Технология ультразвукового контроля технологических трубопроводов атомного реактора
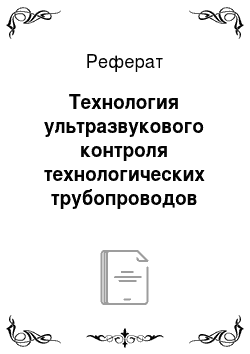
Технология сварки центральной, верхней и нижней частей канала состоит в следующем. Соединение канальных труб с циркониевыми частями переходников осуществляется посредством электронно-лучевой сварки. Стальные части переходных соединений стыкуются с верхней и нижней частями технологического канала посредством сварки в среде аргона. На наружные поверхности стальных частей канала в целях защиты… Читать ещё >
Технология ультразвукового контроля технологических трубопроводов атомного реактора (реферат, курсовая, диплом, контрольная)
Многолетний опыт эксплуатации ядерных энергетических установок с реакторами РБМК-1000 показал, что конструкция технологического канала реактора требует к себе повышенного внимания, так как определяет безопасность работы всего устройства, находясь в условиях жесткого нейтронного облучения, высоких температур и воздействия теплоносителя.
Основной задачей диагностики конструкций является своевременное обнаружение изменения их геометрических параметров и состояния металла.
По мере старения оборудования роль диагностики существенно возрастает. В свете общих тенденций ужесточения требований к качеству оборудования атомной энергетики повышаются требования к точности, надежности и удобству эксплуатации существующих систем контроля. Возникает необходимость в системах ранней диагностики. Учитывая проблемы, связанные с продлением срока эксплуатации АЭС, существует необходимость совершенствования технологии и специального оборудования для ремонта и замены узлов конструкций активной зоны реакторов.
Центральным элементом в активной зоне РБМК-1000 является технологический канал реактора (ТК). От его состояния зависит безопасная работа ядерного реактора [1,2]. Наиболее ответственной частью технологического канала является циркониевая труба и ее сварные швы. В связи с этим, к выбранному ультразвуковому методу контроля в настоящей работе были поставлены следующие задачи: определить оптимальный угол просвета стержня ультразвуком и частоту.
Технология изготовления центральной трубы из сплава Zr + 2,5% Nb заключается в следующем. Из сплава Zr + 2,5% Nb изготавливается слиток, который подвергается последующей ковке при температуре от 950 оC до 1070 оC. Из поковки изготавливаются заготовки. Заготовки подвергаются горячему выдавливанию при температуре от 580 оC до 780 оC с получением прутков. Прутки разрезаются на мерные заготовки и подвергаются закалке: проводится нагрев заготовок до температуры 900−920 оC (температура полиморфного превращения сплава Тпп=860−870 оC) и закалка в воду. Затем изготавливают заготовки механическим способом для горячего выдавливания. Полученные заготовки подвергают отпуску при температуре 560 — 580 оC, после чего их выдавливают при температуре 580 — 780 оC. Выдавленные заготовки после проведения операции отжига при температуре 560−580 оC подвергают холодной деформации на станах холодной прокатки труб с промежуточными отжигами при температуре 560−580 оC. Окончательный отжиг после последней холодной прокатки проводится для получения труб:
- — в частично рекристаллизованном состоянии при температуре 500−540 оC; стержень ультразвук отжиг прокатка
- — в полностью рекристаллизованном состоянии при температуре 540−580 оC.
Отожженные трубы подвергают отделочным операциям для получения готовых труб, которые после этого подвергались визуальному и ультразвуковому контролю. Анализ применения ультразвукового контроля на различных объектах [3] показывает, что наибольшая часть работ проводится на сварных соединениях, причем в большинстве случаев контроль выполняется вручную.
Технология сварки центральной, верхней и нижней частей канала состоит в следующем. Соединение канальных труб с циркониевыми частями переходников осуществляется посредством электронно-лучевой сварки. Стальные части переходных соединений стыкуются с верхней и нижней частями технологического канала посредством сварки в среде аргона. На наружные поверхности стальных частей канала в целях защиты от коррозии наносится металлизационное покрытие алюминием. В итоге получается сварное соединение стальной трубы с трубой из сплава Zr + 2,5% Nb с использованием переходника, выполненного диффузионной сваркой в вакууме [4]. Далее соединение подвергают неразрушающим методам контроля [5]. Наиболее уязвимое место в переходнике — это зона диффузионной сварки, которая представляет собой гребенку зубьев (рис.1). Эта зона подлежит особому контролю.
В циркониевых трубах каналов встречаются осевые трещины, развивающиеся с наружной поверхности и окружные «выбоины» на внутренней поверхности в районах расположения дистанционирующих решеток тепловыделяющих сборок.
Контроль циркониевой части ТК обеспечивает выявление несплошностей, расположенных на наружной и внутренней поверхностях канала, эквивалентных по своей отражающей способности искусственному отражателю типа «риска» глубиной 0,5 мм. Плоскости сечений прозвучивания относительно оси каналов составляют 0°, 45°, 90° и 135°. В каждом сечении контроль проводится прямым и однократно отраженным лучами в двух взаимно противоположных направлениях (рис.2). Контроль осуществляется в автоматическом режиме при перемещении многоэлементного пьезоэлектрического преобразователя снизу-вверх и одновременном его вращении вокруг своей оси. Многоэлементный пьезоэлектрический преобразователь (МПЭП) представляет собой разделенный на несколько частей одноэлементный ПЭП. С каждой части МПЭП снимается свой сигнал, так что количество каналов обработки данных увеличивается, но появляется возможность применения алгоритмов совместной обработки этих сигналов для выявления дополнительных параметров дефектов. Такой подход уже используется в портативных дефектоскопах с ультразвуковыми фазированными антенными решетками [6,7]. Идея применения многоэлементных датчиков не нова и широко используются в разных областях акустики [8−11].

Рис. 2. Схема проведения контроля
Перемещение преобразователя вдоль и вращение его вокруг своей оси в процессе настройки аппаратуры осуществляется в ручном режиме управления. Настройка задержки и длительности развертки каждого такта цикла работы дефектоскопа проводится так, чтобы наибольшая часть развертки на экране дефектоскопа соответствовала пути ультразвукового импульса в контролируемом металле.
В данной работе определены углы падения излучающего и приемного резонаторов, а также выявлены такие явления, как затухание и расслабление ультразвука. В ходе работы было отслежено распространение волнового фронта и математическим путем определена мертвая зона. На основании исследований построены зависимости рекомендованных частот и угла ввода луча стенки реактора от толщины стенки канала (рис.3).
Анализ зависимости свидетельствует, что для наиболее чаще используемой толщины стенки 8 мм необходимо применять частоту ультразвука 5 МГц и угол ввода 70°.
Заключение
Выбраны и рассчитаны параметры акустической системы: типы волн, используемые при контроле, углы ввода и частоты, в зависимости от природы процесса затухания и ослабления ультразвука. Разработанная методика контроля позволяет в достаточной мере выявлять дефекты, а также значительно сократить время пребывания человека в зоне контроля.
- 1. Безопасность АЭС с канальными реакторами. Конструкция активной зоны /Л.А. Белянин, В. И. Лебедев, Ю. В. Гарусов и др. — Энергоатомиздат, 1997. — 255 с.
- 2. Трофимов А. И. Ультразвуковые системы контроля искривлений технологических каналов ядерных реакторов, М.: Энергоатомиздат, 1994. -230 с.
- 3. В. Г. Щербинский, Н. П. Алешин. Ультразвуковой контроль сварных соединений. — 3- е изд., перераб. И доп. — Изд — во МГТУ им. Н. Э. Баумана, 2000. — 496 с.
- 4. Люшинский А. В. Диффузионная сварка разнородных материалов /А.В. Люшинский. — М.: Академия, 2006. — 208 с.
- 5. Коновалов Н. Н. Обоснование применения методов неразрушающего контроля для оценки качества сварных конструкций грузоподъемных кранов // Известия ТПУ, 2004. № 7. — С. 102−103
- 6. Тарасов С. П., Тимошенко В. И., Воронин В. А., Кириченко И. А., Пивнев П. П., Солдатов Г. В., Волощенко А. П., Эсси-Эзинг А.С., Обыденная В. А., Франчук Д.А.
- 7. Dombret Ph., Methodology for the ultrasonic testing of austenitic stainless stell. Nuclear Engineering and Design 131 (1991), North — Holland, pp. 279−284
- 8. S.J. Song and H.J. Kim, «Modeling of Radiation Beams from Ultrasonic Transducers in a Sinsle Medium,» Journal of the Korean Society for Nondestructive Testing, Vol.20, No.2,2000, pp. 134−140