Проект камнеобрабатывающего цеха по производству облицовочных изделий из натурального камня
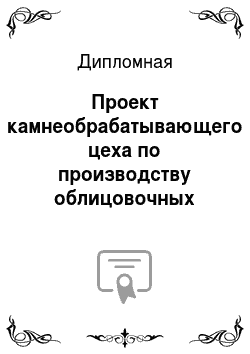
К важнейшей характеристике природного камня, обуславливающей его экологичность и воздействие на живые организмы, является его радиоактивность. При этом радиоактивность может быть как естественной, так и техногенной (возникает в результате радиоактивного облучения различными искусственными источниками излучения). Основными источниками радиации при добыче породы является радиоактивный изотоп… Читать ещё >
Проект камнеобрабатывающего цеха по производству облицовочных изделий из натурального камня (реферат, курсовая, диплом, контрольная)
Аннотация
Дипломная работа: ___ стр., 14 источников, 10 приложений.
Предмет исследования: натуральный облицовочный камень, технологии его обработки и производства облицовочных плит.
В данной работе предложен проект камнеобрабатывающего цеха по производству облицовочных изделий из натурального камня выполнена в соответствии с технологической документацией по проектированию камнеобрабатывающих предприятий. Разработана технологическая схема производства облицовочных плит, выбрано оборудование, соответствующее операционному принципу. В основу принятых конструктивно — компоновочных решений камнеобрабатывающего цеха положен принцип рациональной компоновки оборудования с целью размещения его в минимальном количестве зданий. Приведена смета всех расходов на постройку здания цеха и его последующее функционирование. В проекте учтены нормы техники безопасности и охраны труда.
При соблюдении рекомендаций проекта облицовочные плиты будут соответствовать требованиям мирового уровня.
- 1. Введение
- 1.1 Развитие камнедобывающей и камнеобрабатывающей подотраслей
- 1.2 Конъюнктура мирового рынка декоративного камня
- 1.3 Перспектива развития подотрасли
- 2. Материаловедческая часть: Облицовочные материалы и изделия из них
- 2.1 Основные свойства природного камня
- 2.2 Виды облицовочных материалов
- 2.3 Приемочный контроль плит
- 2.4 Хранение и транспортировка плит
- 2.5 Гранит Санарского месторождения
- 3. Специальная часть: Проектирование камнеобрабатывающего цеха
- 3.1 Обобщенная информация о проектируемом цехе
- 3.2 Определение потребного количества сырья (блоков)
- 3.3 Выбор технологической схемы обработки блоков из гранита
- 3.4 Распиловка блоков на заготовки
- 3.5 Окантовка плит заготовок
- 3.6 Шлифование и калибрование
- 3.7 Полирование плит
- 3.8 Отрезка (окантовка) поперечная
- 3.9 Калибрование и снятие фасок
- 3.10 Линия финишной обработки
- 3.11 Линия отбора
- 3.12 Определение объема отходов камнеобработки
- 3.13 Выбор внутрицехового транспорта
- 3.14 Определение площадей производственных помещений
- 3.15 Выбор системы водоснабжения и гидротранспорта пульпы
- 3.16 Дополнительное производство
- 4. Определение экономических показателей работы камнеобрабатывающих предприятий
- 4.1 Расчет численности рабочего персонала и тарифных ставок
- 4.2 Расчет годового фонда заработной платы
- 4.3 Расчет стоимости производственного здания и административно — бытовых помещений
- 4.4 Расчет стоимости оборудования и амортизационных исчислений
- 4.5 Расчет стоимости электроэнергии
- 4.6 Расчет стоимости воды
- 4.7 Расчет стоимости вспомогательных материалов
- 4.8 Расчет прочих расходов
- 4.9 Смета всех расходов
- 4.10 Расчет основных технико — экономических показателей
- 5. Качество готовой продукции
- 5.1 Контроль технологического процесса и качества готовой продукции
- 5.2 Смазка оборудования
- 6. Эффективность принятых решений
- 6.1 Основные конструктивно-компоновочные решения
- 7. Техника безопасности и охрана труда, охрана предприятия. [8]
- 7.1 Законодательство об охране труда
- 7.2 Нормы, правила и инструкции по охране труда
- 7.3 Общая безопасность производственных процессов
- 7.4 Общие требования безопасности при работе с камнеобрабатываю-щим оборудованием
- 7.5 Действия в аварийных ситуациях
- 7.6 Общие требования безопасности к производственным процессам
- 7.7 Охрана труда и пожарная безопасность на предприятии
- 7.8 Техника безопасности и производственная санитария
- Выводы
- Заключение
- Список использованной литературы
- Приложения
1. Введение
1.1 Развитие камнедобывающей и камнеобрабатывающей подотраслей
Природные облицовочные камни широко используются в разных отраслях народного хозяйства: архитектурной, строительной, технической, художественном камнерезании. Развитие и освоение новых методов добычи и обработки природного облицовочного камня дали возможность значительно расширить области использования камня и уменьшить его стоимость.
Создание промышленных предприятий и объектов культурно-бытового назначения, строительство новых линий метрополитена, увеличение капитального строительства, а также стремление специалистов сделать эти строения долговечными и выразительными требует значительного увеличения объёмов производства облицовочных материалов из природного камня.
1.2 Конъюнктура мирового рынка декоративного камня
Оценочный анализ показывает, что ежегодно в международном торговом обороте находится 20 — 26% общего объёма мирового производства облицовочных материалов и изделий из камня. Лидирующее место здесь, так же как и в уровне производства, принадлежит Италии, объём экспорта — импорта, которой составляет 65% от общего мирового торгового оборота.
Мировой рынок облицовочного камня характеризуется чрезвычайным разнообразием. В тоже время степень насыщенности этого рынка по отдельным регионам неравномерна и обусловлена, прежде всего, уровнем потребления камня в различных странах. В свою очередь, на потребление камня в каждой стране оказывает влияние ряд факторов:
состояние экономики;
национальные и историко-архитектурные традиции;
атхитектурная мода и т. д.
Динамическое развитие за последнее время экономики ряда стран, не обладающих собственной мощной минерально-сырьевой базой облицовочного камня, привело к резко возросшему спросу на этот материал и обусловило появление групп стран — Китай, Индия и др., и даже целых регионов — потребителей камня, определивших характер современного мирового рынка.
Наиболее высока степень насыщенности облицовочным камнем европейского рынка, что объясняется наличием большого числа стран, производящих в широком ассортименте камень на экспорт (Италия, Испания, Греция, Португалия, Финляндия, Швеция и др.). Однако и в Европе сохранились страны со значительным потреблением камня за счёт импорта в перечисленные страны: Германию, Англию, Голландию, Францию и бывшие соцстраны и республики СССР и особенно в Россию. Предметом импорта в перечисленные страны являются готовые изделия и полуфабрикаты.
Наименее насыщен облицовочным камнем американский рынок. Это происходит за счёт традиционно высокого импорта США и относительно низкого уровня собственного производства. Ежегодный объём импорта камня в США, главным образом, в виде облицовочных плит и архитектурно-строительных изделий, составляет 350 — 400 млн. долларов.
За последнее десятилетие значительные перемены произошли в региональной структуре торговли камнем, нарушившие традиционные направления международных рыночных товаропотоков. Так, открылись благоприятные возможности для экспорта облицовочных изделий из камня в страны Ближнего Востока (Кувейт, Саудовскую Аравию, ЮАР и др.). В последнее время весьма перспективный для экспорта рынок формируется в Дальневосточном регионе, где возросшая у ряда стран потребность в камне (Япония, Южная Корея, Тайвань, Сингапур и др.) открывает благоприятные возможности для сбыта облицовочных и архитектурно-строительных изделий. В последнее время резко увеличился спрос на изделия и плиты из гранитов, лабродоритов и приравненных к ним пород.
Главным фактором, предопределяющим спрос на тот или иной вид камня, а также его потребительскую стоимость, является декоративность, то есть совокупность художественно-эстетических свойств его поверхности. При этом основным признаком декоративности, принимаемым в расчёт, является цвет камня. Остальные признаки (рисунок-текстура, структура и др.) учитываются в значительно меньшей степени.
Весомость влияния того или иного цвета на потребительскую стоимость камня в различных странах неоднозначна. Она предопределяется национальными традициями, местной архитектурной модой и другими факторами. [2]
1.3 Перспектива развития подотрасли
В связи с актуальностью вопроса развития камнедобывающей и камнеобрабатывающей подотраслей, проекты цехов по производству облицовочных материалов из натурального камня являются востребованными. В данный момент для российского рынка необходимо расширять выбор видов сырья и номенклатуры изделий. Неограниченные потенциальные возможности, обусловленные огромными территориями способны самостоятельно удовлетворить потребности интенсивно развивающейся строительной индустрии. Поэтому необходимо создание проектов таких цехов, которые способны производить продукцию, удовлетворяющую мировым стандартам качества облицовочных материалов.
натуральный камень облицовочное изделие
2. Материаловедческая часть: Облицовочные материалы и изделия из них
2.1 Основные свойства природного камня
Под основными свойствами камня понимается ряд физико-механических, технологических, эксплуатационных параметров, характеризующих поведение камня под воздействием соответствующих внешних воздействий. Эти свойства относятся к большинству используемых человечеством материалов.
Ниже в таблице № 2.1 даны основные физико-механические и химические свойства природного камня, используемые при его оценке и использовании.
Таблица 2.1.
Основные свойства природного камня
№ п/п | Наименование характеристики | Единица измерения | ГОСТ, СТ СЭВ, организация — разработчик | Европейский стандарт CEA (UNI, Италия) | |
1. | Предел прочности (сопротивление) при сжатии | МПа | ГОСТ 8462–75 ГОСТ 9479–84 | UNI 9724/3 | |
2. | Предел прочности (сопротивление) на изгиб | МПа | ГОСТ 9479–84 | UNI 9724/5 | |
3. | Модуль упругости | МПа | ГОСТ 9479–84 | UNI 9724/8 | |
4. | Плотность (удельный вес) | кг/м3 | ГОСТ 9479–84 ГОСТ 6427–75 | UNI 9724/2 | |
5. | Объемная масса | кг/м3 | ГОСТ 9479–84 ГОСТ 6427–75 | UNI 9724/7 | |
6. | Пористость | % | ГОСТ 9479–84 | UNI 9724/7 | |
7. | Сопротивление удару | М (см) | ; | UNI9724/10 | |
8. | Коэффициент Пуассона (характеризует упругие свойства материала) | ; | ГОСТ 8269–76 | ; | |
9. | Твердость (микротвердость по Моосу) Микротвердость: Алмазной пирамидой По Кноппу По Бринелю НВ ПО Виккерсу НУ По Роквеллу Н | Ед. шкалы Мооса МПа МПа МПа МПа Число Роквелла | ГОСТ 9450–60 — ГОСТ 901 2−59 — ГОСТ 901 3−59 | ; UNI9724/б | |
10. | Коэффициент водопоглощения (впиты вания) | % | ГОСТ 9479–84 | UNI9724/2 | |
11. | Коэффициент снижения прочности на сжатие при пропитке водой | % | ГОСТ 9479–84 | ; | |
12. | Морозостойкость | Циклы (% потери прочности) | ГОСТ 9479–84 | UNI9725 | |
13. | Коэффициент термического расширения | Мм/мС0 | ; | ; | |
14. | Истираемость (сопротивление изнашиванию) | Мм | НИИКС | ; | |
15. | Полируемость | % от эталона | ГОСТ 9480–89 НИИКС | ; | |
16. | Долговечность | Год | ; | ; | |
Существует достаточно много других показателей, характеризующих природный камень, имеющих ограниченное применение при его оценке.
Твердость камня определяется большим количеством методик, некоторые из которых в СНГ не применяются. Наиболее распространенной является шкала Мооса. Твердости различных минералов представлены в Таблица 2.2.
Таблица 2.2.
Истираемость пород характеризует их поверхностный износ (полы, ступени, площадки и др.) при различных механических нагрузках. Классификация различных пород по истираемости представлена в Таблица 2.3.
Полируемость камня (способность получения блеска) зависит в основном от петрографических характеристик камня и измеряются специальным прибором блескомером (блескомер НИИКС-М), где степень полируемости оценивается по сравнению с эталоном (полированный коелгинский мрамор).
Одним из фундаментальных понятий при оценке камня является его долговечность, под которой можно понять сохранение его основных качественных характеристик при использовании в различных условиях.
Поведение камня при различных технологических процессах характеризуется его обрабатываемостью различными методами.
За рубежом принята классификация камня по обрабатываемости с классификацией пород типа гранитов на 5 категорий. При этом не существует определенного показателя, характеризующего породу, и все породы классифицируются из различных соображений:
обрабатываемость ухудшается от 1 класса к 5 с увеличением содержания твердых минералов (кварц, полевой шпат и др.);
обрабатываемость ухудшается от мелкозернистых к крупнозернистым гранитам;
обрабатываемость ухудшается в зависимости от включений и цвета в ряду: черные (габбро — 1 класс) зеленые (2 класс) светлые граниты (3 класс) темные крупнозернистые граниты (4 класс) красные граниты (5 класс) Эти характеристики не являются определяющими и решаются в экспериментальном порядке.
За основу европейской классификации берется коэффициент износа, совпадающий с номером класса. Сравнительный износ алмазного отрезного круга при съеме 300 см2/мин с окружной скоростью 36 м/сек называется коэффициентом износа. Гранит 1 класса имеет коэффициент — 1, а 5 класса — коэффициент 5; то есть износ алмазного круга при обработке гранита 5 класса в 5 раз больше износа при обработке гранита 1 класса По европейской классификации камня по обрабатываемости с увеличением порядкового номера группы камня улучшается обрабатываемость.
Показателями, характеризующими геометрические параметры породы в массиве, и косвенно характеризующими выход готовой продукции при добыче и обработке камня, являются трещиноватость и блочность пород. [5]
Таблица 2.6.
Таблица 2.7.
Абразивность пород оценивается износом различных эталонных материалов при трении о камень. В СНГ наиболее распространена оценка абразивности по Л. И. Барону (износ цилиндрических стальных стержней при трении о необработанную поверхность камня), представленная в Таблица 2.8 [5]
Таблица 2.8.
К важнейшей характеристике природного камня, обуславливающей его экологичность и воздействие на живые организмы, является его радиоактивность. При этом радиоактивность может быть как естественной, так и техногенной (возникает в результате радиоактивного облучения различными искусственными источниками излучения). Основными источниками радиации при добыче породы является радиоактивный изотоп калия — 40К, торий — 232Th и радий — 226Ra, уран [8], содержащие в магматических породах. Высокое содержание радиоактивных включений имеют магматические породы щелочного и кислого состава (граниты, гранодиориты, сиениты, липариты). Наиболее высокой радиоактивностью обладают лейкократовые и аляскитовые граниты, нефелиновые и щелочные сиениты, трахиты, трахилипариты. Меньшей радиоактивностью обладают промежуточные к основным породам породы: андезиты, диориты и др. Наиболее низкой радиоактивностью обладают ультраосновные и основные магматические породы (габбро, диабазы, базальты, перидотиты). Осадочные породы характеризуются более низким содержанием радиоактивных элементов, чем в гранитах и его аналогах. Согласно «Нормам радиационной безопасности «НРБ-88» существуют нормы удельной активности радионуклидов, согласно которым все стройматериалы (породы) делятся на 5 классов. В любом случае все новые породы, используемые в строительстве и быту, должны проходить радиационный контроль, согласно которому должны определяться сферы их применения. Существенным фактором при добыче и эксплуатации каменных материалов является их анизотропия (различие физико-механических свойств в различных направлениях их измерения). Чаще всего анизотропия связана со слоистостью породы, когда свойства породы вдоль и поперек слоистости различаются. Для оценки анизотропии зарубежные стандарты предусматривают измерение основных физико-механических параметров вдоль и поперек слоистости (UNI9724 и др.). Анизотропия используется при добыче и обработке каменного сырья, а также учитывается при облицовке камнем с целью избежать эксплуатационных трещин.
2.2 Виды облицовочных материалов
С увеличением объемов производства изделий из камня, усовершенствованием технологии обработки, дороговизной сырья производство облицовочных плит из природного камня в общем объеме производства изделий из камня неуклонно возрастает. Причем, исходя из дороговизны сырья, повышением требований к качеству облицовки, повышением технологичности облицовки наблюдается непрерывная тенденция уменьшения толщины облицовочных плит, ужесточение допусков на геометрические размеры плит, повышение технологической готовности облицовочных плит, применение стандартных размеров, наличие фасок на лицевой поверхности, наличие закрепительных канавок или прорезей на тыльной стороне плит и др.
В зависимости от исходного материала, плиты подразделяются на следующие виды: плиты облицовочные из природного камня и плиты декоративные на основе природного камня с использованием различных связующих.
На территории СНГ действует ГОСТ 9480–89 на плиты облицовочные из природного камня. Согласно этому ГОСТу допускается изготовление плит следующих размеров, мм:
длиной 150−1500;
шириной150−1200 или полосок и шашек менее 150 мм;
толщиной8−30 мм, или 40 мм из мраморизованного известняка, туфа, ракушечника, известняка.
Предельные отклонения от номинальных размеров пиленых изделий не должны превышать:
по длине и ширине для размеров:
до 600 мм ±1 мм;
свыше 600 мм ±2мм;
по толщине:
для размеров: свыше 30 до 50 мм из мрамора ±2 мм;
из других горных пород ±3 мм;
для размеров свыше 50 мм всех видов пород ±3 мм.
Предельные отклонения от номинальных размеров колотых изделий зависят от вида фактуры и ие должны превышать:
по длине и ширине:
для полированной, гладкой матовой и шлифованной фактур… ±3 мм;
для термообработанной, точечной, «скала» и других фактур… ±5 мм;
по толщине:
для полированной, гладкой матовой и шлифованной фактур… ±3 мм;
для термообработанной, точечной, «скала» и других фактур… ±10 мм.
Изделия изготавливаются прямоугольной и квадратной формы, но по согласованию с потребителем можно изготавливать криволинейные изделия по заданной спецификации, а также изделия с фаской шириной до 5 мм, крепежными отверстиями или пазами.
Кроме того, стандарт нормирует и другие показатели внешнего вида. Так, отклонение от прямого угла пиленых изделий не должно превышать +1 мм на 1 м длины граней, а для колотых изделий этот показатель зависит от фактуры лицевой поверхности и не должен превышать:
для полированной, гладкой, матовой и шлифованной фактур… +2 мм;
для термообработанной, точечной, «скала» и других фактур… ±3 мм.
Отклонения от прямого угла облицовочных плит на 1 м длины не более +1 мм.
Пиленые изделия с полированной и гладкой матовой фактурой в зависимости от качества лицевой поверхности подразделяют на два класса. Пиленые изделия 1-го класса не должны иметь на лицевой поверхности видимых повреждений.
Пиленые изделия 2-го класса могут иметь следующие повреждения:
углов длиной по ребру не более 5 мм не более 2 шт.;
сколы ребер по периметру изделий длиной не более 15 мм… не более 3 шт.
На лицевой поверхности колотых изделий допускаются повреждения углов длиной по ребрам более 15 мм — не более 2 шт., сколы ребер по периметру изделий не более 15 мм — не более 3 шт.
Отклонение от плоскостности на 1 м длины по периметру и диагоналям не должно превышать: — для пиленых изделий с полированной и гладкой матовой фактурой 1-го класса +1 мм, 2-го класса ±2 мм, шлифованной ±3 мм, остальных видов +5 мм; для колотых изделий с полированной, гладкой матовой и шлифованной фактурой ±3 мм, термообработанной, точечной, «скала» и других фактур ±5 мм.
В последнее время в связи с повышением точности обработки, автоматизаций производственных процессов за рубежом широкое распространение получил новый вид продукции из природного камня — стандартные облицовочные плиты с одинаковыми линейными размерами всей партии облицовочных изделий, высокой технологической готовности (наличие фасок на всех гранях лицевой поверхности специальные элементы на задней крепежной поверхности и др.), минимизированными допусками линейных и угловых размеров — «модульные плиты». Условно такие плиты можно разделить на два типа: плиты нормальных размеров, плиты малых размеров типа «кафель» .
Наиболее характерные размеры (мм) стандартных «модульных плит» следующие: 305×305×10; 457,5×457,5×12; 610×610×12 — для внутренней облицовки; 300×600×17; 400×800×17 и 600×1200×20 — для полов; 400×800х (20−30); 600×1200х (20−30) — для наружной облицовки гранитом.
Существующий союзный ГОСТ, как видно из вышеизложенного, устарел и требует доработки. Дефицитность и дороговизна декоративного каменного сырья является предпосылкой развития разнообразных технологических процессов с использованием отходов и некондиционных продуктов добычи и обработки камня в производстве облицовочных плит и изделий. Плиты типа «кафель» выпускаются обычно толщиной 3−8 мм и размерами в плане (ММ): 100×100; 150×150; 150×305 и др.
Учитывая высокие декоративные свойства природного камня и его высокую стоимость, широкое распространение за рубежом получили облицовочные декоративные плиты с мозаичной, брекчиевидной и орнаментной поверхностью, изготовляемые с использованием природного камня (отходы, щебень, бут и др.) и различных неорганических (цемент и др.) и органических (смолы, клеи) связующих. Эти плиты используются как в наружной так и внутренней облицовке зданий и сооружений. В странах СНГ эти плиты получили меньшее распространение, но их объемы производства и использования в силу ряда объективных причин должны в ближайшие годы возрасти. [2]
2.3 Приемочный контроль плит
Соответствие перечисленным требованиям определяют при приемочном контроле плит, который включает определение геометрических размеров и формы, фактуры и качества лицевой поверхности. Для этого от партии плит, изготовленных из одной горной породы и одной фактуры лицевой поверхности, отбирают выборку, объем которой от 5 до 125 шт. в зависимости от объема партии. Приемку осуществляют по одноступенчатому плану. Проверяемая плита считается дефектной, если она не удовлетворяет одному из перечисленных требований. Партия принимается, если число дефектных изделий в выборке меньше или равно приемочному числу.
Плиты из партии, не принятой в результате выборочного контроля, следует принимать поштучно. При этом, как правило, контролируют соответствие плит тем требованиям, по которым партия не была принята.
Каждая партия плит сопровождается документом о качестве, в котором указывают наименование и адрес предприятия-изготовителя, номер и дату составления документа, дату отгрузки, номер партии, число плит в партии и их размеры, породу камня, наименование месторождения, фактуру лицевой поверхности плит и физико-механические свойства породы блоков, нормируемые по ГОСТ 9479.
Плиты упаковывают в ящики или ящичные поддоны в вертикальном положении не более двух рядов по высоте лицевыми поверхностями друг к другу. Допускается упаковка плит из прочных горных пород в пакеты. Между лицевыми поверхностями полированных плит укладывают деревянные или бумажные прокладки. [3]
2.4 Хранение и транспортировка плит
Плиты транспортируют любыми видами транспорта в соответствии с принятыми правилами. При погрузке, выгрузке и транспортировании плит должны быть приняты меры, исключающие их загрязнение и повреждение.
Плиты хранят на предприятии-изготовителе и у потребителя под навесом или на открытых спланированных площадках, обеспечивающих отвод воды и предохранение плиты от загрязнения и повреждения. При хранении на складах без тары плиты должны быть установлены на деревянных прокладках в вертикальном положении лицевыми поверхностями друг к другу. Между лицевыми поверхностями полированных плит следует укладывать бумажные или деревянные прокладки.
Плиты из пород с низкой морозостойкостью следует хранить в условиях, предохраняющих их от резкого перепада температур и атмосферных осадков. [3]
2.5 Гранит Санарского месторождения
В качестве материала используются санарский гранит. По физико-механическим свойствам гранит Нижне-Санарского месторождения соответствует ГОСТ 9479–98 «Блоки горных пород для производства облицовочных, архитектурно-строительных, мемориальных и других изделий» .
Наименование характеристики | Численное значение | |
Средняя плотность | 2,74 г/см. куб. | |
Водопоглощение | 0,32% | |
Предел прочности при сжатии породы в сухом состоянии | 800−1600 кг/см. кв. | |
Морозостойкость | 50 цикл | |
Пористость | 1.26% | |
Истираемость | 9.1/И I | |
Радиационная безопасность гранита Нижне-Санарского месторождения. Согласно проведённых испытаний по оценке радиационной чистоты строительных материалов гранит Нижне-Санарского месторождения имеет удельную эффективную активность естественных радионуклидов в пределах 93−141 Бк/кг, что соответствует I классу горных пород. По ГОСТ 30 108–94 граниты Нижне-Санарского месторождения Могут использоваться без ограничения для внутренней и наружной отделки помещений, дорожного, гражданского и промышленного строительства, благоустройства и создания мемориальных комплексов.
Внешний вид Нижне-Санарского гранита.
Гранит Нижне-Санарского месторождения один из самых благородных в России. Порода имеет красивую, массивную текстуру светло-серого цвета. Местами наблюдаются включения тёмно-серых мелкозернистых габбро в виде изометрических и слабо уплощенных пятен мощностью до 10−15 см, количество их менее 10%.
Оценка декоративности гранита Нижне-Санарского месторождения.
В соответствии с методикой экспертных оценок Нижне-Санарский гранит имеет оценку в баллах — 27,5. Относится ко II классу декоративных горных пород.
3. Специальная часть: Проектирование камнеобрабатывающего цеха
3.1 Обобщенная информация о проектируемом цехе
Проектируемый камнеобрабатывающий цех состоит из следующих зданий и сооружений:
1. Главный корпус с производственным участком, административно-бытовыми помещениями.
2. Шламоотстойник с насосной станцией.
3. Склад заготовок — блоков.
4. Сети водоснабжения, канализации, освещение, внешнее энергоснабжение.
В состав цеха входит склад блоков, открытая площадка размером 78×32 м и обслуживаемая двумя погрузчиками Toyota грузоподъемностью 3 тонны с высотой подъема вил 2,5 м.
Площадь складирования 2485 м2. В зоне действия крана имеется автомобильная дорога. Транспортировка блоков со склада сырья в отделение распиловки производится на рельсовых тележках.
В главном корпусе цеха сблокированы следующие отделения:
цеховые производственные помещения;
административные помещения;
склад инструментов;
бытовые помещения;
площадка упаковки и складирования готовых изделий.
В составе отделений имеются и площадки промежуточного складирования, сбора окола.
Кроме того, в корпусе сблокированы соответствующие объекты:
пульпонасосная станция с отстойными ямами;
железнодорожная ветка.
Транспортные потребности цеха обслуживаются двумя мостовыми и одним козловым краном — 3 тонны.
Готовая продукция может отгружаться на автомобильный транспорт.
Образующийся шлам после обработки по специальным лоткам подается с водой в пульнонасосную станцию, расположенную в главном корпусе. Шлам по пультопроводам подается в шламоотстойник, где происходит осветление воды, которая насосами подается к станкам, таким образом промышленное водоснабжение работает в замкнутом цикле на водообороте.
Очистка шламоотстойника производится один раз в месяц специальным шламовым насосом, после откачки осветленной воды из последней секции. Шлам может быть использован как заполнитель асфальтобетона, в дорожном строительстве, засыпке территории при строительстве.
На пульпонасосной применяются серийно выпускаемые землесосы типа ГРАТ, выпускаемые Бобруйским машзаводом.
Для обслуживания рабочих в цеху предусмотрен бытовой отсек с душевыми сетками и туалетом.
В цеху мастером цеха осуществляется контроль технологического процесса и качества готовой продукции.
Мастер должен иметь оснастку и инструмент для осуществления приемочного контроля на. рабочей площадке следующих изделий:
плиты облицовочные из природного камня по ГОСТ 9480–89;
блоки из природного камня для производства облицовочных плит по ГОСТ 9479–84;
Геометрические размеры и качество лицевой поверхности изделий оценивают измерительными инструментами, а фактуру лицевой поверхности — визуально.
Проверяется качество рабочего инструмента на каждой из операций, а также пооперационный контроль качества промежуточных продуктов.
В разделе «Безопасность жизнедеятельности» проекта представлен раздел техники безопасности работы камнеобрабатывающего производства в соответствии с требованиями ГОСТ 12.3.002.75 «Процессы производственные. Общие требования безопасности, а также все требования действующих нормативов и правил по технике безопасности». Выполнение указанных требований при работе технологического оборудования позволяет обеспечить безопасность обслуживающего персонала.
В разделе генерального плана и транспорта выполнены работы по размещению камнеобрабатывающего цеха. Запроектированы грунтовая дорога и площадки. Выполнен чертеж по привязке и разбивке здания и сооружении на площадке.
Площадь застройки — 6708 м2. Площадь открытого склада — 2485 м2
Рассчитан годовой грузооборот цеха по сырью и готовой продукции на автомобильный транспорт (см. разделы генплана и транспорта).
В разделе энергоснабжения и автоматики выполнены работы по энергоснабжению проектируемого цеха и автоматизации технологических процессов.
Проектом также принято питание электроэнергией насосной станции на шламоотстойнике, наружное освещение площадок и склада блоков.
Здания отапливаемые. Расчетная зимняя температура для Московской области — 25 °C. Нормальный вес снегового покрова равен 100 кгс / м2.
Строительная часть цеха представлена главным корпусом 172×39 м, внутренним шламоотстойником и погрузочной площадкой с крановыми путями.
Шламоотстойник 5×3×2 м в монолитном исполнении.
Схема тепловых сетей принята двухтрубная, закрытая. Присоединение систем отопления и вентиляции непосредственное. Присоединение системы отопления непосредственно к существующей теплотрассе или автономная система по усмотрению заказчика.
Вентиляция принята общеобменная приточно-вытяжная c механическим побуждением.
В разделе водоснабжения и канализации решены вопросы питьевого и производственного водоснабжения, системы канализации корпуса.
Сеть бытовой канализации выполнена для отвода стоков от санитарно-технического оборудования зданий и сооружений. Расход стоков равен 0,2 м3/час; 0,06 л/сек.
Сеть производственной канализации выполнена для отвода стоков от технологического оборудования завода и смыва полов.
Для этой цели в главном корпусе выполнены бетонные лотки, по которым от оборудования самотеком поступает вода со шламом в зумпфы (2 шт) и далее в шламоотстойник. В шламоотстойниках вода отстаивается и (осветленная) и насосами марки 1Д-25−50, Q=25 м3/час, Н = 15 м. в. ст. подается в корпуса к оборудованию по распиловке и шлифовке мрамора.
Насосная станция принята на 2 насоса: I рабочий и I резервный.
Учитывая, что процесс обработки камня выполняется в замкнутом цикле с водой (мокрый процесс), то выбросов в атмосферу и окружающую среду от производственного корпуса не существует.
3.2 Определение потребного количества сырья (блоков)
Таблица 1
Исходные данные для проектирования камнеобрабатывающего предприятия
Наимено-вание породы | Месторо-ждение | Физико-механические свойства | Исходное сырье | Годовая произво-дительность цеха по готовой продукции, м2/год | ||
Прочность на сжатие, МПа | Объемная масса, кг/м3 | Блоки категории | ||||
Гранит | Санарский | Блоки II категории | 300 000 | |||
размеры блоков 2,5×1,6×1,8 м3 (длина-высота-ширина) (объем блоков 7,2 куб. м., вес — 20 тонн) Размеры плит:
длина — 400 мм;
ширина — 300 мм толщина — 30 мм Потребное количество блоков:
Vn = S0/ Wn, м3/год где S0 - годовая производительность цеха по гранитным плитам, м2/год;
Wn — выход готовых плит из 1 м3 блоков, м2/м3;
Wn= 1000*kвых/ (bn + bин +bз), м2/м3
где kвых = 0,7 — коэффициент выхода, зависит от физико-технических свойств горной породы (для твердых пород 0,8 — 0,65), bn = 30 мм — толщина плиты; bин = 7,5 мм — толщина режущего инструмента; bз = 2 мм — суммарная величина зазоров в пропиле;
Wn= 1000*0,7/ (30 + 7,5 +2) = 17 м2/м3,
Потребный объем блоков:
Vn = 300 000/ 17 = 17 647 м3/год;
Согласно исходным данным объем одного блока:
Vбл. = 2,5*1,6*1,8 =7,2 м3
Количество блоков: nn = Vn /Vбл = 17 647/7,2 = 2451 блок.
3.3 Выбор технологической схемы обработки блоков из гранита
При выборе оптимальной технологической схемы нужно руководствоваться следующим:
а) выход готовой продукции должен быть максимальным;
б) количество операций должно быть минимально возможным;
в) максимальное использование современного оборудования
г) стоимость, габариты и вес применяемых технических средств должны быть минимальные, а производительность — максимальная;
д) удельный расход применяемого алмазного инструмента должен быть минимальным.
Для переработки блоков II категории Санарского месторождения гранита принимаем следующую схему:
3.4 Распиловка блоков на заготовки
Согласно выбранной технологической схеме обработки изделия в качестве основного распиловочного оборудования для первого технологического процесса принимаем итальянский станок типа GTG 1600/50/CNC GASPARI MENOTTI.
Станок разработан для распиловки гранитных блоков на заготовки при помощи пакета вертикальных дисков и одного горизонтального диска.
Станок имеет две вертикальные колонны, соединенные между собой посредством прочной опорной балки для укрепления структуры. Главный мост передвигается вдоль по колоннам. Специальное крепление моста к колоннам гарантирует точность распиловки. Блок помещается на тележку, которая передвигается по специальным рельсам. И распиловка, и движение тележки с блоком программируются и контролируются специальной программой контроля PLC.
Основные характеристики:
Вертикальные диски подаются вперед для осуществления распиловки, в то время как подача материала осуществляется за счет передвижения тележки с блоком.
Основная структура состоит из двух устойчивых колонн, имеющих стальные направляющие с ползунами из бронзы, что обеспечивает плавность движения. Система абсолютная герметична.
Мост, несущий шпиндели, в увеличенном размере для достижения максимальной стабильности.
Мост имеет направляющие, по которым передвигается каретка с группой шпинделей.
Каретка с группой шпинделей обладает повышенной устойчивостью. Специальная структура увеличивает устойчивость к рабочей нагрузке и предотвращает вибрации шпинделя.
Тележка с блоком приводится в движение двойным мотор-редуктором. Точность движения достигается посредством специального энкодера.
Колеса имеют двойную секцию скольжения, одну для распиловки, другую для перемещения платформы.
Движения по всем трем осям контролируются инвертером и энкодером.
Все подшипниковые соединения и прочие компоненты разработаны определенным образом, что обеспечивает длительные интервалы между техническими контролями, что, в свою очередь, сокращает простой станка.
Все движения и процесс распиловки контролируются специальной программой контроля PLC.
Имеется возможность установить диски для пошаговой распиловки «лесенкой» для реза до 600 мм.
Диаметр дисков до 1600 мм
Распиловочный станок имеет независимую станцию горизонтально реза, предназначенную для распиловки заготовок, нарезанных вертикальной станцией.
Станок имеет моторизированную тележку для подачи блоков, 3500×4500 мм.
Технические характеристики
Рабочие габариты | ||
Ширина Длина Высота | 460 см 350 см 210 см | |
Общие габариты | ||
Ширина Длина Высота | 860 см 1200 см 570 см | |
Мин. диаметр верт. дисков Макс. диаметр верт. дисков Диаметр гориз. дисков Макс. кол-во верт. дисков | 900 мм 1600 мм 350/400 мм | |
Макс. толщина пакета верт. дисков Мощность шпинделя верт. дисков Мощность шпинделя горизонт. диска | 925 мм 200 кВ 15 кВ | |
Вертикальная станция: | ||
Мощность верт. движения моста (Z ось) Мощность каретки с верт. дисками (Y ось) Мощность тележки с блоком (X ось) Скорость каретки с дисками Скорость моста Скорость тележки с блоком | 4 кВ 4 кВ 1.1 кВ 0−1900 см/мин 0−25 см/мин 0−250 см/мин | |
Горизонтальная станция: | ||
Мощность верт. движения моста (Z1 ось) Мощность каретки с гориз. диском (Y1 ось) Мощность гориз. диска (X1 ось) Скорость каретки с гориз. диском Скорость моста Расход воды Общая установленная мощность Общий вес станка | 1.5 кВ 0.55 кВ 0.37 кВ 0−1400 см/мин 0−25 см/мин 1130 л/мин 230 кВ 46,000 кг | |
В качестве режущего инструмента выбираем АОК 1600 по граниту для многодисковых станков.
Скорость резания — 25 м/с (рекомендуемая скорость резания при распиловке алмазными отрезными кругами для гранитов) Ширина пропила bп = bин + bз,
где bин = 7,5 мм — толщина режущего инструмента;
bз = 2 мм — суммарная величина зазоров в пропиле;
bп = 7,5 + 2 = 9,5 мм.
Количество дисков, необходимое для распиловки блоков на плиты.
m=B/ (bп +bпл) — 1, шт.
где В=1800 мм — ширина блока; bпл = 30 мм — толщина плиты,
m=1800/ (9,5 + 30) — 1= 45 шт.,
Теоретически возможное количество готовой продукции после операции распиловки за год:
ST = 1000 (m+1) *Vn / B, м2
Где Vn — потребный объем блоков м3;
В=1800 мм — ширина блока.
ST = 1000 (45+1) * 17 647/ 1800 = 450 979 м2
Реальное количество готовой продукции после распиловки:
S1 = ST * kp, м2
где kp = 0,9 — коэффициент выхода продукции после операции распиловки
S1 = 450 979* 0,9 = 405 588 м2
Технологическая производительность:
Qтех = H0*S (m+1) *Kдоп/1000, м2/ч Где S — рабочая подача, м/ч
m — число одновременно работающих инструментов;
Кдоп — коэффициент, учитывающий уменьшение производительности за счет врезания инструмента, его перебега или недопила;
Кдоп=Н0/ (Н0+Y1+Д1)
где Н0 — высота распиливаемого блока Н0= 1600 мм; S= 1 м/ч
Y1=30 мм — величина врезания инструмента;
Д1= - 30 мм — недопил блока, предупреждающий его развал;
Кдоп=1600/ (1600+30−30) = 1
Qтех=1600*1* (45+1) *1/1000= 73,6 м2/ч Цикловая производительность станка:
Qц=Qтех*Кц
где Кц — коэффициент цикловой производительности; Кц=0,98
Qц=73,6*0,98=72 м2/ч Фактическая производительность станка:
Qф=Qц*Кф
где Кф — коэффициент использования номинального фонда рабочего времени, при работе в три смены Кф=0,85
Qф=72*0,85=61,3
Время распиловки одного блока:
Ттех = L0/1*1000 = 2500/ 1*1000 = 2,5 часов Расчетное количество станков:
N1 = ST/ F*Qф, шт, где F = 6075 ч — годовой фонд рабочего времени при работе в три смены.
N1 = 450 979/ 6075*61,3= 1,2 шт.
Принимается N1=2 шт.
Учитывая, что удельный расход алмазов равен: q=0,1 карат/м2, суммарный расход алмазов qc=q*ST=0,1*450 979 =45 097,8 карат.
Расход воды при работе станка:
Иc = m *И м3/ч, И = 0,18 м3/ч (на 100 мм диаметра отрезного круга), для диаметра 1600 мм И=2,88
Ис= 45*2,88= 129,6 м3/ч.
3.5 Окантовка плит заготовок
Вторым технологическим процессом в выбранной схеме является окантовка продольная. В результате процесса окантовки из плит — заготовок получают плиты шириной 300 мм, длиной 2500 мм. Окантовка осуществляется с помощью различных типов окантовочных станков.
Для окантовки плит заданного размера принимаем поперечно — окантовочный станок типа TMG600G/01/SB GASPARI MENOTTI
Основные характеристики:
Структура из электросварной стали.
Рабочая поверхность с роликами фрикционного сцепления, диаметр 60 мм, оцинкованные, с ходом 250 мм, линейка для заготовок и угольник.
Каретка с дисками, передвигающаяся по направляющим, имеет мотор-редуктор с инвентором.
4 пневматических пресса для выравнивания заготовок.
Набор створок с заданными размерами (300−305, 400−405, 450, 610)
Фиксированная скорость рольганга.
Полуавтоматический рабочий цикл (кнопка запуска возвратно поступательного движения роликов, автоматический цикл возвратно — поступательной распиловки, кнопки запуска дисков и прессов).
Технические характеристики
Длина станка Ширина станка Высота станка Рабочая ширина Диаметр диска с алмазным покрытием Mакс. толщина распиловки Длина станины Мощность диска Мощность поперечного диска Мощность рольганга Общая установленная мощность | 4500 мм 1700 мм 2170 мм 650 мм 350 мм 30 мм 4500 мм 7.5 kW 1.1 kW 0.75 kW 9.5 kW | |
В качестве связки алмазного слоя принимается связка М5 — 02 (М50) и синтетические алмазы АС 32 зернистостью 500/400.
Удельный расход алмазов q = 1,2 карат/ м2
Скорость резания для этих станков:
V = р* D * n / 60*1000, м/с, где D = 350 мм, диаметр отрезного диска;
n = 1400 об/мин, частота вращения круга;
V = 3,14* 350 * 1400/60*1000 = 25 м/с.
Такая скорость соответствует рекомендациям при распиловке алмазными кругами (для гранитов рекомендуемая скорость резания при распиловке алмазными отрезными кругами — 20−25 м/с) Рабочая подача принимается S = 1,5 м/мин.
Размеры плит, получаемых при продольной окантовке:
L0 = 2500 мм и b = 300 мм Длина рабочего прохода инструмента:
L = L0 + Y + ?, мм, где? — величина перебега инструмента,? = 20 мм;
L0 — длина распиливаемой плиты заготовки, мм;
Y — величина врезания, мм;
Y=v (350/2) 2— (350/2−30) 2=93 мм,
L = 2500+ 93 + 20 = 2613 мм, Технологическая производительность станка определяется по зависимости:
Qтех =60*bпл * S*m* kдоп / 1000, м2/ч, Для продольной окантовки: bпл=30 мм, S=1,5 м/мин, m=1
Кдоп=L0/L=2500/2613=0,96,Qтех = 60*30*1,5*1*0,96/1000=2,6 м2/час. (примерно 240 плит в смену)
Фактическая производительность станка определяется согласно зависимости с учетом рекомендаций раздела 4 (при работе в три смены Ку=0,98, а Кф=0,9):
Qф=Qтех*Ку*Кф
Qф=2,6*0,98*0,9=2,3 м2/ч.
Суммарная поверхность плит-заготовок для окантовки:
S1 = 405 588 м2
Суммарная поверхность плит-заготовок, получаемых после окантовки при Kк = 0,95 (для твердых пород):
S2 = S1* Kк = 405 588 * 0,95 = 385 308,6 м2
Количество плит-заготовок, идущих на окантовку, определяется по зависимости:
Z = S1/H0 *L0. При H0 = 1,6 м, L0 = 2,5 м
Z = 405 588/1,6*2,5 = 101 397 плит Суммарная площадь резов, необходимая для осуществления продольной окантовки плит:
Sc1 = Z * m * bn * L0 =101 397 * 1 * 0,03 * 2,5 = 7604,8 м2.
Учитывая, что на камнеобрабатывающих предприятиях распиловочное оборудование обычно работает в 3 смены, а остальные виды оборудования в 2 смены, принимается годовой фонд рабочего времени окантовочного оборудования: F = 4050 часов.
Число поперечно окантовочных станков:
N = Sc / Qф* F
N = 7604,8 /2,3*4050=0,8 станка.
Принимаем N = 1 станку.
Суммарный расход алмазов на операцию продольной окантовки за год qc=q*Sc=0,1*2932=293,2 карат.
Расход воды при продольной окантовке определяется:
И = D*m/50, л/мин, И= 350*1/ 50 = 7 л/мин = 0,007 м3/ мин.
3.6 Шлифование и калибрование
Для операции шлифования и калибрования принимаем автоматический калибровочный станок для заготовок из гранита CTM600/03 Gaspari Menotti.
Станок предназначен для калибровки заготовок из гранита. Калибровка осуществляется за счет алмазных калибрующих дисков, установленных на независимых шпинделях. Вращение шпинделя независимое от вращения калибрующих кругов и может варьироваться в зависимости от требований оператора. Каждая из головок имеет 8 калибрующих кругов, диаметром 200 мм. Вертикальное движение контролируется энкодером. Высота отображается на экране, размещенном на борту станка.
Автоматическое устройство, считывающее толщину заготовки и сигнализирующее, если толщина превышает заданную.
Материал перемещается по ленте конвейера, натянутой вдоль монолитной станины из высокопрочной стали. Станина покрыта специальными стальными пластинами, гарантирующими оптимальную плоскостность. Лента конвейера приводится в движение моторизированным роликом с мотор редуктором и инвертером.
Заготовка удерживается в рабочем положение за счет специальной направляющей из стали и в окончательной стадии очищается от остатков обработки путем мытья.
Технические характеристики
Длина станка Ширина станка Высота станка | 564 см 230 см 320 см | |
Макс. рабочая ширина Макс. рабочая высота | 65 см 7 см | |
Диаметр калибр. круга Мощность шпинделя Мощность мотора, отвеч. за вращение шпиндельной группы Мощность мотора, отвеч. за верт. движение шпинделя Мощность ленты конвейера Общая установленная мощность | 20 cм 24 кВ 3 кВ 0.75/0.15 кВ 2.2 кВ 85.5 кВ | |
Основные технические характеристики инструмента и показатели режима обработки можно представить в табличной форме. В качестве шлифовального инструмента принимаются шлифовальные круги (таблица 1.3 приложения) 2733 — 0007 [11, 4].
Характеристика выбранного инструмента
Наименование операции | Зернистость алмаза | Тип связки | Марка алмаза | |
Обдирка (калибровка) | 630/500 | М6−10 | А5 или А8 | |
Выбранные показатели режима обработки
Наименование операции | Скорость вращения инструмента | Рабочая подача, м/мин | Давление инструмента на плиту, МПа | ||
продольная | поперечная | ||||
Обдирка (калибровка) | 20−24 | 1,5−2 | ; | 0,08−0,1 | |
Техническая производительность определяется согласно зависимости:
Qtex= 60 * bпл * S * Kдоп / 1000, м2 /ч, где bпл = 300 мм — ширина плиты;
S = 4 м/мин — рабочая подача конвейера станка;
Kдоп=0,9 — коэффициент. учитывающий уменьшение производительности за счет зазора между плитами;
Qtex= 60 * 300* 4* 0,9/ 1000 = 64,8 м2 /ч Фактическая производительность определяется по зависимостям, с учетом рекомендаций раздела 4 (при работе в одну смену конвейерных станков Kу = 0,98, а Kф = 0,9)
Qф = Qtex * Kу * Kф = 64,8 * 0,98 * 0,9 = 57,2 м2 /ч, Количество необходимых станков определим согласно зависимости:
N = S2/Qф *F = 385 308,6/57,2 * 4050 = 0,9 станка Принимаем N = 1 станку.
Расход алмазов на операции шлифования при q=0,2 карат/м2
qc=q*S2=0,2*385 308,6 =77 061,7 карат Расход воды для 1 конвейера при числе шлифовальных головок на конвейере 8 и расход воды на одну шлифовальную головку 2,4 м3 /ч (для калибровочных станков) равен:
И = N * 5* 2, 4 = 10,8 м3 /ч.
3.7 Полирование плит
Для операции полирования плит используем станок PGM600/14 GASPARI MENOTTI.
Станок имеет станину из электросварной стали. Поверхность станины заземлена и идеально отшлифована, стальные заменяемые пластины для абсолютной плоскостности. Вдоль станины натянута специальная лента конвейера с прочной структурой во избежание протяжки. Движение ленты конвейера осуществляется за счет мотор-редуктора, скорость регулируется инвертором и отображается с максимальной точностью на энкодере, прикрепленном к холостому ролику. Мост со шпинделями, выполнен из электросварной стали. Для достижения макс. стабильности шпиндели расположены по центру. Шпиндели имеют хромированные державки для вертикального движения полирующих головок. Мост посредством шарнирных соединений передвигается по роликам, ролики отшлифованы и находятся в масленой ванне. Движение моста осуществляется за счет группы мотор-редукторов, скорость которых регулируется инвертором. Для плавности движения шестерни и зубчатые рейки имеют наклонные зубья и прочную структуру для долговечности. Вертикальное движение полирующих головок и рабочее давление обеспечивают специальные пневматические цилиндры, которые гарантируют синхронное поступательное движение плит под полирующими головками. Полирующие головки разделены между собой специальной металлической диафрагмой с резиновой полоской, которая предотвращает попадание абразива с соседних полирующих головок на обрабатываемую поверхность. Станок имеет стальные створки для замены полирующих поверхностей для каждой из головок. Полировальный станок снабжен центральной автоматической системой смазки.
Таким образом, станок имеет:
1 монолитную структуру из стали с отшлифованной поверхностью со стальными заменяемыми накладками.
1 конвейерную ленту с ускорением от 0 до 600 см/мин.
14 шпинделей для полировки с головками GASPARI, имеющие полирующие диски с мотором 11 кВ, диаметр головок 450 мм.
Движение вверх/вниз и рабочее давление осуществляются посредством специального пневматического цилиндра.
Каждая полирующая головка имеет регулятор пневматического давления.
Скорость моста регулируется на контрольном пульте, находящемся на расстоянии, напротив самого станка.
Все кнопки контроля, в том числе за давлением, находятся на герметичной части панели управления для повышения удобства и максимальной надежности.
Каждая из головок имеет отдельный щиток. Таким образом, возможно прервать работу определенной головок, где требуется замена абразива.
Каждая головка имеет прочную перегородку, позволяющую оператору после того как движение головки остановлено, провести замену абразива в соответствии с нормами безопасности.