Технология ремонта тягового электродвигателя
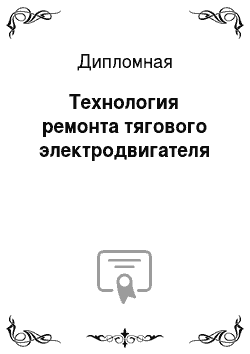
Работа по охране труда проводится в соответствии с «Положением об организации работы по охране труда на железнодорожном транспорте», утвержденным ОАО «РЖД» № ЦЗТ / 2295, ответственность за выполнение правил по технике безопасности возложена на руководителей предприятия. Старшие мастера, мастера, бригадиры обеспечивают выполнение требований по технике безопасности и производственной санитарии… Читать ещё >
Технология ремонта тягового электродвигателя (реферат, курсовая, диплом, контрольная)
Введение
Железнодорожный транспорт требует развития, иначе произойдет резкое замедление в экономическом росте. Для того чтобы не допустить это, разработали Стратегию развития российского железнодорожного транспорта на перспективу до 2030 года.
В качестве стратегической цели поставлено транспортное обеспечение экономического роста, в основе которого лежит эффективное развитие и модернизация ж/д транспорта, который гарантирует единство российского экономического пространства и реализацию гражданских прав на свободное передвижение и создание глобальной конкурентоспособной системы железнодорожного транспорта.
Ряд задач ставится перед стратегией: создание условий, в которых будет возможной реализация основных геоэкономических и геополитический целей РФ. Формирование необходимой инфраструктурной основы для роста экономики в социально-экономическом сегменте.
Также важно обеспечить доступ транспорта к точкам обеспечения ресурсами и промышленного роста, а также в места работы, лечения, отдыха, образования, культурных ценностей — для российских граждан. Привести уровень безопасности и качества перевозок в соответствие с требованиями экономики и населения в соответствии с мировыми стандартами.
Необходимо создать в железнодорожном транспорте и экономике достаточное количество необходимых резервов и провозных способностей для того, чтобы в полном объеме удовлетворить спрос на осуществление перевозок при конъюнктурных колебаниях. Необходимо осуществить процесс глубокой интеграции в транспортную систему мира. Следует поддерживать высокий уровень подготовленности к функционированию в чрезвычайных условиях и соответствовать требованиям безопасности и обороноспособности страны. Важно повышать инвестиционную привлекательность сферы железнодорожного транспорта. Необходимо сохранять роль железнодорожного транспорта в экономике и влиянию на социальную стабильность в отрасли, а также обеспечить высокое качество и условия для жизни железнодорожников. Это важная составляющая общества.
Кроме того, необходимо учитывать вопросы молодежной политики и эффективной поддержки в социальном плане ветеранов отрасли. Важным аспектом является внедрение высоких стандартов по организации труда и его производительности, а также достижения устойчивого обеспечения процесса перевозок кадрами с высокой квалификацией.
Локомотивное хозяйство является одним из наиболее фондоемких в отрасли, на него приходится 12,5% стоимости основных фондов железных дорог. При этом основной составляющей (до 85%) является стоимость тягового подвижного состава.
Характеристики локомотивов определяются тяговыми, эксплуатационными и экономическими свойствами и показателями и должны соответствовать назначению, экономическим и географическим условиям предстоящей их эксплуатации, отражать передовые достижения в области транспортного машиностроения.
К важнейшим тяговым показателям относятся:
величины реализуемой силы тяги и скорости движения;
конструкционная максимально допустимая скорость;
нагрузка от оси на рельсы;
номинальная мощность;
приспособленность локомотива к переменному режиму работы.
К эксплуатационным свойствам локомотива относятся: надежность в работе, ремонтопригодность, степень автономности, мобильности и автоматизации управления, обеспечение безопасности движения и комфортных условий труда для локомотивной бригады.
Экономичность локомотивов характеризуется энергетическими затратами на единицу мощности или перевозимого груза, расходом металла на единицу мощности, сроком окупаемости, удельными расходами на эксплуатацию, техническое обслуживание и ремонты.
Технический уровень эксплуатируемых в настоящее время электровозов был заложен в 60-е-70-е гг. ХХ в. Эксплуатируемые электровозы относятся к первому и второму поколению локомотивов. За прошедшее время технологии в области силовой и слаботочной электроники, автоматики и механики шагнули далеко вперед. Об этом свидетельствует обширный опыт зарубежных стран, где серийно выпускаются и эксплуатируются электровозы 3-го и 4-го поколений.
Конструкция локомотивов нового поколения предусматривает:
сокращение расхода энергоресурсов на тягу поездов на 10−15%;
суммарное снижение эксплуатационных расходов на обслуживание и ремонт за срок службы на 40−60% для электровозов и на 30−40% для тепловозов;
повышение коэффициента готовности до 0,95 для электровозов и до 0,94 для тепловозов;
повышение основных тяговых параметров;
использование на грузовых и маневровых тепловозах в качестве моторного топлива природного газа;
повышение безопасности движения;
улучшение экологических показателей.
1 Общая часть
1.1 Расчет программы и фронта ремонта, инвентарного парка и процента неисправных локомотивов по видам ремонта, сериям и общего по депо.
Расчет программы ремонта для грузовых и пассажирских локомотивов ведется по формуле
(1)
(2)
(3)
(4)
(5)
(6)
где: — общий годовой пробег локомотивов, лок. км;
— среднесетевые нормы пробегов локомотивов, тыс. км.
Для грузового движения:
=8 (лок)
=17 (лок)
=25 (лок)
=50 (лок)
=705 (лок) Для пассажирского движения:
=5 (лок)
=9 (лок)
=10 (лок)
=32 (лок)
=337 (лок) Расчет программы ремонта для маневровых локомотивов ведется по формуле
(7)
=1 (лок)
(8)
=1 (лок)
(9)
=2 (лок)
(10)
=4 (лок)
(11)
=7 (лок)
(12)
=62 (лок) Определение фронта ремонта локомотивов в депо.
Фронт ремонта — это количество локомотивов, одновременно находящихся в течение суток во всех видах ремонта.
Фронт ремонтов определяется по формуле:
(13)
где: — программа данного вида ремонта или технического обслуживания;
— среднесетевые нормы продолжительности, сутки.
Для грузового движения:
= 0,26
= 0,26
= 0,41
= 0,53
= 2,81
Для пассажирского движения:
=0,3
=0,41
=1,57
Для маневрового движения:
=0,02
=0,01
=0,03
=0,02
=0,01
=0,2
Для грузового движения:
(14)
Для пассажирского движения:
(15)
Для маневрового движения:
(16)
Тогда общий фронт ремонта по депо определяется как сумма:
(17)
7 (лок) что соответствует среднему суточному количеству локомотивов, которые простаивают во всех видах ремонта в депо.
Расчет инвентарного парка депо.
Находим общее количество локомотивов в депо по следующей формуле:
(18)
(лок) где: — эксплуатируемый парк грузовых локомотивов;
— эксплуатируемый парк пассажирских локомотивов;
— эксплуатируемый парк маневровых локомотивов;
— локомотивы, отосланные в другие депо;
— резерв управления дороги;
— общий фронт ремонта.
Определение процента неисправных локомотивов.
Процент неисправных локомотивов — это соотношение среднесуточного количества неисправных локомотивов к парку, находящемуся в распоряжении депо, или к инвентарному парку депо. Различают деповской процент неисправных локомотивов, заводской процент неисправных локомотивов и общий процент неисправных локомотивов.
Находим деповской процент неисправных локомотивов:
(19)
=7,4%
Находим заводской процент неисправных локомотивов:
(20)
=0,5%
Находим общий процент неисправных локомотивов:
(21)
= 7,9%
1.2 Определение штата рабочих и служащих депо
Штат административно — управленческого и оперативно — производственного персонала депо определяем по типовым штатам и нормативам численности инженерно — технического персонала и служащих депо, согласно группе депо, оцениваемых по сумме баллов согласно указаниям ОАО «РЖД».
Таблица — Инженерно — технический персонал депо
Наименование должностей | Численность | |
Нормативы численности руководящих работников депо | ||
Начальник депо | ||
Главный инженер | ||
Заместитель начальника депо по ремонту | ||
Старший инженер (инженер) по труду и заработной плате | ||
Главный технолог | ||
Старший экономист | ||
Секретарь (машинистка, делопроизводитель) | ||
Нормативы численности работников отдела кадров | ||
Инспектор по кадрам | ||
Начальник отдела кадров | ||
Нормативы численности работников производственно-технического отдела | ||
Начальник отдела | ||
Инженер (старший инженер) | ||
Техник (старший техник) | ||
Инженер по материально-техническому обеспечению | ||
Инженер по охране труда и технике безопасности | ||
Нормативы численности работников бухгалтерии | ||
Главный бухгалтер | ||
Бухгалтер (старший бухгалтер) | ||
Бухгалтер-рассчетчик | ||
Кассир | ||
Нормативы численности инженерно-технических работников производственных участков | ||
Старший мастер ТР-2 | ||
Мастер | ||
Мастер по реостатным испытаниям | ||
Нормативы численности работников производственных участков | ||
Инженер технолог (старший инженер технолог) | ||
Техник | ||
Техник-рассчетчик (на производственный участок) | ||
Нормировщик | ||
Приемщик локомотивов | ||
Всего | ||
Штат рабочих депо складывается из штата производственных рабочих ремонтных участков и отделений, штата локомотивных бригад и вспомогательных работников.
Штат производственных рабочих, явочное количество производственных рабочих по каждому виду текущего ремонта и технического обслуживания, определяют в соответствии с трудоемкостью: единицы ремонта и его программой:
(22)
где q — нормативная трудоемкость ремонта на один локомотив, чел. ч;
Мрем — годовая программа ремонта;
Т — годовой фонд рабочего времени, ч;
k — коэффициент перевыполнения норм выработки (k =1,15).
Таблица — Нормативы трудоёмкости ремонта
Серия локомотива | Трудоемкость, чел. ч | ||||
ТО-3 | ТР-1 | ТР-2 | ТР-3 | ||
ЭП1 | |||||
ВЛ 80 С | |||||
ЧМЭ-3 | |||||
Явочное количество рабочих составит:
Для ЭП1:
ТР-3: человек;
ТР-2: человек;
ТР-1: человек;
Для ВЛ 80 С:
ТР-3: человек;
ТР-2: человек;
ТР-1: человек;
Для ЧМЭ-3:
ТР-3: человек;
ТР-2: человек;
ТР-1: человек;
ТО-3: человек.
Списочную численность рабочих определяют по формуле:
Чсп = Чяв • (1 + Кзам), (23)
где Кзам — коэффициент замещения отсутствующих рабочих (Кзам = 0,09).
Для ЭП 1:
ТР-3: Чсп = 13 • (1 + 0,09) =14 человек;
ТР-2: Чсп = 12 • (1 + 0,09) =14 человек;
ТР-1: Чсп = 37• (1 + 0,09) =40 человек;
Для ВЛ 80 С:
ТР-3: Чсп = 33 • (1 + 0,09) = 36 человек;
ТР-2: Чсп = 22 • (1 + 0,09) = 24 человек;
ТР-1: Чсп = 93 • (1 + 0,09) =101 человек;
Для ЧМЭ-3:
ТР-3: Чсп = 1 • (1 + 0,09) = 2 человек;
ТР-2: Чсп = 1 • (1 + 0,09) = 2 человек;
ТР-1: Чсп = 2 • (1 + 0,09) = 3 человек;
ТО-3: Чсп = 3 • (1 + 0,09) = 4 человек.
= 14+14+40+36+24+101+2+2+3+4=240 человек.
Штат вспомогательных работников определяют в процентном отношении от трудовых затрат на производственные нужды и принимают в соответствии с руководством по определению штатных контингентов ЦПЭУ/3936 от 25.11.08 для тепловозных депо 15%:
=240 15% =36 человек.
Общее количество рабочих депо:
(24)
Где — общее количество людей в ремонтной работе;
— вспомогательный персонал депо;
— инженерно — технический персонал депо.
Чсп = 240 + 36 + 44 =320 человек
1.3 Определение количества ремонтных и специализированных стойл для выполняемого в депо ТР и ТО локомотивов, выбор типа, длины стойловых участков и размеров основных зданий депо Количество специализированных стойл для каждого вида текущего ремонта или технического обслуживания, определяют в соответствии с годовой программой ремонта, продолжительностью простоя в каждом из них на специализированном стойле с организацией работ в депо.
Количество стойл определяем по формуле:
Для участков ТР-3, ТР-2, ТР-1 и ТО-3:
(25)
где Мрем — программа ремонта или обслуживания за год;
tр — время простоя в ТР или ТО-3, сутки;
Т — количество рабочих дней в году (305);
? — коэффициент, учитывающий неравномерность постановки локомотивов в стойло (для ТР-3 и ТР-2, для ТР-1 и ТО-3).
Подставив значения получим:
Для участка ТР-3:
Для ВЛ80: стойло Для ЭП1: стойла Для ЧМЭ-3: стойло Для участка ТР-2:
Для ВЛ 80: стойло Для ЭП1: стойла Для ЧМЭ-3: стойло Для участка ТР-1:
Для ВЛ 80: стойло Для ЭП1: стойла Для ЧМЭ-3: стойло Для участка ТО-3:
Для ЧМЭ-3: стойло Для участка ТР и ТО-3:
= 0,5+0,19+0,03+0,6+0,3+0,04+1,9+1,1+0,02+0,1=5
Для ТО-5 принимаем — 1 стойло; для ТО-4 — 1 стойло; для скато-опускной канавы — 1 стойло и для резерва (непланового ремонта) — 1 стойло.
Всего 9 стойл.
Депо выбираем прямоугольно-ступенчатого типа, состоящее из 3 ступеней. Первая ступень для участка ТР — 2. Вторая ступень для участка ТР — 1 и ТО — 3. Третья ступень для участка ТР — 3.
Определение длины стойловых участков производится по формуле:
lТР = l•2 + 2•(a+b)+c (26)
lТО = l + 2•(a+b)+c (27)
где l — длина локомотива по осям автосцепки;
a — расстояние от края канавы до торца стены (1,2м);
b — расстояние от края канавы до торцевой стены (3,2м);
c — расстояние, на которое передвигается локомотив для осмотра зубчатой передачи (1,65м).
Подставим значения в формулу:
lТР = 32 • 2 + 2 • (1,2 + 3,2)+1,65 = 74,45 м;
lТО = 32 + 2 • (1,2 + 3,2)+1,65 = 42,45 м.
В соответствие со строительными нормами м., м.
1.4 Выбор и определение площадей служебно-бытового корпуса, отделений и участков производственных мастерских депо
Таблица — Площади отделений и участков производственных мастерских депо, м2
Наименование | Площадь, м2 | |
Дизель — заготовительный цех | ||
Участок топливной аппаратуры | ||
Пропиточно-сушильное отделение | ||
Участок фильтров | ||
Участок секций холодильников | ||
Участок электрической аппаратуры | ||
Электромашинное отделение | ||
Аккумуляторный цех | ||
Тележечное отделение | ||
Участок КМБ | ||
Автотормозное отделение | ||
Сварочное отделение | ||
Кладовая запасных частей | ||
Участок компрессоров и насосов | ||
Механическое отделение | ||
Слесарно-заготовительное отделение | ||
Гальваническое отделение | ||
Инструментальная кладовая | ||
Столярное отделение | ||
Помещение комплексных бригад | ||
Лаборатория | ||
Мастерская главного механика | ||
Отделение по ремонту АЛСН и радио | ||
Отделение по ремонту КИП | ||
Моечное отделение | ||
Водоприготовительное отделение | ||
Экспериментальный участок | ||
Хозяйственный участок | ||
Участок зарядки огнетушителей | ||
Компрессорная депо | ||
Участок технического обслуживания электрокаров и электропогрузчиков | ||
Таблица — Площади административно — служебных помещений локомотивного депо
Наименование помещений | Площадь, м2 | |
Кабинет управления | ||
Кабинет начальника депо | ||
Кабинет главного инженера | ||
Приемная | ||
Рабочие комнаты управления | ||
Отдел кадров | ||
Производственно-технический отдел | ||
Планово-экономический отдел | ||
Бухгалтерия | ||
Касса | ||
Группа оперативно-технического учета | ||
Технические кабинеты и помещения | ||
Технический кабинет | ||
Кабинет автотормозного оборудования | ||
Кабинет по технике безопасности | ||
Рабочие комнаты при участках | ||
Кабинет заместителя начальника депо по ремонту | ||
Контора главного механика | ||
Помещение приемщиков | ||
Диспетчерская | ||
Контора мастеров (суммарная площадь) | ||
1.5 Выбор подъемно-транспортного оборудования цехов, участков и отделений депо
Грузоподъёмность кранов определяется в соответствии с принятой технологией ремонта и массой наиболее тяжёлых обслуживаемых сборочных единиц.
Таблица — Высота отделений мастерских и грузоподъёмность кранов локомотивного депо
Наименование отделений мастерских | Тип крана | Грузоподъёмность | Высота, мм | ||
До головки подкранового рельса | До низа конструкций покрытия | ||||
Электромашинное | Мостовой с кабиной | ||||
Испытательная станция | Мостовой | ||||
Пропиточно-сушильное | Опорный | ||||
Электрической аппаратуры | Мостовой электрический | ; | |||
Секций холодильников | Подвесной | ; | |||
Фильтров | Подвесной | ; | |||
Аккумуляторное, кислотное, ремонтный участок | Подвесной | ; | |||
Щелочное, ремонтный участок | Подвесной | ; | |||
Зарядная | Подвесной | ; | |||
Тележечное | Мостовой с кабиной | ||||
Колёсно-моторных блоков | Мостовой | ||||
Механическое | Подвесной | ; | |||
Кузнечное | Подвесной | ; | |||
Термоотделение | Подвесной | ; | |||
Сварочное | Подвесной | ; | |||
Гальваническое | Подвесной | ; | |||
Компрессорная | Монорельс с тельфером | 0,5 | ; | ||
Прочие отделения мастерских | ; | ; | ; | ||
2. Индивидуальная часть
2.1 Назначение цеха (участка, отделения) и определение объема его работы Электромашинный цех предназначен для деповского ремонта электричесих машин. В состав цеха входят участки по ремонту тяговых электродвигателей, тяговых генераторов и вспомогательных машин электровозов. В состав участков также входят непосредственно машинное отделение, и пропиточно-сушильное.
На участках предусмотрено механизация всех подъемо-транспортных и разборо-сборочных работ с применением механизированного инструмента (кантавателей, индукционных нагревателей и других специальных приспособлений), очистки и дефектации деталей.
Программа ремонта участка в год:
Грузовых локомотивов серии ВЛ 80 С — 25 локомотивов Пассажирских локомотивов серии ЭП 1 — 7 локомотивов Маневровых локомотивов серии ЧМЭ3 — 18 локомотивов Итого: 50 локомотивов
2.2 Определение штата работников электромашинного цеха и организация его работы Штат работников участка определяем в соответствии с рассчитанным объемом и трудоемкостью ремонта одного комплекта сборочных единиц, которые подвергаются ремонту в данном участке.
Расчет производим по формуле:
(28)
где q — нормативная трудоемкость ремонта данного отделения, чел-ч;
Мрем.уз — годовая программа ремонтов узлов;
1,09 — коэффициент, показывающий отношение списочного числа рабочих к явочному;
Т — годовой фонд рабочего времени, ч (1970);
к — коэффициент, учитывающий перевыполнение норм выработки (1,2).
человека.
Списочную численность рабочих определяют по формуле:
Чсп = Чяв • (1 + Кзам) (29)
где Кзам — коэффициент замещения отсутствующих рабочих (Кзам = 0,09).
Чсп = 20• (1 + 0,09) =22 человек.
Мастер — 1 человек.
Бригадир — 1 человек.
Списочный штат работников составляет:
=22 +1+1=24 человек.
На участке работают специализированные бригады слесарей в количестве, необходимом для выполнения заданной программы ремонтов локомотивов. Такая организация системы ремонта локомотивов способствует повышению квалификации рабочих по данной специальности, сохраняет время на выполнение ремонтных операций, улучшает качество ремонта.
Перед началом очередной смены мастер составляет сменные задания, которые доводятся до всех исполнителей. После окончания работы мастер принимает изготовленные или отремонтированные узлы и детали. Детали, которые после разборки на локомотиве и ремонта на участке подлежат возврату на ремонтируемый локомотив, поступают на участок с указанием объема ремонта и сроков возврата. Мастер следит за своевременным выполнением ремонта и возвратом деталей на локомотив.
2.3 Выбор необходимого технологического оборудования электромашинного цеха Выбор необходимого оборудования и подъемно — транспортных средств, производится в соответствии с табелями основного подъемно — транспортного, станочного и технологического оборудования, стендов и приспособлений.
Таблица — Основное оборудование участка по ремонту ТЭД НБ-520
Оборудование | Количество, шт | |
Накопитель неисправной продукции | ||
Верстак | ||
Стеллаж для инструментов | ||
Моечная машина | ||
Стенд для дефектоскопии | ||
Стенд-кантователь | ||
Станок расточный | ||
Стенд для испытания | ||
Накопитель исправной продукции | ||
2.4 Расчет освещения, отопления и вентиляции участка по ремонту ТЭД НБ-520
Затраты на отопление находятся по формуле:
(30)
где — объем участка ремонта, м3;
=11 785
(31)
где — — площадь участка ремонта, м2;
— высота участка ремонта, м;
— количество часов отопительного сезона (4320), ч;
— средний расход тепла в помещении участка ремонта, 30 кДж/час на 1 м³ здания;
— теплопроводность условного топлива (540);
— цена одной единицы условного топлива (40,92).
Затраты на электроэнергию включают в себя затраты на освещение участка ремонта и силовую энергию, которую используют при работе оборудования:
(32)
где — затраты на освещение, руб.;
— затраты на электроэнергию для работы оборудования, руб.
Используются следующие формулы расчета:
(33)
Где — цена одного квт/ч (2,71 руб);
— площадь участка ремонта, м2;
— норма освещенности одного квадратного метра площади;
1,2 — коэффициент, учитывающий потери электроэнергии в сети;
1950 — годовое количество часов осветительной нагрузки, ч;
0,8 — поправочный коэффициент спроса электроэнергии.
(34)
где — суммарная мощность оборудования, кВт/ч (из технического паспорта оборудования);
0,8 — коэффициент загрузки оборудования;
1,2- коэффициент, учитывающий потери электроэнергии в сети.
2.5 Разработка мероприятий по охране труда и противопожарной безопасности участка по ремонту ТЭД-НБ-520
Работа по охране труда проводится в соответствии с «Положением об организации работы по охране труда на железнодорожном транспорте», утвержденным ОАО «РЖД» № ЦЗТ / 2295, ответственность за выполнение правил по технике безопасности возложена на руководителей предприятия. Старшие мастера, мастера, бригадиры обеспечивают выполнение требований по технике безопасности и производственной санитарии на своих участках, инструктируют рабочих и следят за соблюдением правил по технике безопасности, проверяют инструмент и приспособления. Не допускают рабочих к работе без спецодежды и защитных средств, следят за освещением, вентиляцией и отоплением цехов, порядком на рабочих местах. Вновь поступивший рабочий может быть допущен к работе после изучения безопасных приемов труда и сдачи испытания. Первоначально инженер по технике безопасности дает вводный инструктаж. Вводный инструктаж проводят со всеми лицами, вновь поступившими на работу на железнодорожный транспорт или переводимыми с одного предприятия на другое, а так же с учащимися, направленными на предприятие для прохождения производственного обучения, работы и практики. Цель вводного инструктажа — ознакомить с общими положениями по охране труда, условиями работы и правилами внутреннего распорядка на работе.
Первичный инструктаж на рабочем месте проводится в начале первого дня работы, после издания приказа о зачислении Первичный инструктаж проводит руководитель подразделения — начальники цехов, смен, мастера. Первичный инструктаж проводится, с вновь принятыми на работу, при переводе работников с одной работы на другую. Первичный инструктаж на рабочем месте проводится для ознакомления работника с конкретной производственной обстановкой на данном рабочем месте и безопасными приемами труда.
Повторный инструктаж проводят с рабочими, учащимися с целью разъяснения мер безопасности при выполнении работ, ознакомления с приказами, указами по охране труда.
Внеплановый инструктаж проводят в связи с имевшей место производственной травмой или нарушением требований по технике безопасности. Цель инструктажа — разбор и предупреждение подобных случаев. Инструктаж проводят с работниками цеха.
Основными причинами пожаров на участке являются: открытый огонь, электрические искры, вызываемые ударами металлических частей, статическое и атмосферное электричество, несоблюдение установленных правил и инструкций по пожарной безопасности, нарушение правил эксплуатации, неисправность приборов отопления и освещения, незнание свойств пожароопасности и взрывоопасности веществ и материалов.
2.6 Разработка карты неисправности ТЭД НБ-520
Название неисправности | Причина | Способ устранения | |
Снижение сопротивления изоляции обмоток | Попадание внутрь электродвигателя влаги и грязи | Подсушить изоляцию обмоток. Почистить поверхности обмоток от грязи | |
Переброс электрической дуги по коллектору вплоть до кругового огня | Сосредоточение угольной пыли в канавках между коллекторными, пластинами | Очистить и промыть коллектор, щеточный механизм, заменить поврежденные щетки и продуть коллекторную камеру сухим сжатым воздухом | |
Недостаточное давление пружин на щетки | Отрегулировать или заменить пружины | ||
Разрыв и разматывания стеклобандажа обмотки якоря | Превышение максимально допустимой частоты вращения якоря | Проверить исправность системы протипробуксировочной защиты, ремонт якоря с заменой поврежденного стеклобандажа | |
Механическое повреждение бандажа инородными телами | Ремонт якоря | ||
2.7. Назначение ТЭД НБ-520
Тяговый электродвигатель НБ-520 предназначен для преобразования электрической энергии, получаемой из контактной сети, в механическую, передаваемую с вала двигателя на колесную пару электровоза.
Условия, в которых работают тяговые двигатели весьма тяжелые. В отличие от стационарно устанавливаемых машин они подвержены воздействиям окружающей среды, динамическим ударам со стороны рельсового пути и работают в условиях широко, а иногда и резко изменяющихся значений тока, напряжения.
Несмотря на принимаемые меры, из окружающей среды в машины попадают влага и пыль. Влага проникает в поры изоляции обмоток машин, что приводит к снижению ее электрической прочности, создает условия для возникновения электрического или теплового ее пробоя, приводит к ускорен ному ее старению. В сочетании с низкими температурами влага способствует появлению инея и обледенению коллектора и щеточного аппарата, что приводит к повышенному искрению под щетками. Повышенное искрение возникает и от загрязнения коллектора и щеточного аппарата пылью, попадающей в машину через неплотности люков и с охлаждающим воздухом.
Температура окружающей среды может доходить до —40 °С зимой и до + 50 °C летом. Высокая температура ухудшает охлаждение электрических машин, способствует их чрезмерному нагреву, а низкая вызывает загустевание смазки в подшипниках, отпотевание машин при установке э. п. с. в депо.
При прохождении неровностей пути колесные пары э. п. с. воспринимают значительные динамические силы (особенно при высоких скоростях движения). Эти удары, частично сглаженные системой рессорной подвески, передаются тяговым двигателям. Наиболее чувствительны они для тяговых двигателей с опорно-осевым подвешиванием, почти половина массы которых не подрессорена.
От действия динамических сил в элементах машин могут возникать трещины, изломы, повышенная выработка трущихся поверхностей, усиливаться искрение на коллекторе, слабнуть узлы соединений.
Напряжение в контактном проводе, а следовательно, напряжение, подводи мое к тяговым двигателям (и другим электрическим машинам), могут отличаться от номинального значения на 10—12%. В отдельных случаях (например, при рекуперативном торможении) напряжением на зажимах тяговых двигателей может доходить до 1,25 Uном. Заметно повышается напряжение на тяговых двигателях, связанных с боксующими колесными парами. При отрыве токоприемника от контактного провода происходит резкое снижение напряжения на тяговых двигателях, а при грозовых разрядах — его резкое повышение.
Всякое отклонение напряжения от номинального значения ухудшает работу тягового двигателя и снижает его тяговые свойства. Но особенно опасно повышенное напряжение, которое может вызвать потенциальное искрение на коллекторе и образование кругового огня, пробой изоляции обмоток, проводов, изоляции кронштейнов щеткодержателей, выводных кабелей.
При трогании или движении по затяжному подъему тяжеловесных составов или при движении с неполным числом работающих на локомотиве тяговых двигателей токи в них могут значительно превысить их допускаемые значения. Такие даже кратковременные перегрузки могут вызвать повышенное искрение под щетками, нару шить коммутацию, а при определенных условиях привести к образованию кругового огня на коллекторе.
Круговой огонь может возникнуть также и в результате быстрого нарастания тока при переходных процессах, протекающих в тяговых двигателях. Наиболее опасны переходные ре жимы, возникающие в результате образования кругового огня на соседнем параллельно включенном двигателе или при пробое плеча выпрямительной установки.
При боксовании колесной пары частота вращения якоря тягового двигателя резко возрастает. При этом возникают большие центробежные силы, которые могут вызвать повреждение валов якорей тяговых двигателей, ослабление или повреждение якорных бандажей. Кроме того, при повышенной частоте вращения якоря заметно усиливается искрение под щетками, ухудшается коммутация машины и создаются условия для возможного возникновения кругового огня на кол лекторе. В момент восстановления сцепления боксующей колесной пары частота ее вращения (а, следовательно, и связанного с ней якоря двигателя) мгновенно уменьшается. При этом за пас кинетической энергии вращающего ся якоря превращается в удар, пере дающийся на зубчатую передачу, вал якоря, подшипники и другие элементы двигателя, вызывая их повышенный износ, а иногда и поломку.
2.8 Технология ремонта ТЭД НБ-520
Разборка тягового электродвигателя. Поступивший в ремонт тяговый электродвигатель в собранном состоянии обмывается в моечной установке раствором моющего средства «Лабомцд-101» или «Лабомцд- 102» и др. с предохранением от попадания грязи и моющего средства внутрь электродвигателя. Разрешается производить механическую очистку электродвигателя при помощи скребков, обтиркой и т. д.
Разборку электродвигателя рекомендуется производить на поточной линии, оснащенной специальным оборудованием и транспортирующими средствами, или на стационарных разборочных стендах, оборудованных средствами механизации. При разборке производятся следующие работы.
Снимают с остова заглушки, крышки коллекторных люков. Разбирают коробку выводов, снимают крышку, отсоединяют шины, снимают планки и вывертывают пальцы.
Гидропрессовым способом спрессовывается ступица резинокордной полумуфты с конического конца торсионного вала. Снимают лабиринтное кольцо и крышку подшипника, устанавливают технологический стакан и крышку. Снимают кронштейны подвески тягового электродвигателя, крышку, манжету и упорное кольцо. Из масляной камеры втулки якоря удаляют смазку путем наклона электродвигателя или другим способом.
Далее отсоединяют шунты, подходящие к двум верхним кронштейнам траверсы. При этом следует расстопорить траверсу, для чего ее проворачивают, вынимая все щетки из окон щеткодержателей, и подкладывают их под нажимные пальцы на щеткодержателях.
Подшипниковые щиты и крышки тщательно осматривают для выявления трещин, отколов и других повреждений. Подшипниковые щиты, у которых выявлены сквозные радиальные трещины, идущие от посадочной поверхности в остов до посадочного места под подшипник, подлежат замене новыми. Все прочие трещины в подшипниковых щитах и крышках подшипников заваривают электродуговой сваркой. Сварочные швы зачищают заподлицо с основными поверхностями.
Определяя износ посадочных поверхностей подшипниковых щитов, измеряют в каждом подшипниковом щите диаметр поверхности под посадку в остов и диаметр гнезда под посадку роликоподшипника. Со стороны коллектора в подшипниковых щитах замеряют диаметр расточки под установку траверсы. Замеры посадочной поверхности производят по двум взаимно-перпендикулярным диаметрам. Средний диаметр измерения вычисляется как полусумма двух диаметров.
Определяют также износ поверхностей под крепежные болты в подшипниковых щитах измерением толщины щита в местах отверстий для болтов, крепящих щит к остову, и диаметр проходных отверстий под болты крепления щита к остову.
Измеряют размер от торца упора подшипникового щита в остов до торца упора подшипника в щит. Определяют износ поверхностей крышек подшипников и упорных колец; проверяют во внутренних крышках подшипников диаметр упорной части крышки под посадку в подшипниковый щит, в наружных крышках — диаметр посадочной поверхности в щит и диаметр проходных отверстий под болты.
Проверяют состояние лабиринтных поверхностей крышек подшипников и подшипникового щита со стороны коллектора. Разрешается оставлять без исправлений раковины в лабиринтных нитках длиной не более 3 мм каждая, при общей длине раковин на одной нитке не более 5%. При этом не должно быть совпадения раковин на двух смежных нитках лабиринта.
В подшипниковых щитах и крышках подшипников, износ которых превышает нормы, а также имеются трещины и дефекты резьбы, производят заварку или наплавку. После выполнения сварочных работ (заварка трещин, наплавка посадочных поверхностей щитов в остов, наплавка посадочных поверхностей гнезд под роликовые подшипники, наплавка лабиринтов, заварка отверстий) щиты и крышки подвергают механической обработке.
Дефектация остова. При внешнем осмотре магнитной системы остова в собранном виде особое внимание следует обращать на состояние изоляции катушек и выводов для выявления сколов, выжигов, механических повреждений изоляции, ослабление посадки катушек, дефектов сердечников полюсов.
При удовлетворительном состоянии изоляции и выводов катушек, сердечников полюсов магнитная система остова при пробегах до 2,4 млн км не разбирается, а при повреждении отдельных катушек производится замена только дефектных катушек.
Катушки полюсов проверяются на междувитковое замыкание на импульсной установке.
Тщательным внешним осмотром проверяют состояние изоляции катушек полюсов, отсутствие повреждений и выжигов покровной и корпусной изоляции. Осматривают выводы катушек полюсов; проверяют исправность изоляции шунтов; пайку наконечников шунтов и состояние контактных поверхностей наконечников.
В зависимости от пробегов в эксплуатации и дефектов по результатам дефекации определяется объем ремонта катушек полюсов:
— катушки главных полюсов, у которых выявлены повреждения изоляции или выводов, ремонтируют с полной заменой корпусной и междувитковой изоляции и выводов;
— катушки добавочных полюсов, у которых выявлены междувитковые замыкания и повреждения корпусной изоляции или выводов, ремонтируют с полной заменой корпусной и междувитковой изоляции и выводов.
Траверса со щеткодержателями. Траверса, кронштейны и накладки осматриваются с целью обнаружения в них трещин, отколов, износа гребенки и резьбы шпилек кронштейнов. Для определения необходимого ремонта траверсу разбирают, сняв соединительную шину, щеткодержатели и кронштейны. Для этого отворачивают гайки, крепящие пальцы, и снимают их с траверсы. Обод и зубья траверсы очищают от смазки, промывают в керосине и протирают чистыми сухими салфетками.
Калибрами проверяют резьбовые отверстия в траверсе и кронштейнах. Повреждения в траверсе и кронштейнах устраняют заваркой. Траверса с поврежденными зубьями подлежит замене. Места отколов и трещин в траверсе и кронштейнах разделывают под электросварку, после чего рассверливают резьбовые отверстия с негодной резьбой, срубают сварку в торце шпильки М16 кронштейна, вывертывают негодную шпильку и заменяют ее новой, срубают также негодную подкладку траверсы. Торец шпильки М16 в кронштейне обваривают кругом.
При заварке и наплавке поврежденных деталей руководствуются Инструкцией по сварочным и наплавочным работам ЦТ-336.
На станках обрабатывают все посадочные и сопрягаемые поверхности, сверлят заваренные резьбовые отверстия. При этом диаметры посадочных поверхностей траверсы, размеры ниток гребенок кронштейнов и других сопрягаемых поверхностей траверсы и кронштейнов, а также резьба должны быть восстановлены согласно чертежам новой детали. Отремонтированную траверсу, за исключением зубьев, покрывают красной эмалью ГФ-92ХС.
В гребенке кронштейнов допускается оставлять без исправлений срыв ниток не более 5% общей площади ниток. При большем износе гребенку следует восстановить элекгронаплавкой с последующей обработкой. Шпильки кронштейнов с поврежденной резьбой заменяют новыми.
Осматривают пальцы кронштейнов щеткодержателей. Пальцы, имеющие прогары прессмассы, трещины, поврежденную резьбу шпилек, заменяют. Царапины и подобные легкие повреждения поверхности изоляции пальцев устраняют обработкой шлифовальной бумагой. Калибруется и контролируется резьба М24 шпилек пальцев.
Пальцы кронштейнов щеткодержателей сушат и проверяют сопротивление изоляции каждого пальца кронштейна по отношению к корпусу. Величина сопротивления изоляции, измеренная мегомметром на напряжение 2500 В, должна быть не ниже 100 МОм. Электрическую прочность изоляции пальцев испытывают напряжением 5,5 кВ промышленной частоты в течение 1 мин. Пальцы, получившие пробой изоляции при испытании, а также имеющие сколы, трещины и выжиги или сорванную резьбу, заменяют новыми.
Дефектация якоря служит для определения состояния узлов и сборочных единиц якоря. При этом проверяется состояние лобовых частей якоря, бандажей, вала, пакета сердечника, коллектора; отсутствие выжига изоляции, железа сердечника, меди коллектора и обмотки. Бандажи и клинья крепления обмотки следует обстучать молотком массой 200 г на отсутствие ослабления бандажей и клиньев.
Очистку якоря необходимо производить техническим моющим средством «MJI-80».
Затем измеряют диаметр шеек вала под упорные, лабиринтные втулки и внутренние кольца роликоподшипников, диаметры и длину коллектора по рабочей части и петушкам.
На стендах дефектоскопии валов проверяют шейки валов под внутренние кольца подшипников и наружные поверхности внутренних колец подшипников качения. На основе результатов проверки, испытаний и измерений, а также сведений о пробегах в эксплуатации определяют объем ремонта каждого якоря.
Устраняют задиры, риски, отклонение от округлости, конусообразность и сверхдопустимый износ на шейках вала путем вибродуговой наплавки под слоем флюса в соответствии с Инструкцией по сварочным и наплавочным работам ЦТ-336 или применяя хромирование с последующей токарной обработкой до размеров новой детали либо проточку до следующего ремонтного размера. Промежуточные размеры не допускаются. Для всех ремонтных размеров должен соблюдаться допуск на обработку, как для нового вала. После восстановления наплавкой или хромированием посадочных мест под внутренние кольца роликоподшипников, упорные и лабиринтные втулки должны быть обеспечены размеры новой детали. После проточки переходные галтели и размеры вдоль оси вала должны соответствовать чертежу новой детали.
Допускается оставлять без исправления шейки вала, имеющие продольные риски, мелкие вмятины и раковины в местах посадки роликовых колец, лабиринтных и упорных втулок глубиной до 0,1 мм (не более трех) и отклонение от округлости и конусообразность в пределах норм.
Якори электродвигателей, пришедших в ремонт с пробегом до 1,2 млн км от начала эксплуатации или последнего капитального ремонта, ремонтируются без замены обмотки с пропиткой. Якори с пробегом 2,4 млн км и выше ремонтируются с полной сменой обмотки якоря.
Сборка тягового электродвигателя. Все детали тягового электродвигателя осматриваются, удаляется стружка, грязь, зачищаются заусенцы мелкозернистой шлифовальной шкуркой, детали протираются техническими салфетками.
Проходные отверстия под болты и заклепки при относительном их смещении в соединяемых деталях исправляют рассверливанием или развертыванием или заваривают и вновь просверливают. Раздача отверстий (увеличение) с помощью оправки не допускается.
Резьба болтов, гаек и отверстий для крепления полюсных сердечников, подшипниковых щитов и крышек, валов, коллекторов, фланцев щеткодержателей и кожухов проверяется резьбовыми калибрами степени точности 7Н.
Не допускается ввертывание завышенных по длине болтов или нормальных болтов в заниженные по глубине нарезки отверстия.
Посадочные поверхности подшипниковых щитов и крышек подшипников протираются технической салфеткой, смоченной в нефрасе. Цилиндрические поверхности внутренних крышек подшипника, прилегающие к подшипниковому щиту, смазывают густотертыми цинковыми белилами МА-011−1. Монтаж подшипниковых щитов и запрессовка подшипников производится в следующем порядке:
— подшипниковые узлы электродвигателя заправляются смазкой Буксол;
— трубки и подшипниковые камеры продуваются сжатым воздухом;
— масляная трубка заполняется смазкой Буксол до появления смазки в камере.
Внутренние крышки устанавливаются в подшипниковые щиты.
При подготовке роликоподшипников к запрессовке в подшипниковые щиты проверяют номера наружных обойм подшипников, протирают насухо безворсовой чистой салфеткой все поверхности роликоподшипников и посадочные поверхности подшипниковых щитов смазывают тонким слоем индустриального масла И20А, а ролики — тонким слоем смазки Буксол.
3. Экономическая часть
3.1 Производственная программа
Программа деповского ремонта участка по ремонту ТЭД НБ-520 в год берем с исходных данных Таблица 10 — Программа деповского ремонта
Серия локомотива | Количество ремонтов и технических обслуживаний | ||||
ТР — 3 | ТР — 2 | ТР — 1 | ТО — 3 | ||
ЭП 1 | |||||
ВЛ 80 С | |||||
ЧМЭ3 | |||||
3.2 Технико-производственные показатели
Таблица — Нормативы трудоёмкости ремонта ТЭД НБ 520
Серия локомотива | Норматив трудоемкости комплексной бригады | ||||
ТР — 3 | ТР — 2 | ТР — 1 | ТО — 3 | ||
ЭП 1 | ; | ||||
ВЛ 80 | ; | ||||
ЧМЭ3 | ; | ||||
Таблица — Общая трудоемкость
Серия локомотива | Трудоемкость, чел. ч | ||||
ТО-3 | ТР-1 | ТР-2 | ТР-3 | ||
ЭП 1 | |||||
ВЛ 80 С | |||||
ЧМЭ-3 | |||||
Процент участия участка в расходах по материалам и запасным частям принимаем пропорционально трудоёмкости ремонта:
(34)
где qрем — трудоёмкость данного ремонта, чел-ч;
qобщ — общая трудоёмкость данного ремонта, чел-ч.
Стоимость материалов и запасных частей на единицу ремонта определяем по долевому участию участка:
(35)
где Сед — ориентировочная стоимость материалов и запасных частей на единицу каждого ремонта, руб.;
k — процент участия данного цеха в расходах по материалам и запасным частям на единицу ремонта.
Стоимость материалов и запасных частей для участка составляет:
рублей.
3.3 План по труду
Списочное количество производственных рабочих было рассчитано в пункте 2.2 и составляет 13 чел. Управление участком по ремонту тягового электродвигателя ведет старший мастер цеха.
Средний разряд работников на участке по сведениям нормировщиков составляет 4,8.
Полученное расчётом количество производственных рабочих разбиваем согласно тарифной сетке по разрядам:
Таблица — Тарифная сетка
Разряды | |||||||||
Тарифный коэффициент | 1,14 | 1,37 | 1,63 | 1,89 | 2,12 | 2,31 | 2,50 | 2,69 | |
Часовые тарифные ставки | 42,7 | 51,32 | 61,06 | 70,8 | 79,42 | 86,53 | 93,65 | 100,77 | |
Число рабочих | |||||||||
Средний разряд рабочих определяется по формуле:
(36)
где Тм — ближайший меньший тарифный разряд по тарифной сетке;
Кср — средний тарифный коэффициент разряда рабочих;
К1 — тарифный коэффициент ближайшего меньшего тарифного разряда;
К2 — тарифный коэффициент ближайшего большего тарифного разряда.
Средний тарифный коэффициент при такой квалификации рабочих равен:
Средний разряд рабочих равен:
Составляем штатную ведомость:
Графа 1: Профессия рабочих — Слесари Графа 2: Средний тарифный разряд рабочего (4,7)
Графа 3: Списочное количество (20чел.)
Графа 4: Месячная тарифная ставка одного производственного рабочего.
Тарифная ставка одного производственного рабочего за час определяется путем интерполяции:
(37)
где Tч — часовая тарифная ставка искомого не целого разряда по цеху;
a — часовая тарифная ставка ближайшего меньшего целого разряда тарифной сетки;
b — часовая тарифная ставка ближайшего большего целого разряда;
n — число долей к целому разряду;
10 — постоянное число, показывающее число десятых долей в целом разряде.
Тогда часовая тарифная ставка равна:
рублей Месячная тарифная ставка получается умножением часовой тарифной ставки на количество рабочих часов в месяц:
Tмес= Tч•165,5 = 75,20•165,5 = 12 445 рублей В графу 4 заносят данные расчета тарифных ставок по видам ремонта для контингента рабочих цеха по формуле:
ТСТ = ЧСП • ТМЕС (38)
ТСТ = 20• 12 445 = 248 900 рублей Оклад мастера — 16 677 рублей Оклад бригадира — 15 499 рублей.
Графа 5: Определение сдельного приработка Процент дополнительной оплаты труда к тарифной ставке — 15%
Тпр = ТТРст • 0,15 (39)
Тпр = 248 900 • 0,15 = 37 335 рублей Графа 6: Средний размер премии.
А) для производственных рабочих можно принимать до 25% от сдельного приработка (от суммы граф 4 и 5 штатной ведомости) Тпрем = (Тст + Тпр) • 0,25 (40)
Тпрем = (248 900 + 37 335) •0,25 = 71 558 рублей Б) для работников с повременной оплатой труда можно средний размер премии принимать до 30% от тарифной ставки (от графы 5 штатной ведомости) ТМАСпрем = ТМАСОКЛ • 0,3 (41)
ТМАСпрем = 16 677 • 0,3 = 5003 рублей ТБРпрем = ТБРОКЛ • 0,3 (42)
ТБРпрем = 15 499• 0,3 = 4649 рублей Графа 10: Общий заработок рабочих участка по ремонту тягового электродвигателя НБ-520 за месяц получается суммирование граф 4, 5, 6.
А) Общий заработок слесарей:
ТОБЩ = Тпрем + Тст + Тпр (43)
ТОБЩ = 71 558+248900+37 335=357793рублей Б) Общий заработок бригадира и матера:
ТМАСОБЩ = ТМАСОКЛ + ТМАСПРЕМ (44)
ТМАСОБЩ = 16 677 + 5003 = 21 680 рублей ТБРОБЩ = ТБРОКЛ + ТБРПРЕМ (45)
ТБРОБЩ = 15 499 + 4649 = 20 148 рублей Графа 11: Годовой фонд заработной платы определяется умножение месячного заработка на количество месяцев в году.
А) годовой фонд заработной платы слесарей:
ТГОД = ТОБЩ • 12 (46)
ТГОД = 357 793• 12 = 4 293 516 рублей Б) годовой фонд заработной платы бригадира и мастера:
ТМАСГОД = ТМАСОБЩ • 12 (47)
ТМАСГОД = 21 680 • 12 = 260 160 рублей ТБРГОД = ТБРОБЩ • 12 (48)
ТБРГОД = 20 148• 12 = 241 776 рублей Таблица — Штатная ведомость
Наименование профессий | Тарифный разряд | Контингент | Месячный фонд заработной платы, руб | Фонд заработной платы в рублях | ||||
Тарифная ставка | Сдельный приработок | Премия | Итого за месяц | Итого за год | ||||
Производственные рабочие | ||||||||
Слесарь | 4,7 | |||||||
Итого | 4,7 | |||||||
Цеховой штат | ||||||||
Мастер | Окл | |||||||
Бригадир | Окл | |||||||
Итого | ||||||||
Всего | ||||||||
3.4 План эксплуатационных расходов
Статья 768 — текущий ремонт производственных зданий, сооружений.
Стоимость 1 м² равна 20 500 руб. Площадь участка по ремонту тягового электродвигателя НБ-520 = 150 м².
Найдем материалы, затрачиваемые на ремонт здания:
20 500•150•0,045=138 375 рублей Затраты на отопление находятся по формуле:
(49)
где Vздобъем участка ремонта, м3;
Тотколичество часов отопительного сезона (может быть принято по региону), 4320 ч;
qтсредний расход тепла в помещении участка ремонта, 30 кДж/час на 1 м³ здания;
? — коэффициент полезного действия отопительного оборудования (0,56);
Мусл.т — теплопроводность условного топлива (зависит от выбранного топлива), 540 ккал;
Цусл.т — цена одной единицы условного топлива (постоянно корректируется), 40,92 руб.
Объем участка ремонта найдем по формуле:
Vзд = Sуч • Нуч (м3), (50)
где Sуч — площадь участка ремонта, 150 м²;
Нч — высота участка ремонта, 8 м;
Vзд = 150 • 8 = 1200 м³
Затраты на электроэнергию включают в себя затраты на освещение участка ремонта и силовую энергию, которую используют при работе оборудования:
Еэл = Еосв + Есил, (51)
где Еосв — затраты на освещение, руб.;
Есил — затраты на электроэнергию для работы оборудования, руб.
Затраты на освещения:
Еосв = ЦкВт/ч • Sуч • 0,016 • 1950 • 0,8 • 1,2, (52)
где Цквт/ч — цена одного квт/ч (2,71 руб.);
Sуч — площадь участка ремонта, м2;
0,016- норма освещенности одного квадратного метра площади;
1,2 — коэффициент, учитывающий потери электроэнергии в сети;
1950 — годовое количество часов осветительной нагрузки, ч;
0,8 — поправочный коэффициент спроса электроэнергии.
Еосв = 2,71 • 150 • 0,016 • 1950 • 0,8 • 1,2 = 12 175 рублей Затраты на электроэнергию:
Есил = Цквт/ч • ?Nэл. • 0,8 • 1,2•1950, (53)
где ?Nэл — суммарная мощность оборудования, кВт/ч (из технического паспорта оборудования — 8 кВт/ч);
0,8 — коэффициент загрузки оборудования;
1,2- коэффициент, учитывающий потери электроэнергии в сети.
Есил = 2,71 • 15. • 0,8 • 1,2 • 1950 = 76 096 рублей Еэл = 12 175 + 76 096 = 88 271 рублей Затраты на бытовую, хозяйственную, техническую воду можно определить по расчетной формуле:
Евод = Цвод • (Мб.хоз + Мтех) (54)
где Цвод — цена одного кубического метра воды (17 руб.)
Мб.хоз — расход воды на хозяйственно-бытовые нужды, м3;
Мтех — расход воды на технические нужды, м3 (обмывку деталей).
При расчете учитываются нормы расхода воды на хозяйственно-бытовые и технические нужды:
Расход воды на хозяйственно — бытовые нужды, м3:
Мб.хоз = 0,065 • Асп • 305 • 0,8 • 1,1 (55)
где 0,065 — норма расхода воды на одного чел. в сутки на хозяйственно-бытовые нужды (65 л/чел, то есть 0,065 м3/ч);
Асп — расчетная списочная численность рабочих на участке ремонта, (20 чел.);
305 — количество рабочих дней в году;
0,8- поправочный коэффициент потребности воды;
1,1- коэффициент, учитывающий утечку воды.
Мб.хоз = 0,065 • 20 • 305 • 0,8 • 1,1 = 348 м³
Расход воды на технические нужды:
Мтех = 0,2 • Угод • 0,8 • 1,1 (56)
где 0,2 — норма расхода воды на обмывку одной детали, м3/дет;
Угод — программа ремонта в цехе (240 тяговых электродвигателей в год);
Мтех = 0,2 • 240 • 0,8 • 1,1 = 42 м³
Евод = 17 • (348 + 42) = 6630 рубля Статья 761 — расходы по охране труда и производственной санитарии планируются в размере 5% от фонда заработной платы производственных рабочих.
2 389 860 • 5% = 119 493 рубля Статья 798 — подготовка кадров и выплаты, связанные с ней, принимаются 0,1% от общего фонда зарплаты производственных рабочих данного участка ремонта.
4 293 516 • 0,1% = 4293 рублей Статья 801 — предварительный осмотр и медицинское освидетельствование работников железнодорожного транспорта, принимается 0,1% от общего фонда заработной платы производственных рабочих данного участка ремонта.
4 293 516 • 0,1% = 4293 рублей Статья 771 — расчет амортизационных отчислений. Сумму амортизационных отчислений определяют по одному или двум показателям в зависимости от сферы производства:
на капитальный ремонт основных производственных фондов;
на полное их восстановление.
Амортизационные отчисления определяются исходя из их балансовой стоимости и установленных норм амортизационных отчислений.
Нормы отчислений на полное восстановление зданий в среднем — 3,9%, оборудования — 7,9%. Для расчета амортизационных отчислений следует заполнить таблицу Таблица — Расчёт амортизационных отчислений
Наименование | Балансовая стоимость, руб | Норма амортизационных отчислений, % | Сумма амортизационных отчислений | |
Здания и сооружения | 3,9 | |||
Стоимость оборудования | 12,8 | |||
Инструмент, приспособление, инвентарь | ||||
Итого | ; | ; | ||
Балансовая стоимость здания = S уч * Z
Z — Стоимость 1 м² равна 11 500 (руб)
S уч — площадь цеха Балансовая стоимость здания =150*11 500=1725000 (руб)
3.5 Основные и общехозяйственные расходы
Таблица — План расходов участка ремонта
№ статей расходов | Наименование статей расходов | Программа ремонта | Контингент | Элементы затрат | Всего затрат | |||||||||
Годовой фонд зарплаты | Отчисления на соц. нужды | Материалы | Отопление | Электроэнергия | Вода | Амортизация | Капитальный ремонт | Прочие расходы | ||||||
Прямые расходы по видам работ и местам возникновения затрат | ||||||||||||||
Ремонт тягового подвижного состава | ||||||||||||||
Отчисления на социальные нужды производственного персонала | ||||||||||||||
Итого | ||||||||||||||
Расходы общие для всех мест возникновения затрат и видов работ | ||||||||||||||
761 (461) | Охрана труда и производственная санитария | |||||||||||||
765 (469) | Содержание и эксплуатация оборудования | |||||||||||||
768 (463) | Текущий ремонт зданий и сооружений | |||||||||||||
771 (465) | Амортизация основных производственных средств | |||||||||||||
Итого | ||||||||||||||
Общехозяйственные расходы | ||||||||||||||
785 (485) | Содержание цехового аппарата управления | |||||||||||||
785 (497) | Отчисления на социальные нужды цехового аппарата управления | |||||||||||||
798 (479) | Подготовка кадров и выплаты, связанные с ней | |||||||||||||
Медицинский осмотр и освидетельствование | ||||||||||||||
Итого | ||||||||||||||
Всего | ||||||||||||||
3.6 Себестоимость единицы ТЭД НБ-520
Себестоимость продукции является одним из качественных показателей работы предприятия. Этот показатель дает возможность оценить не только работу, но и качество управления предприятием, в конечном счете.
Себестоимость ремонта одного ТЭД НБ-520 составляет:
Сед = =22 759 рублей Итого себестоимость единицы ремонта ТЭД НБ-520 составит 22 759 рублей.
Себестоимость ремонта и эксплуатационной работы зависит от многих факторов: объёма и стабильности работы организации, условий труда, количества и квалификации рабочих, условий цен на материалы, электрическую энергию, зарплату и прочее.