Графит: особенности строения и свойства
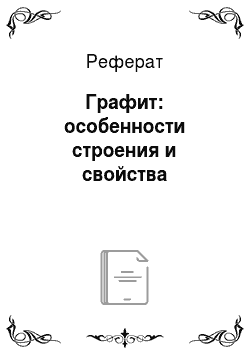
Соединения с галогенами. При контакте графита с газообразным или жидким бромом легко образуется соединение, состав которого можно передать формулой С8Бг. В этом соединении графит выступает в роли донора электронов. Поэтому формула C+8 3Br2 более правильна, так как указывает на то, что в межслоевое пространство включается молекулярный бром с переносом одного электрона примерно на каждые три… Читать ещё >
Графит: особенности строения и свойства (реферат, курсовая, диплом, контрольная)
Глава 1. Графит природный
Низкий коэффициент теплового расширения графита и связанная с этим высокая стойкость к температурным напряжениям является решающим фактором применения его как важного и незаменимого вспомогательного материала в металлообрабатывающей, чугунолитейной и сталелитейной промышленности, т. е. всюду, где рабочие поверхности должны предохраняться от прямого воздействия расплавленного металла. Важным преимуществом при таком использовании является также его несмачиваемость полностью восстановленными металлами и нейтральными шлаками, прочность при высоких температурах. Применение графита при отливе деталей повышает качество отливов, уменьшает количество брака, и предупреждает образование пригара, на удаление которого требуется большие усилия и затраты. Сырые литейные формы и стержни покрываются слоем сухого графитового порошка. Применение для этих целей кристаллического графита марки ГЛ дает весьма ценные результаты. Для сухих форм и стержней в качестве противопригарного материала применяются литейные краски, представляющие собой водные суспензии натурального графита с определенными добавками. Литейные краски, создавая на поверхности формы тонкий защитный слой, препятствуют непосредственному соприкосновению легкоплавких минералов формовочной смеси с расплавленным металлом.
Кристаллический графит применяется для бурения в нефтегазодобывающей отрасли, а также в других областях.
Применяется для изготовления огнеупорных изделий: плавильных тиглей, стаканов, пробок для ковшей, крышек, муфт, форсунок, реторт и т. д.
Использование тигельного графита значительно увеличивает теплопроводность изделий, что способствует повышению их стойкости к повышениям температуры и скорости нагревания. Будучи практически неплавким и химически инертным ко многим материалам, графит сообщает изделиям особенно высокую инертность, значительно улучшает их качество, придает тиглям гладкую поверхность, к которой плохо пристает расплавленный металл.
Главные признаки при определении пригодности графита для тигельного производства — размер кристаллов, количество золы и ее состав.
Применяется в качестве добавки для изготовления активных масс щелочных аккумуляторов и графитированных антифрикционных изделий из цветных металлов, а также для изготовления угольных электродов — для электропечей и электролизеров, в которых выплавляются: специальные стали, магний, алюминий, ферросплавы и другие цветные и черные металлы, с целью уменьшения переходного сопротивления электрическому току.
Применяется при изготовлении графитовых препаратов и паст, используемых в качестве смазок, электропроводящей резины, изделий специального назначения и в порошковой металлургии.
Применяется для изготовления противопригарных покрытий при получении отливок в литейном и металлургическом производстве, резинотехнике, асбестотехнических изделиях, станкостроении, приборостроении и других отраслях промышленности.
Графит незаменим при изготовлении скользящих контактов (электрощёток), где наряду с электрическими и механическими свойствами используются главным образом, его хорошие антифрикционные свойства. Изготовленные из графита щётки имеют высокую механическую прочность, выдерживают большую тепловую и электрическую нагрузку, практически нечувствительны к пробою и обладают очень низким коэффициентом трения.
Применяется при производстве угольных электродов для электропечей и электролизеров, в которых выплавляются специальные стали, магний, алюминий, ферросплавы и другие цветные и чёрные металлы. С целью уменьшения переходного сопротивления электрическому току электроугольный графит в виде паст и порошков используется также для уплотнения контактов в стыковых люфтах.
Карандашный графит — малозольный, мягкий, тонкоизмельченный, без примесей кварца, железа и других жестких примесей. Применяется для изготовления карандашей и для других целей.
Показатели | ГК-1 | ГК-2 | ГК-3 | |
Остаток на сетке № 0063, % не более | 0,5 | 0,5 | 1,0 | |
Зольность, % не более | 1,0 | 3,0 | 5,0 | |
Массовая доля железа, в пересчёте на Fe203, % не более | 1,0 | 1,0 | 2,0 | |
Влажность, % не более | 0,5 | 1,0 | 2,0 | |
Применяется при изготовлении графитовых препаратов и паст, используемых в качестве смазок, электропроводящей резины, изделий специального назначения и в порошковой металлургии.
Показатели | П | |
Зольность, % не более | 7,0 | |
Летучих веществ, % не более | 1,0 | |
Массовая доля влаги, % не более | 1,0 | |
Массовая доля серы, % не более | 0,2 | |
Остаток, % не более на сетке № 016 | 1,5 | |
Данная марка графита нашла применение в металлургии, литье, резинотехнике, станкостроении, приборостроении и других отраслях промышленности.
Кристаллический графит — один из основных материалов применяемых для производства высококачественных гальванических элементов.
Применение элементного графита при изготовлении положительных электродов повышает электропроводность, улучшает контакт между частицами двуокиси марганца, тем самым, повышая потенциал электрода.
Введение
элементного графита в состав шихты для производства шамотных форм увеличивает их стойкость, что приводит к значительному повышению производительности конверторов. Элементный графит соответствует требованиям по предельно допустимому содержанию меди и отсутствию примесей свинца, кобальта, никеля, мышьяка, что позволяет увеличить срок службы элементов.
Представляет собой высокодисперсный порошок природного графита.
Применяются в качестве компонентов для приготовления графитовых смесей и технологических смазок, изготовления химстойких и антикоррозийных покрытий в качестве добавки — ластификатора при таблетировании, как компоненты клея для прорезиненных тканей, для контактов и резисторов в радиотехнике и для других целей. Препараты пожарно-взрывобезопасны, не токсичны.
Глава 2. Графит и его соединения включения
Углерод имеет несколько аллотропных модификаций, из которых наиболее известны графит и алмаз. Можно упомянуть также карбин — линейные полимерные цепочки (=С=С=С=) п или (-С=С-С=) n, фуллерены — сферические и эллипсоидальные молекулы (например, С60 и С70), аморфный углерод (сажу, например). Графит — наиболее стабильная при обычных условиях модификация, имеет ярко выраженное слоистое строение. В слоях атом углерода прочно связан химической связью с тремя другими находящимися на расстоянии 1,42 А, угол С-С-С равен 120°. Таким образом, плоский слой представляет собой как бы паркет из гексагонов, в вершинах которых расположены центры атомов углерода (рис. 1, а, б). Расстояние между слоями значительно больше — 3,35 А, слои связаны друг с другом фактически лишь слабыми ван-дер-ваальсовыми силами. Слои расположены таким образом, что половина атомов одного слоя находится под центрами гексагонов другого, а вторая половина — друг под другом (рис. 1, а, в), то есть в графите два вида кристаллографически разных атомов углерода. В обычном гексагональном графите слои расположены точно один под другим через один (чередование слоев АБАБАБ.). Напомним, что в кристаллохимии есть понятие элементарная ячейка — наименьший объем кристалла с максимальным набором элементов симметрии, повторением которого можно воспроизвести весь кристалл. Обычный графит имеет гексагональную элементарную ячейку с параметрами a = b = 2,464 А, c = 6,701 А, z = 4; ячейка представляет собой призму, в основании которой лежит ромб с острым углом в 60° и длиной ребра 2,464 А, высота призмы 6,701 А, и такая ячейка содержит четыре атома углерода. На рис. 1 элементарная ячейка выделена. Реже встречается ромбоэдрическая модификация, у которой чередование слоев через два — АБВАБВ.
Как видно из расстояний между атомами в слоях и расстояний между слоями, все четыре валентных электрона участвуют в образовании химических связей в слое. Поэтому кратность связи 1,33 (длина одинарной связи в алмазе равна 1,544 А). Однако очень малая часть электронов (примерно 1 на 18 000 атомов) находится в зоне проводимости, формируя металлическую связь между слоями. По этой причине металлическая связь вносит крайне небольшой вклад в энергетику взаимодействия между слоями, которая определяется в основном ван-дер-ваальсовыми силами, но существенным образом определяет свойства графита, такие, как теплопроводность, которая в три раза превышает теплопроводность ртути, электропроводность, которая соизмерима с металлической (0,1 от электропроводности ртути), и характерный металлический блеск графита. Слоистость структуры определяет ярко выраженную анизотропию свойств: электропроводность вдоль направления слоев на два порядка выше, чем перпендикулярно им, и теплопроводность также гораздо (в пять раз) выше в направлении параллельно слоям, коэффициент теплового расширения перпендикулярно слоям примерно в 20 раз больше, чем параллельно им. И это понятно, так как слабая связь между слоями легче расшатывается тепловым движением, чем сильная химическая связь в слоях. Относительно слабая связь между слоями позволяет широко использовать графит в качестве скользящих контактов для электрических машин, делает графит удобным твердым смазочным материалом для нагретых частей установок и двигателей (однако заметим, что при температурах порядка 2500° С и выше графит в значительной мере теряет свои смазочные свойства). С химической точки зрения графит достаточно инертен: заметное окисление на воздухе начинается лишь при температуре выше 500° С и даже при воздействии такого агрессивного реагента, как фтор, при комнатной температуре и давлении 5 кбар в течение 19 дней не наблюдалось никаких изменений.
Указанные физические свойства вместе с химической стойкостью графита позволяют использовать его в широчайшем диапазоне человеческой деятельности — от приготовления красок и грифелей для карандашей (название «графит» произошло от греч. урафсо — писать) до сопел ракетных двигателей и замедлителей нейтронов в атомных реакторах. Графит широко используют в химической промышленности для изготовления теплообменников, трубопроводов для агрессивных сред, как наполнитель пластмасс, материал для электродов разного назначения и многое, многое другое. Он является неоценимым материалом в металлургии для изготовления плавильных тиглей, труб, кристаллизаторов, чехлов для термопар и т. д. Однако, несмотря на свою достаточно высокую химическую инертность, графит довольно легко дает так называемые интеркала-ты (слоистые соединения включения [2]) и с гораздо менее химически активными реагентами.
Наиболее легко образуются соединения с тяжелыми щелочными металлами (начиная с калия). Для этого достаточно контакта графита с избытком жидкого или парообразного металла при температурах порядка.
графит строение свойство фланцевый
300−500° С. Открыты они были Фреденхагеном в 1926 году. Соединение калия с графитом КС8 имеет вид желтой бронзы и обладает гораздо более высокой электропроводностью, чем сам графит. Реакции внедрения металла в межслоевое пространство графита экзотермична, и выделение тепла возрастает в ряду К (360) — > - *Rb (486) — «- Cs (666 Дж/г графита). Из рис. 2 видно, что при плавном изменении условий синтеза (изменение температуры образца при постоянном давлении паров калия) на кривой состава соединения калия с графитом (аналогично с Rb и Cs) наблюдаются четкие площадки, говорящие об образовании нескольких соединений практически определенного состава, а не о твердых растворах (с заметной областью гомогенности) за счет постепенного заполнения межслоевого пространства щелочным металлом. Структурные исследования показали, что при внедрении атомов металла (М) слои графита раздвигаются (от l = 3,35 А в графите до l = 5,40 (К), 5,65 (Rb) и 5,95 А (Cs)) и смещаются таким образом, что становятся точно друг под другом (чередование АМАМА.). Такое смещение требует всего около 8 кДж/г атом и окупается благоприятной геометрией. Гостевые атомы располагаются не беспорядочно, а как показано на рис. 1, в на расстоянии 4,91 А друг от друга. Стехиометрия при таком расположении атомов (см. выделенную элементарную ячейку) составляет МС8. Как видно из рис. 2, а также из данных по межслоевым расстояниям, металл внедряется в виде иона, отдавая свой электрон в графитовый слой. Графит, таким образом, является макроанионом.
При понижении концентрации металла (давления паров) в исходной реакционной смеси снижается и его содержание в соединении за счет как понижения концентрации в слое (убирается каждый третий атом металла, сетка расположения ионов из треугольной становится гексагональной и стехиометрия в слое становится МС12), так и за счет появления незаполненных слоев. Если слои металла отделены друг от друга двумя (тремя, четырьмя и т. д.) слоями графита, то соединение называется соединением второй (n = 2) (третьей, n = 3, четвертой, n = 4 и т. д.) ступени. Стехиометрия для соединения II ступени — МС24, для III ступени — МС36, для IV ступени — МС48 и т. д. Чередование слоев графита для соединения II ступени таково: АМАВМВАМА, то есть через слой металла слои графита расположены одинаково, а граничащие друг с другом смещены как в чистом графите. Нетрудно видеть, что период идентичности в, А вдоль оси с = (n — 1) 3,35. Встречаются соединения и дробных ступеней, например соединение степени 3/2, в котором чередование слоев таково: АМАВМВМВМВА., то есть как бы сочетаются в соотношении 1: 1 соединения первой и второй ступеней.
Соединения с литием и натрием. Расположение ионов лития в межслоевом пространстве графита отличается от описанного выше для тяжелых щелочных металлов (см. рис. 1, д, е): они расположены ближе друг к другу — а = 4,29 А и стехиометрия для соединений первой ступени LiC6. Поскольку ион лития маленький (r = = 0,68 А), графитовые слои раздвигаются незначительно (/ = 3,73 А) и расположение их друг относительно друга такое же, как в графите, то есть параметр с = 2/. Известны соединения от LiC6 до LiC72 (XII ступень). Но непосредственно с графитом при обычных условиях литий не взаимодействует. Для этого нужны высокие температуры (Т > 400° С) и давления (Р > 10 кбар). Обычно соединения лития получают обработкой графита раствором лития в аммиаке или метиламине.
С натрием графит взаимодействует хуже всего. Известны только соединения высоких ступеней (NaQ8 — №С64). Нужно, однако, заметить, что при очень больших давлениях и температурах были получены фазы с гораздо более высоким содержанием металла в графите (вплоть до LiC2, NaC2, MC4-6, где М = K, Rb, Cs). При этом наблюдается явление «гнездования» гостевых ионов с некоторым перекрыванием их сфер, очерченных ионными радиусами.
Соединения с другими металлами. Непосредственно щелочноземельные металлы (Ca, Sr, Ba) и лантаниды (Sm, Eu, Yb) образуют соединения МС8 в условиях, близких к таковым для лития. Нагревание должно быть осторожным, так как перегрев ведет к образованию карбидов. В этих случаях металл внедряется в виде иона. Прямым синтезом с переходными металлами (Mn, Fe, Co, Ni, Cu, Mo) по понятным причинам не удавалось получить подобные соединения. Красивый обходной маневр предложили Ю. Н. Новиков и М.Е. Воль-пин. Они осторожно восстанавливали (водородом или лучше анион-радикалом, например натрий-нафталином) слоистые соединения хлоридов соответствующих металлов. Интересно, что, zumFe° было получено соединение первой ступени с межслоевым расстоянием 5,8 А и это соответствует внедрению скорее свободного атома железа с его ван-дер-ваальсовыми размерами. В некоторых случаях, однако, со временем межслоевое пространство уменьшалось до 4,66 А, и это авторы объясняют взаимодействием гость-хозяин по типу образования л-комплексов.
Тройные соединения. Соединение КС8, имеющее цвет желтой бронзы, уже при обычных условиях в атмосфере водорода медленно его адсорбирует и превращается в соединение второй ступени КС8Н2/3, окрашенное в голубой цвет. В этом соединении между двумя слоями графита, расположенными на расстоянии 8,53 А, помещается тройной гостевой слой — калий-водород — калий. Реакцией гидрида калия с кристаллическим графитом удалось получить не только это соединение, но и фиолетовое соединение первой ступени КС8Н4. Интересно, что давление десорбции подобных дейтеридов в шесть раз выше, чем у гидридов, и в этом отношении интеркалаты графита имеют преимущества перед гидридами металлов при разделении изотопов. Имеется также сообщение о том, что при низких температурах (ниже — 180° С) довольно быстро сорбируются и водород и дейтерий, но при этом не наблюдается обменной реакции H2 + D2 — «- 2HD, и теплота сорбции составляет всего — 9 и — 11 кДж/моль соответственно. И то и другое свидетельствует о том, что в данном случае наблюдается обычная физическая сорбция в отличие от описанной выше хемосорбции. Сорбционная способность КС24 для Н2 составляет 144 см3 г» 1, что позволяет ему конкурировать с такими сорбентами, как активированный уголь или цеолиты. При этом изотопный эффект в некоторых случаях значительно выше, чем для синтетических цеолитов, использующихся для разделения изотопов водорода в газовой хроматографии.
Аммиак и амины образуют синие соединения состава С12М (№Н3) 2, в которых толщина межслоевого пространства / = 6,6 А не зависит от природы металла, но зависит от природы амина (6,9 А для метиламина и 8,5 А для этилендиамина). Это и понятно, поскольку размер молекул аминов больше размера катиона любого из рассматриваемых металлов.
До середины 90-х годов не были известны соединения включения графита с органическими молекулами в отличие от некоторых глин — слоистых силикатов (например, монтморилонит) и слоистых дисульфидов (например, MoS2). И связано это, скорее всего, с тем, что только ван-дер-ваальсового взаимодействия недостаточно для раздвижения слоев и образования соединений. Интеркалаты графита в значительной мере образуются за счет переноса заряда от гостевой подсистемы к хозяйской или наоборот. Однако соединения графита с щелочными металлами могут включать многие органические молекулы, образуя тройные соединения. При этом взаимодействие между металлом и органической молекулой играет важную роль. ТГФ и бензол легко взаимодействуют с соединениями второй ступени МС24 (M = K, Rb, Cs) и LiC12, образуя соединения первой ступени. Бензол не взаимодействует с КС8, но включается в него вместе с ТГФ, образуя уже четверное соединение К (ТГФ) 0,4 (С6Н6) 0,4С8. А вот удалить бензол из этого соединения в отличие от ТГФ практически невозможно, и связано это с тем, что бензол олигомеризуется в межслоевом пространстве с образованием не только бифенила, но даже трии тетрафенила. Аналогично при — 80° С этилен обратимо внедряется в CsC24, однако уже при 0 °C реакция становится необратимой благодаря полимеризации.
Соединения с галогенами. При контакте графита с газообразным или жидким бромом легко образуется соединение, состав которого можно передать формулой С8Бг. В этом соединении графит выступает в роли донора электронов. Поэтому формула C+8 3Br2 более правильна, так как указывает на то, что в межслоевое пространство включается молекулярный бром с переносом одного электрона примерно на каждые три молекулы брома. Казалось бы, хлор как более электроотрицательный элемент должен образовывать еще более прочное соединение. Но аналогичное соединение с хлором крайне неустойчиво и существует при очень низких температурах (- 78° С). Иод вообще не образует соединений с графитом, фтор хотя и взаимодействует с графитом, но внедряется не молекула, тогда как молекулы ICl и IBr внедряются в межслоевое пространство графита даже лучше, чем бром. В чем же дело? Очевидно, что не химическая природа галогена определяет его реакционную способность в данном случае. Картина проясняется, если мы вспомним, что расстояния между впадинами в центре гексагонов графитового слоя (см. рис. 1 и 3) равно 2,46 А, расстояния между атомами в Br2, ICl и IBr равны 2,27; 2,40 и 2,49 А, тогда как в молекулах F2, Cl2 и I2 межатомные расстояния 1,42; 1,99 и 2,67 А соответственно, то есть либо слишком малы, либо слишком велики для удобного расположения молекулы гостя между слоями графита. Более того, молекула брома даже несколько растягивается при интеркаляции (расстояние между атомами в молекуле брома увеличивается на 0,04 А), приспосабливаясь таким образом к геометрии межслоевого пространства.
Как мы уже отмечали, непосредственно фтор не взаимодействует с графитом при обычных условиях. Но при повышенных температурах (350−630°С) образуются нестехиометрические соединения валового состава C%F (0,8 < x <2). Цвет изменяется от черного через разные тона коричневого и желтого к белому по мере увеличения содержания фтора в соединении. Эти так называемые высокотемпературные фториды графита разделяют на два типа нестехиометрических соединений: полифториддиуглерод, у которого состав близок к C2F, и полифторидмоноуглерод — CF. Первый получается в интервале температур 350−400°С, второй — 400−600°С. Интересно, что если уж получен полифториддиуглерод, то он не переходит в полифторидмоноуглерод даже за 120 ч при температуре 600 °C. В этих соединениях между углеродом и фтором образуются связи в значительной степени ковалентные. В результате этого графитовый слой теряет свою индивидуальность, угол С-С-С в соединении становится меньше 120°, а углеродный слой — не плоским, а складчатым, длина связи С-С увеличивается, существенно уменьшается электропроводность и CF является изолятором. Строение рассмотренных соединений, по данным их первооткрывателя японского исследователя Н. Ватанабэ, представлено на рис. 3, из которого видно, что каждый атом углерода имеет четыре ковалентные связи. В случае CF к каждому атому углерода поочередно с одной и другой стороны слоя присоединяется по атому фтора, а в случае C2F атомы углерода поочередно связаны с атомами фтора с одной, а с атомами углерода соседнего слоя с другой стороны. Для этих соединений не характерно образование интеркалатов. Другое дело — фториды графита, получаемые при низких температурах (15 — 100° С) с помощью катализаторов (HF, AgF и т. д.). При таком осторожном фторировании дело не доходит до образования ковалентных связей C-F, и так называемые низкотемпературные фториды графита — неплохие проводники электрического тока и весьма склонны к образованию соединений включения. Их состав CxF, где 2 < х < 24. Здесь, как и в рассмотренном выше случае, выделяются несколько доминирующих составов с х = 2, 4 и 6.
Соединение C6F является соединением включения ионов фтора в графит, матрица которого выполняет роль макрокатиона (рис. 3, в). В соединениях C4F и CF1 графитовый слой остается плоским, связь в значительной мере сохраняет ионный характер, они достаточно хорошо проводят электрический ток и легко образуют соединения включения с неорганическими (например, ClF3, N2O4) и органическими (ацетон, бензол, толуол) молекулами. Синтезированное при низких температурах соединение C2F имеет приблизительно тот же интервал составов, что и высокотемпературная модификация C2F, о которой речь шла выше, но существенно отличается, как показали новосибирские исследователи А. С. Назаров, В. Г. Макотченко и другие, строением и свойствами. В отличие от высокотемпературной модификации в низкотемпературной C2F (как и в C4F) графитовый слой одинарный с расположением фтора по обе стороны. Фтор достаточно прочно удерживается в отличие от упомянутых только что гостевых органических и неорганических молекул, которые относительно легко могут быть удалены при нагревании или замещены другими гостевыми молекулами обменными реакциями, что позволяет говорить о фторграфитовой матрице и фтор, расположенный в межслоевом пространстве, относить к хозяину, а не к гостю. Подобные фторграфитовые матрицы кроме прямого фторирования графита могут быть получены из слоистых соединений.
Соединения с галогенидами металлов. Гексафториды некоторых переходных элементов, обладающие высоким сродством к электрону (PtF6, IrF6, OsF6), образуют с графитом соединения включения I ступени. С AsF5 образуется аналогичное соединение по реакции.
3ASF5 + 32C^m = 2C16AsF6 + ASF3
Нужно заметить, что соединения включения графита с дефицитом электронов в графитовом слое (так же как и с их избытком) с одним и тем же гостем в зависимости от условий равновесия могут образовывать соединения разных ступеней. Причем при монотонном изменении условий равновесия состав интеркалата меняется скачкообразно, с четко выраженными остановками на изобаре, говорящими об образовании фактически соединений определенного состава (см. рис. 2, б).
Хлориды железа (II) и (III), никеля, кобальта, марганца, меди, алюминия, галлия, редкоземельных элементов в присутствии окислителя (обычно Cl2) достаточно легко образуют интеркалаты разных ступеней в зависимости от условий синтеза. Некоторые из них, как соединения с хлоридом алюминия, легко разлагаются водой, другие, как соединения с хлоридом железа, довольно устойчивы к ней.
Соединения с кислотами. В присутствии сильных окислителей графит взаимодействует со многими кислотами: азотной, фтористоводородной, фосфорной, трифторуксусной и хлорной. Вообще первым обнаруженным соединением включения графита был его бисульфат C+4 HSO4 2H2SO4, открытый П. Шауфхейтлем в 1841 году. Возможны реакции обмена кислотами, например
C+4 HSO4 2H2SO4 + 3H3PO4 — > - > C+4 H2PO4 2H3PO4 + 3H2SO4
Оксиды и фтороксиды графита в какой-то мере аналогичны высокотемпературным фторографитам: в них также связь углерод-кислород (фтор) в значительная степени ковалентная и графитовые слои теряют свою планарность. Окись графита может быть получена окислением графита сильными окислителями (KClO3, KMnO4) в крепких растворах серной кислоты. Здесь реакция идет в две стадии: сначала (в считанные минуты) образуется бисульфат графита с включенными окислителями, а затем уже идет (в течение нескольких часов) реакция окисления графита. Оксифториды получают фторированием окиси графита, изучены они мало.
Окись графита. Окись графита — широко употребляемый термин для продуктов окисления графита, далеко не полностью соответствует этому. Любая окись графита, даже высушенная над Р2О5, содержит водород, и состав ее переменный (С7О4Н2-С8О4Н3). В высушенной над Р2О5 окиси графита межплоскостные расстояния порядка 6 А, и это расстояние практически не меняется при поглощении до 4,5% воды, тогда как в дальнейшем межслоевое расстояние увеличивается пропорционально содержанию воды и может достигать 12 А. Кроме воды окись графита способна сорбировать другие полярные жидкости. На этом основано приготовление мембран, проницаемых для воды и непроницаемых для неполярных веществ (например, благородных газов, азота). При внедрении в окись графита н-спиртов и н-аминов слои могут раздвигаться до 40 А и более, и в этом окись графита очень похожа на слоистые алюмосиликаты (глины, натриевый монтмориллонит, например).
Сам графит обладает исключительно большим набором полезных физико-химических свойств, которые позволяют широко использовать его в различных областях человеческой деятельности. Способность графита включать ионы (атомы, молекулы) разнообразных веществ позволяет в некоторых случаях существенно усилить его полезные свойства. Интеркаляция, как правило, приводит к существенному увеличению электропроводности. Так, проводимость C24ICl превышает проводимость золота при одинаковых условиях. Это обусловлено ростом концентрации носителей тока по сравнению с графитом при сохранении их высокой подвижности, связанной с двухмерным характером явления переноса. На рис. 5 показана электропроводность некоторых соединений включения графита наряду с электропроводностью металлов. Это сравнение показывает перспективность использования интеркалатов графита в качестве электропроводников, особенно если учесть, что сейчас хорошо развито изготовление углеродных волокон и ведутся работы по получению волоконных интеркалатов. Основной недостаток этих материалов — неустойчивость их работы во времени.
Глава 3. Герметизация фланцевых соединений с использованием ленточных уплотнителей на основе терморасширенного графита
Снижение затрат на эксплуатацию и обслуживание технологического оборудования — один из наиболее значимых вопросов, стоящих перед руководителями промышленных предприятий. Учитывая, что в России основные производственные фонды большинства отраслей промышленности сейчас изношены, сокращение издержек становится все более актуальным. Решить эту проблему помогут уплотнители для разъемных соединений. Они обеспечивают безаварийную работу оборудования, а использование современных материалов и внедрение новых энергои ресурсосберегающих технологий герметизации позволяет сократить издержки на обслуживание и ремонт.
Одним из важнейших факторов, мешающих развитию отечественной промышленности, является высокая энергои ресурсоемкость материального производства и низкий технический уровень оборудования. Поэтому практически для всех промышленных отраслей, будь то энергетика, нефтехимия или машиностроение, актуальной является сейчас проблема обеспечения надежной герметизации разъемных соединений. Решение ее позволит избежать ненужных затрат временных, человеческих и материальных ресурсов.
Любой контактный уплотнитель работает по следующей схеме: его с большим усилием сжимают в разъемном соединении, создавая запас потенциальной энергии упругости. При этом материал уплотнителя перекрывает собой микроканалы на уплотняемой поверхности фланцев и тем самым предотвращает утечку рабочей среды.
До недавнего времени для фланцевых соединений использовались уплотнительные материалы, изготовленные на основе асбеста. В ряде случаев, особенно при герметизации сред с высоким рабочим давлением и температурой, применялись металлические (как правило, стальные) плоские, трубчатые или спирально навитые прокладки. Многолетний опыт эксплуатации этих уплотнений показал, что они имеют ряд существенных недостатков и не могут обеспечить надежную герметизацию в условиях циклических тепловых и динамических нагрузок.
В частности, содержащий асбест паронит не обеспечивает необходимого запаса энергии упругости и подвержен релаксации — особенно в условиях циклических нагрузок. Это, в свою очередь, вызывает ослабление затяжки уплотнения и как следствие — потерю герметичности. Таким образом, сокращаются межремонтные сроки эксплуатации оборудования, и требуются дополнительные затраты на устранение аварийных ситуаций при разгерметизации.
Уплотнительные изделия нового поколения.
В настоящее время широко известны опасные последствия, вызванные применением асбеста. Особую опасность представляет асбестовая пыль. В развитых странах жесткие требования экологической безопасности, высокая конкуренция и возрастающие требования современной промышленности обусловили интенсивное развитие уплотнительной техники, внедрение новых материалов и передовых технологий. С конца 70-х годов ведущие западные компании, специализирующиеся в области уплотнений, вынуждены были затратить огромные усилия и средства на разработку новых безасбестовых материалов для применения их в качестве уплотнений во фланцевых соединениях и набивках сальников арматуры и насосов.
В результате были получены и апробированы альтернативные уплотнительные материалы, среди которых доминирует терморасширенный графит (ТРГ), или пенографит, нашедший наиболее широкое применение. Этот материал создан в результате научных и технологических разработок на основе природного графита путем термической обработки гидролизованных интеркалированных соединений графита (ИСГ). Совокупностью физико-химических свойств материалов на основе графита обусловлено их эффективное применение в качестве уплотнительных.
В 1990 году группа ученых МГУ им. Ломоносова во главе с д. т. н.В. В. Авдеевым занялась освоением промышленного производства отечественного уплотнительного материала на основе ТРГ. В целях разработки и внедрения высоких технологий химической и термической обработки природного графита было создано научно-производственное предприятие, на базе которого отечественными специалистами был получен и апробирован уникальный материал — гибкая графитовая фольга. Продукт не уступал по качеству западным аналогам — в частности, по содержанию чистого углерода (99,5%). В последующие годы чистота графита была доведена до уровня 99,9%.
Уплотнения на основе графитовой фольги оказались не только экологически чисты, но и устойчивы к воздействию органических и минеральных кислот (за исключением серной кислоты при концентрации выше 60% и азотной кислоты при концентрации выше 10%, царской водки, хромовой кислоты), спиртов, альдегидов, эфиров, хлорорганических и хлорнеорганических сред.
Энергетика — одна из первых отраслей российской промышленности, на предприятиях которой были опробованы разработки ученых МГУ. Результаты оказались убедительными: межремонтный период оборудования, в котором применялись графитовые уплотнители, увеличился примерно в 3 раза. Снижение затрат на обслуживание оказалось довольно значительным, и в 2001 году глава РАО «ЕЭС России» А. Б. Чубайс распорядился более широко применять этот материал на всех электростанциях энергосистемы.
Ленточные уплотнители — новые возможности для российских предприятий В России с началом внедрения уплотнений на основе пенографита проблема надежной герметизации была отчасти решена, но лишь для разъемов небольших габаритов. Отечественные производители не выпускали листовые уплотнения шириной более 1000 мм. Поэтому потребители по-прежнему использовали старые материалы, так как покупать чрезвычайно дорогие уплотнители импортного производства (которые тоже ограничены размером в 1500 мм) российские предприятия зачастую просто не имели возможности.
Отечественными специалистами был предложен новый подход к решению проблемы. Он заключался в использовании так называемых ленточных уплотнений. Было предложено вырезать графитовую ленту из рулона фольги, подвергать специальной деформационной обработке (гофрированию), а затем укладывать непосредственно на разъем по спирали, формируя многослойную прокладку.
Самая сложная задача, которую специалистам предстояло решить, — это найти правильный способ гофрирования фольги, ведь она неэластична и не обладает достаточной гибкостью. В результате многочисленных экспериментов решение было найдено. Новый способ гофрирования получил название «непрерывная деформация в упругой оболочке». Суть изобретения в следующем: графитовая лента пропускается через пару зубчатых колес, вершины зубьев которых покрыты пленкой из упруго-эластичного полимерного материала. В результате при вращении зубчатых колес графитовая лента деформируется в условиях всестороннего сжатия, что исключает ее повреждение с появлением трещин и разрывов.
Таким образом была решена задача по отработке технологии получения фланцевых ленточных уплотнений. Новый метод герметизации имеет ряд существенных преимуществ по сравнению с традиционными способами:
1. Появилась возможность формировать прокладку любого радиуса и любой формы.
2. Ленточная технология уплотнения безотходна, в то время как при вырубке уплотнений из листов часть материала просто выбрасывается.
3. Монтаж ленточного уплотнения очень удобен. Ленты можно устанавливать непосредственно на уплотняемой поверхности фланца ручным методом.
Однако, наряду с очевидными преимуществами, новый метод герметизации имел и ряд недостатков. Во-первых, при укладке уплотнителя не был исключен обрыв ленты. Во-вторых, качество и точность укладки не были достаточными — при ручном методе имело место небольшое смещение слоев ленты в радиальном направлении. В-третьих, негативным фактором с точки зрения охраны труда являлось применение аэрозольного клея. И, наконец, очень сложно было осуществлять укладку ленты в труднодоступных местах и в стесненных условиях — например, когда фланцевое соединение располагалось ниже уровня перекрытия.
В результате дальнейшей работы по усовершенствованию продукта и технологии в целом была получена лента с клеевым слоем и лента с заданным радиусом кривизны. Для этого разработали и апробировали установки для нанесения клея на ленту и для ее закругления. Закругленную ленту гораздо легче укладывать в труднодоступных местах, а наличие липкого слоя позволяет зафиксировать слои, исключая их смещение. Особенно ценным новшеством стали ленточные уплотнители, армированные стальной нержавеющей лентой. По основным физико-механическим свойствам (прочность на сжатие, циклическая стойкость к релаксации, упругость, прочность на разрыв и т. п.) такие уплотнители существенно превосходят уплотнители без армирования. Теперь их невозможно повредить при укладке и эксплуатации.
В настоящее время ленточные уплотнения на основе графита опробованы и успешно применяются во многих отраслях промышленности: нефтяной, целлюлозно-бумажной, химической, металлургической, деревообрабатывающей и др. Опыт показывает, что применение новейших технологий позволяет значительно повысить технический уровень оборудования и тем самым снизить производственные издержки.
Однако немаловажным является и вопрос доступности продукта для потребителя. Поэтому следует отметить, что производство ленточных графитовых уплотнений — одна из немногих сфер российской промышленности, где удалось применить отечественные наработки и создать продукт мирового качества, оставив его при этом доступным по цене для российских предприятий.
1. Сережкин В.Н., Блатов В.А. Координационные числа атомов и структура металлов // Соросовский Образовательный Журнал. 1999. № 8. С.35−39.
2. Дядин Ю.А. Супрамолекулярная химия: Клатратные соединения // Там же. 1998. № 2. С.79−88.
3. Okino F., Touhara H. Graphite and Fullerene Intercalation Compounds // Comprehensive Supramolecular Chemistry / Ed. by J. L. Atwood et al. Oxford: Pergamon Press, 1996. Vol.7. P.25−76.