Накладные направляющие в станинах
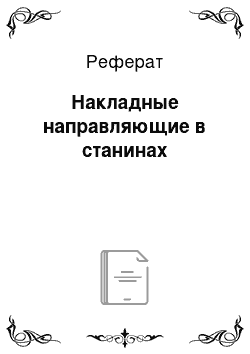
Некоторые рекламные утверждения об улучшении прямолинейности перемещения рабочих органов по сравнению с точностью поверхностей, к которым эти направляющие прикреплены, находят частичное подтверждение только в отношении вертикальной плоскости, но никак не горизонтальной. Следовательно, необходимо получить при механической обработке не только точные размеры, но и высокую точность в отношении… Читать ещё >
Накладные направляющие в станинах (реферат, курсовая, диплом, контрольная)
Кроме цельных направляющих скольжения, используют накладные (рис. 14.31 и 14.32). Такие направляющие представляют собой закаленные планки, изготовленные из легированных сталей. Для этих целей рекомендуются стали: 18ХГТ, упрочняемая цементацией и последующей объемной закалкой; 8ХФ, подвергаемая закалке с индукционным нагревом; ШХ15СГ с объемной закалкой. Планки винтами крепят к станине. Твердость рабочих поверхностей планок достигает HRC 62, в то время как твердость закаленного чугуна на 10 ед. меньше.
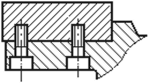
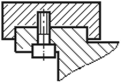
Рис. 14.31. Схемы крепления накладных направляющих
Особенность технологии изготовления таких направляющих состоит в том, что поверхности станины под крепление планок можно окончательно подготовить, а затем прикрепить планки, обладающие высокой точностью.
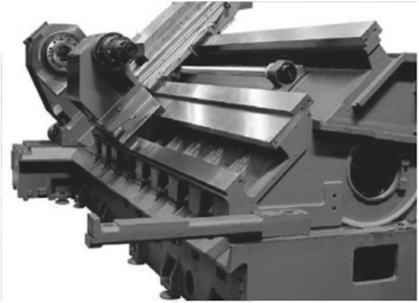
Рис. 14.32. Станок со стальными накладными направляющими
В качестве материала трущихся по станине поверхностей столов, кареток, салазок и др. в настоящее время используют чугуны, бронзы, компаунды, пластики. К сопряжениям предъявляют следующие требования:
- — износостойкость;
- — малая величина коэффициента трения покоя, близость его к коэффициенту трения движения и малая зависимость от скорости перемещения;
- — стабильность под воздействием различных факторов: внутренних напряжений, тепловых нагрузок; влаги, масел, кислот, щелочей;
- — высокая жесткость;
- — облегченность достижения точного сопряжения между поверхностями скольжения станины и сопрягаемой детали;
- — экономические показатели изготовления.
Чугун в качестве материала столов, кареток, салазок превосходит прочие материалы по жесткости, а с точки зрения антифрикционных свойств уступает бронзе, компаунду и пластмассам. Но он может превосходить их по долговечности в реальных эксплуатационных условиях, когда не обеспечена хорошая защита направляющих от попадания загрязнений на трущиеся поверхности.
>".
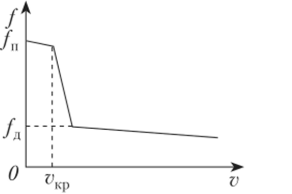
Рис. 1433. Зависимость коэффициента трения от скорости.
V
Малое значение коэффициента трения и малая разница между значениями коэффициентов трения покоя и движения в направляющих скольжения призваны уменьшить вероятность возникновения при малых скоростях явления slip-stop, которое вызывает скачкообразность движения рабочего органа.
На рис. 14.33 показано, как с увеличением скорости перемещения v в начале движения в момент г>кр коэффициент трения /п резко падает до значения /д. Опасность возникает при торможении. При уменьшении скорости перемещения происходит резкое возрастание коэффициента трения. Увеличиваются силы сопротивления перемещению, и движущийся рабочий орган останавливается, не достигнув нужного положения.
Защитные уплотнения выполняют в виде комбинации стальных, резиновых и пластмассовых скребков, прикрепленных к торцу стола, суппорта, салазок и прижимаемых к направляющим благодаря собственной упругости или действия пружины.
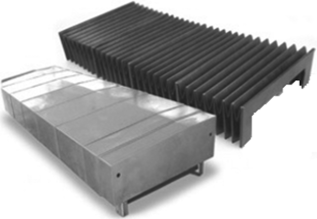
Рис. 14.34. Защита направляющих: телескопическая и гофрозащита.
Кроме скребков применяют телескопические щитки, гармониковые меха (гофрозащиту) (рис. 14.34) и стальную ленту.
Чугунные направляющие столов, кареток и салазок подвергают шабровке (рис. 14.35). На направляющие станины, используя смоченный в краске кусок войлока или поролона, наносят слой краски, о толщине которого при определенных навыках можно судить по интенсивности окраски. Из красок наиболее удобна берлинская лазурь, которая хорошо просматривается как на светлом, так и на темном материале. Сопрягаемую деталь накладывают на окрашенное место станины и перемещают ее несколько раз вдоль направляющих. Отпечаток краски возникает только на выступающих местах, которые и нужно удалить шабровкой. Многократно повторяя описанную процедуру, добиваются очень точного взаимного сопряжения направляющих.
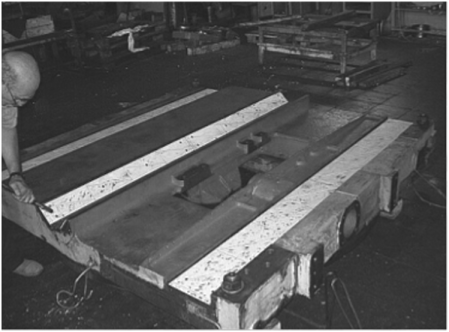
Рис. 1435. Операция шабровки.
Завершают шабровку разбивкой поверхности на пятна. В одном квадратном сантиметре окончательно обработанной поверхности должно быть заданное число пятен краски, которое может быть более десяти. Кроме того, щуп толщиной 0,02—0,03 мм не должен входить в стык между сопрягаемыми поверхностями. Иногда оговаривают, что щуп может «закусывать на глубину не более нескольких (конкретно скольких) миллиметров».
Шабровка — трудоемкая ручная работа, предоставляющая возможность достичь чрезвычайно высокой точности сопряжения. Попытки получить такую точность шлифованием пока не увенчались успехом. Точно так же, несмотря на многолетние и многочисленные попытки, не удалось механизировать шабровку.
Бронзовые пластины направляющих крепят к столам, кареткам, салазкам коническими головками винтов. Пластмассовые направляющие в виде лент приклеивают эпоксидной смолой. Клей наносят с помощью шпателя на ту сторону ленты, которая для лучшей адгезии имеет повышенную шероховатость. Деталь после приклейки пластмассовых лент укладывают на станину, при необходимости увеличивают ее тяжесть за счет груза и оставляют чаще всего на сутки до полного отверждения клея.
Из отечественных пластмасс наилучшие результаты показывает наполненный фторопласт, из импортных материалов — торсайт. В качестве наполнителей, призванных улучшить антифрикционные свойства и увеличить жесткость материала, выступают бронзовый порошок, графит, дисульфид молибдена, кокс. Коэффициент трения в направляющих из наполненного фторопласта в паре с чугуном или закаленной сталыо составляет 0,04—0,06 и в области низких скоростей скольжения мало изменяется. Для таких направляющих характерны малая сила трения, высокая износостойкость, достаточно высокая контактная жесткость.
Направляющие с прикрепленными бронзовыми пластинами или приклеенными лентами пластика подвергают шабровке аналогично описанной процедуре шабрения чугунных поверхностей.
Избежать шабровки можно при использовании компаунда в качестве материала направляющих сопряженной со станиной детали. Компаунд — это двухкомпонентная композиция на основе эпоксидного клея с добавками графита и дисульфида молибдена в качестве антифрикционных присадок и мелкотертой глины в качестве основы, обеспечивающей жесткость.
Компаунд изготавливают по свойству жидкотекучести в трех исполнениях: густой, средний и жидкий. Густой компаунд имеет пастообразный характер, его наносят шпателем, средний запрессовывают, жидкий заливают. Для протяженных поверхностей лучше всего использовать пастообразный компаунд, который наносится на поверхность стола, каретки шпателем, затем деталь переворачивают и укладывают на станину. Для поверхностей средних размеров наиболее надежным способом формообразования является запрессовка компаунда.
Непосредственно перед использованием в основную массу компаунда вводят отвердитель, тщательно перемешивают. Использовать массу с введенным отвердителем нужно в течение ближайших 15—20 мин, позднее начнется ее отверждение.
На рис. 14.36 представлен вариант, в котором полость под компаунд 4 и 7 вырезана, а металл опорной поверхности в местах 5 и б удаляют механической обработкой после отверждения компаунда. Слой компаунда равен примерно 2 мм. Для получения такой толщины слоя между сопряженной деталью 2 и станиной 1 зазор создан конструкцией детали, но возможен вариант с прокладками.
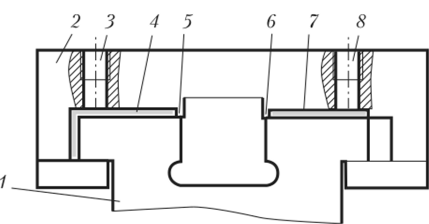
Рис. 14.36. Схема направляющих с компаундом.
Станину перед началом работ выверяют. На ее направляющие во избежание прилипания к ним компаунда распыляют тонкий слой воскового покрытия, растирают до минимальной толщины. Поверхность, к которой компаунд будет приклеиваться, для лучшей адгезии выполняют с низкой шероховатостью Rz 40-ь80 мкм.
При использовании запрессовки или заливки вокруг направляющих сопряженной детали выполняют ограждение, оставляя небольшое окно в наиболее удаленном от литников 3, 8 месте. Производители компаунда поставляют вместе с материалом ручные прессы для выполнения работ. Появление компаунда в окне свидетельствует о заполнении всего пространства направляющих.
Через 24 ч можно продолжать работу с сопряженной деталью. Компаунд после отверждения идеально копирует макрои микрогеометрию направляющих станины.
В металлорежущих станках с ЧПУ в последнее время вместо направляющих скольжения начали широко использовать направляющие качения. Коэффициент трения в этих направляющих снизился до 0,05. Первоначально появились роликовые блоки, которые получили название «танкетки» (рис. 14.37).
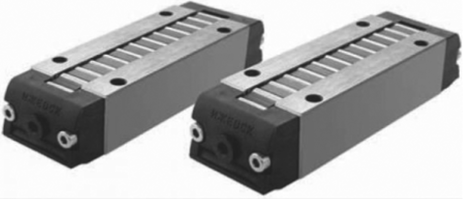
Рис. 1437. «Танкетки».
"Танкетки" прикреплены к подвижному узлу, опорой для роликов служит закаленная поверхность базовой детали. Изобретение такого устройства убрало зазор между направляющими и позволило существенно увеличить скорость перемещения рабочих органов. Однако в дальнейшем при эксплуатации подобных направляющих выявился ряд трудностей, связанных с необходимостью изготовления с чрезвычайно высокой точностью мест для установки танкеток и точного их монтажа. Перекосы и чрезмерные натяги стали причиной выхода танкеток из строя.
Несколько позднее направляющие качения были усовершенствованы, появился новый класс направляющих — рельсовые (рис. 14.38 и 14.39). Именно такой вид направляющих сегодня пользуется наибольшей популярностью.
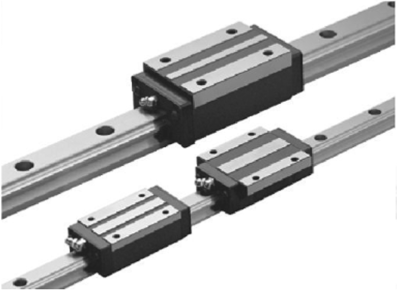
Рис. 14.38. Внешний вид направляющих качения.
Направляющие качения представляют собой рельсы (штанги, шины). Каждый из рельсов несет одну-две подвижные каретки, которые четырьмя или шестью винтами скрепляют с неподвижным рабочим органом станка. Телами качения, циркулирующими в каретках, являются шарики или ролики. Роликовые направляющие обладают в сравнении с шариковыми повышенной жесткостью.
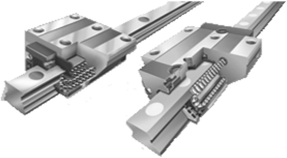
Рис. 1439. Устройство кареток шариковых и роликовых направляющих
Рельс имеет специальный профиль, с каждой из боковых сторон имеется по две дорожки качения (рис. 14.40). В рельсовой направляющей стандартного типоразмера они расположены под углом 90° друг к другу и под 45° к горизонтали. В миниатюрных рельсовых направляющих применяют только две дорожки. Крепление рельсовой направляющей к станине станка осуществляется через сквозные вертикальные отверстия, выполненные с постоянным шагом по длине рельса.
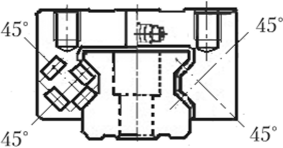
Рис. 14.40. Расположение дорожек качения в направляющих качения
Каретка располагается сверху на рельсе и охватывает его с боковых сторон. Внутри каретки находится четыре кольцевых ряда тел качения, шариков или роликов, которые катятся по дорожкам качения рельса, а возвращаются внутри каретки. Располагаются ряды с каждой из сторон каретки под углом 90° друг к другу, как показано на рис. 14.40. Пластмассовый сепаратор объединяет ролики или шарики каждого ряда в «гусеничную» цепь. В каретках большинства моделей имеются смазочные отверстия и ниппель, через который в них подается консистентная смазка. По торцам с двух сторон каретка снабжена устройством защиты от попадания внутрь загрязнений.
С целью повышения жесткости направляющих между рельсами, каретками и телами качения создают предварительный натяг (преднатяг), который подразделяется па малый, средний и увеличенный.
Главными преимуществами рельсовых направляющих является устойчивость к резким изменениям нагрузки, легкость и плавность движения, высокая точность, жесткость, надежность.
Основной задачей при изготовлении станин с такого типа направляющими является подготовка поверхностей, к которым крепятся рельсы. В горизонтальном направлении один рельс 2 является ведущим, его ориентируют по вертикальному буртику станины 1 (рис. 14.41). Второй рельс занимает свое положение самостоятельно.
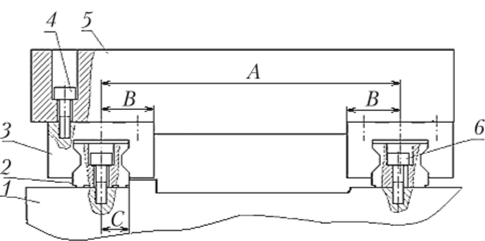
Рис. 14.41. Направляющие качения на станине.
Каретки 3 притянуты винтами 4 к поверхностям подвижного рабочего органа 5. Их нужно поджать к вертикальным буртикам. Нормальная сборка будет обеспечена, если размеры А и В в станине и сопрягаемой подвижной детали 5 будут выполнены одинаковыми, равными размеру в каретке, с жестким допуском ±0,1 мм. С таким же допуском должны быть выполнены размеры поперечных и продольных координат резьбовых отверстий в станине, равные размерам в рельсе. На рис. 14.41 показан поперечный размер С.
Некоторые рекламные утверждения об улучшении прямолинейности перемещения рабочих органов по сравнению с точностью поверхностей, к которым эти направляющие прикреплены, находят частичное подтверждение только в отношении вертикальной плоскости, но никак не горизонтальной. Следовательно, необходимо получить при механической обработке не только точные размеры, но и высокую точность в отношении плоскостности, прямолинейности, параллельности, перпендикулярности различных поверхностей станин и сопрягаемых деталей, на которых монтируют рельсы и каретки направляющих.
Современный подход к обработке с достижением перечисленных высоких требований свидетельствует, что их целесообразно фрезеровать на высокоточных обрабатывающих центрах. Именно фрезеровать, а не шлифовать. Шлифовальные станки не могут формировать горизонтальные и вертикальные поверхности двух взаимно перпендикулярных направляющих. Тем более что на ОЦ одновременно с лезвийной обработкой плоскостей имеется возможность в одном технологическом установе образовывать резьбовые крепежные отверстия, что немаловажно для точного монтажа направляющих.
Попытки просверлить отверстия по рельсам на сборке обрекают монтаж высокоточных устройств на серьезную неудачу. Достаточно, как показано на рис. 14.41, касания боковой стороны рельса винтом 6 при завинчивании, и достижение высокой точности прямолинейности перемещения рабочего органа в горизонтальной плоскости станет невозможным.
Вопросы и задания для самопроверки
- 1. Какие детали относятся к базовым, какие поверхности для них характерны, какие технические требования к ним предъявляются?
- 2. Какие материалы используют для изготовления базовых деталей?
- 3. Какие станки используют для обработки базовых деталей?
- 4. Каковы способы уменьшения уровня внутренних напряжений и их особенности?
- 5. Как выполняется вибрационное старение?
- 6. В чем преимущества и недостатки каждого из способов уменьшения уровня внутренних напряжений?
- 7. Как компенсировать действие сил тяжести при установке заготовок?
- 8. Каковы особенности изготовления станин с направляющими скольжения?
- 9. Опишите назначения направляющих качения и подготовку поверхностей для их монтажа.