Обработка криволинейных отверстий в труднообрабатываемом материале
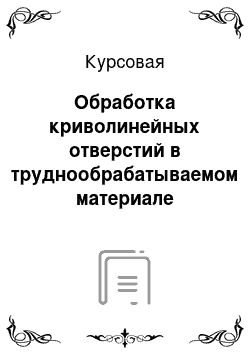
Точность размеров детали и воспроизводимость профиля катода зависят и от локализации процесса, которая определяется составом электролита, плотностью тока, межэлектродным промежутком, характером рабочей поверхности электрода-инструмента и способом изоляции нерабочей части его. Для этого используются покрытие катодов эмалью, капроном, фторопластом-3 и установка эбонитовых втулок. Осаждение… Читать ещё >
Обработка криволинейных отверстий в труднообрабатываемом материале (реферат, курсовая, диплом, контрольная)
Міністерство освіти і науки України Чернігівський державний технологічний університет Кафедра ТМ Розрахунково-графічна робота з дисципліни: «Технологія та обладнання нетрадиційної обробки»
на тему: «Обробка криволінійних отворів у важкооброблюваному матеріалі»
Виконав:
ст. гр. ТМ-001
Івашньов О.В.
Перевірив:
Доцент Микитенко М.Ф.
Чернігів 2003
Содержание Задание 3
1. Электроэрозионная обработка 4
1.1 Описание процесса 4
1.2 Производительность 16
1.3 Точность 18
1.4 Качество поверхности 19
2. Электрохимическая обработка 21
2.1 Описание процесса 21
2.2 Точность 28
2.3 Шероховатость 30
3. Электроэрозионно-химическая обработка 33
Заключение
35
Список использованной литературы 36
Задание Согласно индивидуального задания провести анализ 3 — 4 методов нетрадиционной обработки.
Задание:
Получить криволинейное отверстие в труднообрабатываемом материале.
1. Электроэрозионная обработка
1.1 Описание процесса При электроэрозионной обработке для разрушения металла, снимаемого на данной операции слоя, используется электрический разряд, возникающий при прохождении электрического тока через диэлектрическую среду. Сопутствующее электрическому разряду физическое явление, заключающееся в переносе материала электродов и приводящее к разрушению поверхности одного из них — токопроводящего обрабатываемого, называется электрической эрозией. Поэтому этот способ электрической обработки называется электроэрозионным.
Рис. 1. Схема электроискровой обработки Электроэрозионная обработка осуществляется включением инструмента и обрабатываемой заготовки в цепь электрического колебательного контура, преобразующего непрерывный постоянный ток в импульсы требуемой мощности и частоты. Для этого вначале использовалась только релаксационная схема (рис. 1); в этом случае конденсатор накапливает электрическую энергию и затем быстро отдает ее, развивая большую мгновенную мощность. Учитывая это, электрическую схему делят на два контура; I — зарядный и II — разрядный. Зарядка конденсатора С производится постоянным током, поступающим от генератора или выпрямителя через реостат R; обмотки конденсатора соединены с заготовкой 3 и инструментом 1. Между ними возникает искровой разряд, при этом процесс эрозии имеет ярко выраженный полярный эффект, вследствие которого один электрод (заготовка) разрушается значительно больше другого (инструмента). Форма и размеры разрушения электрода-заготовки достаточно точно воспроизводят форму и размеры электрода-инструмента (рис. 1, б).
Электрический разряд происходит в жидкой среде 2 (маловязких маслах, керосина, этиловом спирте и его водных растворах); жидкость является одним из элементов, создающих механизм эрозионного разрушения, вместе с тем она задерживает материал, переносимый при разряде, обеспечивает быстрое его удаление, а затем быстрое восстановление электрических параметров зазора и понижает температуру катода. Помимо этого в жидкости при прохождении через нее разряда возникают газообразование и гидродинамические явления, создающие дополнительный взрывной эффект, облегчающий разрушение материала срезаемого слоя. При электроэрозионной обработке периодически образуются на обрабатываемой поверхности лунки, накладываемые друг на друга. Выброс металла всегда сопровождается образованием по краям кратера валика. Объем валика составляет около 40% объема лунки (рис. 1, в); его высота соизмерима с глубиной лунки (соответственно 0,2 и 0,22 мм), ширина (около 0,5 мм) равна верхнему радиусу лунки. Если энергию импульса значительно увеличить (до 170 Дж), то на внутренних и наружных склонах валика образуются складки. Они являются результатом растекания металла, выдавливаемого из лунки. Температура, возникающая в разрядном канале, чрезвычайно высока и намного превышает температуру плавления и кипения любого обрабатываемого материала.
Причины образования кратеров при эрозионном разрушении полностью не выяснены. Вначале была предложена гипотеза тепловой природы электрической эрозии, согласно которой искра плавит поверхностный слой и осуществляет его разрушение. Н. И. Лазаренко и Б. Р. Лазаренко разработали электродинамическую теорию искровой электрической эрозии металлов. Они считают, что еще во время разряда под действием электродинамических сил в пораженном импульсом участке анода происходит выброс металла не только расплавленного, но и в твердой фазе, только размягченного. Б. Н. Золотых дает другое объяснение: выброс материала при эрозии является результатом выделения растворенного в металле газа и кипения его во всем объеме прогретой лунки.
Процесс электроэрозионной обработки разделяется на два этапа — съем материала и вынос продуктов обработки из рабочей зоны. Оба этапа представляют собой сложный комплекс физических явлений, в основе которых лежат электротермические процессы.
Электроэрозионное разрушение состоит из двух основных явлений: 1) электрических, приводящих к возбуждению в жидкой диэлектрической среде разряда, и 2) тепловых, вызывающих действие электрического разряда на заготовку.
Электрические явления в рабочем зазоре протекают в две стадии.
1. Подготовка и образование канала сквозной проводимости. При этом происходит вытягивание вдоль силовых линий электрического поля мостиков из токопроводящих частиц, находящихся в жидкости во взвешенном состоянии; нарушение диэлектрической прочности масляной пленки, наступающее при определенном критическом напряжении; постепенное формирование токопроводящего мостика, сопровождающееся ростом силы тока до тех пор, пока мостик не взрывается с образованием ионизированного, хорошо проводящего канала, позволяющего пропустить ток большой силы. Это сопровождается интенсивным нагревом канала и увеличением его диаметра со скоростью распространения ударной волны. Следовательно, причиной образования канала проводимости является неоднородность жидкости.
Таким образом, первая стадия разряда включает в себя две фазы — фазу пробоя (10−8 — 10−7 с) и фазу неустойчивого искрового разряда, проходящего в фазу искродугового разряда (10−4 с). Осциллограммы процесса искрового разряда показывают, что он представляет собой нестационарный дуговой процесс. Для электроискровой обработки эта стадия является завершающей; для электроимпульсной — начальной.
2. Стадия дугового разряда. Электрические процессы характеризуются тем, что ток принимает установившееся значение, его величина определяется только кривой питающего напряжения. Это приводит к большим плотностям тока. Электрическая дуга в этом случае является высококонцентрированным преобразователем электрической энергии в тепловую. Объемная концентрация мощности в этом преобразователе составляет 300 кВт/мм2, а энергия — до 30 000 Дж/мм3. Температура канала разряда в этом случае примерно 5000 °C и более.
Относительная величина съема материала с анода и катода определяется электрическими режимами и теплофизическими константами их материалов. Для второй стадии дуговой наибольший съем металла имеет место в том случае, когда заготовка является катодом. Следовательно, для электроискровой обработки определяющее влияние имеет первая стадия, поэтому оптимальной является прямая полярность, когда заготовка служит анодом. Напротив, для электроимпульсной обработки решающее значение имеет вторая стадия; поэтому оптимальной является обратная полярность (заготовка — катод).
Теплоту, подводимую к электродам, можно представить в виде объемных и поверхностных источников энергии. Объемные источники, т. е. источники, действующие в каждой единице объема электрода, обусловлены эффектом Джоуля-Ленца. Наибольшие температуры в этом случае будут у поверхности, поскольку объемная плотность тока у поверхности резко увеличивается. Поверхостные источники возникают вследствие передачи теплоты из канала разряда на поверхность; распространение его в глубь электрода происходит благодаря теплопроводности. В зависимости от характера протекания тепловых процессов при электроэрозионной обработке съем материала осуществляется следующим образом:
1) путем нагрева поверхности электрода до температуры плавления и непрерывного удаления металла по мере плавления в капельном состоянии (рис. 2, кривая 1);
2) в результате нагрева поверхности электрода до температуры плавления, но с последующим скоплением металла и удалением его в капельном состоянии в конце разряда (кривая 2).
3) удалением материала, когда до окончания разряда происходит его вынос только путем «спокойного испарения» (кривая 4);
4)удалением материала, когда наряду с капельным выбросом в конце разряда имеет место в процессе разряда «спокойное испарение» (кривая 3);
Рис. 2. Зависимость толщины снимаемого слоя h от длительности импульса t и С
5)путем взрывного испарения. Силы, достаточные для взрывного выброса металла при электрической эрозии, получаются при больших токах и мощностях импульса или при средних токах и мощностях, но длительном разряде. Электродинамические силы имеют наибольшую величину у поверхности и тем самым препятствуют выбросу металла. Вследствие этого жидкий металл находится под повышенным давлением и температура его кипения повышается. В результате этого образуются центры испарения, что приводит к взрывному испарению микрообъемов, лежащих ниже наружной поверхности, и к выбросу жидкого металла в виде капель. При малых токах и мощностях электродинамические силы малы; в этом случае эрозионное разрушение происходит путем спокойного испарения. Напротив, при кратковременных разрядах и относительно больших мощностях удаление металла из лунки происходит в виде струй паров, образующихся путем взрывного испарения материала поверхностного слоя. Процесс съема зависит не только от длительности импульса, но и от его мощности. Так, скоростная киносъемка показывает, что при мощностях 300 Вт видна светящаяся зона, свидетельствующая о «спокойном испарении», дальнейшее повышение мощности дает выброс в виде капель металла, а при 1000 Вт и более имеет место съем металла в виде струй паров. Изменение способа съема металла увеличением мощности импульса в 6 раз (с 300 до 1870 Вт) дает повышение удельного объема снимаемого металла в 32 раза.
Следовательно, решающее значение в эрозионном разрушении имеет теплота, выделяемая в процессе разряда. Она приводит к интенсивному газовыделению, возникновению силы сжатия при действии тепловой волны и появлению термокапиллярных сил. Наряду с этим при эрозионном разрушении действует большое число других физических процессов. Например, раскаленное днище анода вступает в химическое взаимодействие с раскаленной плазмой, образуя химические соединения; последние под действием электрического тока диффундируют глубоко в толщину анода. В результате этих процессов обрабатываемая поверхность при электроэрозионной обработке представляет собой ряд лунок отвердевшего металла; на нее накладываются сфероидальные оплавленные выступы, представляющие собой приваренные диспергированные частицы металла. Поверхность покрывается темной пленкой из осевших и спекшихся с металлом электрода мельчайших частиц продуктов пиролиза керосина, имеющей следы оголенных оплавленных участков. Эрозионностойкая пленка, постепенно покрывая рабочую поверхность электрода, защищает его от термического воздействия разряда. Поэтому, подбирая оптимальные режимы, можно осуществить электроэрозионную обработку с пониженным износом инструмента. В этом случае необходимо получить динамическое равновесие, с тем, чтобы среднее количество образующейся пленки равнялось ее убыли за счет эрозии. Рассмотрение строения пленок показывает, что продукты пиролиза и образующаяся на аноде пленка имеют кристаллическую структуру. Образование этой пленки вызвано распадом рабочей среды под действием электродов после окончания разряда. В зависимости от свойств среды образование пленки протекает преимущественно или на аноде, или только на катоде. Структурная схема электроэрозионной обработки показана на рис. 3.
Электроэрозионная обрабатываемость является определенным свойством данного материала, так как при изменении параметров импульса изменяется абсолютное число импульсов, необходимых для выброса 1 см³ обрабатываемого материала; однако относительный порядок их расположения остается неизменным. Интенсивность эрозионного разрушения определяется: 1) теплофизическими параметрами обрабатываемого материала (температурой и теплотой плавления и испарения, теплоемкостью и теплопроводностью); 2) режимами обработки — электрическими (энергией, длительностью и частотой действия импульса) и механическими (кинематикой обработки, режимами подачи, жесткости) и 3) свойствами межэлектродной среды (электропроводностью, текучестью, вязкостью, насыщенностью газами и парами).
Электроэрозионной обработке поддаются только токопроводящие материалы; электроэрозионная обрабатываемость материалов определяется критерием Палатника:
где с — теплоемкость в калг/град;
— плотность в г/см3;
— теплопроводность в калсм2/градг;
Т — температура плавления металла в °С.
Рис. 3. Структурная схема электроэрозионной обработки Производительность электроэрозионной обработки характеризуется количеством снятого металла в единицу времени (измеряется в мм3/мин, г/мин); помимо обрабатываемости материала она зависит от режимов обработки и в первую очередь от мощности N, реализуемой в межэлектродном промежутке:
W = CN,
где
N = Аf,
С — коэффициент, определяющий влияние всех других факторов и прежде всего теплофизических свойств материала;
А — энергия единичного импульса в Втс;
f — частота действия импульсов в Гц.
Рис. 4. Способы улучшения эвакуации продуктов обработки из межэлектродного промежутка: а — нагнетанием жидкости сквозь полый обрабатывающий электрод: б — созданием разрежения, выбрасыванием жидкости из сопла; в — нагнетанием жидкости через полый электрод и вокруг создаваемого отверстия; г — нагнетанием и отсасыванием жидкости; д — использованием ступенчатого электрода; 1 — диск для черновой обработки; 2 -диск для чистовой обработки.
Способ и скорость удаления продуктов разрушения из зоны обработки оказывает решающее влияние на производительность и точность обработки. При электроэрозионной обработке удаление продуктов разрушения может быть естественным и искусственным. В первом случае удаление продуктов происходит под действием динамических сил электрического поля, а также давления выделяющихся газов. При изготовлении деталей с достаточно глубокими полостями во многих случаях этого оказывается недостаточно. Поэтому применяется искусственная система удаления продуктов разрушения в виде специальных систем (рис. 4).
Производительность электроэрозионной обработки зависит также от сочетания видов металлов обоих электродов, площади и относительной глубины обработки. При малой площади или большой относительной глубине прошиваемого отверстия обильное газовыделение и образующиеся продукты разрушения не позволяют задавать в рабочем зазоре значительные мощности. Поэтому увеличение площади до определенного предела ведет к росту производительности. При очень больших площадях происходит снижение производительности вследствие ухудшения условий удаления продуктов эрозии из рабочего зазора; при этом скопления металлических частиц затрудняют бесперебойное повторение импульсов. Поэтому во всех случаях применяют системы принудительного циркулирования жидкости в рабочем зазоре, а также выполняют один электрод вибрирующим или вращающимся.
Интенсивность эрозионного разрушения определяется количеством выделяемой за один разряд энергии, а также временем разряда: чем оно меньше, тем больше энергии концентрируется в одном разряде; вследствие чего разряд имеет большую температуру и интенсивность съема металла. Передача теплоты внутрь обрабатываемой поверхности требует некоторого времени. Это определяет оптимальное соотношение энергии и продолжительности разряда; оно зависит от теплопроводности материала заготовки и его склонности к образованию поверхностных разрушений при локальном нагреве. Продолжительность интервалов между импульсами определяется временем, необходимым для деионизации межэлектродного зазора и удаления из него продуктов эрозии и газовых пузырьков. Большое значение при этом имеют гидрои газодинамические процессы. Таким образом, основными параметрами периодических импульсов определенной формы являются продолжительность импульса, скважность, амплитуда и частота.
Энергия импульса W (измеряется в Дж) определяет количество материала, удаляемого при электроэрозионной обработке единичным разрядом, т. е. размеры лунки.
Длительность импульса tи (измеряется в мкс) определяет время действия импульса по току или э. д. с. При электроискровой обработке tи<10−4 с, при электроимпульсной tи>10−4 с. Значение длительности импульса определяет условия электроэрозионного разрушения и прежде всего тепловой режим, а также надежность удаления материала. При малых tи (до десятков микросекунд) энергия выделяется в течение очень короткого времени; поэтому температуры очень высоки и вместе с тем теплота не успевает распространиться внутрь детали. В этом случае происходит надежное удаление продуктов разрушения. Поэтому малые длительности импульса применяются для электроэрозионной обработки материалов с высокой температурой плавления или склонных к образованию микротрещин (например, металлокерамических). Большие длительности импульса (до нескольких тысяч микросекунд) применяются для обработки обычных сталей и сплавов; в этом случае теплота проникает на большую глубину и тем самым лучше расплавляет металл. Этот процесс электроэрозионной обработки энергетически более выгоден.
Скважность импульса q определяется как отношение времени (периода) повторения импульса Т к длительности импульса tи, т. е. q=T/tи; иногда применяется обратный термин — коэффициент заполнения 1/q.
Следует различать скважность импульсов по току и по э. д. с; первая характеризует скважность импульсов под нагрузкой, вторая — на холостом ходу. Для электроискровой обработки q>5−10, а для электроимпульсной q<5. При малой скважности ухудшаются условия удаления продуктов разрушения.
Амплитуда, А определяет максимальные значения тока и напряжения, получающиеся при каждом импульсе; при электроэрозионных методах обработки амплитуды импульсов тока составляют от долей до десятков тысяч ампер, а амплитуды импульсов напряжения — от десятков до нескольких сотен вольт.
Частота импульсов f определяется периодом, т. е. временем между началом действия смежных импульсов Т, т. е.
f=1/T Гц.
При электроэрозионной обработке f=0,5102 — 2106 Гц.
Рассмотренные параметры электроэрозионной обработки, связаны между собой следующими зависимостями:
С повышением частоты при той же энергии импульса растет производительность электроэрозионной обработки. Пределы роста частоты определяются условиями деионизации рабочего зазора и удаления из него продуктов разрушения.
Непосредственный контроль параметров импульса в рабочем промежутке затруднителен; поэтому во многих случаях режимы характеризуются параметрами генераторов. Для обработки применяют генераторы двух типов. Генераторы I типа называются зависимыми или релаксационными; параметры задаваемых ими импульсов (ток, напряжение) определяются нелинейностью сопротивления рабочего зазора. Генераторы II типа называются независимыми или импульсными; задаваемые ими импульсы создаются без использования нелинейных свойств рабочего зазора. При релаксационных схемах параметры импульса характеризуются емкостью конденсаторов, величиной зарядного тока, напряжением; при импульсных — напряжением и силой тока в импульсе, длительностью импульса, частотой их следования.
При электроэрозионной обработке происходит разрушение одновременно и анода, и катода, т. е. заготовки и инструмента. Одним из средств снижения износа инструмента является применение униполярных импульсов, т. е. импульсов, при которых ток не меняет своего направления. Условно принято называть полярность прямой, если происходит преимущественно эрозионное разрушение анода, и обратной, если происходит прежде всего разрушение катода.
1.2 Производительность Производительность процесса электроэрозионной обработки оценивается отношением объема или массы удаленного металла ко времени обработки.
Если бы удалось вести процесс при постоянной энергии импульсов, производительность можно было бы оценить как произведение энергии импульсов на их частоту. На практике условия протекания отдельного импульса могут отличаться из-за различий в состоянии межэлектродного промежутка и размера зазора, несоответствие между числом импульсов, выработанных генератором и реализуемых в зазоре.
Для получения высокопроизводительного режима необходимо, чтобы как можно больше импульсов участвовало бы в процессе эрозии.
Повысить производительность можно, если подобрать оптимальное сочетание факторов, позволяющих увеличить долю полезной энергии импульса, его мощность и частоту следования рабочих импульсов. Для этого необходимо достичь оптимального соотношения между максимальным значением силы тока в импульсе и его длительностью.
Зависимость: производительность — площадь обработки — мощность. При малой площади обработки число участков, на которых возможен разряд, значительно меньше, чем число импульсов, поступающих от генератора, так как часть площади перекрыта газовыми перекрыта газовыми пузырями от предшествующих разрядов. Время существования газового пузыря в 5…10 раз больше, чем длительность импульса. А разряд через газ возможен только при более высоком напряжении, поэтому часть импульсов генератора не вызывает эрозии. Снижается производительность.
Если увеличивать площадь обрабатываемой поверхности, то скорость съема материала металла будет возрастать, но в дальнейшем произойдет ее снижение. Это объясняется тем, что с течением времени ухудшаются условия удаления продуктов обработки из межэлектродного промежутка. Все большее число импульсов генератора не будет вызывать эрозии из-за накопления газов и металлических частиц в пространстве между электродами.
Количество продуктов обработки зависит также от энергии импульсов, их числа и времени действия, т. е. от мощности, реализуемой в межэлектродном промежутке. При малой мощности количество расплавленного металла невелико, с ростом подводимой мощности оно возрастает, но при этом увеличивается и количество продуктов обработки, которые тормозят процесс съема металла. Для получения высокой производительности необходимо правильно выбрать сочетание площади обрабатываемой поверхности и мощности. Такой выбор выполняют с помощью пространственных диаграмм в координатах силы тока — площадь обработки — производительность.
Зависимость производительности от глубины внедрения электрода-инструмента. По мере углубления отверстия усложняется удаление продуктов обработки и поступление свежей жидкости в межэлектродный промежуток. Наличие большого количества электропроводных капель застывшего металла вызывает импульсы, энергия которых тратится на расплавление таких частиц. Для предотвращения таких (паразитных) импульсов используют принудительную прокачку жидкости через межэлектродный промежуток под давлением 100…200 кПа.
Прокачку можно применять и при периодическом прекращении процесса с выведением электрода-инструмента из заготовки; используют также вибрацию электродов, их вращение и др.
Влияние на производительность свойств рабочей среды. В зависимости от свойств рабочей среды изменяются доля полезного использования энергии импульса, его предельная мощность. Для каждого вида обработки применяют оптимальные диэлектрические среды. Так, при электроэрозионном процессе с малой энергией импульсов высокую производительность обеспечивает дистиллированная и техническая вода, керосин; при грубых режимах на электроимпульсном режиме применяют тяжелые фракции нефти (масла, дизельные топлива и др.) с высокой температурой вспышки (до 450 К).
В процессе обработки жидкая рабочая среда загрязняется, из-за чего снижается производительность. Загрязненность оценивают в процентном отношении массы продуктов обработки к массе жидкости. При загрязненности 4…5% для черновых и 2…3% для чистовых процессов производительность остается практически одинаковой по сравнению с чистой средой. Дальнейшее возрастание содержания продуктов обработки, особенно на чистовых режимах приводит к снижению числа рабочих импульсов и производительности.
В процессе остывания частицы металла вызывают испарение части жидкости, изменение ее вязкости и зольности. Для поддержания высокой производительности необходимо периодически заменять рабочую среду.
Для повышения производительности на обрабатываемой площади может быть параллельно размещено несколько электродов-инструментов. Если они подключены к одному генератору импульсов, то такая обработка называется многоэлектродной. При подключении каждого электрода к своему источнику энергии обработку называют многоконтурной.
1.3 Точность Под точностью обработки деталей понимается степень соответствия ее формы и размеров чертежу. Отклонения от формы и размеров называется погрешностью.
Также как и при механической обработке, на размеры погрешности оказывают влияние состояние технологической системы, погрешности установки, базирования инструментов, внутренние напряжения в материале заготовки, ее нагрев при обработке.
В процессе обработки форма и размеры электрода-инструмента нарушаются из-за износа. Износ на различных участках инструмента различен. Так, на участках инструмента, имеющих вогнутость, число разрядов меньше, следовательно, износ на них будет выражен слабее. Если учесть условия выноса продуктов обработки из промежутка, то различия в износе различных участков еще более возрастут.
Чтобы снизить влияние износа электродов-инструментов на точность изготовления, а) изготовляют инструмент из материала, стойкого к эрозии, например из вольфрама, меднографита, коксографитовых композиций; б) используют так называемые безизносные схемы, при которых часть материала заготовки или из рабочей среды осаждают на инструменте, компенсируя тем самым его износ; в) заменяют изношенные участки инструмента путем продольного перемещения, или заменяют весь инструмент; г) производят правку и калибровку рабочей части инструмента.
1.4 Качество поверхности В результате электроэрозионной обработки поверхность приобретает характерные неровности, а приповерхностные слои металла притерпевают физико-химические изменения. Это оказывает влияние на эксплуатационные показатели обрабатываемых деталей.
Поверхностный слой формируется за счет расплавленного металла, оставшегося на поверхности лунки, и прилегающего к ней слоя металла, подвергнутого структурным изменениям от быстрого нагрева и охлаждения металла. Поверхностный слой состоит из так называемого белого слоя, в котором наблюдаются химико-термические превращения, переходного слоя, в котором имели место только термические изменения и под которым находится неизмененный металл заготовки. Измененная зона, образуемая белым слоем, содержит продукты диэлектрической среды, в частности углерод и элементы, входящие в состав электрода-инструмента. У остальных заготовок в этой зоне образуются карбиды железа, которые способствую упрочнению поверхности.
Состояние поверхностного слоя определяет износостойкость, прочность и другие свойства детали в механизме. После электроэрозионной обработки поверхностный слой приобретает свойства, по-разному влияющие на эксплуатационные характеристики деталей. Положительными являются повышение твердости поверхности при сохранении вязкости середины, большое количество лунок на поверхности, плавное их сопряжение. К недостаткам следует отнести возможность появления трещин, растягивающих напряжений, трудность получения поверхности с малой шероховатостью.
Схема электроэрозионной обработки криволинейного отверстия: 1 — обрабатываемая заготовка; 2 — электрод-инструмент.
2. Электрохимическая обработка
2.1 Описание процесса Электрохимический метод обработки создан советскими инженерами В. Н. Гусевым и Л. П. Рожковым в 1928 г.; особенностью его по сравнению с обычной электролитической схемой является наличие в зазоре интенсивного движения электролита при высоких плотностях тока (от десятков до сотен ампер на 1 см² обрабатываемой поверхности). Электрохимическая обработка является перспективным методом изготовления деталей из труднообрабатываемых материалов; она обеспечивает шероховатость поверхности до 1,25 — 0,16 мкм и точность обработки до ±20 мкм, а также большую производительность (до 1500 -2000 мм3/мин). Электрохимическую обработку осуществляют следующим образом (рис. 5): заготовку 1 соединяют с положительным полюсом источника постоянного тока (анод); инструмент 2 (катод) является отрицательным полюсом; при этом профиль катода соответствует профилю поверхности, которую необходимо получить в результате обработки. Заготовку и инструмент помещают в камеру, изготовленную из неэлектропроводного материала. Подача электролита в зазор между анодом и катодом приводит к замыканию электрической цепи и в результате этого к растворению поверхности анода, т. е. обрабатываемой заготовки.
Основой электрохимической обработки является процесс локального анодного растворения, происходящий при высокой плотности постоянного тока в проточном электролите. При съеме материала происходит изменение конфигурации межэлектродного зазора, что вызывает перераспределение плотности электрического тока, изменение гидродинамических условий и как следствие этого — копирование профиля катода. Интенсивное движение жидкости обеспечивает стабильный и высокопроизводительный процесс анодного растворения, вынос продуктов растворения из рабочего зазора и отвод теплоты, возникающей во время обработки.
Рис. 5. Схема (а) и установка (б) для электрохимической обработки: 1 — камера-контейнер; 2 — электродвигатель системы подачи катода-инструмента; 3 — винт, 4 — катод-инструмент для обработки впадины лопатки; 5 — заготовка; 6 — манометр; 7 — катод и инструмент для обработки спинки лопатки; 8 — распределительная камера; 9 — насос для подачи электролита; 10 — ванна с электролитом; 11 — теплообменник; 12 — центрифуга; 13 — подпорный вентиль.
Электрохимическую обработку осуществляют на специальной установке, состоящей из источника питания постоянным током, гидросистемы, подающей электролит в рабочий зазор, механизма, обеспечивающего заданную кинематику процесса и контрольных устройств. Для получения достаточно больших плотностей тока необходимы агрегаты, дающие напряжение 5−30 В; это требует защиты и изоляции токопроводящих частей и камеры от остальной части установки. Для электрохимической обработки, требующей больших величин силы тока (10 000 А и выше), при проектировании электросистемы следует уделять особое внимание разработке рациональной системы подвода тока к электродам с минимальными потерями. К системе гидрооборудования относятся системы для подачи электролита и для прокачки охлаждающей жидкости, а также очистные устройства (фильтры, отстойники, центрифуга). Электрохимический метод используют для обработки наружных и внутренних поверхностей деталей (рис. 6).
Рис. 6. Схемы электрохимической обработки: а — обработка плоской поверхности при поступательном движении инструмента и неподвижной детали; б — обработка цилиндрической фасонной поверхности при подаче инструмента и вращении детали; в — кольцевое сверление при подаче инструмента и неподвижной детали; г — сверление глухого отверстия, когда инструмент и деталь неподвижны, д — обработка кольцевого паза, когда инструмент вращается, а деталь неподвижна; е — нарезание внутренних спиральных канавок при вращательно-поступательном движении инструмента и неподвижной детали; 1 — катод; 2 — изоляционный слой; 3 — деталь; 4 — медная трубка, покрытая слоем резины (катод); 5 — патрубок отвода электрода; 6 — патрубок подвода электролита.
Во всех схемах обработки подача электрода осуществляется непрерывно по заранее заданному закону или регулируется в зависимости от интенсивности съема металла, сохраняя при этом оптимальную величину зазора между электродами. Последний метод исключает, с одной стороны, замыкание электродов и, с другой — значительно увеличивает интенсивность растворения и поэтому является наиболее производительным. Для осуществления такого рода обработки применяют автоматические следящие системы.
Контрольные устройства должны обеспечивать измерение важнейших параметров процесса в течение всего цикла обработки и прежде всего силы тока, его напряжения, температуры и скорости движения электролита, его значения рН, характеризующего щелочность или кислотность электролита.
С физической точки зрения в основе процесса электрохимической обработки лежит явление электролиза. Анодное растворение металлов происходит под действием электрического тока, проходящего через электролит, если в электролит погрузить электроды, соединенные с источником постоянного тока. При этом на аноде возможны два процесса: 1) атомы металла, отдавая электроны во внешнюю электрическую цепь, заряжаются положительно; ионы металла вследствие электрической упругости растворения непосредственно переходят в раствор; 2) анионы раствора реагируют с металлом электрода и затем, уже в виде определенных химических соединений, переходят в электролит. Для электрохимического формообразования деталей используют второй процесс; в этом случае под действием внешней э. д. с. слабосвязанные электроны из атомов поверхностного слоя уходят во внешнюю электрическую цепь, разрывая связь этих атомов с массой металла. Положительно ионизированные атомы вступают в реакцию с анионами электролита, образуя соединения, которые или растворяются в электролите, или создают на поверхности пленку. Анодное растворение металлических сплавов под действием постоянного тока в водном растворе поваренной соли NaCl приводит к тому, что в процессе обработки при участии иона хлора Сlобразуется промежуточное соединение с обрабатываемым металлом (Fe, Ni, Сr и др.). Ионы хлора образуют с железом комплекс [FeOH]+Сl-, который в дальнейшем реагируя с ионом ОНпереходит в раствор в виде гидрата закиси железа:
[FeОН]+ Сl- + ОНFe (ОН) 2 + Сl-.
Гидрат закиси переходит в гидрат окиси железа и выпадает в осадок:
4Fe (ОН)2 + О2 + 2Н2О 4Fe (OH)3.
Аналогичные реакции имеют место и с другими элементами обрабатываемого материала.
Во всех случаях на катоде происходит восстановление водорода согласно реакциям:
Н+ + е Н; Н +Н Н2.
Выделяющийся на катоде водород при открытом способе элекрохимической обработки из-за разбрызгивания представляет опасность с точки зрения техники безопасности, и поэтому требует устройства вытяжной системы. При закрытом способе обработки, в камерах водород удаляется с потоком электролита.
Отходы, образующиеся при электрохимической обработке, представляют собой пастообразную массу болотного цвета, содержащую 60−80% воды, 8−10% электролита (например хлористого натрия) и 12−20% окислов и гидратов в виде частичек тонкой фракции.
Структурная схема электрохимической размерной обработки представлена на рис. 7.
Производительность электрохимической обработки определяется количеством вещества, растворенного под действием тока; согласно закону Фарадея оно прямо пропорционально количеству электричества, прошедшего через раствор электролита
G = kIt г,
где k — весовой электрохимический эквивалент обрабатываемого материала в г/а*ч;
I — сила тока в А;
t — время обработки в ч.
Рис. 7. Структурная схема электрохимической обработки.
Для повышения интенсивности съема металла с анода применяют ток большой плотности, доходящей в отдельных случаях до 200 — 250 А/см2. Однако повышение скорости растворения металла при увеличении анодной плотности тока ограничено вторичными процессами, сопутствующими анодному растворению. К ним относится покрытие поверхности анода продуктами солей, которые образуются при анодном растворении. При увеличенных плотностях тока они выделяются в большом количестве и поэтому не успевают раствориться в электролите. Это явление, называемое механическим пассивированием, определяет предел повышения производительности электрохимической обработки за счет увеличения плотности тока, так как этот слой обладает значительным электрическим сопротивлением.
Обрабатываемость материалов электрохимическим процессом определяется видом образующейся на поверхности детали пленки. По этой причине затруднена обработка этим методом титановых сплавов, так как титан и его сплавы обладают большой склонностью к пассивации в водных растворах электролитов. Наиболее вероятной причиной пассивации титана в этих средах является образование на его поверхности защитной пленки, не растворимой в воде и разбавленных кислотах и препятствующей прямому контакту между электролитом и металлом. Для оценки электрохимической обрабатываемости материала по этому параметру можно применить поляризационные кривые снимаемые потенциостатическим способом. Сущность способа заключается в определении плотности внешнего поляризационного тока или скорости анодного металла при задаваемом постоянном значении потенциала. При этом можно определить потенциал металла, при котором он начинает переходить из активного состояния в пассивное, и потенциал полного пассивирования.
Интенсивность растворения анода зависит также от скорости движения электролита. По мере увеличения скорости движения электролита до определенной величины происходит повышение съема металла. Это объясняется тем, что продукты анодного растворения, обладающие значительным омическим сопротивлением, быстрее уносятся из рабочего зазора. Подача свежего электролита между электродами повышается, и соответственно увеличиваются фактическая плотность тока и съем металла. При достижении некоторой предельной величины скорости движения электролита фактор удаления продуктов растворения уже не оказывает заметного влияния на электропроводность раствора, и величина съема металла фактически остается постоянной.
2.2 Точность Точность электрохимической обработки определяется погрешностями изготовления катода и установки заготовки, степенью поддержания постоянства температуры и скорости движения электролита как по времени, так и по отдельным точкам обрабатываемой поверхности, неравномерностью движения электрода, а также рядом других факторов, определяющих устойчивость процесса электрохимического растворения. К ним относятся, например, равномерность поддержания зазора оптимальной величины и постоянство плотности тока. Изменение выхода металла по току в зависимости от его плотности, обусловленное явлениями пассивации и поляризации, приводит к возникновению дополнительных погрешностей. Конструкции входного и выходного отверстий для электролита должны обеспечивать равномерность движения потока в рабочем зазоре, избегая ее турболизации. Наиболее благоприятные условия для равномерного протекания жидкости в межэлектродном промежутке создаются при закрытом способе обработки, когда электроды полностью погружены в электролит; при этом увеличивается съем металла, улучшается точность и снижается шероховатость поверхности. При открытом способе наблюдается известное колебание силы тока, что свидетельствует о периодическом оголении в некоторых местах поверхности электродов.
Определенное влияние на точность обработки оказывает неравномерность снимаемого припуска, так как в начале обработки выступающие участки катода располагаются ближе к плоской поверхности заготовки (анода).
Вследствие этого на этих участках за счет меньшего сопротивления электролита проходит ток большей плотности, что ведет к более интенсивному местному растворению. Таким образом, для того чтобы обработать заданную конфигурацию детали, необходим дополнительный слой металла; толщина его определяется степенью неравномерности припуска и требуемой точностью обработки. Поэтому заготовки, поступающие на обработку, должны иметь минимально необходимый припуск. Он может быть определен по методике, аналогичной методике, предложенной проф. А. П. Соколовским для определения точности механической обработки, или по экспериментальной зависимости, представленной на рис. 8.
Рис. 8. Зависимость величины минимально-необходимого припуска Zmin от максимального зазора sZ mах между электродами: 1 — э = 0,6 мм; 2 — э = 0,3 мм Интенсивность выравнивания припуска характеризуется разностью скоростей съема металла на выступах и впадинах; исходя из законов Фарадея и Ома.
Точность размеров детали и воспроизводимость профиля катода зависят и от локализации процесса, которая определяется составом электролита, плотностью тока, межэлектродным промежутком, характером рабочей поверхности электрода-инструмента и способом изоляции нерабочей части его. Для этого используются покрытие катодов эмалью, капроном, фторопластом-3 и установка эбонитовых втулок. Осаждение на поверхности электрода-инструмента малейшего слоя металла существенно влияет на точность воспроизводимого профиля. Инструмент-катод изготовляют из различных хорошо токопроводящих материалов (меди и ее сплавов, латуни, нержавеющей стали и др.). При монтаже катода следует обеспечивать его изоляцию для защиты от блуждающих токов. При проектировании катода-инструмента надо вводить соответствующую корректировку его формы: например, если необходимо получить плоскую поверхность, то используют электрод-инструмент со слегка выпуклым профилем, так как металл быстрее удаляется с краев заготовки. Кроме того, следует учитывать, что острые углы на поверхности электрода-инструмента на детали не воспроизводятся, места переходов получаются с радиусом не менее 0,2 мм. При изготовлении цилиндрических отверстий надо предусматривать корректировку возникающей конусности. Отсутствие практически износа электрода-инструмента способствует большей точности электрохимического метода обработки.
2.3 Шероховатость Шероховатость поверхности, получающейся после электрохимической обработки, обычно не высока и достигает 1,25 — 0,16 мкм. Она зависит от шероховатости поверхности заготовки и величины припуска, кроме того, на ее величину влияют и другие факторы. Так, с увеличением скорости движения электролита шероховатость поверхности снижается. Увеличение плотности тока при неизменной скорости движения электролита повышает шероховатость поверхности. Поэтому для получения высокого класса чистоты поверхности при электрохимической обработке повышение плотности тока должно сопровождаться увеличением скорости движения электролита. В процессе обработки происходит сглаживание поверхностных неровностей по мере удаления слоев металла с поверхности обрабатываемой заготовки. Эффект сглаживания можно объяснить наличием на поверхности детали тонкого прианодного слоя, отличающегося пониженной электропроводностью.
Наряду с высокой чистотой поверхности электрохимическая обработка не приводит в отличие от обработки резанием к появлению в поверхностном слое микротрещин и остаточных внутренних напряжений. Это объясняется отсутствием значительной нагрузки в системе заготовка-инструмент. Усилия, возникающие в рабочем зазоре при циркуляции электролита с большой скоростью, не вызывают никаких изменений физико-механических свойств поверхностного слоя. При электрохимической обработке сложных по структуре жаропрочных сплавов (например, никелевых) отдельные фазы подвергаются анодному растворению в разной мере. Поэтому в процессе анодного растворения выявляются форма зерен и наличие разных фаз; оба явления ведут к снижению качества поверхности. Это относится и к различным включениям, которые также приводят к неравномерному съему и образованию таких дефектов, как местное растравливание, питтинги, межкристаллитная и внутрикристаллитная коррозия. Наиболее заметны эти дефекты в зонах обработки, имеющих малые плотности тока; при увеличении плотности тока растравливание уменьшается. Улучшение качества поверхности в этом случае объясняется влиянием вязкости концентрированного слоя продуктов растворения анода на электрическую миграцию ионов. Повышение температуры электролита приводит к формированию на поверхности плохо удаляемого слоя и увеличению степени растравливания. Она повышается также с ростом содержания примесей в сплаве. Подбор оптимальных режимов практически исключает эти отрицательные явления. Так, при обработке сплава ЭИ437Б происходило растравливание металла по границам зерен; повышение плотности тока до 50−60 А/см2 ликвидировало это явление.
После электрохимической обработки поверхность имеет матовый оттенок; это требует проведения последующего полирования. Причиной матовости является образование на поверхности тонких пленок; их химический состав определяется реакциями, протекающими между материалом детали и электролитом в процессе анодного растворения; толщина пленок равна примерно 0,003 мм.
Схема электрохимической обработки криволинейного отверстия: 1 — электрод-инструмент; 2 — обрабатываемая заготовка.
3. Электроэрозионно-химическая обработка Электроэрозионно-химическая обработка основана на сочетании электроэрозионной и электрохимической обработки. Применение в качестве рабочей жидкости электролита позволяет при одинаковых напряжениях значительно увеличить межэлектродный зазор. Это улучшает условие удаления продуктов эрозии; кроме того, этому способствует уменьшение их размеров вследствие их частичного растворения.
Механизм возникновения пробоя в электролите резко отличается от пробоя в диэлектрике, так как электролит обладает весьма большой проводимостью. Поэтому в этом случае для создания пробоя необходимо наличие плохо проводящего слоя между электродами и электролитом. Производительность этого метода обработки определяется соотношением между током эрозии и током анодного растворения.
Особые требования при этом методе обработки предъявляются к материалу инструмента; он должен быть теплостойким и прочным и обеспечивать прочное сцепление восстановленного слоя инструмента. Этим требованиям удовлетворяет графит (например, марки ЭЭГ). Для восстановления инструмента рекомендуется вводить в электролит газ, содержащий углерод (пропан). В этом случае при химическом разложении на поверхности инструмента осаждается пироуглерод или пирографит.
Введение
газа снижает износ инструмента с 2,0−2,5% до 0,5−09%. Следует учитывать, что во всех случаях уменьшение доли эрозионного разрушения ведет к снижению интенсивности износа инструмента. Электроэрозионно-химическая обработка рекомендуется для выполнения черновых операций, когда требования точности изготовления невелики, например, для прошивания щелей, отверстий, окон в вырубных штампах, фильер и т. д.
Процесс анодного растворения создает хорошие условия для пробоя промежутка, так как на катоде-инструменте имеется парогазовый слой. Эрозия обрабатываемой поверхности, в свою очередь, способствует удалению пассивирующей пленки, значительно ускоряя диффузию и вынос продуктов обработки.
Электрическая эрозия сильно сказывается на размерах шероховатости поверхности. На ней возникают углубления, которые несколько сглаживаются анодным растворением. Энергоемкость такого метода значительно ниже, чем электроэрозионного. Это объясняется лучшими условиями протекания процесса и за счет этого снижением числа разрядов, не производящих удаление металла.
Заключение
Изобретение электроэрозионной обработки вот уже несколько десятилетий позволяет машинои приборостроителям решать сложные технологические задачи при изготовлении деталей сложной конфигурации из обрабатываемых материалов. ЭЭО позволяет конструкторам и технологам выбрать оптимальный вариант конструкции, материала детали и технологического процесса.
1. Артамонов Б. А., Волков Ю. С. и др. Электрофизические и электрохимические методы обработки материалов. Москва, «Высшая школа», 1983
2. Лившиц А. Л. Электроэрозионная обработка металлов. Москва, «Высшая школа», 1979
3. Подураев В. Н. И Камалов В. С. Физико-химические методы обработки. М., «Машиностроение», 1973, 346 с.