Назначение и конструктивное использование сталеразливочных ковшей
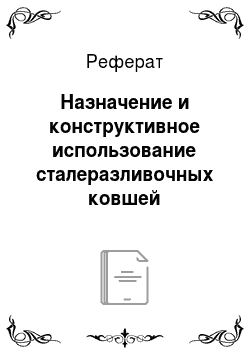
Периодичность работы ковша обусловливает резкий нагрев и охлаждение огнеупорной футеровки. Разница температур наливаемой стали и подогретой до 300—800° С футеровки составляет 800—1350° С. Нередко охлаждение ковша ускоряют обдувкой воздухом и даже поливом водой, что создает весьма жесткие условия службы огнеупоров. При очистке ковшей от остатков шлака не исключены механические повреждения… Читать ещё >
Назначение и конструктивное использование сталеразливочных ковшей (реферат, курсовая, диплом, контрольная)
Назначение и конструктивное использование сталеразливочных ковшей.
План.
- Введение
- 1.Сталеразливочные ковши и их эксплуатация
- 2.Футеровка ковшей
- 3. Оборудование для выпуска стали из ковша
- Заключение
- Литература
Современный период развития металлургической технологии характеризуется постепенным выносом операций, обеспечивающих получение металла высокого качества, непосредственно из плавильного агрегата во вспомогательный агрегат или в специально оборудованный ковш. Роль самих плавильных агрегатов все больше сводится к получению жидкого полупродукта определенного состава и температуры.
Сталь из мартеновской печи или электропечи выпускают по желобу в сталеразливочный ковш, а затем разливают по изложницам сверху или сифоном в зависимости от принятого метода и условий разливки.
От качества и своевременной подготовки к плавке оборудования в значительной степени зависит и качество слитка.
Подготовку выпускного желоба и сталеразливочного ковша, сборку разливочной канавы следует выполнять тщательно, а само оборудование должно находиться в исправном состоянии. Только при этих условиях возможны безаварийная разливка стали и получение от плавки высокого выхода годного.
Сталеразливочные ковши служат для приема стали из сталеплавильного агрегата, транспортирования и последующего ее литья в изложницы или на МНЛЗ.
1. Сталеразливочные ковши и их эксплуатация.
Сталеразливочный ковш выполняет следующие функции:
1) служит емкостью для транспортировки металла от сталеплавильного агрегата до места разливки;
2) является устройством, с помощью которого сталь распределяется по изложницам или по кристаллизаторам установки непрерывной разливки;
3) выполняет роль агрегата, в котором осуществляется ряд металлургических процессов (раскисление, легирование, обработка вакуумом, продувка инертным газом, обработка жидкими синтетическими шлаками или твердыми шлаковыми смесями и т. п.);
4) служит емкостью, в которой металл выдерживается при требуемой температуре в течение всего времени разливки плавки.
Соответственно к ковшу предъявляются следующие требования:
ковш (без металла) должен быть возможно более легким и компактным;
ковш должен быть снабжен простыми и надежными устройствами, обеспечивающими выдачу металла необходимыми порциями и с необходимой интенсивностью;
ковш должен иметь футеровку, обеспечивающую возможно более длительную его кампанию от ремонта до ремонта;
4) конструкция и футеровка ковша должны обеспечивать минимальные потери тепла (минимальноеохлаждение металла) в течение периода разливки.
Кожух ковша — сварной, форма ковша — усеченный конус со сферическим днищем. Отношение диаметра к высоте — близко к единице. Обычно сечение ковшей круглое, в некоторых случаях — слегка овальное (для того, чтобы при неизменном размере траверсы разливочного крана использовать ковши большей емкости). Объем ковша рассчитывается исходя из объема всей массы металла плюс определенный (5—10%) слой шлака.
Сменное оборудование для разливки стали состоит из сталеразливочных ковшей и разного типа изложниц с поддонами. В зависимости от способа разливки и марки стали используется различное вспомогательное оборудование. В цехах с машинами непрерывного литья заготовок значительно сокращается количество оборудования и высвобождаются производственные площади.
Сталеразливочный ковш представляет собой открытую футерованную емкость, позволяющую в течение небольшого промежутка времени сохранять жидким металл и разливать его в слитки. С учетом способа разливки слитки могут отливаться в изложницы непосредственно из ковша или с помощью дополнительного оборудования и приспособлений (промежуточных ковшей, воронок, центровых изложниц и т. п.).
Сталеразливочные ковши, применяемые на отечественных заводах, стандартизированы по массе принимаемого жидкого металла (ГОСТ 7358−55). С учетом их емкости под плавку подается один, два или даже три ковша. Определенные трудности возникают при использовании двух ковшей разной емкости, подаваемых на одну плавку. Поэтому на современных заводах эксплуатируются ковши одной емкости.
Металлическая конструкция ковшей выполняется из толстолистовой стали и в зависимости от способа изготовления (сварной или клепаный) будет различаться по массе.
Ковши сверху могут выполняться с одним или двумя носками, по которым отводится избыток шлака в шлаковые чаши или коробки. В конверторных и эдектросталеплавильных цехах, а также в мартеновских, имеющих качающиеся мартеновские печи, надобность оборудовать ковши носками отпадает, так как нужное количество шлака и даже часть металла можно задержать в сталеплавильном агрегате.
Днище кожуха ковша выполняется с одним или двумя отверстиями, предназначенными для выхода торцовой части сталеразливочных стаканов. К боковой поверхности кожуха крепится стопорный механизм; если разливка производится через два стакана, число стопоров и их механизмов соответственно удваивается.
В зависимости от емкости сталеразливочные ковши принято делить на группы (табл.1).
Таблица 1.
Примерные размеры сталеразливочных ковшей.
2. Футеровка ковшей.
сталеразливочный ковш.
В качестве огнеупорной футеровки используют стандартный шамотный кирпич (ГОСТ 5341—69). Общая толщина футеровки ковша слагается из двух рядов кирпича — арматурного и рабочего. Швы между ними не должны совпадать во избежание прорывов металла. Также не допускается совпадение вертикальных швов рабочего ряда. К ковшевому кирпичу предъявляются требования сохранения постоянства объема при его нагревании или допускается небольшое изменение размеров, обеспечивающих достаточную плотность всей кладки.
Внутренний арматурный ряд футеруют нормальным кирпичом, укладываемым на плашку с использованием огнеупорной массы, состоящей из огнеупорной глины и шамотного порошка, замешанных на воде. Футеровку днищ выполняют из стандартного ковшевого кирпича.
На стойкость футеровки ковшей влияют их размеры (высота, диаметр, конусность); условия горячей обработки (длительность оборота, способ охлаждения, число ремонтов днища); сортамент стали; условия выпуска жидкой стали; количество и состав шлака в ковше присадки на шлак извести или шамота для охлаждения шлака и снижения его активности; дополнительные рафинировочные операции в ковшах; условия разливки (сверху, сифонным способом, на УНРС); скорость разливки — низкая скорость приводит к высокому износу футеровки; продолжительность слива шлака после окончания разливки.
Износу огнеупорной кладки одновременно способствуют механические, физические, химические факторы, имеющие сложный характер. С увеличением длительности разливки действие этих факторов усиливается (химическая эрозия, термические напряжения особенно в нижней части ковша).
Для кладки рабочего наружного ряда используют специальный по форме и размерам ковшевой лекальный кирпич, обеспечивающий наименьшую толщину швов (допускается толщина шва не более 2 мм). Кладка рабочей футеровки стен ковша делается ступенчатой, по мере опускания вниз она утолщается. В зависимости от высоты и емкости ковша рабочую футеровку стен разделяют по высоте на две или три зоны, толщина которых получается из условий полного использования кирпича, укладываемого на ребро к арматурному ряду. Стенка ковша со стороны, противоположной желобу печи или летки конвертора, выкладывается толще за счет применения более широкого кирпича.
Иногда кирпичи рабочего ряда стен ковша укладывают по спирали так называемым винтовым способом.
На отечественных и зарубежных заводах ведутся работы по применению набивной футеровки ковша.
Все шире применяются торкретирующие массы для удлинения срока эксплуатации ковша и снижения удельного расхода огнеупоров. В Японии, например, практикуется способ восстановления изношенной футеровки ковша набивкой обожженных огнеупорных масс без связки в промежуток между железным шаблоном и огнеупорной кладкой. При заполнении ковша сталью шаблон расплавляется и связывает огнеупорную массу.
Наша промышленность выпускает стандартные ковши емкостью от 50 до 480 т. Масса порожнего футерованного ковша емкостью 300 т 72,5 т, масса порожнего 480-т ковша 136,3 т. Разливочный ковш переносится и удерживается во время разливки разливочным краном. Применяются разливочные краны различной грузоподъемности, т: 260—75/15; 350—75/15; 450—100/20; 630—90/16. Первое число означает грузоподъемность главной.
тележки, второе и третье числа — грузоподъемности большого и малого подъемов вспомогательной тележки. Разливочный кран большой грузоподъемности — сложное и дорогостоящее сооружение. Обычно емкость сталеплавильного агрегата на действующих заводах ограничивается именно грузоподъемностью разливочного крана.
Ковши футеруются или шамотом, иди магнезито-доломитовыми или высокоглиноземистыми огнеупорными материалами. Футеровка ковша делается или из кирпичей, или монолитной. Для изготовления монолитной футеровки требуется соответствующее оборудование, однако при этом заметно снижаются трудовые затраты.
Стойкость футеровки ковшей, изготовленных из обычных шамотовых кирпичей, 10—15 плавок (наливов). Футеровка изнашивается неравномерно, наибольший износ наблюдается в том месте, куда падает струя металла (так называемая «боевая стенка» Ковша), и в районе шлакового пояса, В тех случаях, когда металл в ковше подвергается различным методам обработки, включая методы, связанные с энергичным перемешиванием металла, стойкость шамотовой футеровки резко снижается; в этих случаях футеровка ковша делается из высокоогнеупорных материалов. В зависимости от качества огнеупорных материалов технологии обработки стали в ковше расход ковшевых огнеупоров колеблется от 3 до 5 кг/т стали.
Для футеровки сталеразливочных ковшей в СССР используются шамотные уплотненные (открытая пористость 18 и 19%) и плотные (открытая пористость до 16%) изделия марки КШУ-32, КШУ-37, КШУ-39, КШП-37 и КШП-39. Цифра в обозначении марки соответствует минимальному процентному содержанию в огнеупоре окиси алюминия. Основные физико-химические показатели шамотных изделий, регламентируемые ГОСТ 5341–69, приведены в табл. 2.
Таблица 2.
Характеристика прочности огнеупоров.
Огнеупорный материал. | Предел прочности на сжатие при комнатной температуре кН/см2. | Температура начала деформации при нагрузке 20 Н/см2, 0С. | Огнеупорность, 0С. | |
Шамот. | 0,98−6,88. | |||
Динас. | 2,45−2,94. | |||
Магнезит. | 2,94−4,90. | |||
Хромомагнезит. | 2−5. | 1500−1630. | ||
Периклазошпинелидный. | 4−8. | >1550. | ||
Периодичность работы ковша обусловливает резкий нагрев и охлаждение огнеупорной футеровки. Разница температур наливаемой стали и подогретой до 300—800° С футеровки составляет 800—1350° С. Нередко охлаждение ковша ускоряют обдувкой воздухом и даже поливом водой, что создает весьма жесткие условия службы огнеупоров. При очистке ковшей от остатков шлака не исключены механические повреждения огнеупора. Из описанных выше условий эксплуатации ковшей вытекает комплекс требований к рабочим свойствам огнеупоров, включающий хорошую устойчивость против коррозионного и эрозионного разрушения расплавленным металлом и шлаком, достаточную термическую стойкость, отсутствие значительной усадки при температурах службы. Конкретные физико-химические показатели огнеупоров (огнеупорность, плотность, прочность и т. д.) могут быть весьма различными, так как стойкость зависит от всего комплекса свойств. Показатели определяются соответствующими стандартами и техническими условиями на штучные изделия и неформованные огнеупоры, предназначенные для сталеразливочных ковшей. В последние годы все большее применение находит внепечная обработка металла в ковшах: продувка инертными газами, вдувание порошкообразных реагентов, обработка синтетическими шлаками, вакуумирование, подогрев в ковше и т. п. Условия службы огнеупоров в этих случаях существенно утяжеляются и возникает необходимость использования огнеупоров, более устойчивых к действию разрушающих факторов. В таких ковшах применяют преимущественно высокоглиноземистые материалы. [2, с. 209].
3. Оборудование для выпуска стали из ковша.
Оборудование для выпуска стали из ковша состоит из стопорного устройства и разливочного стакана. Обычно в каждом ковше устанавливается один комплект такого оборудования, однако в больших ковшах для ускорения разливки монтируются два таких комплекта. Разливочный стакан устанавливается в гнездо, предусмотренное в днище ковша (в самой низкой точке днища — так, чтобы в стакан сливался из ковша весь металл, без остатка). После разливки каждой плавки стакан заменяется новым.
Стопорные устройства бывают двух типов:
вертикальные стопоры (или просто стопоры). Данное устройство включает вертикальный стопор, проходящий внутри ковша через массу металла (рис. 1). С помощью механизма рычажного типа стопор поднимается и опускается. При подъеме нижний конец стопора («пробка» стопора) отходит от разливочного стакана и через открывшееся отверстие металл из ковша выливается в изложницу. Стопор состоит из сплошного или полого металлического стержня, на который надета серия катушек.
из огнеупорного материала (обычно из шамота); стопорные устройства скользящего типа. Крепится к кожуху ковша снизу снаружи. Отверстие разливочного стакана перекрывается (и открывается) горизонтальным отсекающим движением скользящей огне.
упорной плиты. В зависимости от вида движения отсекателя (прямолинейное или вращательное) скользящие затворы делят на шиберные (рис. 2, а) и поворотные или дисковые (рис. 2,б) с несколькими отверстиями разного диаметра. Дисковые затворы позволяют менять по ходу разливки скорость истечения металла из ковша или, наоборот, сохранять ее по мере опорожнения ковша (по мере опускания уровня металла в ковше проводить разливку через отверстия все большего диаметра). Расположение затворного устройства вне ковша позволяет производить необходимые операции с находящимся в ковше металлом (перемешивание и т. д.) без опасения повредить стопор и вызвать этим аварийный выход металла из ковша. Надежность скользящего затвора зависит от огнеупорности и износостойкости скользящих плит, от точности их изготовления и притирки.
В процессе разливки сечение разливочного стакана меняется. Опасным является случай так называемого зарастания стакана. Такое явление наблюдается, в частности, при разливке стали, раскисленной алюминием. Образующиеся при раскислении частицы корунда А12О3 оседают на внутренних стенках стакана, образуя тугоплавкую и прочную настыль, внутренний диаметр стакана начинает уменьшаться и, если не принять необходимых мер, разливка может вообще прекратиться. Для предотвращения таких явлений, а также для предотвращения случаев застывания металла (особенно первых его порций) в полости стакана за время от выпуска плавки до начала разливки в разливочный стакан подается (с небольшой интенсивностью) инертный газ. Падение струи стали из ковша вниз в изложницу или в кристаллизатор сопровождается рядом явлений, отрицательно влияющих на качество металла.
Большой напор металла, вытекающего из крупного ковша, вызывает интенсивное разбрызгивание струи при ударе о дно изложницы или о поверхность жидкого металла. При большом напоре струя перестает быть непрерывной, что приводит к эжектированию окружающего воздуха, интенсивному развитию вторичного окисления стали, увеличения содержания азота и т. д.
Рисунок 1-Сталеразливочный сварной ковш емкостью 480 т со стопорным устройством: 1-сливной носок; 2-цапфа; 3-плита; 4-упор; 5-пояс жест кости; 6-стопор; 7-корпус; 8-огнеупорный кирпич; 9-скоба; 10-вилка; 11-ползун; 12-вилка; 13-направляющая труба; 14-винтовой механизм; 15- гидравлический цилиндр; 16-пружина; 17-ручной рычажный механизм; 18-шамотная пробка; 19-сталевыпускной стакан.
Диаметры разливочных стаканов могут быть различными (от 50 до 120 мм), но все они достаточно велики.
При истечении металла через отверстие в днище ковша создается положение, при котором основное перемещение жидкого металла происходит по оси стакана. Получается, что столб металла, располагающийся над отверстием стакана, как бы непрерывно «проваливается», а объемы металла, находящиеся вблизи стенок ковша, не перемещаются и поступают на разливку в последнюю очередь.
Рисунок 2-Скользящий затвор: а-шиберного типа (1-разливочный стакан ковша; плиты; 3 -гнездовой кирпи; 4 — наружный разливочный стакан; 5- металлический защитный кожух; 6 -устройство для перемещения плиты); б-вращающийся (1-верхний стакан, 2-неподвижная плита, 3-вращающаяся плита. 4-коллектор, 5-ротор, 6-пружины, 7-редуктор, 8-электродвигатель, 9-предохранительный кожух, 10-футеровка промежуточного ковша).
Температура и свойства этих объемов металла отличаются от температуры и свойств внутренних слоев, что приводит к нестабильности качества слитков, отлитых в различные периоды времени по ходу разливки. При входе жидкого металла в стакан происходит сжатие (сужение) струи, которое продолжается до определенной глубины, после чего поток снова расширяется, заполняя все поперечное сечение стакана. Отрыв потока от стен каналами связанное с ним вихреобразование создают в стакане зону пониженного статического давления и являются основной причиной увеличения сопротивления движению жидкости в струе, а также захвата струей воздуха. Дополнительная трудность при решении проблемы организации истечения струи металла из ковша заключается в том, что по мере опорожнения ковша меняется напор металла (высота металла в ковше); может оказаться, что удовлетворительный характер истечения струи в начале разливки (небольшая величина отношения диаметра струи к высоте столбаметалла в ковше) сменяется неудовлетворительным в конце разливки (при неизменном диаметре струи напор металла резко уменьшился). На характер движения металла в ковше и в стакане влияет также расположение стакана относительно стенок ковша.
На практике для организации нормальной разливки используют ряд приемов:
1) сечение, размеры и форму разливочного стакана и его расположение в ковше выбирают по результатам предварительного моделирования с учетом размеров ковша, состава стали и необходимой скорости разливки. Горизонтальное сечение стаканов может быть круглым, эллиптическим, крестообразным и т. д. По высоте стаканы могут быть цилиндрическими, цилиндрическими с закруглением углов на входе струи, формы диффузора, конфузора, в форме диффузора с переходом в цилиндр и др. (рис.3).
2) используют удлиненные стаканы таким образом, чтобы металл проходил по разливочному стакану, не соприкасаясь с окружающим воздухом; защищают струи металла, вытекающего из ковша, инертным газом, подаваемым из кольцеобразного устройства, окружающего струю; инертный газ подают непосредственно в стакан таким образом, что условия истечения струи определяются не изменяющимся по ходу разливки напором металла, а воздействием выходящего из пористых стенок стакана инертного газа;
5) перемешивают металл в ковше;
6) применяют промежуточные разливочные устройства (воронки, промежуточные ковши и т. п.), позволяющие разливать металл почти до конца разливки всей плавки с неизменной и требуемой скоростью истечения.
Использование различных промежуточных устройств позволяет резко уменьшить разбрызгивание при ударе струи о дно изложницы или о поверхность разливаемого металла. Применение таких промежуточных разливочных устройств, как воронки, корытообразные футерованные емкости с несколькими отверстиями в днище и т. п., ограничено отдельными случаями (например, разливка единичных крупных слитков для поковок).
Применение же промежуточных ковшей получило широкое распространение, особенно при непрерывной разливке, когда характер воздействия струи на кристаллизующийся металл имеет особое влияние на качество слитка.
Рисунок 3-Формы сталеразливочных конфузорных стаканов:
а-щелевого для отливки листових слитков; б-крестового.
В зависимости от условий поставки ковш может изготовляться с правым или левым расположением носка. Если условия производства стали позволяют обеспечить скачивание шлака перед выпуском плавки (конвертерный, электросталеплавильный цехи), сливной носок у ковша отсутствует. В случае оборудования разливочного ковша затворами с электромеханическим приводом на его кожухе размещаются редукторы с электродвигателями.
Ковши малой вместимости имеют плоское днище, большегрузные — выпуклое наружу. В днище вварены фланцы, снабженные штырями для крепления затворов, служащих для дозированного выпуска жидкой стали.
Как правило, сталеразливочные ковши оборудованы двумя затворами, реже — одним. Вариант с двумя затворами следует считать предпочтительным, так как в этом случае не только улучшается оборачиваемость ковша, но и увеличивается в два раза надежность агрегата в целом, поскольку при выходе из строя во время разливки одного затвора можно использовать второй в качестве резервного.
В ковшах с двумя стопорами время разливки стали сокращается. При этом улучшается качество поверхности слитков, повышается стойкость футеровки ковша. Чтобы исключить подтекание стали через неплотности меж-ду пробкой и стаканом, эти элементы ковша притирают друг к другу. Предупреждение приваривания пробки к стакану достигается их изготовлением из разных огнеупорных материалов: пробки из графита — стакана из шамота, пробки из шамота — стакана из магнезита. До заполнения сталью ковши тщательно просушивают газовыми горелками. Длительность сушки ковша после смены футеровки зависит от его емкости и составляет 6−8часов.
Заключение
.
Для успешного проведения процесса разливки стали необходимо использование технологического оборудования, в частности сталеразливочных ковшей. Надежность ковшей — непременное условие нормальной работы сталеплавильного цеха.
При постоянном росте производительности сталеплавильных цехов повышается потребность в сталеразливочных ковшах. Для ускорения оборачиваемости ковшей и повышения их стойкости в разливочных пролетах усовершенствуется и создается новая технология подготовки ковшей к принятию металла, главным образом по повышению стойкости футеровки и организации скоростных ремонтов.
В последнее время назначение сталеразливочных ковшей расширилось, что обуславливает дальнейшее совершенствование их конструкций.
1. Металлургия стали. Кудрин В. А. М.: Металлургия, 1981. — 488с.
2. Сосненко М. Н. Мартеновское производство стали. М.: Металлургия, 1969. — 248с.
3. Заверюха Н. В. и др. Разливщик стали. М.: Металлургия, 1974. — 208с.
4. Великин Б. А. и др. Футеровка сталеразливочных ковшей. М.: Металлургия, 1980. — 120с.
5. Пудиков Д. В. и др. Эксплуатация сталеразливочных ковшей с набивной футеровкой. Х.1962. — 63с.
6. Дубров Н. Ф. и др. Разливка стали. М.: Металлургия, 1975. — 200с.