцо (17).
16. Снимите скользящую муфту (18), будьте внимательны — выпадут фиксаторы и прижимные пружины, держите внизу наготове салфетку.
17. Снимите соединительные детали (19).
18. Двух — или трехзахватный съемник надеть на косозубую шестерню 2-ой передачи (21). Снять косозубую шестерню с втулкой (22),
дисковой зубчатой муфтой (23), внутренним кольцом (24), промежуточным кольцом (25), наружным кольцом (26) и ступицей
синхронизатора (20), (используйте проставку).
19. Снимите игольчатые роликоподшипники (27).
20. Зажмите вторичный вал со стороны выходного вала.
21. Подхватите скользящую муфту (28) двух — или трехзахватным съемником и снимите кольцо синхронизатора (29), зубчатую муфту (30), роликоподшипник (31) и косозубую шестерню (32) (используйте проставку).
УКАЗАНИЕ: снимая скользящую муфту, будьте внимательны, фиксаторы (33) и прижимные пружины (34) могут выпасть; используйте салфетку.
22. Удалите фиксаторы и пружины. Подхватите косозубую шестерню 3-ей передачи (35) двух — или трехзахватным съемником и снимите вместе с роликоподшипником (36), ступицей синхронизатора (37), кольцом синхронизатора (38) и зубчатой муфтой (39).
(Используйте проставку)
23. Снимите игольчатые роликоподшипники (40).
1.3 Сборка вторичного вала КП КаМАЗ
Рис.5 Сборка вторичного вала КП
1. Зажмите вторичный вал (1) со стороны первичного вала.
2. Слегка смажьте игольчатый роликоподшипник (2) и насадите на вторичный вал.
3. Косозубую шестерню (3), 2-я передача, насадите на вторичный вал, чтобы шлицы для зубчатой муфты синхронизатора смотрели в сторону выходного вала.
4. Проверьте предел износа деталей синхронизатора (см. главу 6). 5. Дисковую зубчатую муфту (4) насадите на шлицы косозубой шестерни (3). Слегка выпуклое внутреннее зацепление дисковой зубчатой муфты показывает в сторону выходного вала.
6. Внутреннее кольцо (5) насадить на дисковую зубчатую муфту. Язычки должны смотреть в сторон}' выходного вала.
7. Промежуточное кольцо (6) насадить таким образом, чтобы язычки попали в вытачки дисковой зубчатой муфты.
8. Насадить наружное кольцо (7). Язычки должны смотреть в сторону выходного вала.
9. При помощи трех соединительных вставок (8) выровняйте язычки наружного кольца и язычки внутреннего кольца. Спозиционируйте язычки внутреннего и наружного колец внахлест, чтобы потом
соединительные вставки попали в вытачки ступицы синхронизатора (9) и были над язычками. После того, как все будет согласовано, удалите вставки.
10. Ступицу синхронизатора (9) нагреть примерно до 120 гр. по Цельсию и насадить на шлицы вторичного вала. Спозиционированные язычки должны быть при этом в вытачках ступицы синхронизатора. Выступы наружного кольца должны входить в вытачки ступицы синхронизатора. Проворачивать синхронизатор можно при помощи пластмассовой оправки.
11. Осевой зазор косозубой шестерни (3) должен составлять по меньшей мере 0,20 мм.
12. Вставить соединительные вставки (8) в ступицу синхронизатора (9).
13. Скользящую муфту (10) провести над ступицой синхронизатора и наружным кольцом и подвести к дисковой зубчатой муфте.
14. Вставить новые соединительные пружины (11) и имеющиеся фиксаторы (12), правильно расположить их в ступице синхронизатора.
Рис.6 Сборка вторичного вала КП
УКАЗАНИЕ: " СИНХРОНИЗАЦИЯС ДВОЙНЫМКОНУСОМ" .
Правильно вставьте фиксаторы в корпус синхронизатора.
15. При помощи подходящего инструмента подправьте положение фиксаторов в ступице синхронизатора и в скользящей муфте.
16. Насадите наружное кольцо (13). Язычки должны зацепляться в соединительное кольцо, а выступы в вытачки ступицы синхронизатора.
17. Вставьте промежуточное кольцо (14). Язычки должны смотреть в сторону выходного вала. Вставьте внутреннее кольцо (15) и произведите зацепление язычков с соединительным диском.
18. Дисковую зубчатую муфту (16) с выпуклым внутренним зацеплением насадить с таким расчетом, чтобы оно смотрело в сторону первичного вала и входило бы в зацепление с промежуточным кольцом (14).
Включить скользящую муфту в нейтральном положении и прижать к дисковой зубчатой муфте. Вы отчетливо услышите щелчок фиксаторов, вставших на место
19. Нагреть втулку (17) до 120 гр. по Цельсию и насадить на вторичный вал, добиться хорошего осевого положения. Если есть необходимость, подправьте пластмассовой оправкой.
20. Слегка смажьте игольчатый роликоподшипник (18) и наденьте на втулку (17).
21. Косозубую шестерню (19) для 1-й или 5-й передачи насадите на игольчатый роликоподшипник (18) таким образом, чтобы шлицы вошли в зацепление с дисковой зубчатой муфтой.
22. Зубчатую муфту (20) нагреть до температуры 120 гр. по Цельсию и насадить на вторичный вал. Добиться хорошего осевого положения.
УКАЗАНИЕ: Буртик зубчатой муфты должен «смотреть» в сторону выходного вала.
23. Осевой зазор косозубой шестерни первой или пятой передачи должен составлять как минимум 0, 20 мм.
24. Нагреть втулку (21) до температуры 120 гр. по Цельсию, насадить на вторичный вал, обеспечить хорошее осевое положение.
25. Слегка смазать маслом игольчатый роликоподшипник (22) и надеть на втулку (21).
26. Косозубую шестерню (23) для заднего хода надеть на вторичный вал поверх игольчатого роликоподшипника.
Шлицы должны «смотреть» в сторону первичного вала.
27. Нагреть роликоподшипник (24) до температуры примерно 100 гр. по Цельсию, насадить на вторичный вал, добиться хорошего осевого положения. В случае необходимости воспользуйтесь пластмассовой оправкой.
28. Заправьте упорное кольцо (25) в кольцевой паз вторичного вала.
УКАЗАНИЕ: Осевой зазор упорного кольца должен составлять от 0 до 0,05 мм. Соответствующее упорное кольцо выберите по каталогу запасных частей.
29. Насадите на вторичный вал прижимное кольцо (26).
УКАЗАНИЕ: Прижимного кольца (26) в прежнем исполнении больше нет.
30. Зажмите вторичный вал со стороны выходного вала.
31. Слегка смазать маслом игольчатый подшипник (27) и насадить на вторичный вал.
32. Косозубую шестерню (28).3-я или 7-я передача надеть на игольчатый роликоподшипник; шлицы косозубой шестерни должны «смотреть» в сторону — первичного вала.
33. Зубчатая муфта (29) насадить на шлицы косозубой шестерни.
34. Кольцо синхронизатора (30) насадить на зубчатую муфту.
35. Нагреть ступицу синхронизатора (31) до температуры 120 гр. по Цельсию, насадить на шлицы вторичного вала, проследите за правильным осевым положением. В случае необходимости подправьте при помощи пластмассовой оправки.
УКАЗАНИЕ: Выступы кольца синхронизатора должны попадать в вытачки ступицы синхронизатора.
36. Насадить скользящую муфту (32).
Рис.7 Сборка вторичного вала КП
Рис.8 Сборка вторичного вала КП
УКАЗАНИЕ: Отфрезерованные вытачки с внутренней стороны скользящей муфты должны идти внахлест с теми местами ступицы синхронизатора, где будут расположены прижимные пружины (33) и фиксаторы (34).
37. Вдавите в отверстия корпуса синхронизатора новые пружины и имеющиеся фиксаторы и вставьте в скользящую муфту.
38. Расположите кольцо синхронизатора таким образом, чтобы выступы попадали в вытачки ступицы синхронизатора. Проверьте предел износа, см. главу 6.
39. Наденьте зубчатую муфту (36) на кольцо синхронизатора.
40. Подтяните скользящую муфту к нейтральному положению, прижимая при этом друг к другу кольцо синхронизатора (35) и зубчатую муфту. (36). Будет слышно как войдут на место и щелкнут фиксаторы.
41. Вставить оба роликоподшипника (37) в косозубую шестерню (38), 4-я передача.
УКАЗАНИЕ: отверстия роликоподшипников для смазки должны «смотреть» наружу (см. направление стрелки).
42. Роликоподшипник вместе с косозубой шестерней нагреть до температуры 100 гр. по Цельсию, насадить на вторичный вал, проследить, чтобы весь пакет подшипников лежал соосно.
УКАЗАНИЕ: шлицы косозубой шестерни должно «смотреть» в сторону выходного вала.
43. Осевой зазор косозубой шестерни должен составлять по меньшей мере 0,05 мм.
УКАЗАНИЕ: предложение по сборке: осевое кольцо (39), роликоподшипник (40), разборное кольцо (41), упорное кольцо (42) и кольцо (43) монтировать только по прочтении главы 11 «Настройка валов» .
2.1 Карта дефектации вторичного вала КП КаМАЗ
Наименование детали (сборочной единицы). Вал вторичной коробки передач | ||||||
Материал: Сталь 30 ХГТ ГОСТ 4543–71. | ||||||
Твердость: 59.65 НRCэ | ||||||
Позиция на эскизе | Возможный дефект | Способ установления дефекта и средства контроля | Размер, мм | Заключение | ||
По рабочему чертежу | Допустимый без ремонта | |||||
Износ шейки под передний подшипник | Калибр-скоба НЕ 40П ГОСТ 2015;84 или микрометр МК50−1 ГОСТ 6507 | 29,98 | Железнение Хромирование Наплавка | |||
Износ шлицов по толщине | Калибр ролики Штангенциркуль Радиусные шаблоны | 4,2 | 4,211 | Наплавка | ||
Вмятины от роликов или износ шейки под подшипники шестерни четвертой передачи | Осмотр Калибр-скоба НЕ 81Сга ГОСТ 2015;84 или микрометр МК 100−1 ГОСТ 6507 | 45,02 | Наплавка | |||
Износ шлицов по толщине | Калибр ролики Штангенциркуль Радиусные шаблоны | Наплавка | ||||
Вмятины от роликов или износ шейки под подшипники шестерни третьей передачи | Осмотр Калибр-скоба НЕ 81Сга ГОСТ 2015;84 или микрометр МК 100−1 ГОСТ 6507 | 51,48 | Наплавка | |||
Износ шлицов по толщине зуба | Осмотр Калибр ролики Штангенциркуль | 4,2 | 4,211 | Наплавка Хромирование | ||
Вмятины от роликов или износ шейки под подшипники | Осмотр Калибр-скоба НЕ 81Сга ГОСТ 2015;84 или микрометр МК 100−1 ГОСТ 6507 | Наплавка | ||||
Износ шлицов по толщине зуба | Осмотр Калибр ролики Штангенциркуль Радиусные шаблоны | 6,5 | 6,615 | Наплавка | ||
Износ шейки под задний подшипник | Калибр-скоба НЕ 40П ГОСТ 2015;84 или микрометр МК50−1 ГОСТ 6507 | 55,02 | Железнение Хромирование Наплавка | |||
; | Скручивание вала | осмотр | ; | ; | Браковать | |
; | Биение | Индикатор часового типа | Не более 0,12 | Не более 0,12 | Браковать | |
; | Облом и трещины | Осмотр | ; | ; | Наплавить. Заварить. Браковать. | |
3.1 Выбор и обоснование способов восстановления вторичного вала КП
Восстановленный вторичный вал должен отвечать следующим техническим требованиям:
овальность и конусность;
сообразность шейки под передний подшипник не более 0,01 мм, шейки под задний подшипник не более 0,02 мм;
нецилиндричность отверстия под роликовый подшипник не более 0,01 мм;
радиальное биение отверстия под роликовый подшипник не более 0,01 мм;
радиальное биение отверстия под роликовый подшипник относительно шеек под передний и задний подшипник не более 0,03 мм;
радиальное биение шейки под сальник относительно шеек под передний и задний подшипники не более Ra=1.25мкм, отверстия под роликовый подшипник не более Ra=0,63мкм.
Наиболее интенсивно изнашиваются следующие сопряжения:
шлицевое сопряжение вторичного вала с синхронизатором 4-й и 5-й передач;
наружные обоймы подшипников вторичного вала с картером
коробки передач;
посадочное место под подшипники на вторичном валу.
При передаче переменного крутящего момента коробкой передач в данном шлицевом сопряжении происходят соударения втулки синхронизатора со шлицами вторичного вала. При этом наблюдаются и осевые перемещения колебания синхронизатора относительно вторичного вала, а также радиальные колебания, вызванные дисбалансом валов и шестерен. Эти факторы вызывают изнашивание и деформацию шлицевых элементов сопряжения. Проверка сопряжения на смятие показала, что максимальное напряжение более чем в два раза ниже допустимого. Следовательно, смятия и пластической деформации шлицевого сопряжения в процессе эксплуатации с большой вероятностью не происходит.
Из этого следует, что чаще всего изнашивается посадочное место под подшипник. Самое целесообразное восстановление посадочных мест под подшипники из вышеперечисленных (железнение, хромирование, наплавка), это — хромирование и вибродуговая наплавка.
Электролитическое хромирование является эффективным способом повышения износостойкости трущихся деталей, защиты их от коррозии, а также способом защитно-декоративной отделки. Значительную экономию дает хромирование при восстановлении изношенных деталей. Процесс хромирования широко применяется в народном хозяйстве. Над его совершенствованием работает ряд научно-исследовательских организаций, институтов, вузов и машиностроительных предприятий. Появляются более эффективные электролиты и режимы хромирования, разрабатываются методы повышения механических свойств хромированных деталей, в результате чего расширяется область применения хромирования. Знание основ современной технологии хромирования способствует выполнению указаний нормативно-технической документации и творческому участию широких кругов практических работников в дальнейшем развитии хромирования.
Вторым наиболее целесообразным из способов восстановления вторичного вала коробки передач является вибродуговая наплавка. Этот способ наплавки является разновидностью дуговой наплавки металлическим электродом. Процесс наплавки осуществляется при вибрации электрода и подачей охлаждающей жидкости на наплавленную поверхность.
Преимущества способа:
небольшой нагрев деталей, не оказывающий влияние на термообработку;
высокая производительность процесса;
возможность получить наплавленный слой без пор и трещин;
минимальная деформация детали, которая не превышает полей допусков посадочных мест;
возможность получения наплавленного металла требуемой твердости и износостойкости.
Недостатки:
невысокая производителькость.
Рациональный режим наплавки:
напряжение 28.30;
сила тока 70−175 А;
диаметр проволки 1,6 мм;
скорость подачи проволки — 1,3 м/мин;
скорость наплавки — 0,5 — 0,6 м/мин;
амплитуда вибрации 1,82 мм.
В связи с тем что преимуществ вибродуговой наплавки больше и её чаще используют на производстве восстановление шейки под подшипник будет производится наплавкой.
4.1 План технологических операций по устранению дефектов
№ п/п | Наименование и содержание операции | Оборудование | Приспособление | Инструмент | Установочные базы | ||
Рабочий | Измерительный | ||||||
Токарная правка центров | Токарно-винторезный станок модели 1к62 | Патрон трех кулачковый, центр люнет | Сверло центрованное Р18 | Шаблон | Шейка ф17,18 центр отв. | ||
Шлифовальная шлифовать шейку под наплавку | Кругло шлифовальный станок модели 3Б151 | Поводковый патрон центр | Шлифовальный круг ПП600*305 24 А 40 ПСМ 25к8А | Микрометр МК 75−100−01 ГОСТ 6507–78 | Шейка ф17,18 центр отв. | ||
Наплавочная наплавить шейку вибродуговой наплавкой | Переоборудованный токарно-винторезный станок модели 1к62-м выпрямитель ВС, А — 600/300 Головка для наплавки 9АИЖ-5; Вибратор ОКС — 1252А | Патрон трех кулачковый, центр | Кусачки, комбинированные ГОСТ 5547–77 | Штангенциркуль ШЦ 1−125−01 ГОСТ 166–80 | Шейка ф17,18 центр отв. | ||
Шлифовальная предварительно шлифовать шейку под подшипник | Кругло шлифовальный станок модель 3Б151 | Поводковый патрон центр | Шлифовальный круг МП600*40*305 24А40ПСМ 25к8А | Микрометр МК — 75−100−0,01 ГОСТ 6507–78 | Шейка ф17,18 центр | ||
Шлифовальная чистовое шлифование шейки под подшипник | Кругло шлифовальный станок модели 3Б151 | Поводковый патрон центр | Шлифовальный круг МП 600*40*305 | Микрометр МК-75−100−0,01 ГОСТ 6507–78 | Шейка ф17,18 центр | ||
Моечная промыто деталь | Ванная с садовым раствором | Подвеска для мойки детали | |||||
Сушильная Удалить следы влаги | Сушильный шкаф | подвеска | |||||
Контрольная контролировать размеры диаметров шейки, шлиц шпоночной канавки | Плита проверочная, подставка под плиту | Контрольная | Стойка индикаторная индикатор часового типа микро метр МК — 75−100−0,01 ГОСТ 6507–78 Кольцо калибр шлицевое | ||||
5.1 Выбор оборудования приспособления и инструмента
Для правки центров выбираем токарный — винторезный станок 1к62.
Для шлифования шейки вала под подшипник применяем кругло шлифовальный станок 3б151.
Приспособление для наплавки — наплавочная головка УАНЖ — 5. Инструмент режущий переменяется с пластинками, из быстро режущей стали Р18 и твердого сплава Т5К10, позволяющие вести обработку на повышенных скоростях.
Для шлифовальной операции применяется шлифовальный круг МП 600*40*305
Измерительный инструмент приминается для межоперационного и окончательного контроля детали.
Штангенциркуль ШЦ 1 — 125 — 0,1
Микрометр МК — 75, кольцо — калибр шлицев
Калибр НЕ
Калибр — скоба — НЕ ГОСТ 2015– — 84
Калибр ГОСТ 7951– — 59
5.2 Расчет режимов и норм времени по операциям
Операция 005 Токарная
Править центровке отверстия с двух сторон оси. Инструмент-сверло центровое. Размеры отверстия: d=7,5 мм l=3,6 мм
Назначим режим резания: подача Sr=0,08 мм/об;
Скорость резания Vт=20 м/ мин. Подачу корректируем по паспорту станка модели «1к62». Sф=0,074 мм/об.
Число оборотов шпинделя:
n= (1000* т) / (П*Д); обмин
nт= (1000*20) / (3,14*7,5) =849 об/мин
Число оборотов корректируем по паспорту станка модели «1к62» na=800 обмин
Основное время:
То= (L*j) / (Sф *nф); мин
где L — длина прохода сверла, j — число проходов
Sф — фактическая подача, nф — фактическое число оборотов
где l-длина обрабатываемой детали, l1 — величина врезания
l1=t*ctg
где t-глубина резания
t= /2=7,5/2=3,75
половина угла сверла
=60
L1=3,75*ctg60=3,75*0,58=2,2 мм
То= (3,6+2,2) / (0,074*800) =0,10 мин
Вспомогательное время
Твсп=tуст+ tпер, мин
где tуст — время на установку и снятия детали
tпер — вспомогательное время, связанное с переходом
tпер=0,16мин
Твсп=0,87+0,16=2,47мин
Дополнительное время
Тдоп= ((То + Твсп) /100) *k
где k — процент дополнительного времени, k=8% для токарных работ
Тдоп= ((0,1+2,47) /100) *8=0,21 мин
Штучное время
Тшт= То+ Тв +Тдоп=0,1+2,47+0,21=2,78 мин
Подготовительно-заключительное время
Тз-н=4мин
Операция 010. Шлифование
Шлифовать шейку под наплавку.
Исходные данные: Деталь-вал вторичный коробки передач Д=65 мм; d=64,90 мм; l=493 мм. Материал — СТАЛЬ 30 ХГТ ГОСТ 4543–71.
Твердость-HRC 45 — 55. Масса детали — 2,75 кг.
Оборудование — кругло шлифовальный станок-3Б151.
Режущий инструмент — шлифовальный круг ПП 600*40*305.
Установка детали — в центрах.
Условия обработки — с охлаждением.
Вид шлифования — круглое наружное с выходом шлифовального круга в одну сторону.
Содержание операции — установить деталь; шлифовать шейку; измерить шейку; снять деталь.
Последовательность расчета. Режима резания
Припуск на обработку
t= (Д — d) /2= (65 — 64,90) /2=0,1 мм
Поперечная подача (глубина шлифования), St
St=0,005…0,010
Принимаем по паспорту станка модели «3Б151»
St=0,0075 мм/ход стола
Скорость резания определяем по таблице по принятой подаче, глубине шлифования и диаметру шлифуемой поверхности детали до 60 мм. =20м/мин
Определяем число оборотов шпинделя:
nт= (1000*) / (П*Д) = (1000*20) / (3,14*29,94) =211 об/мин
Определяем nф, корректируя nт по паспорту станка
na=150 об/мин
Основное время. Принимаем метод врезания
То= Z/ (nф *St) *k
где Z-припуск на шлифование
nф — фактическое число оборотов шпинделя
St — поперечная подача
k — коэффициент, учитывающий износ круга о точность шлифования; k=1,1…1,4 При черновом шлифовании принимаем k=1,3
То= 0,1/ (150*0,0075) *1,3=0,12мин
Вспомогательное время
Тв= Тв + Тв + Тв
где Тв — вспомогательное время на установку и снятие детали
Тв=0,80 мин, Тв=0,80+0,40+0,25=1,45 мм
Дополнительное время
Тдоп = ((То +Тв) /100) *k; k=9%
Тдоп = ((0,12+1,45) /100) *9=0,14 мин
Штучное время
Тшт =То +Тв +Тдоп, Тшт=0,12+1,45+0,14=1,71мин
Подготовительно заключительное время
Тз-н=9мин
Операция 015. Наплавочная
Содержание операции:
1) установить деталь;
2) направить шейки;
3) снять деталь.
Оборудование: токарно-винторезный станок, модернизированный 1К62 — М; выпрямитель ВСА — 600/300; головка для наплавки УАНЖ — 5.
Приспособления: кусачки комбинированные.
Материал наплавки: электродная проволока — 30 ХГСА.
Последовательность определения режимов вибродуговой наплавки. Размеры наплавленных поверхностей: — шейка под подшипник d1=29,74 мм Д1=31,1 мм l1=42; Нmax =4,92 мм Нmin=4,88 мм l1=40 Ннапл=6,24 мм
Режим наплавки: — диаметр электродной проволоки dэ=1,6 мм; - плотность тока Да=85А/мм; - сила сварочного тока У=0,785*d*Да, А
У=0,785*1,6*85=170А
напряжение дуги U= 27В; - коэфицент плавки н=7,5; - масса расплавленного металла — Gр. м
Gр. м= (У* н) /60= (170*7,5) /60=21,3 г/мин
Объем расплавленного металла Qр. м
Qр. м=Gр. м / =21,3/7,812=2,7 см/мин
Скорость подачи электродной проволоки — п. р.
п. р. =Qр. м /0,785d= 2,7/ (0,785* (1,6)) =1,35 м/мин
Подача (шаг наплавки)
S= (1,2…2,0) *d, мм/об
S= (1,2…2,0) *1,6=1,92…3,2 мм/об
Корректируем подачу по паспорту станка модели 1К62 Sф=2,8мм/об
Скорость наплавки — н
н= (0,785d* пр *k*a) / (t*S)
где t — толщина слоя t=0,68 мм
к=0,90, а=0,96
н= (0,785 (1,6) *1,35*0,90*0,96) / (0,68*2,8) =1,23 м/мин=123 мм/мин
Частота вращения детали
n= (1000* м) * (П*Д) = (1000/1,23) / (3,14*30) =13,05 об/мин
Корректируем n по паспорту станка nф=12,5об/мин
Техническое нормирование автоматической наплавки.
Основное время
То= (L/ (n*S)) *j
где L — длина наплавки, мм
n — число оборотов, об/мин
S — шаг наплавки, мм/об
j — количество слоев наплавки
То= (42/ (2,8*12,5)) =1,2
Вспомогательное время
Тв= Тв1 +Тв2 +Тв3
где Тв1-время, связанное на установку и снятие детали, мин
Тв1=0,30 мин
Тв2-время, связанное с переходом
Тв2=0,7 на один погонный метр валика
L= (П*Д*l) /S= (3,14*30*32) / (1000*2,8) =1,077 м
Тв2= 0,7*1,077=0,75 мин
Тв3 — время на один поворот детали
Тв3=0,46
Тв=0,30+0,75+0,46=1,51мин
Дополнительное время
Тдоп= ((То +Тв) /100) *k; мин
Где К=15%
Тдоп= ((1,2+1,51) /100) *15=0,41 мин
Штучное время
Тшт=То+Тв+ Тдоп=1,2+1,51+0,41=3,12мин
Подготовительно-заключительное время
Тпз=8+1+0,8+0,1+1,3+4,5=16,6мин
Наплавка шлицев продольным способом.
Основное время
То= (L/ н) *j=мин
То= (32/123) *1=0,26 мин — на один шлиц
То= 0,26*6=1,56мин
Вспомогательное время
Тв= Тв1+ Тв2+ Тв3
Тв1-время на установку, крепление и снятие детали
Тв1=0,29мин
Тв2-время, связанное с переходом, определяется исходя из нормы 1,4мин на 1 погонный метр валика
Тв1= (1,4*32) /1000=0,05 мин
Вспомогательное время на поворот детали на 180 и установки наплавочной головки равно 0,46, а на 6 поворотов
Тв3=0,46*6=2,76мин
Тв=0,29+0,05+2,76=3,1мин
Тдоп= ((То +Тв) /100) *k= ((1,56+3,1) /100) *15=0,7 мин
Штучное время
Тшт= То +Тв+ Тдоп=1,56+3,1+0,7=5,36мин
Подготовительно — заключительное время
Тп-з=8+1+0,8+0,1+1,3+5,4=16,6мин
Общее штучное время на операцию
Тшт=3,12+5,36=8,48мин
Общее подготовительное время на операцию
Тп-з=16,6+16,6=33,2мин
Операция 020. Шлифование.
Шлифовать шейку под подшипник после наплавки.
Исходные данные: деталь — вал вторичный коробки передач Д=31,1 d=42
Материал — сталь 30 ХГТ ГОСТ 4543–71. твердость-НRС 45 — 55, масса детали-2,75 кг.
Оборудование — кругло шлифовальный станок 3Б151.
Режущий инструмент — шлифовальный круг — ПП 600×40×305
Установка детали — в центрах.
Условия обработки — круглое наружное шлифование.
Содержание операции: установить деталь в центрах, предварительно шлифовать шейку, окончательно шлифовать шейку, измерить шейку, снять деталь.
Черновое шлифование.
Режимы резания: припуск на обработку б=0,5 мм
Поперечная передача (глубина шлифования St)
St=0,005…0,010
Принимаем по паспорту станка модели 3Б151
St =0,0075 мм/ход стола.
Скорость резания = 20м/мин
Число оборотов шпинделя
nт = (1000*) / (П*Д) = (1000*20) / (3,14*31,1) =204,8 об/мин
Корректируем nт по паспорту станка модели 3Б151
na =150 об/мин
Основное время
То = (Z/ (nф *St)) *k; мин
где k=1,3
То = (0,05/ (150*0,0075)) *1,3=0,6 мин
Вспомогательное время
Тв = Тв +Тв +Тв=0,8+0,3+0,25=1,35мин
Дополнительное время
Тдоп = ((То +Тв) /100) *k= ((0,6+1,35) /100) *9=0,18 мин
Штучное время
Тшт = То +Тв +Тдоп=0,6+1,35+0,18=2,13мин
Подготовительно — заключительное время
Тз-н =7мин
Операция 025. Шлифование чистовое.
Режим резания принимаем nф =159об/мин, =20 м/мин, St =0,0075 мм/ход стола. Припуск на обработку б=0,05 мм
Основное время:
То = (Z/ (nф *St)) *k=* (0,05/ (150*0,075)) *1,7=0,08 мин
Вспомогательное время:
Тв=0,6+0,35+0,25=1,2мин
Дополнительное время:
Тдоп= ((То +Тв) /100) *k= ((0,08+1,2) /100) *9=0,12 мин
Штучное время:
Тшт=0,08+1,2+0,12=1,4мин
Подготовительно — заключительное время
Тп-з =7 мин
5.3 Расчет технических норм времени
Тн =Тшт + (Тп-з /х), мин
Технологические нормы времени для всех операций:
Тн =2,789+ (4/15) =3,05мин
Тн=1,71+ (9/15) =2,31мин
Тн =8,48+ (33,2/15) =10,7мин
Тн =8,42+ (11/15) =9,15мин
Тн =2,13+ (7/15) =2,6мин
Тн =1,4+ (7/15) =1,87мин
6.1 Проектирование и расчет производственного участка
Расчет количества рабочих
При проектировании участков по восстановлению деталей, годовой объем работ Тг, используемый для определения производственных рабочих, рассчитывается по формуле:
Тг =t*n*N*kм. р
где t — трудоемкость
N =4000ед
k = 0,98
t =Tн /60= 3,05/60=0,05 чел — час
t = 2,31/60=0,04ч-ч
t =10,7/60=0,18 ч-ч
t =9,15/60=0,15 ч-ч, t =2,6/60=0,04 ч-ч
t =1,87/60=0,03 ч-ч
Годовая трудоемкость по операциям:
Тг =0,05*1*4000*0,98=196 ч-ч
Тг =0,04*1*4000*0,98=156,8 ч-ч
Тг =0,18 *1*4000*0,98=705,6 ч-ч
Тг =0,15 *1*4000*0,98=588 ч-ч
Тг =0,04 *1*4000*0,98=156,8 ч-ч
Тг =0,03 *1*4000*0,98=117,6 ч-ч
Количество производственных работ
m=Тг /Фд. р.
Фд. р. — действительный фонд рабочего времени (Фд. р. =2070 час)
Токари: mяв =196/2070=0,1 чел
Принимаем: m яв=1 чел
Наплавщики: mяв =705,6/2070=0,34 чел
mяв =1 чел
Шлифовщики: mяв = (156,8+156,8+117,6) /2070=0,21чел
mобщ =1+1+1=3человека
6.3 Расчет количества оборудования
Хо =Тг /Фд. о
Где Фд. о — действительный фонд времени оборудования (2025час)
Хо =196/2025=0,1 шт.
Хо = 156,8/2025=0,08 шт.
Хо =705,6/2025=0,35 шт.
Хо =588/2025=0,3 шт.
Хо =156,8 /2025= 0,08 шт.
Хо =117,6/2025=0,06 шт.
Принимаем количество оборудования по операциям:
хо=1 ед хо=1 ед хо=1 ед хо=1 ед хо=1 ед хо=1 ед
Коэффициент загрузки оборудования
Кз = (хо) /n
Кз =0,1/1=0,1 или 10%
Кз =0,35/1=0,35 или 35%
Кз = (0,08+0,08+0,06) /1=0,22 или 22%
Кз = (0,17+0,08) /1=0,25 или 25%
Средний коэффициент загрузки
Кз = (0,1+0,35+0,22+0,25) /4=0,23 или 23%
6.4 Расчет площади
Площадь участка по принятому оборудованию
Fуч=Fобщ *Кn, м
Fобщ =3,75+3,75+8,61+0,66+0,75+1,28+0,8+0,63+0,4+2*0,6+0,4+0,5=22,76 м
Fуч =22,76*3,5=79,66 м принимаем Fуч =80 м
6.5 Планировка оборудования и рабочих мест
Выбираем одноэтажное здание с шагом колон 6 м и шириной пролета 12 м. Технологическое оборудование располагается с соблюдением необходимых расстояний между станками и конструктивными элементами зданий. Рабочее место должно быть освещено.
Ведомость оборудования и инвентаря.
№ n/n | Наименование и модель | Кол-во Шт. | Габариты L*B, мм | Плошать, м | Примечание | |
Токарно-винторезный станок 1к 62 | 3212*1166 | 3,75 | ||||
Токарно-винторезный станок 1к62-м (переоборудован) | 3212*1166 | 3,75 | ||||
Кругло — шлифовальный станок 3Б151 | 4100*2100 | 8,61 | ||||
Головка для наплавки УАИЖ-5 | Устанавливается на станке | |||||
Сварочный выпрямитель ВСА600/300 | 1100*600 | 0,66 | ||||
Стол сварщика | 1034*724 | 0,75 | ||||
Вибратор ОКС — 1252А | 600*600 | 0,36 | Устанавливается на станке | |||
Ванна моечная | 1500*850 | 1,28 | ||||
Камера сушильная | 1000*800 | 0,8 | ||||
Плита проверочная | 1000*630 | 0,63 | ||||
Подставка для контрольной плиты | 800*500 | 0,4 | ||||
Стол для мастера и контроля | 1000*600 | 0,6 | ||||
Тумбочка инструментальная | 800*500 | 0,4 | ||||
стеллаж | 1000*500 | 0,5 | ||||
6.6 Организация транспортировки детали
Транспортировка детали на участок производится вручную, в виду малых габаритов и веса. После механической обработки вал моют в ванне в содовом растворе, сушат в шкафе и подвергают 100%контролю. После контроля годные детали транспортируют на склад готовой продукции.
6.7 Организация технического контроля
Технический контроль качества являются составной частью системы управления качеством ремонта автомобилей, охватывающей все элементы и стадии производственного процесса.
При разработке технологического процесса ремонта вторичного вала коробки передачи особое внимание было уделено вопросам технического контроля, который осуществляется исполнителями в процессе обработки, а также итоговый контроль, которому подвергаются все детали.
В целях уменьшения количества брака применяется летучий контроль, осуществляемый периодически контрольным мастером.
Выбор средств контроля производится с учетом типа производства и его организационной структуры, типа детали и объема производственной программы.
Для контроля деталей на операциях используется стандартные и специальные измерительные инструменты и калибры.
7.1 Техника безопасности, противопожарная защита и промышленная санитария
Основы техники безопасности и производственной санитарии по ремонту и техническому обслуживанию автомобилей отражены Государственным стандартом РФ № 2583 от 17 июля 1995 г.
В соответствии с действующими правилами все вновь поступающие рабочие обязаны пройти обучение технике безопасности при выполнении работ.
Они могут быть допущены к работе только после прохождения:
вводного инструмента по технике безопасности
инструктаж по технике безопасности непосредственно на каждом переходе на другую работу или при изменении условий работы.
Во время вводного инструктажа рабочих знакомят:
с характером предприятия
с основными причинами несчастных случаев
с обязанностями по соблюдению правил техники безопасности
с разновидностью индивидуальных защитных средств и порядком пользования ими
способами оказания первой помощи при несчастных случаях.
При инструктаже также соблюдают правила электробезопасности и пожарной безопасности.
Инструктаж на рабочем месте проводит непосредственный руководитель, в подчинении которого направлен рабочий.
При инструктаже сообщает:
обязанности не данном рабочем месте
устройство и обслуживание машин и механизмов
требования безопасного обращения с электрооборудованием и инструментами
правила пользования индивидуальными защитными средствами
системы сигнализации
правила личной гигиены.
Инструктаж заканчивается практическими выполнениями безопасных приемов работы непосредственно на рабочем месте
Все станки должны иметь индивидуальное освещение, деревянную подставку под него рабочего.
Все подвижные части станка должны быть закрыты кожухами и окрашены в сигнальные цвета безопасности.
На шлифовальных станках обработка проводится с применением охлаждающей жидкости путем подачи струн в зону обработки, что исключает появление абразивной пыли.
Оборудование, потребляющее электроэнергию, имеют заземление, электрическая проводка помещена в защитные металлорукова или стальные трубы.
В места подвода электрической энергии к оборудованию устанавливают знак «высокое напряжение» .
Рабочие должны иметь специальную одежду, при работе, которая должна быть плотно застегнута, волосы заправлены под головной убор. Рабочие станочники должны работать в защитных очках.
Меры противопожарной безопасности: пожарная сигнализация, водоснабжение для противопожарных целей, противопожарный щит.
Для оказания первой медицинской помощи при микротравмах на участке имеется медицинская аптека, а в цехе медпункт.
Требования техники безопасности при работе на токарных станках.
Пользоваться режущим инструментом, имеющим правильную заточку.
Устанавливать и снимать режущий инструмент только после полного восстановления станка.
Не удалять стружку от станка непосредственно руками и инструментом, пользоваться для этого специальными крючками и щетками сметками.
Не допускать разбрызгивание масла и других жидкостей на пол.
После окончания работы привести в порядок рабочее место.
Требования техники безопасности при работе на шлифовальных станках.
Не устанавливать на станках не исправные круги.
Проверить круг и шпиндель на отсутствие биения.
Не устанавливать на станок погнутую деталь.
При установке и закреплении детали необходимо:
— крепить деталь только специальными упорами;
— оберегать круг от ударов и толчков.
Станок должен быть огражден.
Для удаления абразивной пыли пользоваться щетками сметками и совками, при этом одевать защитные очки.
Требования техники безопасности при наплавочных работах.
При выполнении наплавочных работ все оборудование, находящееся под напряжением должно быть надежно заземлено. Рабочее место должно быть оборудовано местной вентиляцией. Все токоведущие части, а также клеммы для присоединения проводов должны иметь защитные кожухи.
Заключение
В дипломном проекте был усовершенствован процесс восстановления вторичного вала КПП методом вибродуговой наплавки с последующей токарной и шлифовальной обработкой. Была произведена установка новейшего оборудования, которое удовлетворяет всем самым новейшим техническим стандартам и нормам, таким как экономичность, производительность, безопасность труда, долговечность.
Стоимость восстановления методом вибродуговой наплавки на данном оборудовании обходится в 0.5 раза дешевле, производительность труда увеличилась на 15.7%. С учетом этих изменений были просчитаны все режимы, т.к. резание, шлифование, наплавка и были пересчитаны все нормы времени на операции.
1. «Ремонт автомобилей». Под редакцией С. И. Румянцев, М, Транспорт, 1988 г.
2. Карагодин В. И., Митрохин Н. Н. «Техническое нормирование ремонтных работ», М., Колос, 1979 г.
3. Матвеев Н. А., Пустовалов И. И., «Техническое нормирование ремонтных работ», М., Колос, 1979 г.
4. «Краткий справочник металлиста», под ред. Орлова П. Н., м., 1986 г.
5. «Оборудование для ремонта автомобилей», под ред. Шахнева, М., Транспорт, 1979 г.
6. Мельников П. С., «справочник технолога»
7. «Справочник технолога авторемонтного производства», под ред. Малышева А. Г., М., Транспорт, 1977 г.
8. Клебанов Б. В., «Проектирование производственных участок авторемонтных предприятий», М., Транспорт, 1975 г.
Приложение
Измерительный инструмент.
Штангенинструмент: ШЦ — 1
Рис. 1 штангенциркуль
1 — штанга; 2 — губки для измерений; 3 — рамка; 4 — винт для фиксации; 5 — шкала нониуса; 6 — устройство для точного перемещения рамки.
Микрометры: Гладкий микрометр МК
Рис. 2 микрометр МК
1 — скоба; 2 — пятка; 3 — установочная мера; 4 — микровинт; 5 — стопор;
6 — стебель; 7 — барабан; 8 — трещотка.
Индикатор рычажно — зубчатый
Рис. 3 Индикатор рычажного типа
1 — циферблат; 2 — корпус; 3 — указатель — ограничитель; 4 — винт установки нуля; 5 — наконечник; 6 — стержень; 7 — гильза; 8 — арретир; 9 — стрелка.