Разработка методов для распознавания дефектов структуры с использованием изображения поверхности паковок
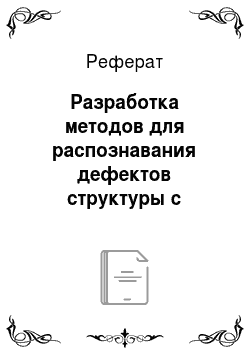
Результаты исследования. Анализ влияния условий съемки на порог бинаризации показал, что для получения приемлемого качества изображения нельзя установить фиксированное значение порога. Оно изменяется в весьма широких пределах от 30 до 240 (в градациях серого). При низком пороге бинаризации хорошо сохраняется изображение нити, но велик уровень шумов. При высоком пороге бинаризации шумы могут… Читать ещё >
Разработка методов для распознавания дефектов структуры с использованием изображения поверхности паковок (реферат, курсовая, диплом, контрольная)
Формирование текстильных паковок высокого качества предполагает обеспечение оптимальной структуры намотки. Параметрами, характеризующими структуру намотки, является в первую очередь расстояния между последовательно укладываемыми витками. Известно, что при формировании паковок фрикционным способом параметры структуры паковок постоянно изменяется [1, 2] по определенному закону. Это приводит к образованию дефектов структуры, в виде последовательно укладываемых на одно и тоже место витков, так называемая жгутовая намотка. С целью устранения жгутовой намотки применяют различные по конструкции механизмы рассеивания витков.
Оценить эффективность работы таких механизмов и качество намотки в целом можно только на основе анализа взаимного расположения витков в готовой паковке. съемка бинаризация изображение дефект Процесс такого анализа является довольно трудоемким и сопряжен со значительной нагрузкой на оператора. Он требует высокого внимания при контроле структур намотки при разматывании паковок в течение значительного времени (около часа). Поэтому создания системы контроля структуры намотки на основе систем технического зрения является актуальной. В работе [3] отражен щпыт авторов по работе над указанной проблемой.
Анализ литературных данных. Одной из первых работ в указанном направлении является [4, 5], где предпринята попытка создания системы контроля структуры намотки на основе аппаратной реализации. Созданная система обладала рядом существенных недостатков, основным из которых надо признать жесткую привязку к одному типу паковок и необходимость вращения паковки, что не позволяло проводить анализ с достаточно большой скоростью.
Развитие вычислительной техники позволило создавать системы анализа параметров структуры намотки, основанные на методах распознавания образца [6, 7]. Используемые в этой работе решающие правила не позволяли анализировать взаимное расположение отдельных нитей, наличие жгутовых образования в теле паковки устанавливалось по отклонениям формы намотки на отдельных диаметрах. Указанные недостатки не позволяли получить удовлетворительное качество анализа.
Достаточно высокую эффективность анализа параметров структуры намотки можно получить путем распознавания отдельных нитей [8−11]. Для идентификации отдельных нитей на поверхности намотки могут применяться различные алгоритмы и системы фильтрация изображения. Анализ наиболее распространенных решений в этой области приведен в [12].
В [13] показано, что наиболее перспективным алгоритмом, на результаты которого не влияют возможные разрывы на изображении нити, является алгоритм на основе преобразований Хоха [14, 15].
Основные теоретические положения. В работе Нуриева М. Н. [3] показано, что на основе преобразований Хоха можно создать надежный алгоритм распознавания дефектов структуры намотки нити на бобину по изображению ее поверхности. Однако такой алгоритм требует значительного объема вычислений и поэтому не может работать достаточно быстро.
Большой объем вычислений связан с тем, что все точки изображения проверяются на принадлежность к определенному классу прямых линий. В том случае, когда анализу подвергается динамическое изображение, мощным средством для сокращения объема вычислений при распознавании его элементов является сравнение последовательно отснятых кадров [16, 17]. При анализе структуры намотки такая возможность появляется в том случае, когда анализируемая бобина разматывается. В этом случае необходимо сравнить два последовательно отснятых кадра, и выделить изображение смотанной между двумя последовательными кадрами нити. Поскольку все остальные изображения на этих кадрах остаются неизменными, то выделить требуемое изображение можно вычитанием яркости соответствующих пикселей друг из друга. В результате вычитания значения разности яркости для всех пикселей статической части изображения принимают значение близкое к нулю, а изменившейся части изображения значение отличной от нуля. Критерием близости разности яркости к нулю служит экспериментально определяемое пороговое значение X. Исходное изображение преобразуется в новое, предназначенное для анализа с помощью преобразований Хоха, по следующему правилу Исходные кадры видеоизображения переводились в серое полутоновое изображение, затем соседние кадры попиксельно вычитались друг из друга, после чего проводилась бинаризация по правилу (1). При этом подбиралось значение порогового уровня X по критерию малого уровня шума при сохранении изображения нитей.
На рис. 2, а показан кадр (720×576 пикселей) исходного видеоизображения бобины, на рис. 3, б — фрагмент (210×170 пикселей) изображения, полученного как разность исходного и следующего за ним кадра. На рис. 3, а показано бинаризованное изображение (порог бинаризации 40 мс). Как видно, после бинаризации уровень шума на изображении высокий. При увеличении порога бинаризации до 120 мс (рис. 3, б) уровень шума на изображении снижается, однако при этом изображение нити не получается сплошным, оно разбито на участки, причем ширина разрывов сравнима с шириной целых участков. Это может создавать определенные трудности для работы алгоритмов распознавания образа нити на изображении.
где f (x, y, i) — значение яркости исходного изображения пикселя с координатами x, у на i-том кадре; d (x, y, i) — значение яркости нового изображения пикселя с координатами x, у на i-том кадре; X — значение порогового уровня (порога бинаризации).
Таким образом, с помощью преобразования по формуле (1) производится бинаризация изображения, что в дальнейшем упрощает процесс распознавания отдельных нитей на поверхности паковки.
Материалы и методы исследования. Для исследования алгоритма были использованы тестовые видео-изображения, полученные с помощью устройства (рис. 1), на которых зафиксирован процесс размотки бобин, сформированных на прядильной пневмомеханической машине БД-120−2 и прядильно-крутильной машине ПК-100.
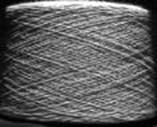
Рис. 1. Схема устройства для контроля качества структуры намотки
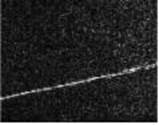
Рис. 2. Изображение поверхности бобины: а — исходное изображение поверхности бобины; б — разностное изображение анализируемого фрагмента
Результаты исследования. Анализ влияния условий съемки на порог бинаризации показал, что для получения приемлемого качества изображения нельзя установить фиксированное значение порога. Оно изменяется в весьма широких пределах от 30 до 240 (в градациях серого). При низком пороге бинаризации хорошо сохраняется изображение нити, но велик уровень шумов. При высоком пороге бинаризации шумы могут практически отсутствовать, но пиксели, изображения нити частично утрачиваются (количество пикселей, принадлежащих нити может уменьшиться в 2−20 раз). Таким образом, порог бинаризации при построении алгоритма распознавания структуры намотки не может быть постоянным. Его назначение оператором внесет большую долю субъективизма в работу системы и существенно замедлит ее работу.
Автоматизировать выбор порога бинаризации можно на основе анализа гистограмм яркости пикселей разностного изображения. В этом случае назначается количество самых ярких пикселей, которое должно остаться на изображении после обработки. Этот параметр должен зависеть от размера изображения, однако в задаче распознавания структуры намотки анализируемый фрагмент изображения может оставаться постоянным, а поэтому количество пикселей изображения после обработки можно зафиксировать на постоянном уровне.
На рис. 4 показана гистограмма яркости пикселей разностного изображения. По гистограмме выбирается порог, при котором после бинаризации останется заданное количество наиболее ярких точек. На рис. 5, а приведено изображение, для которого этот параметр равен 1000 пикселей, что соответствует порогу бинаризации, равному 165 (в градациях серого). Шум на изображении достаточно эффективно устранён. Незначительное количество ярких точек на изображении существенным образом не скажется на эффективности работы алгоритма распознавания нити.
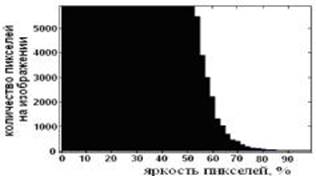
Рис. 4. Гистограмма яркости пикселей изображения для автоматического выбора порога бинаризации
а.
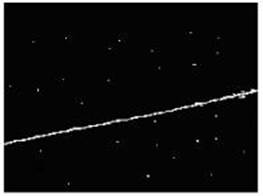
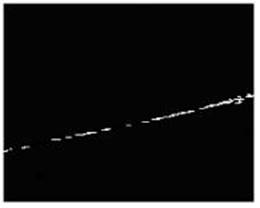
б Рис. 5. Бинаризованное изображение поверхности бобины с автоматическим выборам порога бинаризации: а — порог бинаризации 65мс (автоматический выбор), без фильтра; б — порог бинаризации 40 мс с фильтром 7×7 элементов
Для улучшения качества изображения перед бинаризацией можно использовать шумоподавляющие фильтры [8−10]. Суть их работы заключается в том, что яркость пикселя определяется в зависимости от яркости окружающих его пикселей. Количество окружающих пикселей определяется размером маски, которая представляет собой, как правило, квадратную матрицу. Фильтрация осуществляется перемещением слева направо (или сверху вниз) маски на один пиксель. При каждом положении маски производится перемножение элементов матрицы, содержащей весовые множители на соответствующие значения яркостей точек исходного изображения с последующим суммированием этих произведений.
Полученное значение присваивается пикселю изображения, соответствующего центральному элементу маски. Обычно это значение делится на заранее заданное число — нормирующий множитель. Маска содержит нечетное число строк и столбцов, чтобы центральный элемент определялся однозначно.
Очевидно, что чем больше размер маски, используемой для фильтрации, тем большее время требуется для выполнения этого процесса.
Подготовка изображения к распознаванию включает в себя следующие операции:
- — копирование цветного изображения из буфера видеокамеры в буфер программного приложения (5 мс);
- — получение серого полутонового изображения из цветного (15 мс);
- — получение разностного изображения;
- — фильтрация разностного изображения одним из фильтров (40 мс);
- — построение гистограммы разностного изображения и расчет порога бинаризации (20 мс);
- — бинаризация разностного изображения (10 мс).
Здесь также приведены средние временные затраты при обработке одного кадра изображения для каждой операции.
На рис. 5, б показано изображение с порогом бинаризации 40 мс и сглаживающим фильтром 7×7 элементов. Шумы на изображении практически устранены, однако, несмотря на низкий порог бинаризации, изображение нити получается тонким и разорванным.
Выводы. 1. Сравнение двух последующих кадров при видеосъемке формируемой бобины позволяет выделить изображение наматываемой нити.
2. На основе анализа гистограммы распределения яркостей точек изображения можно построить алгоритм автоматического определения порога бинаризации.
- 1. Палочкин, С. В. Методы и средства контроля основных параметров текстильных паковок [Текст] / С. В. Палочкин, П. Н. Рудовский, М. Н. Нуриев. — Москва, 2006. — 240 с.
- 2. Рудовский, П. Н. Теоретические основы формирования технологической оценки паковок при фрикционном наматывании [Текст]: автореф. дисс. … д-ра техн. наук / П. Н. Рудовский. — Кострома, 1996.
- 3. Нуриев, М. Н. Контроль качество паковок крестовой намотки на основе методов технического зрения [Текст] / М. Н. Нуриев. — Баку: Элм, 2008.
- 4. Rudowskij, P.N. Kontrole des Spulenaufbau bei wilder Wicklung [Text] / P. N. Rudowskij // Melliand Textilberichte. — 1997. — Issue 3. — P. 138−141.
- 5. Нуриев, М. Н. Устройство для комплексного контроля технологических параметров паковок крестовой намотки [Текст] / М. Н. Нуриев, П. Н. Рудовский // ПолезнаяМодель^и — Режим доступа: http://poleznayamodel.ru/ model/7/72 317.html
- 6. Рудовский, П. Н. Получение графической модели паковок крестовой мотки [Текст] / П. Н. Рудовский, М. Н. Нуриев, П. Н. Киселев // Известия вузов. Технология текстильной промышленности. — 2006. — № 3. — С. 124−125.
- 7. Рудовский, П. Н. Разработка комплексного показателя для оценки формы паковок крестовой мотки [Текст] / М. Н. Нуриев, П. Н. Киселев // Известия вузов. Технология текстильной промышленности. — 2006. — № 5. — С. 131−133.
- 8. Волгин, А. Б. Обработка и распознавание цифрового изображения самокрученых нитей с целью определения значения и направления крутки [Текст] / А. Б. Волгин, П. Н. Рудовский // Вестник Костромского государственного технологического университета. — 2012. — № 2 (29). — С. 37−39.
- 9. Денисов, А. Р. Применение методов кластерного анализа для контроля качества паковок крестовой намотки [Текст] / А. Р. Денисов, Л. Ю. Киприна, П. Н. Рудовский // Известия вузов. Технология текстильной промышленности. — 2006. — № 4. — С. 111−113.
- 10. Нуриев, М. Н. Совершенствование алгоритма распознавания паковок крестовой намотки [Текст] / М. Н. Нуриев, П. Н. Рудовский // Известия вузов. Технология текстильной промышленности. — 2008. — № 2. — С. 121−123.
- 11. Рудовский, П. Н. Методика количественной оценки параметров структуры намотки [Текст] / П. Н. Рудовский, Л. Ю. Киприна, М. Н. Нуриев // Вестник Костромского государственного технологического университета. — 2004. — № 11. — С. 27−30.
- 12. Киприна, Л. Ю. Оценка качества структуры текстильных паковок с использованием современных информационных технологий [Текст] / Л. Ю. Киприна, П. Н. Рудовский. — Кострома: Изд-во КГТУ, 2011. — 111 с.
- 13. Нуриев, М. Н. Обнаружение дефектов структуры намотки по изображению поверхности бобины с помощью преобразования Хоха [Текст] / М. Н. Нуриев // Известия Вузов. Технология текстильной промышленности. — 2008. — № 3. — С. 128−131.
- 14. Орлов, А. А. Преобразование Хоха для отрезков [Текст] / А. А. Орлов, О. В. Прохоренко, Е. А. Ивлева // Методы и системы Обработки информации. — М.: Горячая линия-Телеком, 2005. — С. 82−89.
- 15. Орлов, А. А. Методы и алгоритмы обработки и выделения структурных элементов полутоновых изображении на основе преобразования Хоха [Текст]: автореф. дисс. … канд. техн. наук / А. А. Орлов. — С.-Пб.: 2001. — 16 с.
- 16. Грузман, И. С. Цифровая обработка изображении в информационных системах [Текст]: уч. пос. / И. С. Грузман, В. С. Киричук, В. П. Косых, Г. И. Перетягин, А. А. Спектор. — Новосибирск: Изд-во НГТУ, 2000. — 156 с.
- 17. Прэтт, У. Цифровая обработка изображений [Текст] / У. Прэтт. — М.: Мир, 1982. — 460 с.