Инструменты Лин
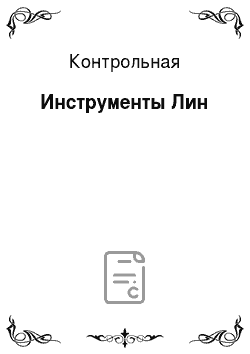
Конечно, только за счет лидерских качеств невозможно провести коренные изменения в характере и мировоззрении персонала компании. Довольно часто приходится применять административно-организационные меры, без которых не обходятся ни в Европе, ни в Японии. Планирование и постоянная работа по вовлечению персонала позволили нам получить хорошие результаты, подчеркивает Владимир Арженцов. Количество… Читать ещё >
Инструменты Лин (реферат, курсовая, диплом, контрольная)
Бережливое производство (англ. Lean production/Lean manufacturing) — логистическая концепция менеджмента, сфокусированная на разумном сокращении размеров заказа на выпуск продукции, удовлетворяющей спрос при повышении ее качества; снижении уровня запасов используемых ресурсов; постоянном повышении квалификации производственного персонала, охватывающим весь контингент; внедрение гибких производственных технологий и интегрирование их в единые цепи с взаимодействующими технологиями партнеров.
Цели бережливого производства:
— сокращение затрат, в том числе трудовых;
— сокращение сроков разработки новой продукции;
— сокращение сроков создания продукции;
— сокращение производственных и складских площадей;
— гарантия поставки продукции заказчику.
— максимальное качество при определённой стоимости либо минимальная стоимость при определённом качестве.
1. Характеристики инструментов Лин
1.1 Метод Кайдзен
Система Кайдзен основана на научном подходе: снача лапроизводится анализ отдельных элементов процесса, а за-тем предлагаются пути их улучшения. Бережливое производство пронизано идеей Кайдзен или непрерывного улучшения — небольших, постепенных и последовательных изменений, предпринимаемых постоянно и оказывающих положительное воздействие на общее состояние производства.
Кайдзен предусматривает осмысленное отношение к выполнению операций и требует определённого времени для того, чтобы научиться осознанно выбирать лучшие методы работы. Для анализа идей по улучшению производства не обходимо использовать новые инструменты.
Следовательно, хотя инновации могут коренным образом изменить стандарт достижимых показателей, их уровень будет снижаться, если не заниматься постоянным пересмотром и совершенствованием нового стандарта.
Поэтому любая инновация должна подкрепляться Кайдзен, чтобы поддерживать достигнутый уровень и продолжать совершенствование, как это наглядно демонстрирует рисунок 1.1 применительно к системе улучшений бизнес-процессов на различных уровнях: мега-, макро-, и микропроцессы управления в организации.
Рисунок 1.1 Ключевая роль микропроцессов в успехе всех процессов Следует особенно отметить психологические аспекты системы Кайдзен. При реализации стратегии кайдзен задействовано по принципу Парето — Джурана 80−95% персонала, при инновационном подходе — 20−5%.
Важная особенность кайдзен — это требование от всех и каждого личных усилий. Менеджменту приходится прилаать сознательные и постоянные усилия для поддержания духа совершенствования (рисунок 1.2).
Рисунок 1.2 Инструменты бережливого производства В центре внимания кайдзен находится скорее процесс, чем результат. Сильная сторона японского менеджмента — успешная разработка и применение системы, которая признает цели, делая акцент на средства Кайдзен требует от руководства значительных затрат времени и сил, которые нельзя заменить вливаниями капитала. Вкладывать в кайдзен — значить вкладывать в людей. Таким образом, Кайдзен ориентирован на человека, а инновации — на технологию и деньги.
1.2 Система 5S
Система 5S — это пять простых принципов рациональной организации рабочего пространства, соблюдая которые, можно извлечь максимальную выгоду от имеющихся ресурсов. Систему 5 S успешно применяют не только на производственных предприятиях, но и в офисах, в том числе в организациях, предоставляющих различные виды услуг.
Система 5S — это устранение потерь за счет активного вовлечения работающих в процесс непрерывного совершенствования. Значение системы 5S имеет философский характер, поскольку 5S направлено не только на устранение напрасных действий (прямой эффект): напрасные движения в поисках предметов, напрасная повторная подготовка из-за ненайденных предметов, напрасная трата времени на извлечение необходимых предметов, напрасное использование пространства для хранения ненужных предметов, напрасные движения для устранения ненужных предметов.
Система 5S через повышение способности к самосовершенствованию приводит к осознанию путей улучшения (косвенный эффект): массовое усвоение основ «5S» в рамках всеобщего движения за осуществление указанного принципа — радикальное средство для снижения затрат. В ходе реализации принципа пяти «S» воспитывается тщательное отношение к «предметам», что является основой мировоззрения для осуществления деятельности по снижению себестоимости.
Основные моменты деятельности по внедрению системы 5S:
— создание комитета (совета) 5S и выборы лидеров на каждом рабочем месте;
— осознание начала выполнения принципов 5S;
— контроль выполнения 5S с использованием списка объектов проверки;
— поддержание порядка, чистоты и уборки;
— фиксация непрерывных улучшений с использованием, например, принципа фотосъемки контрольных точек.
Метод съемки контрольных точек заключается в использовании сводной таблицы, вывешенной на стенде для объявлений, на которую наклеиваются в хронологическом порядке фотографии, наглядно демонстрирующие, какие недостатки имеются в настоящее время, и каким образом изменяется положение на объекте. Порядок осуществления метода съёмки контрольных точек приведен на рисунке 1.3
Рисунок 1.3 Порядок осуществления метода съемки контрольных точек
1.3 Система общего производительного обслуживания оборудования
Система общего производительного обслуживания оборудования (ТРМ) — обслуживание оборудования, позволяющее обеспечить его наивысшую эффективность на протяжении всего жизненного цикла с участием всего персонала. Целью ТРМ является создание предприятия, которое постоянно стремится к предельному и комплексному повышению эффективности производственной системы. Средством достижения цели служит создание механизма, который, охватывая непосредственно рабочие места, ориентирован на предотвращение всех видов потерь.
Самой главной отличительной особенностью ТРМ является самостоятельное техническое обслуживание оборудования операторами, без чего невозможно реализовать принцип «О своем оборудовании забочусь сам». Кроме того, как видно из определения ТРМ, одна из основ этой системы — стремление свести различные потери из-за простоев оборудования к нулю, так называемое, «стремление к нулю».
Как говорят классики менеджмента — если не можешь измерить параметры процесса, очень сложно управлять этим процессом. Поэтому при внедрении ТРМ очень важно начинать с количественного измерения потерь, которые интегрально характеризует коэффициент общей эффективности оборудования (ОЕЕ). ОЕЕ — это показатель системы всеобщего ухода за оборудованием, отражающий степень эффективности его использования. ОЕЕ равен произведению трех составляющих:
— производительность — количество изделий, которое может быть произведено рабочим или единицей оборудования за определенный промежуток времени;
— готовность оборудования — сравнение времени, в течение которого изготавливается продукт и номинального времени выпуска изделия;
— качество — сравнение общего количества изделий, изготовленных за период времени и количества изделий, отвечающих требованиям потребителей.
Измерение ОЕЕ позволяет узнать, какие именно потери снижают эффективность использования станков. Регулярно отслеживая ОЕЕ, можно выявить закономерности и тенденции, вызывающие проблемы в функционировании оборудования. Кроме того, измерение этого показателя дает возможность увидеть результаты действий по улучшению использования оборудования. Измерением и улучшением ОЕЕ должны заниматься рабочие. Операторы хорошо знают особенности функционирования оборудования, поэтому они лучше всего понимают, каким образом следует совершенствовать работы станков. Сбор данных для расчета показателей ОЕЕ должен проводить рабочий персонал, эксплуатирующий данное оборудование. В качестве примера в таблице 3 приведены значения ОЕЕ и его составляющих для изготовления изделия на термопластавтомате.
1.4 Система Канбан
Цель системы Канбан — производить только необходимую продукцию в требуемом количестве и в нужное время. Главное преимущество системы Канбан состоит в предотвращении перепроизводства. Итак, система Канбан позволяет:
— устранить перепроизводство — главную причину потерь;
— увеличить маневренность производства, с тем, чтобы лучше реагировать на изменения потребительского спроса;
— координировать выпуск продукции малыми партиями и разнообразить ассортимент выпускаемой продукции;
— упростить процесс снабжения;
— интегрировать все производственные процессы, привязав их к потребностям потребителей.
Поскольку в системе Канбан на предыдущих этапах производства выпускается ровно столько деталей, сколько было изъято последующим процессом и закончив один процесс, рабочие изымают детали у предыдущего процесса. Они берут столько, сколько нужно, и тогда, когда нужно. Сигналом для изъятия служит заказ потребителя. Такая система производства называется вытягивающей.
Автономное обслуживание — это ещё один важный элемент вытягивающего производства. Поддержание работоспособного состояния станков, выполнение планового технического обслуживания, равно как и остальные элементы ТРМ, весьма существенны для успешного функционирования системы Канбан. Канбан — это передовой метод визуального управления, успех которого во многом зависит от дисциплины рабочих и понимания важности начинаний, заложенных системой 5S. Надёжным фундаментом, обеспечивающим прочность системы вытягивающего производства, является визуальное рабочее место. Правильно организованное рабочее место начинается с внедрения основ 5S и содержания рабочего места в порядке, установки подвесных знаков, постоянных улучшений, инициируемых всеми рабочими. В системе канбан отрицается принцип «больше, ещё больше», как и выпуск продукции только по той причине, что её есть из чего выпускать, поскольку это ведёт к возникновению самых громадных потерь, то есть перепроизводству.
Безусловно, «чистое» внедрение системы Канбан (особенно в условия неравномерного спроса и возможности срыва поставок комплектующих) дело непростое и мы рекомендуем гибридную систему производственных заказов и Канбан, апробированную в группе предприятий по производству офисной мебели. При этом введем несколько определений.
Заказ: заказ на производство продукции, подтвержденный поступлением денег на счет производителя.
Индикатор фактического состояния матрицы склада: минимально допустимое значение количества продукции на складе.
Матричная продукция (МП): матричные продукты (по номенклатуре и объёму), входящие в матрицу продуктов в объемах годового (месячного) матричного заказа и изготавливаемые производителем на основании индикаторов состояния склада дистрибюторской компании (ДК) в установленный период времени.
Нематричная продукция (НМП): продукция, включенная в каталог продукции (по номенклатуре), в объемах сверх указанных в матричном заказе, или не вошедшая в матрицу продуктов.
Алгоритм работы планово-диспетчерского отдела предприятия (ПДО) включает следующие шаги:
— Проверка состояния индикаторов фактического состояния склада ДК;
— Выбор МП по сработавшим индикаторам;
— Проверка объемов поставленной МП;
— В случае выполнения объема поставки МП, уведомляет ДК о выполнении объема поставки по данной продукции и формирует заказ на поставку НМП;
— Основанием для поставки НМП является подтвержденный запрос на поставку (канбан) с обязательным указанием способа доставки.
Канбан — автономная сигнальная система производства по принципу «точно вовремя». Канбаны внутри предприятия выполняют функцию производственных нарядов-заказов, они автоматически инструктируют о порядке выполнения работ. Канбаны предоставляют два вида информации:
1. Какие детали или изделия были использованы и в каком количестве;
2. Где и как должны производиться детали или изделия;
3. Канбаны указывают, что стандартные операции (матричный продукт) могут стартовать в любое время исходя из существующих условий на рабочем месте. Также канбаны устраняют необходимость бумажной работы на начальных стадиях производства.
2. Практическая часть
Работа по внедрению принципов бережливого производства на ОАО «КАМАЗ» началась в 2006 году. За это время на предприятии рассмотрено 50 тыс. проектов, 150 тыс. кайдзен-предложений. Внедрение новых подходов к производству потребовало 35 млн. рублей вложений, но результат того стоит: автогигант получил эффект в сумме 9 млрд. рублей.
По словам заместителя председателя комитета развития производственной системы ОАО «КАМАЗ» Владимира Арженцова, в 2007 году, получив первые положительные результаты внедрени Лин, на предприятии появилось осознание того, что необходимо создавать единую производственную систему во всех организациях и подразделениях группы компаний КАМАЗ. Работа началась с создания центрального управляющего органа — «Координационного совета», далее был создан «Комитет развития производственной системы». Мы назвали свою производственную систему — PSK, уточнил Владимир Арженцов.
Производственная система КАМАЗ — это совокупность бизнес-процессов ОАО «КАМАЗ», его поставщиков и товаропроводящей и сервисной сети, организованных на основе нового мировоззрения персонала на принципах бережливого производства, направленных на безопасное производство работ и удовлетворения потребителя.
«Философию Лин мы начали активно внедрять с обучения руководителей компании по программе „Лидерство“, — отметил менеджер. — „Лидерство“ — это одно из ключевых понятий в бережливом производстве».
Мировая практика показывает, что процесс внедрения принципов бережливого производства имеет три фазы (фаза изучения потребительского спроса, фаза обеспечения непрерывности потока ценности, фаза сглаживания). ОАО «КАМАЗ» находится сейчас во второй фазе.
Конечно, только за счет лидерских качеств невозможно провести коренные изменения в характере и мировоззрении персонала компании. Довольно часто приходится применять административно-организационные меры, без которых не обходятся ни в Европе, ни в Японии. Планирование и постоянная работа по вовлечению персонала позволили нам получить хорошие результаты, подчеркивает Владимир Арженцов. Количество поданных и реализованных предложений растет с каждым годом в разы. В 2010 году будет подано и реализовано проектов и предложений почти столько же, сколько за предыдущие четыре года. Количество поданных предложений в среднем на одного работника ежегодно растет почти в два раза и уже сегодня составляет более двух предложений на одного работника.
Эффект от внедрения принципов бережливого производства — не только в рублях, высвобожденных площадях и оборудовании. Важным результатом является и то, что резко вырос уровень культуры производства. Главные сборочные конвейеры стали мало отличаться от мирового стандарта. Всего три года назад они были больше похожи на склады, практически все свободное пространство на сборочных конвейерах было заставлено металлической тарой с комплектующими. Примерно такая же картина была и на конвейере сборки кабин. Повсеместно была низкая освещенность рабочих мест.
Реализуя принцип «Go And See» (Иди и Смотри), работники компании посетили множество предприятий, добившихся успехов в реализации Лин — заводы компании ТОЙОТА, а также заводы Даймлер, ХОНДА, МАЗДА.
Были открыты первые проекты по внедрению Производственной системы КАМАЗ в дилерских и сервисных центрах в Казани, Кемерово, Нижнем Новгороде.
Первый совместный проект под названием «МАЯК», помимо выявления и устранения известных семи видов потерь, выделяет еще два источника потерь, которые в переводе с японского означают «перегрузку» и «неравномерность».
Таким образом, в результате внедрения проекта «МАЯК» на ОАО «КАМАЗ» планируют снизить время такта выпускаемой продукции на главных сборочных конвейерах, конвейере сборки кабин, в цехе сборки мостов и цехе сдачи автомобилей в два раза, выравнить процессы и обеспечить работу всех вышеназванных цехов с тактом в 240 секунд, при этом увеличить производительность труда не менее чем на 20%, обеспечить выпуск 48 000 автомобилей на одном конвейере, тогда как сейчас такое количество выпускается на двух конвейерах.
Проектом «МАЯК» предусматривается стандартизация всех процессов сборки, что приведет к резкому повышению качества нашей продукции. 8 сентября состоялось торжественное открытие проекта «МАЯК». Уже сегодня есть положительные результаты. 30% операций на главном сборочном конвейере выполняются с новым тактом, который снижен в 2,2 раза по сравнению с существующим.
Заключение
Большое количество инструментов Лин создает у некоторых предприятий соблазн начать с того, что понятнее и легче. Но это ошибка. Основная концепция, лежащая в основе Лин — ускорение потока, или (что тоже самое) — сокращение времени производственного цикла. Поэтому начинать нужно с выстраивания потока и сокращения потерь, которые этому препятствуют. Часто «внедренцы» (консультанты также не исключение) сосредотачиваются на потерях в принципе, добиваясь повсеместного их сокращения. Это скорее ошибка, поскольку все потери должны рассматриваться прежде всего с точки зрения потерь скорости потока. Такой подход позволяет держать фокусировку на главном — ускорении генерации денежного потока.
Ускорение потока связано с сокращением незавершенного производства. Поэтому основной подход для балансировки потока в Лин — последовательное и неуклонное снижение количества изделий в партии. При очередном снижении количества изделий в партии выявляется большое число потерь (например, слишком долгая переналадка, ненужная транспортировка), которые и нужно исключать. Этот процесс и является самым трудоемким. Он затягивает процесс отладки на годы. Получение реальных результатов для бизнеса обычно составляет 5−6 лет.
Внедрение Лин — очень хрупкий процесс и большинство внедрений в мире терпит неудачу. Для ускорения внедрения и получения стабильных результатов мы рекомендуем использовать одновременно принципы Теории ограничений — начинать внедрение инструментов Лин не по всей цепочке, а в так называемых «узких местах» производственной системы. В этом случае первые реальные результаты появляются через 2−3 месяца. Стабильность результатов гарантируется тем, что вы всегда будете фокусировать свое внимание на основном факторе, ограничивающем получение финансовых результатов. Правильность такого подхода доказала и сама Тойота.
Кроме того, есть основания полагать, что инструменты бережливого производства естественным образом ограничены следующими условиями:
— Длительный жизненный цикл продукции
— Относительно небольшой ассортимент продукции
— Относительно постоянный спрос на продукцию При нарушении этих условий встает вопрос о принципиальной возможности сбалансировать поток и в этом случае лучше вообще изначально ориентироваться на управление на основе Теории ограничений, которая применима и в этих условиях.
Список используемых источников
логистический менеджмент лин канбан
1. Манн Д. «Бережливое управление: Бережливым производством», РИА «Стандарты и качество», 2008.
2. Луйстер Т., Теппинг Д. «Бережливое производство: от слов к делу», РИА «Стандарты и качество», 2008.
3. Вумек Джеймс П., Джонс Дэниэл Т. «Бережливое производство: Как избавиться от потерь и добиться процветания вашей компании», пер. с английского — (5е изд.) М: Альпина Бизнес Букс, 2010.
4. Майкл Джордж «Бережливое производство плюс шесть сигм в сфере услуг», издательство «Манн, Иванов и Фербер», 2011
5. «Производство без потерь для рабочих», пер. с англ. — М.: ИКСИ, 2007.
6. Паскаль Деннис «Сиртаки по-японски. О производственной системе Тойоты и не только», пер. с англ. — М.: ИКСИ, 2007. «Точно вовремя для рабочих», пер. с англ. — М.: ИКСИ, 2007.
7. Майкл Джордж «Бережливое производство плюс шесть сигм в сфере услуг», издательство «Манн, Иванов и Фербер», 2011
8. «Стандартизованная работа», пер. с англ. — М.: ИКСИ, 2007.
9. «Кайдзен для рабочих», пер. с англ. — М.: ИКСИ, 2007.
10. «Быстрая переналадка для рабочих», пер. с англ. — М.: ИКСИ, 2008.