Разработка технологического процесса восстановления коленчатого вала двигателя автомобиля ЗИЛ-131
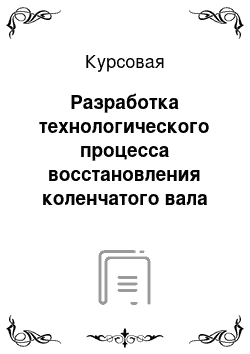
Автомобильный транспорт — одна из важнейших отраслей народного хозяйства, развивается как неотъемлемая часть единой транспортной системы. В современных условиях дальнейшее развитие экономики немыслимо без хорошо налаженного транспортного обеспечения. В условиях, когда наметилась тенденция к оживлению и восстановлению реального сектора экономики, автомобильный транспорт способствует нормализации… Читать ещё >
Разработка технологического процесса восстановления коленчатого вала двигателя автомобиля ЗИЛ-131 (реферат, курсовая, диплом, контрольная)
Содержание Введение
1. Обоснование размера производственной партии деталей
2. Характеристика автомобиля
3. Разработка технологического процесса восстановления детали
3.1 Ремонтный чертеж детали
3.2 Характеристика детали и условия его работы
3.3 Выбор способа восстановления детали
3.4 Схема технологического процесса
3.5 План технологических операций
4. Разработка операций по восстановлению деталей
4.1 Исходные данные
4.2 Содержание операций
4.3 Определение припусков на обработку
4.4 Расчет режимов обработки
5. Графическая часть
5.1 Расчет годовой трудоемкости работ на участке
5.2 Расчет количества производственных рабочих на участке
5.3 Расчет количества основного оборудования на участке
5.4 Расчет площади участка
6. Организация труда на производственном участке
6.1 Охрана труда Заключение Список использованной литературы
Введение
Целью данного курсового проекта является разработка технологического процесса восстановления коленчатого вала двигателя автомобиля ЗИЛ 131 с применением наиболее прогрессивных форм и методов организации авторемонтного производства, что обеспечит повышение качества и снижение затрат при КР, улучшит условия труда на АРП. Также это повысит уровень заработной платы рабочих, что привлечет новые, опытные кадры.
Автомобильный транспорт — одна из важнейших отраслей народного хозяйства, развивается как неотъемлемая часть единой транспортной системы. В современных условиях дальнейшее развитие экономики немыслимо без хорошо налаженного транспортного обеспечения. В условиях, когда наметилась тенденция к оживлению и восстановлению реального сектора экономики, автомобильный транспорт способствует нормализации положения в финансовой и кредитной сфере. От его чёткости и надёжности во многом зависят трудовой ритм предприятий промышленности, строительства и сельского хозяйства. Он обеспечивает наряду с другими видами транспорта рациональное производство и обращение продукции промышленности и сельского хозяйства, удовлетворяет потребности населения в перевозках.
Уровень развития транспортной системы государства — один из важнейших признаков ее технологического прогресса и цивилизованности. Потребность в высокоразвитой транспортной системе еще более усиливается при интеграции в европейскую и мировую экономику.
Транспортная система становится базисом для эффективного вхождения России в мировое сообщество и занятия в нем места, отвечающего уровню высокоразвитого государства.
Нарастающая автомобилизация страны требует системных мер, направленных на ограничение ее негативных последствий для общества, при максимально возможной реализации ее преимуществ и выгод.
Автомобильный транспорт России представляет собой наиболее массовый вид транспорта. На его долю приходится более половины объема пассажирских перевозок и три четверти грузовых перевозок.
Основными причинами активного использования автотранспорта стали присущие ему гибкость доставки и высокая скорость междугородних перевозок. Кроме того, помощью автомобильного автотранспорта груз может доставляться «от дверей до дверей» без дополнительных затрат на перегрузку, а также с необходимой степенью срочности. Этот вид транспорта обеспечивает регулярность поставки. Здесь, по сравнению с другими видами транспортных средств, предъявляются менее жесткие условия к упаковке товара.
Большая мобильность, возможность оперативно реагировать на изменения пассажиропотоков ставят автотранспорт «вне конкуренции» при организации местных перевозок пассажиров.
Основная часть автомобильного парка страны эксплуатируется в нетранспортных организациях. При этом сеть автомобильных дорог наряду с парком коммерческих автомобилей используется также автомобилями, находящимися в личном пользовании граждан.
Вообще, сфера применения автотранспорта широка. Он выполняет большую часть коротких внутрирайонных перевозок, доставляет грузы к станциям железных дорог и речным пристаням и развозит их к потребителям. В северных и восточных районах страны, где почти нет других видов сухопутного транспорта, им осуществляются дальние межрайонные перевозки.
Автомобильный транспорт в России выполняет свыше 55% объёмов внутренних грузовых перевозок и более 60% пассажиров, с тенденцией увеличения этой доли, являясь, таким образом, главным перевозчиком для основных секторов экономики.
В настоящее время транспорт оказывает заметное влияние на экономическое развитие страны в целом. На транспорте занято свыше 3,2 млн. человек, что составляет 4,6% работающего населения.
Ежедневно автотранспортом перевозится около 17 млн. тонн грузов и более 62 млн. пассажиров. Если сравнивать с аналогичным показателем железнодорожного транспорта, то это почти в 6 раз больше по объемам перевозок грузов и в 17 раз — по перевозкам пассажиров.
В последние годы общая численность парков автобусов и грузовых автомобилей изменялась практически незначительно. Тем временем интенсивно растет количество легковых автомобилей в собственности граждан. Автомобилизация страны стимулируется инвестициями населения и бизнеса, которые ежегодно вкладывают только в новые автомобили до 4 миллиардов долларов. По сути дела, конечными потребителями автомобилизации становятся все отрасли экономики, а также социально-культурная сфера, пассажиры и владельцы личных автомобилей и другие виды транспорта, являющиеся смежными звеньями в системе товародвижения.
В России с ее огромной территорией именно транспорт объединяет в единый комплекс буквально все отрасли экономики. Именно транспорт обеспечивает не только нормальную жизнедеятельность государства, но и его национальную безопасность и целостность. Всевозрастающие масштабы общественного производства, расширение сфер промышленного использования природных ресурсов, развитие экономических и культурных связей как внутри страны, так и с зарубежными странами, требования обороноспособности страны не могут быть обеспечены без мощного развития всех видов транспорта, широко разветвленной сети путей сообщения, высокой мобильности и маневренности всех видов транспорта.
Транспорт в нашей стране способствует решению таких важных политических задач, как ликвидация экономического отставания окраинных районов, противоположности между городом и деревней, расширение связей народов нашей страны, укрепление их дружбы, обмен достижениями во всех отраслях народного хозяйства и областях культуры.
1. ОБОСНОВАНИЕ РАЗМЕРА ПРОИЗВОДСТВЕННОЙ ПАРТИИ Для определения оптимальной величины размеров производственной партии деталей существует несколько формул, предложенных разными авторами.
Понятие партии и методы определения размеров партии становится крайне важным при календарном планировании и управлении исполнением плана в производстве. Размер партии оказывает влияние на уровень незавершенного производства и запасов, на пропускную способность рабочих центров, а в итогена уровень производственных затрат и эффективности всего производства.
Партия — группа заготовок определённого наименования и типоразмера, запускаемый в обработку одновременно в течении определённого интервала времени.
В условиях серийного ремонтного производства размер принимают равным месячные потребности ремонтируемых или изготавливаемых деталей.
Важным условием повышения производительности труда при применении более совершенного оборудования является увеличение размера партий одинаковых изделий. Этот размер может быть увеличен даже при неизменном объеме выпуска готовой продукции.
Методы определения размеров партии не сложные, но существуют некоторые условия и ограничения, которые необходимо рассматривать.
В стадии проектирования технологических процессов величину производственной партии деталей можно определить ориентировочно по следующей формуле:
Х=(N•n•t/фдн) Х=6800•1•5/253=134
где,
N — производственная программа изделий в год;
n — число деталей в изделии;
t — необходимый запас деталей в днях для обеспечения непрерывности сборки;
t = 2−3 дня — для крупных деталей, хранение которых возможно на одноярусных стеллажах, подставках, лагах;
t = 5 дней — для средних деталей, хранение которых возможно на многоярусных стеллажах;
t = 10−30 дней — для мелких деталей, хранение которых возможно в контейнерах и другой таре;
Фдн. — 253 — число рабочих дней в году.
2. Характеристика автомобиля ЗИЛ-131
Технические характеристики автомобиля ЗИЛ-131
коленчатый вал двигатель автомобиль ЗиЛ-131 представляет собой дальнейшее развитие конструкции армейского грузового автомобиля в классе грузоподъемности до 5 т. На машине установлен восьмицилиндровый карбюраторный двигатель мощностью 150 л.с. Все колеса автомобиля — ведущие односкатные переменного давления. Необходимый уровень давления в шинах поддерживается с помощью централизованной системы регулирования давления воздуха. Грузовик оснащен «проходными» задними мостами, что позволило уменьшить количество карданных валов. Привод к передним колесам — отключаемый. Машина имеет экранированное электрооборудование Завод — изготовитель: Завод имени Лихачева Марка: Зил-131
Колесная формула: 6 х 6
Масса перевозимого груза, кг: по дорогам 5000, по грунту — 3500
Полная допустимая масса прицепа, кг: по дорогам 6 500, по грунту — 4000
Масса снаряженного автомобиля, кг: без лебедки — 6135, с лебедкой 6 400
Полная масса, кг: без лебедки — 11 135, с лебедкой — 11 925
Нагрузка на дорогу, кН (кгс) Через шины передних колес: 2 900
Через шины колес тележки: 3 560
Габаритные размеры, мм: 7 040×2 500×2 480 (с тентом — 2975)
База, мм: 3350+1250
Колея, мм: задняя и передняя — 1820
Дорожный просвет: мм: под передней осью — 330, под задней осью — 355
Двигатель: ЗИЛ-50 810
Рабочий объем, см3: 5996
Тип: бензиновый
Максимальная мощность при 3200 об/мин (л. с.): 150
Максимальный крутящий момент при 2000 об/мин, Н*м (кгс*м): 402
Конфигурация: V8
Цилиндров: 8
Клапанов: 16
Ход поршня, мм: 95
Диаметр цилиндра, мм: 100
Степень сжатия: 6,5
Система питания: карбюратор
Охлаждение: жидкостное
Клапанной механизм: OHV
Метал блока цилиндров: Чугун
Материал ГБЦ: Алюминий
Тактность (число тактов): 4
Порядок работы цилиндров: 1−5-4−2-6−3-7−8
Рекомендованное топливо: А-76
Сцепление: однодисковое, сухое
Коробка передач: 5-ти ступенчатая с синхронизаторами 2−3 и 4−5 передач
Передаточные числа: 7.44; 4,10; 2,29; 1,47; 1,00; з/х 7,09
Раздаточная коробка: 2-х ступенчатая
Передаточные числа: 2,08; 1,00
лавная передача: двойная с коническими спиральными и цилиндрическими прямозубыми шестернями
Рулевой механизм: винт и гайка с гидроусилителем
Усилитель: гидравлический
Тормозные системы
Рабочая: барабанные, на все колеса с пневматическим приводом
Стояночная: барабанные на трансмиссию с мех. Приводом
Подвеска
Передняя: на 2-х продольных полуэллиптических рессорах, амортизаторы гидравлические, телескпич. 2-х стороннего действия
Задняя: балансирная на продольных полуэллиптических рессорах
Шины: 12.00×20″
Кабина: цельнометаллическая, закрытая, трехместная
Платформа: деревянная, задний борт откидной
Погрузочная высота, мм: 1 430
Лебедка: механическая с приводом от КОМ
Глубина преодолеваемого брода, м: 1,4
Максимальная скорость, км/ч: 80
Тормозной путь со скоростью 40 км/ч, м: 14; 50км/ч, м: 29
Расход топлива при скорости 40 км/ч, л/100 км: 40; 60 км/ч, л/100 км: 35
Запас хода — 850
3. Разработка технологического процесса восстановления детали
3.1 Ремонтный чертеж детали Рисунок 1- Коленчатый вал двигателя Дефекты:
1 Износ коренных шеек по наружному диаметру.
2 Износ шейки вала под приводной шкив.
3 Износ шпоночного паза под шестерни и приводной шкив.
3.2 Характеристика детали и условий ее работы Коленчатый вал двигателя изготовлен из стали марки 40ХФА — сталь образуются только при малых скоростях охлаждения в узком интервале температур, когда мала степень переохлаждения жидкой фазы.
У стали хорошие технологические и прочностные свойства, что определяет широкое применение их как конструкционного материала. Однако, благодаря высоким литейным свойствам, достаточной прочности и относительной дешевизне, стали нашли широкое применение в машиностроении.
Для того что бы улучшить механические свойства изделий их необходимо применить к термической обработке.
Термообработка — это процесс обработки изделий из металлов и сплавов путем теплового воздействия с целью изменения их структуры и свойств заданном направлением. Любая термическая обработка состоит из следующих операций:
— Нагрев
— Выдержка
— Охлаждение Классификация термической обработки.
Собственная термообработка предусматривает только температурное воздействие. Она применяется:
— как промежуточная операция, для улучшения технологических свойств металлов.
— как окончательную, для предания такого комплекта механических и физических свойств.
Химико-термическая обработка проводится при нагреве сплава, изменением состава поверхностного слоя путем воздействия химическими реакциями.
Термомеханическая обработка представляет собой тепловое воздействие с применением пластической операции, для изменения структуры сплава.
3.3 Выбор способов восстановления детали Каждая деталь должна быть восстановлена с минимальными трудовыми и материальными затратами при обеспечении максимального срока службы детали после ремонта. Это возможно при рациональных способах восстановления детали. Здесь следует учитывать, что один и тот же способ устранения дефектов в разных случаях может иметь разный эффект в организации производства. Выбор способов устранения дефектов коленчатого вала двигателя автомобиля ЗИЛ 131
1 Износ коренных шеек по наружному диаметру.
2 Износ шейки вала под приводной шкив.
3 Износ шпоночного паза под шестерни и приводной шкив.
Возможные способы устранения:
по дефекту 1
— Слесарной механической до РР.
— Наплавка под слоем флюса.
— Вибродуговая.
по дефекту 2
— Вибродуговая
— Железнение
— Аргонно-дуговая по дефекту 3
— железнение
— наплавка под слоем флюса
— вибродуговая наплавка Кд = Ки•Кв•Ксц•Кп где, Кд — коэффициент долговечности;
Ки — коэффициент износостойкости;
Кв — коэффициент выносливости;
Ксц — коэффициент сцепляемости;
Кп — поправочный коэффициент, учитывающий фактическую работоспособность восстановленной детали. Кп = 0,8 — 0,9.
Кд1=0,95•0,9•1•0,9=0,76
Кд2=0,91•0,87•1•0,9=0,71
Кд3=1•0,62•1•0,9=0,55
Кд4=0,91•0,77•1•0,9=0,71
Кд5=0,91•0,82•0,85•0,9=0,63
Кд6=0,7•0,6•1•0,9=0,37
Кд7=1•0,62•1•0,9=0,55
Кд8=0,91•0,82•0,85•0,9=0,63
Кд9=0,7•0,7•1•0,9=0,44
Методика выбора способов восстановления следующая:
1. Выбрать по технологическому критерию, используя карты дефектации по ремонту автомобилей, возможные способы восстановления по каждому дефекту.
2. Дать комплексную оценку каждого метода по значению коэффициента долговечности.
3. По каждому дефекты выбрать способ восстановления с максимальным значением коэффициента долговечности.
Таблица 1- Выбор рационального способа восстановления коленчатого вала автомобиля Зил 131
Номер дефекта | Применение | Износостойкости | Выносливости | Сцепляемости | Долговечности | Экономичности | Принятый способ | |
Слес. мех. до РР | 0,95 | 0,9 | 0,76 | ; | Слес. мех. до РР | |||
Наплавка под слоем флюса | 0,91 | 0,87 | 0,71 | ; | ||||
Вибродуговая | 0,62 | 0,55 | ; | |||||
Железнение | 0,91 | 0,82 | 0,85 | 0,63 | ; | Под слоем флюса | ||
Под слоем флюса | 0,91 | 0,71 | 0,71 | ; | ||||
Электро-дуговая | 0,7 | 0,6 | 0,37 | ; | ||||
Железнение | 0,91 | 0,82 | 0,85 | 0,65 | ; | Железнение | ||
Вибродуговая | 0,62 | 0,55 | ; | |||||
Аргонно-дуговая | 0,7 | 0,7 | 0,44 | ; | ||||
При анализе способов устранения каждого дефекта выявлены три способа, пригодных для устранения всех дефектов: Слес. мех. до РР, железнение, наплавка под слоем флюса.
3.4 Схема технологического процесса Схема технологического процесса — это последовательность операций, необходимых для устранения дефекта детали. При наличии на детали нескольких дефектов схемы составляются на каждый в отдельности.
Таблица 2 — Схема технологического процесса устранения группы дефектов коленчатого вала двигателя автомобиля Зил 131
Дефект | Способ устранения | № операции | Наименование и содержание операции | Установочная база | |
1 схема | |||||
Износ коренных шеек по наружному диаметру | Слес. Мех. До РР | Шлифовальная: Шлифовать до РР | Центровые отверстия | ||
Отсос: Продуть шейку | Центровые отверстия | ||||
ОТК | Проверить | ||||
2 схема | |||||
Износ шейки вала под приводной шкив | Под слоем флюса | Шлифовальная: Шлифование | Центровые отверстия | ||
Отсос: Продуть шейку | Центровые отверстия | ||||
Наплавка:Наплавить слой метала | Центровые отверстия | ||||
Износ шейки вала под приводной шкив | Под слоем флюса | Токарная: Расточить | Центровые отверстия | ||
Шлифовальная: Шлифовка черная | Центровые отверстия | ||||
Шлифовальная: Шлифовка чистая | Центровые отверстия | ||||
Отсос: Продуть шейку | Центровые отверстия | ||||
ОТК | Проверить | ||||
Износ шпоночного паза под шестерни и приводной шкив | Железнение | Шлифовальная:Шлифовать шейку | Центровые отверстия | ||
Моечная:Промыть деталь | Центровые отверстия | ||||
Обезжиривание:Обезжирить деталь | Центровые отверстия | ||||
Изоляция:Изолировать деталь | Центровые отверстия | ||||
Железнение | Центровые отверстия | ||||
Моечная:Промыть деталь | Центровые отверстия | ||||
ОТК | Проверить | ||||
3.5 План технологических операций Для восстановления деталей применяют разные виды технологий: подефектную, жесткофиксированную, маршрутную и т. п.
Маршрутная технология характеризуется технологическим процессом на определенную совокупность дефектов у данной детали. Таким образом, восстановление детали может производиться несколькими технологическими процессами, в зависимости от сочетания дефектов. Этот способ имеет наибольшее распространение в авторемонтном производстве, его и следует применять при выполнении курсового проекта.
Маршрут ремонта должен предусматривать технологическую взаимосвязь сочетаний дефектов со способами их устранения. Для составления маршрутной карты подготовительным этапом является план технологических операций.
Таблица 3 — План технологических операций устранения группы дефектов коленчатого вала ДВС 508.10.
Операция | Наименование и содержание операции | Оборудование | Приспособления | Инструменты | Габариты | ||
Рабочий | Измерительный | ||||||
Шлифовальная: Шлифовать шейки до РР | Шлифовальный станок модели 3420 | Приспособления для крепления | Шлифовальный круг | МК 100−1 | 2800х | ||
Отсос: Продуть шейки | Промышленный пылесос | Шелевые насадки | Пневматический пистолет | ; | 300х | ||
ОТК | ; | ; | ; | ; | ; | ||
Шлифовальная: Шлифовать шейки | Шлифовальный станок модели 3420 | Приспособления для крепления | Шлифовальный круг | МК 100−1 | 2800х | ||
Отсос: Продуть шейки | Промышленный пылесос | Шелевые насадки | Пневматический пистолет | ; | 300х | ||
Наплавка: Наплавить слой металла | Переоборудованный токарный станок | Приспособления для крепления | Электро сыпучий флюс | ; | 2355х | ||
Токарная: Расточить до нужного диаметра | Токарный станок модели 1616 | Приспособления для крепления | Шлифовальный круг | МК 100−1 | 2355х | ||
Шлифовальная: Шлифовать шейки (грубо) | Шлифовальный станок модели 3420 | Приспособления для крепления | Шлифовальный круг | МК 100−1 | 2800х | ||
Шлифовальная: Шлифовать шейки | Шлифовальный станок модели 3420 | Приспособления для крепления | Шлифовальный круг | МК 100−1 | 2800х | ||
Отсос: Продуть шейки | Промышленный пылесос | Шелевые насадки | Пневматический пистолет | ; | 300х | ||
ОТК | ; | ; | ; | ; | ; | ||
Шлифовальная: Шлифовать поверхность | Шлифовальный станок модели 3420 | Приспособления для крепления | Шлифовальный круг | МК 100−1 | 2800х | ||
Шлифовальная: Шлифовать поверхность | Шлифовальный станок модели 3420 | Приспособления для крепления | Шлифовальный круг | МК 100−1 | 2800х | ||
Отсос: Продуть деталь | Промышленный пылесос | Шелевые насадки | Пневматический пистолет | ; | 300х | ||
Обезжиривание: Обезжирить деталь | Стол | Ацетон | Кисть | ; | 1500х | ||
Изоляция: Изолировать поверхность | Стол | Раствор | Кисть | ; | 1500х | ||
Железнение: | Ванна | ; | Состав | МК 100−1 | 1500х | ||
Моечная: Промыть деталь | Ванна | Вода | Содовый раствор | ; | 1500х | ||
ОТК | ; | ; | ; | ; | ; | ||
4. РАЗРАБОТКА ОПЕРАЦИЙ ПО ВОССТАНОВЛЕНИЮ ДЕТАЛЕЙ
4.1 Исходные данные Коленчатый вал двигателя автомобиля Зил 131
Деталь — Кол. вал ДВС 508.10
Материал — Сталь 40ХФА;
Твердость HRC 52—62;
Масса — не более 20 кг;
Оборудование — Шлифовальный станок модели 3420;
Приспособление — Тиски на поворотных столах;
Установка детали — в центрах;
Режущий инструмент — Шлифовальный круг;
Условия обработки — Без охлаждения;
4.2 Содержание операции
1. Операция наплавочная.
2. Операция механической обработки (шлифовка)
4.3 Определение припусков на обработку Определение припусков на обработку необходимо для дальнейшего расчета режимов обработки. Правильно выбранные величины операционных припусков влияют на качество обработки и себестоимость ремонта деталей. При этом следует учитывать величины межоперационных припусков, требуемую толщину наращиваемого слоя.
Железнение Определить припуски на обработку при Железнение шпоночного паза под шестерни и приводной шкив ДВС 508.10:
Номинальный размер dном=10−0,015−0,065.
Принимаем к расчету dном=10.
т.е.dmax=10,534,14;dmin=10,1 мм.
Ремонт требуется при dдоп=10,1
Предположим, диаметр изношенного отверстия dизм=10. Перед железнением деталь шлифуют «как чисто» для устранения следов износа и придании правильной геометрической формы.
Припуск на шлифование «как чисто» составит:
мм Где, — припуск на чистовое шлифование, мм.
С учетом шлифования «как чисто» диаметр втулки составит:
Dmin=10+0,1=10,1, мм.
Для восстановления отверстий следует нанести слой металла (железнением) такой толщины, чтобы после обработки обеспечить размеры и шероховатость по рабочему чертежу, выполнив предварительную и окончательную обработки.
Определяем припуск на шлифование после железнения.
Предварительное: мм.
Окончательное: мм.
Таким образом, максимальный размер после железнения должен быть:
.
Dmax=10+0,5+0,034=10.534,мм.
Следовательно, толщина гальванического покрытия должна быть не менее, мм Н=(10,534−10,1)/2=0,217
Результаты расчета Шлифование до железнения «как чисто».
Припуск мм.
Толщина железнения Н=0,217 мм.
Шлифование после железнения:
— предварительное мм.
— окончательное мм.
Наплавка под слоем флюса Определить припуски на обработку при восстановлении наплавкой под слоем флюса износа шейки вала под приводной шкив. Диаметр изношенных посадочных поясков под гильзы цилиндра dизм=49.97 мм.
Перед наплавкой требуется обработка для устранения неравномерности износа. В данном случае — расточка.
Припуск на предварительную обработку. Принимаем .
Минимальный диаметр составит:
мм
Dmin=49.97+2•1= 51.97
На этот размер наплавляется слой толщиной Н.
После наплавки деталь обрабатывается до номинального размера шлифованием. Шлифование в зависимости от требуемой чистоты поверхности должно быть в 2−3 стадии:
— черновое — для обдирки наружной сварочной корки
мм Принимаем мм.
— чистовое — для обработки до размера по рабочему чертежу
мм.
Номинальный диаметр гильзы:
Dном=50−0,025 мм.
Принимаем Dном=50 мм .
Диаметр наплавленной гильзы составит:
мм
Dmax=50−2•0.4−2•0.05=49.1
Толщина наплавленного слоя равна:
мм
H=(51.97−49.1)/2=1.435, мм Если известны размеры детали до обработки и после обработки, то припуск на обработку определяется так:
4.4 Расчет режимов обработки Режимы обработки следует определять по каждой операции в отдельности с разбивкой на переходы. Параметры режимов обработки следующие:
наплавка автоматическая — сила сварочного тока, скорость наплавки, шаг наплавки, высота наплавленного слоя за один проход, положение шва, присадочные материалы и др.;
гальваническое покрытие — атомная масса, валентность, электрохимический эквивалент, выход металла по току, плотность и др.
Нормирование для наплавки под слоем флюса:
мин где:
— длина наплавляемой поверхности детали, мм (определяется по рабочему чертежу);
n — частота вращения детали, об/мин;
S — подача сварочной головки, мм/об;
i — число слоев наплавки.
To=(50(•3,14)/(4•100))•2=0,7,мин-принимаем 1 мин.
Нормирование для железнение:
где: Н — толщина слоя покрытия на сторону с учетом припуска на шлифование, мм.
г — плотность осажденного метала, г/см3
Dk = плотность тока на катоде, А/дм2
с — электрохимический эквивалент, теоретическое количество металла, выделяющегося на катоде в процессе электролиза, г/А· ч;
з — коэффициент выхода металла по току.
То=(10•60•0,217•7,7)/(50•1,042•90)=21,38 мин — принимаем 22 мин
5. ГРАФИЧЕССКАЯ ЧАСТЬ
5.1 Расчет годовой трудоемкости работ на участке При проектировании участков восстановления деталей годовой объем работ используемый для определения количества производственных рабочих, рассчитывается по формуле:
чел.-ч.
где:
t — трудоёмкость на единицу продукции и для заданных условий, чел.-ч.;
n — число одноименных деталей в изделии;
N — годовая программа;
— маршрутный коэффициент ремонта.
Тг=0,6•1•6800•3,5=14 280, чел.-ч.
5.2 Расчет количества производственных рабочих на участке Количество ремонтных рабочих на проектируемом участке определяется по формуле:
чел.,
где:
— годовая трудоёмкость работ на участке, чел.-ч.;
— действительная годовой фонд времени рабочего, ч.
Мс=14 280•1840=7,7 чел, принимаем 7 чел
5.3 Расчет количества основного оборудования на участке Где, — годовая трудоёмкость работ на участке, чел.-ч.;
— действительная годовой фонд времени работы оборудования, ч.
Хо=14 280/1050=13.6, принимаем 13 мест рабочего оборудования
5.4 Расчет площади участка Площадь производственного участка рассчитывается исходя из суммарной площади, занятой оборудованием и инвентарем, и коэффициента требуемой плотности расстановки оборудования на соответствующем участке по формуле:
где: Fоб — суммарная площадь горизонтальной проекции технологического оборудования и организация оснастки, м2;
Кn — коэффициент плотности расстановки оборудования
Fy=13,324 4=53,296 м². принимаем участок со сторонами 54 м²
Для расчета суммарной площади горизонтальной проекции технологического оборудования и организационной оснастки составляется сводная ведомость технологического оборудования и организационной оснастки по следующей формуле указанной в таблице, ведомости технологического оборудования и организационной оснастки.
Таблица 5 — Ведомость технологического оборудования и организационной оснастки
№ п/п | Наименование | Тип или модель | Количество | Размеры в плане, мм | Общая площадь, м2 | |
Шлифовальный станок | 2800×1700 | 4,76 | ||||
Токарный станок | ; | 2355×852 | ||||
Переоборудованный токарный станок | Универсал | 2355×852 | ||||
Пылесос | ; | 300×200 | 0,06 | |||
Стол | ; | 1500×750 | 2,25 | |||
Ванна | ; | 1500×750 | 2,25 | |||
Стелаж для готовых деталей | ; | 600×400 | 0,24 | |||
88 8 | Стелаж для инструментов | ; | 1200×500 | 0,6 | ||
Тележка для деталей | ; | 800×500 | 0,4 | |||
ИТОГО: | 14,564 | |||||
В ведомость технологического оборудования и технологической оснастки включается всё основное и вспомогательное технологическое оборудование и организационная оснастка проектируемого участка.
6. Организация труда на производственном участке Порядок составления проектов организации труда на производственных участках авторемонтных предприятий.
Общая характеристика участка:
Порядок составления проектов организации труда на производственных участках авторемонтных предприятий Общая характеристика участка:
1 Вид выполняемых работ — слесарная, станочная, наплавочная;
2 Производственная площадь — 54, м2
3 Тип производства — серийное;
4 Вид характеристики производственного процесса — механизированный;
5 Вид системы управления — централизованное управление производством;
По результатам определения числа рабочих мест и закрепления их за работающими составим карту расстановки рабочих по рабочим местам:
Таблица 6 — Карта расстановки рабочих по рабочим местам
Наименование основной работы выполняемых на рабочем месте | Требуемая профессия работящего | Разряд выполняемой работы | Возможные совмещения с работами на рабочем месте | Состав применяемого оборудования и технологической оснастки | |
Продувка | слесарь | слесарная | Компрессор, воздушный пистолет | ||
Наплава под слоем флюса | сварщик | ; | Переоборудованный токарный станок | ||
Расточка | токарь | фрезеровщик | Шлифовальный станов модели 3420 | ||
Шлифование | шлифовщик | слесарь | Шлифовальный станов модели 3420, Нутромер, ШЦ1−125−0,1 | ||
Железнение | гальваник | ; | Подвеска для железнения; микрометр; ванна для железнения | ||
6.1 Охрана труда Под охраной труда понимают систему законодательных актов и соответствующих им мероприятий, направленных на сохранение здоровья и работоспособности трудящихся. Система организационных и технических мероприятий и средств, предоставляющих предотвращение производственный травматизм, носит название техники безопасности.
Производственная санитария предусматривает мероприятия по правильному устройству и содержанию промышленных предприятий и оборудования (надлежащее освещение, правильное расположение оборудования и т. д.) создание наиболее здоровых и благоприятных условий труда, предотвращающих профессиональные заболевания рабочих. КЗоТ является основным положением по охране труда.
Техника безопасности при выполнении работ Для предупреждения производственного травматизма в каждом предприятии необходимо:
— инструктировать по безопасным приёмам работы;
— контролировать соблюдение правил техники безопасности.
Техника безопасности в топливном цехе:
— при снятии агрегатов и деталей, связанных с большим физическим напряжением, а также при неудобстве в работе следует применять приспособления и съёмники, обеспечивающие безопасность выполнения данной работы;
— при разборке снимать, транспортировать и устанавливать тяжеловесные узлы следует при помощи подъёмно-транспортных механизмов, оборудованных приспособлениями, захватами, гарантирующими полную безопасность работ;
— запрещается пользоваться электроинструментом с неисправной изоляцией или отсутствием заземления.
Кроме изучения инструкций предусматривается вводный инструктаж при поступлении на работу, инструктаж на рабочем месте, дополнительные инструктажи и обучение по специальной программе.
Вводный инструктаж проводится в целях ознакомления поступающих на работу с общей производственной обстановкой и особенностями работы предприятия, с опасностями, встречающимися при работе на предприятии.
Инструктаж непосредственно на рабочем месте является практическим показом безопасного приёма труда.
Заключение
В данном проекте рассматривается вопрос разработки технологического процесса ремонта маховика двигателя автомобиля ЗИЛ-508.10 в условиях авторемонтного предприятия с годовой производственной программой КР.
Произведен расчет производственной партии ремонтируемых деталей за один день работы АРП.
В следующем разделе проекта произведена разработка технологических операций для восстановления детали в условиях АРП.
В четвертом разделе проекта произведена разработка технологических операций для восстановления детали в условиях АРП.
В пятом разделе произведен расчет норм времени на выполнение технологических операций по восстановлению детали с разными дефектами.
В следующем разделе мною выполнена технологическая документация на технологический процесс восстановления детали в виде марки двух операционных карт и двух карт эскизов.
Исходя из вышеизложенного считаю, что цель, поставленная в задании на курсовой проект, выполнены в целом на достаточно высоком техническом уровне.
1. Ремонт автомобилей. Под ред. Румянцева С. И. М., Транспорт, 1981.
2. Клебанов В. Б. и др. Ремонт автомобилей. М., Транспорт, 1974.
3. Боднев А. Г., Шаверин Н. Н. Лабораторный практикум по ремонту автомобилей. М., Транспорт, 1984.
4. Матвеев В. А., Пустовалов И. И. Техническое нормирование ремонтных работ в сельском хозяйстве. М., Колос, 1979.
5. Дехтеринский Л. В. и др. Технология ремонта автомобилей. М., Транспорт, 1979.
6. Оборудование для ремонта автомобилей. Под ред. Шахнева М. Н., Транспорт, 1979.
7. Справочник технолога авторемонтного производства. Под ред. Малышева А. Г., Транспорт, 1977.
8. Верещак Ф. П., Абелевич Ш. А. Проектирование авторемонтных предприятий. М., Транспорт, 1973.
9. РК — 200 — РСФСР — 1/1 — 2035 — 80. Автомобиль ЗИЛ — 130 и его модификации (без двигателя). Руководство по капитальному ремонту. Минавтотранс РСФСР, техническое управление, 1981.
10. РК-200-РСФСР-2/1−2036;80. Автомобиль ГАЗ — 53А (без двигателя).
Руководство по капитальному ремонту. М., Минавтотранс РСФСР, техническое управление, 1981.
11. РК — 200 — РСФСР — 2/1 — 2056 — 80. Двигатели ЗМЗ — 53 и ЗМЗ — 672.
Руководство по капитальному ремонту. М., Минавтотранс РСФСР, техническое управление, 1981.
12. РК — 20 — РСФСР — 2025 — 73 (80). Автомобиль ГАЗ — 24 «Волга». Руководство по капитальному ремонту. М., Транспорт, 1976.
13. РД — 200 — РСФСР — 2/1 — 0007 — 76.
Руководство по нормированию технологических процессов капитального ремонта автомобилей. М., Минавтотранс РСФСР, техническое управление, 1978.
14. Классификатор технологических операций в авторемонтном производстве. Росавторемпром, КТВ «Авторемонт», Митикский филиал, 1981.
15. Клебанов Б. В. Проектирование производственных участков авторемонтных предприятий. М., Транспорт, 1975.
16. Липкинд А. Г. и др. Ремонт автомобиля ЗИЛ — 130. М., Транспорт, 1978.
17. Справочник технолога — машиностроителя. М., Машиностроение, 1973,1986.
18. Суханов Б. Н. и др. Техническое обслуживание и ремонт автомобилей. Пособие по курсовому и дипломному проектированию. М., Транспорт, 1985.
19. Методические указания по ремонту автомобилей и двигателей.,
Н. Новгород, 1993.