Проектирование станочного приспособления
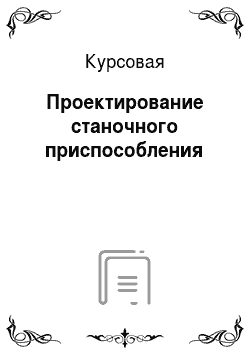
Из-за применения специального приспособления для установки данной детали на горизонтально-фрезерной операции достаточно эффективно в условиях серийного производства так как затраты на его проектирование и изготовление распределяются на все детали в партии. Конструкция данного приспособления позволяет уменьшить вспомогательное время на установку детали т.к. при установке не требуется выверка… Читать ещё >
Проектирование станочного приспособления (реферат, курсовая, диплом, контрольная)
КУРСОВОЙ ПРОЕКТ По предмету: Технологическая оснастка Тема: Проектирование станочного приспособления
РЕФЕРАТ
Курсовой проект: пояснительная записка 18 с., 5 рисунков, 1 таблица, 4 источника.
Исходные данные: чертеж детали, годовая программа выпуска.
Цель проекта: произвести технологическую подготовку производства валика с учетом серийности производства и требованиями достижения качества детали при минимальной себестоимости.
В курсовом проекте был выполнен анализ технологичности, разработан технологический процесс обработки валика. Для обработки заготовки на горизонтально-фрезерной операции было спроектировано специальное зажимное приспособление.
После выбора модели приспособления были произведены проверочные расчеты наиболее нагруженных ее частей.
Разработанно: чертеж детали, сборочный чертеж приспособления, карта наладки, маршрутный технологический процесс.
ТЕХНОЛОГИЧЕСКАЯ ОСНАСТКА, СХЕМА БАЗИРОВАНИЯ, КАРТА НАЛАДКИ, ПРИСПОСОБЛЕНИЕ, ВАЛИК, ФРЕЗА, ЗАГОТОВКА
1. Технологическая часть
1.1 Анализ технологичности конструкции детали
1.2 Выбор метода получения заготовки
1.3 Разработка маршрутного технологического процесса
1.4 Проектирование операции
2. Конструкторская часть
2.1 Разработка схемы базирования и расчётной схемы
2.2 Расчёт усилия закрепления
2.3 Расчёт усилия на приводе и параметров привода
2.4 Расчёт элементов приспособления на прочность
2.5 Расчёт погрешности установки заготовки в приспособлении
2.6 Описание конструкции и принципа работы приспособления Выводы
Перечень ссылок
приспособление погрешность заготовка деталь валик
В данный момент времени машиностроение находится на стадии развития и модернизации. Требования к качеству производимых изделий повышается, а сроки производства значительно сокращаются, в связи с этим возникает необходимость совершенствовать технологию производства. Одним из способов сокращать время производства и улучшать качество изделий является применение различных станочных приспособлений. Приспособления значительно сокращают вспомогательное время операции. Существует множество видов, моделей и исполнений приспособлений. Они могут быть как ручными, так и механизированными, рассчитанных на несколько заготовок и на одну и т. д.
Однако изготовление и применение станочных приспособлений рентабельно лишь в случаях серийного и массового производства.
В данном курсовом проекте стоит задача спроектировать станочное приспособление для обработки лысок в условия серийного производства. Конструкция приспособления должна отвечать многим требованиям, таким как удобство использования, эргономичность, безопасность, быстродействие, требовать минимальные затраты на его изготовление и ремонт и т. д.
1. Технологическая часть
1.1 Анализ технологичности конструкции детали
Данная деталь относится к классу валов и изготовлена из конструкционной стали 45, химический состав которой следующий: С — 0,42 — 0,50%; Si-0,17−0,37%; Mn-0,50−0,80%; Cr — 0,25%; S-0,04%.
Данный материал имеет следующие физико-механические свойства:
02 = 32 МПа, В = 54 МПа, = 20%, = 475%.Данная сталь относится к классу среднеуглеродистых сталей, а, следовательно, хорошо обрабатывается резанием.
Замена конструкции вала сварной или сборной конструкцией является нецелесообразным.
На исходном чертеже детали проставлены все необходимые размеры с отклонениями, параметры шероховатости поверхностей соответствуют точности их размеров и не требуют дополнительных отделочных операций.
Чертеж детали имеет все необходимые виды, разрезы, сечения и выполнен в соответствии с требованиями ЕСКД. Все поверхности данной детали доступны для обработки и контроля.
После обработки возможно непосредственное измерение размеров при помощи стандартного и специального мерительного инструмента.
Нетехнологичными элементами на детали являются: отверстия ?6 и ?4 мм, расположенные на цилиндрических поверхностях, они обрабатываются на сверлильной операции с применением специального приспособления. Поверхности 20js6, 17js6, 20h6 подвергаются шлифованию, но не имеют канавок для выхода шлифовального круга.
Поверхности 20js6, 17js6, 20h6, 6h6 получаются двукратным точением и трёхкратным шлифованием, 7−0,1 — двукратным точением. Торцы, фаска и цилиндрические поверхности 22, 26 получаются однократным точением; пазы — фрезерованием. Отверстие 6Н7 сверлится, зенкеруется и развертывается, отверстие 2Н10 сверлится и зенкеруется.
Несмотря на указанные недостатки, деталь является технологичной.
1.2 Выбор метода получения заготовки
Для данной детали, исходя из её формы, размеров и материала, возможно использование таких методов получения заготовки, как: ковка, штамповка и заготовки из мерного проката. При выборе метода получения заготовки из проката 30 мм, масса заготовки 0,5 кг и коэффициент использования материала:
где
Mz — масса заготовки, Md — масса детали, Ким = 0.8, что приемлемо в серийном производстве.
Рисунок 1.1 — Эскиз заготовки.
1.3 Маршрутный технологический процесс
Таблица 1.1.
Поверхность | Токарно-револьверная | Токарно-винторезная | Вертикально-сверлильная | Горизонтально-фрезерная | Вертикально-фрезерная | Кругло-шлифовальная | |
Торец Ш20 | х | ||||||
Ш20js6 | х | х | |||||
Ш26 | х | ||||||
Ш22 | х | ||||||
Ш20h6 | х | х | |||||
Ш17js6 | х | х | |||||
Ш7−0,1 | х | ||||||
Ш6h6 | х | х | |||||
Торец Ш6 | х | ||||||
Отв.Ш6Н7 | х | ||||||
Отв.Ш2Н10 | х | ||||||
х | |||||||
Пазы R9,5 | х | ||||||
1.4 Проектирование операции
Согласно заданию выполняем детальное проектирование операции 020 горизонтально-фрезерной.
Обработка производится комплектом из двух дисковых фрез со вставными ножами из твердого сплава Т5К10. Фреза 2245−0003 Т5К10 ГОСТ 6469–69 (правая) и 2245−0003 Т5К10 ГОСТ 6469–69 (левая). Диаметр фрез 125 мм, число зубьев 10.
Для выполнения данной операции принимаем горизонтально фрезерный станок с крестовым столом модели 6Р11, со следующими характеристиками [1]:
Размеры стола, мм…200×800
Число Т-обр. пазов…3
Ширина Т-обр. пазов, мм…18
Расстояние между пазами, мм…70
Диаметр отв. шпинделя, мм…29
Обороты шпинделя, об/мин…63−2800
Подачи прод. и попер., мм/мин.11,2−500
Подачи вертик., мм/мин…;
Продольный ход стола, мм…400
Поперечный ход стола, мм…160
Вертикальный ход стола, мм…320
Наиб. масса обраб. детали, кг…250
Габариты станка, мм.:
длина…1525
ширина…1875
высота…1515
Масса станка, кг…1290
Определим скорость резания при фрезеровании:
V=;
Глубину фрезерования назначаем t=мм; ширина фрезерования B=3мм; подачу Sz=0.14 мм/зуб.
Kv = KmvKnvKuv;
Поправочный коэффициент равен:
Кv = KmvKuvKiv, где
Kmv — поправочный коэффициент на обрабатываемый материал Ст45,
Kmv = Кг (750/ув)nv=1*(750/600)=1.25; [1];
Kuv — поправочный коэффициент на инструментальный материал, для твердого сплава Т5К10 Kuv = 0,65;
Kпv — поправочный коэффициент, учитывающий влияние состояния поверхностного слоя заготовок на скорость резания, для проката Kпv = 0,9. На основании этого получаем поправочный коэффициент, равный:
Кv = 1,25*0,65*0,9=0,73;
Значения коэффициентов и показателей степени:
Сv=740; q=0.2; x=0.4; y=0.4; u=0; p=0; m=0.35; T=180мин. 2]
В результате расчёта получим:
V=201
Частота вращения:
501об, Корректируем частоту вращения по паспорту станка:
n= 500об/мин.
По полученной частоте вращения рассчитываем действительную скорость резания дисковой фрезы:
м/мин.
Рассчитаем значение тангенциальной силы, составляющей силы резания
Pz=,
Коэффициенты для дисковой фрезы:
Cv=261; x=0.9; y=0.8; u=1.1; q=1.1; w=0.1.
Км = (ув/750)0,75 =(530/750)0,75=0,7, — поправочный коэффициент, учитывающий влияние качества обрабатываемого материала на силовые зависимости, где ?=530 МПа — предел прочности материала детали, np=0.75- показатель степени.
Тангенциальная сила:
Pz=267Н, Для данной схемы фрезерования:
Ph/Pz=0.8…0.9 [1],
Pv/Pz=0.7…0.9 [1],
Ph=Pz*0.85=267*0.85=227 H.
Pv=Pz*0.8=267*0.8=213H
Мощность резания:
Nрез== кВт.
2. Конструкторская часть
2.1 Разработка схемы базирования и расчетной схемы
Для заданной операции принимаем следующую схему базирования:
Рисунок 2.1 — теоретическая схема базирования.
Для данной схемы базирования составляем расчетную схему:
Рисунок 2.2 — расчётная схема обработки.
2.2 Расчёт усилия закрепления
Согласно расчетной схемы составляем уравнения силового баланса, из которых определяем усилие закрепления.
;
;
f — коэффициент трения [2],
f=0.16
;
;
;
;
;
.
где:
к = к1 к2 к3 к4 к5 к6 к0,
к0 — коэффициент гарантированного запаса, к0 = 1.5
к1 — коэффициент, учитывающий затупление инструмента, к1 =1.6
к2 — коэффициент, учитывающий неравномерность припуска, к2 =1
к3— коэффициент, учитывающий прерывистость поверхности, к3 =1
к4— коэффициент, учитывающий постоянство силы закрепления, к4 =1
к5— коэффициент, учитывающий эргономичность конструкции, к5 =1
к6— коэффициент, учитывающий расположение сил относительно опор к6 =1
к = 1.5 1.6 = 2.4,
т.к. к =2.4, то принимаем к =2.5.
=771Н.
1898Н.
Необходимое усилие закрепления определяем как сумму усилий закрепления для сил резания Ph и Pv:
Q= Qh + Qv = 771+1898 = 2669 H.
2.3 Расчет усилия на приводе и параметров привода
Рисунок 2.3 — Схема привода.
Усилие на приводе:
W* l2= Q* l1,
l1=10мм, l2=20мм — длины рычагов.
H,
Зная усилие на приводе, рассчитаем параметры пневмоцилиндра.
При условии, что для закрепления воздух подается в штоковую полость диаметр цилиндра определяется по формуле:
где
P — давление в пневмосети, Р=0,63МПа,
=0,95 — КПД пневмоцилиндра.
м.
Wусилие на приводе, Н, р — давление в пневмосети, р = 0,63МПа,
— КПД, = 0,95.
Принимаю ближайшее стандартное значение Dц, = 40 мм Диаметр штока для пневмоцилиндра определяется по следующей зависимости
dшт = 0.25Dц, = 0.25*40 = 10 мм.
Фактическое усилие на штоке Фактическое усилие закрепления Q=2W=2802Н.
2.4 Расчёт элементов приспособления на прочность
Шток пневмоцилиндра имеет резьбовое отверстие М8, которое воспринимает усилие W=1401H.
Проверка резьбы на срез:
где d1— внутренний диаметр резьбы вилки, мм; d1=6,466 мм.
К — коэффициент полноты резьбы, принимаю К=0,87.
Кт — коэффициент неравномерности нагрузки по виткам резьбы, с учетом пластических деформаций принимается равным 0,55…0,75, принимаю Кт=0,65.
Нг — длина сопряженной части опоры и штока пневмоцилиндра, мм; Нг=20мм,
[]cp — допускаемые напряжения среза, мм. Для материала вилки (сталь 45) при термообработке улучшение []cp =145Мпа. 6].
Проверка резьбы тяги на смятие производится исходя из условия: [6]
где (р=1,25мм — шаг резьбы)
d — наружный диаметр резьбы, мм, d =8мм,
D1 — Внутренний диаметр резьбы, мм =6,466 мм,
[]см — допускаемые напряжения смятия материала, Мпа. []см =360Мпа. 6].
Таким образом условия прочности при расчете резьбы на смятие и на срез выполняются.
2.5 Расчёт погрешности установки заготовки в приспособлении
Т.к. лыски обрабатываются одновременно пакетом фрез, то погрешность выдерживаемого размера 14 зависит от точности установки фрез на оправку. Однако, возможно смещение детали относительно настроенных фрез, поэтому выполним проверку относительно радиального размера 12. Этот размер зависит от зазоров в посадках шпонки в пазах станка и приспособления и призм на осях.
где з — погрешность закрепления, так как усилие закрепления направлено перпендикулярно выдерживаемому размеру з=0 ;
б — погрешность базирования.
Погрешность базирования при установки заготовки в призме для выдерживаемого размера Н. 1]
Рис. 2.4 — Схема установки.
Погрешность закрепления при установке в призму определяется по формуле
,
где KRz, KHB ,C1- постоянные коэффициенты, для установки на призму KRz=0,005, KHB=15, C1=0,086+8,4/Dзаг=0,086+8,4/20=1,28;
m — постоянная степень, для установки на призму m=0,7;
Rz — параметр шероховатости заготовки, мкм, Rz=10мкм;
НВ — твердость материала заготовки по Бринеллю, для стали 45 НВ 350.
Погрешность приспособления в данном случае не влияет на точность обработки, так как настройка на размер идет по закрепленной заготовке, а не по элементам приспособления.
мкм.
Допуск на выдерживаемый размер: Т=180мкм.
Для работоспособности и обеспечения точности выполняемого размера должно выполнятся следующее условие: у 1/3Т,
где Т — поле допуска на выполняемый размер.
Проверим выполнение данного условия:
1/3Т = 1/3*180 = 90 мкм.
Как было рассчитано раньше у = 41мкм, следовательно, вышеприведенное условие выполняется.
2.6 Описание конструкции и принципа работы приспособления
Рисунок 2.5 — Схема приспособления.
На данном рисунке представлено приспособление, которое состоит из плиты поз.6, с установленными на ней пневмоцилиндром поз.19, опоры поз.1 с двумя призмами поз.20, стойкой поз.2, запрессованной установочной втулки поз.7; шток пневмоцилиндра соединен с рычагом поз.8 посредством стандартной вилки поз.14 и осей. Для того чтобы во время обработки не допустить выкручивания винтов, устанавливаются стопорные шайбы. Работает приспособление следующим образом: заготовка устанавливается в призмы и установочную втулку, при этом поршень находится в крайнем левом положении, затем воздух подается в штоковую полость и поршень под воздействием давления перемещается вправо, перемещая рычаг и закрепляя заготовку.
Выводы
При выполнении курсового проекта проведен анализ технологичности конструкции детали, разработан технологический процесс механической обработки. На операцию 020 горизонтально-фрезерную сконструировано специальное приспособление, для которого выполнены расчеты на прочность и точность. При проектировании учтены особенности конструкции и условия работы деталей и узлов приспособлений в сравнении с деталями общего машиностроения. Получены практические навыки в проектировании станочных приспособлений, в выборе наиболее оптимальной схемы базирования.
Из-за применения специального приспособления для установки данной детали на горизонтально-фрезерной операции достаточно эффективно в условиях серийного производства так как затраты на его проектирование и изготовление распределяются на все детали в партии. Конструкция данного приспособления позволяет уменьшить вспомогательное время на установку детали т.к. при установке не требуется выверка детали, а привод зажимного устройства механизирован.
Из вышесказанного, можно сделать вывод целесообразности использования спроектированного приспособления в условиях серийного производства.
Перечень ссылок
1. Справочник технолога машиностроителя. В 2-х т. Т. 2/ Под ред. А. Г. Косиловой и Р. К. Мещерякова. — 4-е изд., перераб. и доп. — М.: Машиностроение, 2011. 496 с.
2. Анурьев В. И. Справочник конструктора машиностроителя: в 3-х т. Т1. — 8-е изд., перераб. и доп. Под ред. И. Н Жестковой. — М.: Машиностроение, 2009. — 920с.
3. Станочные приспособления: Справочник. В 2-х т. Т.1/Под ред. Б. Н. Вардашкина, А. А. Шатилова. — М.: Машиностроение, 2010. 592 с.
4. Обработка металлов резанием: Справочник технолога/ А. А. Панов, В. В. Аникин, Н. Г. Бойм и др.; Под общ. Ред. А. А. Панова. — М.: Машиностроение. 2008. — 736 с.