Другие работы
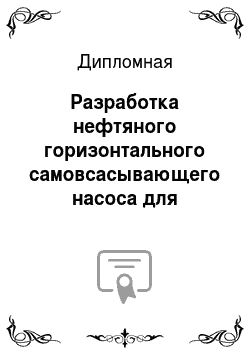
В нефтяной промышленности России широко применяются центробежные насосы различного конструктивного исполнения (горизонтального с горизонтальным расположением ротора и вертикального с вертикальным расположением ротора) для перекачивания разнообразных рабочих сред. технологиях и производственных установках промышленных предприятий предусматривается откачка и перекачка химически активных…
Дипломная 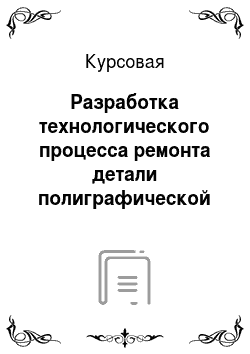
При подробном осмотре (исследовании) изношенных деталей, можно выявить, что износились только отдельные части (поверхности) этих деталей и экономически выгодно бывает не выбрасывать деталь и изготавливать новую, а восстановить изношенные поверхности старой детали. Но это зависит от технических требований к точности размеров и форм, к шероховатости и твердости изнашиваемых деталей, а также…
Курсовая 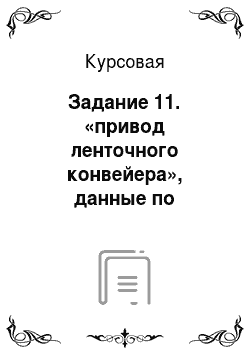
Шпонка под червячным колесом. Параметры соединения: d=60 мм; bxhxl=18×11×63 мм; =7 мм; =269,2* Н*мм. Шпонка на выходном конце вала. Параметры соединения: d=42 мм; bxhxl=12x8x56 мм; =5 мм; =269,2* Н*мм. Шейнблит, А. Е. Курсовое проектирование деталей машин / А. Е. Шейнблит. — М.: Высш. шк.,. Отношение /=2990/2226=1,343>e, поэтому эквивалентную нагрузку определяем с учетом осевой. Осевые…
Курсовая 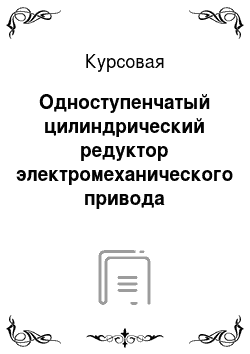
Расчёт расстояния от внутренней стенки корпуса редуктора до осей болтов. Расчёт расстояний от внутренней стенки корпуса редуктора до осей болтов. Расчёт ширины фланцев, соединяющих основание и крышку корпуса редуктора. Где — диаметр наружного кольца подшипника быстроходного вала, 110 мм. Где — диаметр наружного кольца подшипника тихоходного вала, 160 мм. Предварительно выбран шариковый радиальный…
Курсовая 
Помимо использования цепей в приводах, в машиностроении широко применяют цепные устройства, т. е. цепные передачи с рабочими органами (ковшами, скребками) в транспортерах, элеваторах, экскаваторах и других машинах. Цепи производят на специализированных заводах, они стандартизованы (Основные нормативно-технические документы: ГОСТ 13 568−97, 13 568−75, 21 834−87, 191−82, 588−81, 589−85, 5946−79…
Курсовая 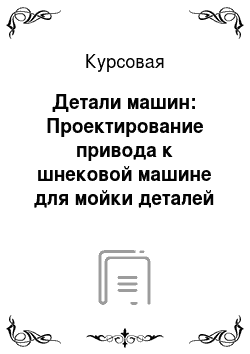
Смазывание зубчатых зацеплений и подшипников применяется в целях защиты от коррозии, снижения коэффициента трения, уменьшения износа, отвода тепла и продуктов износа, от трущихся поверхностей, снижения шума и вибраций. Контроль уровня масла, находящегося в корпусе редуктора, контролируют маслоуказателями. Наибольшее распространение получили жезловые маслоуказатели, так как они удобны для осмотра…
Курсовая 
В обязанность этого лица входит указание водителю погрузчика дороги, подача предупредительных сигналов и обеспечение безопасности при движении погрузчика. При выполнении погрузочно-разгрузочных работ с применением машин непрерывного транспорта (конвейеров, элеваторов и др.). Укладка грузов должна обеспечивать равномерную загрузку рабочего органа и устойчивое положение груза. Подача и снятие груза…
Курсовая 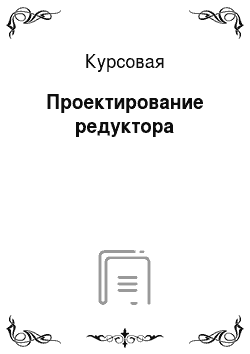
Определяемые параметры Окружная скорость в зацеплении, м/с3,794Расчёт на контактную прочность Коэффициент, учитывающий неравномерность распределения нагрузки по длине контактных линий1,63 Удельная окружная динамическая сила, Н/мм7,97 Коэффициент, учитывающий динамическую нагрузку, возникающую в зацеплении до зоны резонанса1,007 Окружная сила на делительном цилиндре, Н11 040,069 Удельная расчетная…
Курсовая 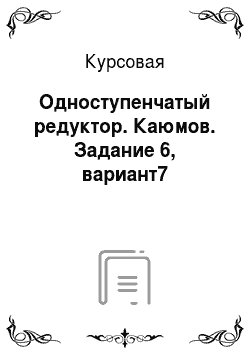
На валы закладывают шпонки и напрессовывают элементы передач редуктора. Маслоудерживающие кольца и подшипники следует насаживать, предварительно нагрев в масле до 80−100 градусов по Цельсию, последовательно с элементами передач. Собранные валы укладывают в основание корпуса редуктора и надевают крышку корпуса, покрывая предварительно поверхности стыка крышки и корпуса спиртовым лаком. Для…
Курсовая 
Значение коэффициента запаса усталостной прочности (=2.5÷4).Коэффициент запаса усталостной прочности: — по нормальным напряжениям:; Значение коэффициента запаса усталостной прочности (=2.5÷4).Коэффициент запаса усталостной прочности: — по нормальным напряжениям:; Коэффициенты асимметрии цикла для углеродистой стали, Коэффициент запаса усталостной прочности: — по нормальным напряжениям:; Значения…
Курсовая 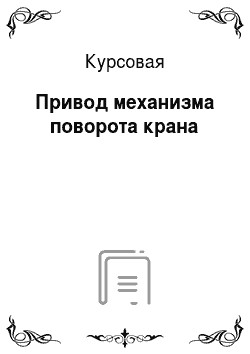
В редукторе смазыванию подлежат зубчатые зацепления и подшипники качения. Т.к. окружная скорость зубчатых колес в обоих зацеплениях превышает 1 м/с для смазывания зубьев применим картерную смазку, при которой зубья колеса второй ступени погружаются в масло и разбрызгивают его, обеспечивая смазывание зубьев всех зубчатых колес. Для предотвращения попадания продуктов износа зубьев вместе с маслом…
Курсовая 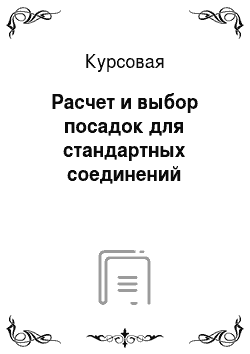
В. И. Анухин «Допуски и посадки». Учебное пособие. 4-е издание — СПб.: Питер, 2007.-207 с. Димов Ю. В. Метрология, стандартизация и сертификация: учебник для вузов. — 2-е изд. — СПб: Питер, 2006. Черменский О. Н., Федотов Н. Н. Подшипники качения. Справочник-каталог. — М.: Машиностроение, 2003. ЕСДП СЭВ в машиностроении и приборостроении. Справочник. В 2 т. — М.: Стандарты, 1989. Методические…
Курсовая 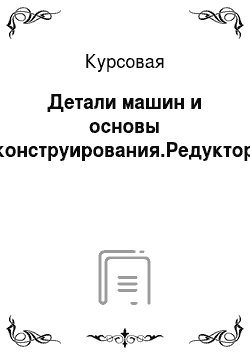
H = 446 МПа; при = 1,2 значение требуемого предела контактной выносливости (535 МПа. Зубья колёс из среднеуглеродистых конструкционных сталей после нормализации или улучшения имеют (H lim = 2 HB + 70. Следовательно, требуемая твёрдость зубьев (233 HB. В данном случае достаточно применить объёмное упрочнение — улучшение. Нормализация не может быть использована, так как не обеспечивает требуемой…
Курсовая 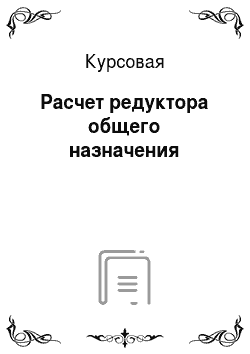
Технологичность конструкции тем выше, чем меньше затраты на её производство. С этой целью в проектируемом редукторе используются литые чугунные корпус и крышки, что допускает их минимальную механическую обработку. В конструкции редуктора используются стандартные посадки, конструктивные элементы, а также стандартные крепёжные детали и уплотнительные устройства. Это повышает его технологичность…
Курсовая 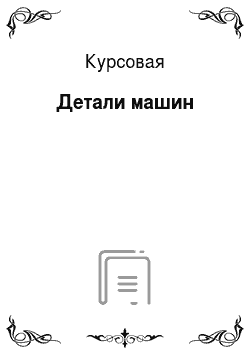
После этого собранные валы устанавливаются в корпус редуктора и заливается масло. Смазка подшипниковых узлов осуществляется с помощью солидола непосредственно заправленного в подшипники. Затем на корпус редуктора устанавливается крышка. Центрирование крышки осуществляется с помощью центрирующих штифтов. Затем крышка привинчивается к корпусу редуктора, стык покрывается герметиком. Следующий этап…
Курсовая