Композиционные абразивные материалы
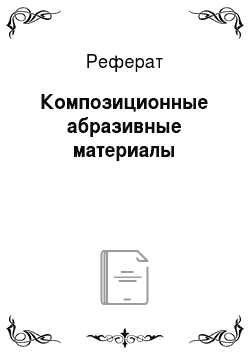
В наших экспериментах для проведения алюмотермического процесса приготавливалась шихта из кварцевого песка, порошка алюминия и нефтяного кокса по принятому стехиометрическому соотношению. Использовался кварцевый песок Орловского месторождения, отвечающий нормативно-технической документации, утвержденной в установленном порядке, с содержанием Si02 не менее 99,1%, РегОз не более 0,25%. Порошок… Читать ещё >
Композиционные абразивные материалы (реферат, курсовая, диплом, контрольная)
За рубежом и в России ведутся работы по созданию новых композиционных абразивных материалов на основе карбида кремния и корунда. При этом в традиционную шихту, используемую для получения карбида кремния по реакции.

добавляют металл алюминий, и тогда идет реакция.

Реакция (4.4) протекает с выделением теплоты в 300 кДж, или 2 квт ч на 1 кг получаемого SiC, что позволяет реализовать энергетически более выгодный процесс получения абразивного материала. Кроме того, отсутствие при прохождении реакции (4.4) оксида углерода СО делает процесс экологически более чистым, образование единой двухфазной системы SiC — АЬОз, представляющую собой совокупность множества зерен из карбида кремния, распределенных в матрице из корунда. Такая композиция, очевидно, удобна для использования ее при шлифовании, поскольку при разрушении зерна такой структуры локализуется на границе фаз, составляющих композицию, что должно обеспечивать повышение прочности зерна [60].
В наших экспериментах для проведения алюмотермического процесса приготавливалась шихта из кварцевого песка, порошка алюминия и нефтяного кокса по принятому стехиометрическому соотношению. Использовался кварцевый песок Орловского месторождения, отвечающий нормативно-технической документации, утвержденной в установленном порядке, с содержанием Si02 не менее 99,1%, РегОз не более 0,25%. Порошок алюминиевый марки АПВ, отвечающий ТУ 48−5-152−78. Нефтяной кокс малосернистый (ГОСТ 22 898−78) с содержанием активного углерода 80−85%. В качестве материала для устройства нагревателя (керна) применялся возвратный керновый хорошо прографитированный материал (с производственных печей) крупностью 0−30 мм.
Процесс осуществляли в крупнолабораторной печи сопротивления мощностью 160 кВт. Рабочая длина печи 1300 мм, ширина 1100 мм. Питание печи — от батареи трансформаторов типа ОСУ 100/05, регулировка напряжения — автотрансформатором АОМК 250/05.
Контроль температуры в реакционной зоне печи осуществлялся пирометром с помощью специальной визуальной трубы.
Полученные продукты отделяли от слоев, подвергшихся частичному разложению, и от полупродуктов. Из отсортированного материала приготавливали пробы для испытаний.
Подготовку проб для сравнительных испытаний получаемых продуктов производили методом сухого измельчения. Исходный продукт после ручной разбивки до кусков размером минус 100 мм дробили в щековой дробилке при разгрузочном зазоре 5 мм с последующей классификацией на плюс 5, минус 5 мм. Оставшиеся непродробленные после трехкратного измельчения частицы крупностью 5 мм и материал крупности минус 1,25 мм, представляющий собой, в основном, полупродукты, удалялись. Из материала минус 5 мм высевалась фракция — 1600 -т- 1250 мкм, по которой выполнялся анализ продуктов.
Получаемые продукты подвергали химическому, рентгеноструктурному, микроскопическому, микрорентгеноспектральному анализам. Определяли микромеханические характеристики, прочность единичных зерен, разрушаемость, режущую способность, эксплуатационные свойства зерна в шлифинструмейте.
Химический анализ продуктов проводился, но методикам государственного основного стандарта, разработанного применительно к абразивным материалам. Пробы в виде монолитных кусков или сыиучей массы дробилки перемешивали, сокращали квартованием до 10 — 15 г, доводили в ступке Абиха до минус 100 мкм, отмагиичивали и подвергали химанализу. При выполнении анализа в пробах определяли содержание поверхностных примесей алюминия (А1), свободного углерода (Ссв), суммы кремния и его оксида (Si + SiCb), оксида железа (Ре20з), а также суммы карбида кремния и оксида алюминия (SiC + + АЬОз), с последующим определением содержания SiC и АЬОз.
Рентгеноструктурный анализ проб продукта проводился фотометодом на аппарате УРС-55 в медном, фильтрованном излучении, в камере Дебая. Качественный состав исследуемых объектов устанавливался, но эталонным рентгенограммам и рентгенометрическим определениям. Для количественного анализа использовался метод гомологических пар. Эталонные смеси готовили из порошков: (SiC III + ctАЬОз); (SiC II + а-АЬОз); (Р—SiC + а—АДОз) через каждые 10% ог 10 до 90% содержания a-АЬОз в смесях.
Исследования микроструктуры продукта проводили на микрошлифах, приготовленных на чугунном притире с применением алмазных паст от ACM 20/14 до ACM 1/0. Дальнейшие исследования микроструктуры и фотографирование образца проводилось на микроскопах МИМ-8 и ПМТ-3 при увеличении 500х.
Микрорентгеноспектральный анализ проводился на отечественном микроанализаторе МАР-2 по точкам с набором информации об интенсивности характеристического рентгеновского излучения в каждой в течение 10 с при ускоряющем напряжении 25 кВ токе зонда 0,50 мА. В качестве эталона были использованы металлический алюминий и карбид кремния.
Физико-механические характеристики испытуемых образцов определяли с помощью разработанных нами приборов и методов контроля шлифматериалов.
На лабораторной печи сопротивления (обычно применяемой для получения карбида кремния) выполнено 24 печекомпании (плавки). Из них 7 с изменениями содержания в шихте алюминия, 17-е изменениями габаритов реакционной зоны, электрорежима на получение больших количеств продукта на приготовление шлифматериалов.
В реакционную зону печи загружали шихту, приготовленную из кварцевого песка, нсфяного кокса и порошка алюминия, в теплоизоляционные зоны — обычную возвратную шихту, образующуюся при получении карбида кремния. Подача тепла в реакционную зону осуществлялась от керна-нагревателя.
Образовавшиеся в печи продукты представляли собой прочный блок, который целиком извлекали из печи и разбивали на куски 50 100 мм, отдельные куски крупностью 200 — 300 мм вынуждены были раздавливать на прессе, при этом разрушение их происходило при усилиях свыше 300 т. После крупного дробления куски визуально рассортировывали на полупродукт низкотемпературных зон, шлаковидный, плотный и металлизированный материалы. Из-за неоднородности кусков сортировка была весьма условной. Шлаковидный и плотный материал считали продуктом.
Семь плавок были проведены с целью выявления возможности осуществления алюмотермического процесса в керновой печи сопротивления, влияния содержания алюминия в шихте на происхождение реакций и получаемые продукты.
Состав реакционной шихты соответствовал массовому содержанию алюминия в шихте 33, 26 и 18%, и был рассчитан на содержание в получаемом продукте 63, 56 и 46% электрокорунда. Габариты загрузки печи, одинаковые для этой группы плавок, показаны на рис. 4.4. При загрузке печи в боковую часть на расстоянии 7 — 8 см от поверхности керна устанавливали вольфрамрениевую, а на расстоянии 23 — 15 см — хромельалюминиевую термопары. В реакционную зону загружали 500 — 600 кг шихты.

Рис. 4.4. Поперечный и продольный разрезы засуженной печи сопротивления: 1,2- термопары; 3 — реакционная шихта; 5 — рабочий электрод; 6 — керн При обычном электронагреве шихты для получения карбида кремния в этой же печи температура 1600 °C в 7 — 8 см от керна может быть достигнута за 4 — 5 часов, что соответствует скорости подъема температуры порядка 4−8 °С/мин. При содержании в шихте 33% алюминия температура в 7 — 8 см от керна (рис. 4.5) поднялась от 200 до 1700 °C за 5 — 6 минут, т. е. скорость подъема температуры составила 280 — 240 °С/мин. Такой скачкообразный подъем температуры мог быть обусловлен лишь дополнительным к электроэнергии выделением тепла в реакционной зоне за счет экзотермической реакции восстановления кремнезема алюминием.

Рис. 4.5. Характер изменения температуры в реакционной зоне печи: расстояние от поверхности керна 7 — 8 см • -содержание А1 в шихте 33%; о — содержание А1 в шихте 26%; А — содержание А1 в шихте 18%; расстояние от поверхности керна 13−15 см:? — содержание А1 в шихте 33%; X — содержание А1 в шихте 18%.
Меньшему содержанию алюминия в шихте (18%) соответствовала и меньшая (40 — 50 °/мин) скорость подъема температуры в той же точке реакционной зоны.
Такой же характер подъема температуры имел место и в 13 — 15 см от поверхности керна. Меньший интервал времени между началом подъема температуры в точках установки термопар наблюдали при большем содержании алюминия в шихте. Таким образом, визуально наблюдаемые на печи явления, зафиксированный скачкообразный подъем температуры в реакционной зоне печи, корреляция между количеством алюминия и скоростью нагрева шихты однозначно подтверждают прохождение экзотермической реакции восстановления кремнезема алюминием.
В период разогрева реакционной зоны и интенсивного газовыделения на плавках с шихтой, содержащей 33% алюминия, из-за бурного протекания процесса мощность снижали на 30 — 60 % при содержании 26 и 18% алюминия — сохраняли на достигнутом уровне или продолжали медленно повышать.
В зависимости от состава шихты, внешнего вида продукта предыдущих плавок и хода процесса печь отключали после выбора электроэнергии 530 — 670 кВт/ч.
Поперечный разрез продуктов плавки в печи показан на рис. 4.6. Поверхностный слой I представлял собой сыпучую шихту, характерную для плавок на карбид кремния, далее (в четком соответствии границам реакционной зоны при загрузке печи) расположен слой 2 зеленовато-серого цвета, переходящего в серый, весьма прочный. Следующий слой 3 — непрерывный переход от слоя 3 к слою 4 серого цвета, очень прочный. Слой 4 — продукт шлаковидного типа, темно-серого цвета, тяжелый, с металлическим звуком при уларе, с включениями (особенно в подине) очень плотного материала. Между слоем 4 и керном 6 расположена плотная темная «корка» 5 из кристаллов, похожих на карбид кремния, и корольков, сравнительно легко отделяющихся от остальной массы материала. Толщина всех этих слоев по длине печи разная, без геометрически правильных границ. В образовавшихся блоках имелись разнообразные полости и раковины.
Химические и рентгеновские исследования показали (табл. 4.6): все объекты в зонах образования продукта и полупродукта содержат SiC, АЬОз, Al, Si, SiCb, С. В некоторых пробах обнаружен A1N. Во всех без исключения пробах оксид алюминия находится в виде аAI2O3. Карбид кремния представлен, как правило, смесью кубического (Р—SiC) и гексагонального SiC. По полученным данным кусковые пробы продуктов алюмотсрмичсского процесса содержали не менее 73% композита (SiC + АЬОз).

Рис. 4.6. Поперечный разрез отплавленной печи: 1 — теплоизоляционная шихта; 2 — слой зеленовато-серый, переходящей в серый, плотноспеченный; 3 — непрерывный переходящий от слоя 3 к слою 4, серый, весьма плотный; 4 — шлаковидный, темно-серого цвета, с включениями очень плотного материала (7−8 см); 5 — полость (3 — 10 см); 6 — керн Из анализа микроструктуры и по данным микрорентгеноспектральный исследований следует, что продукт представляет собой материал с мелкозернистой двухфазной структурой (размер фаз от 2 до 40 мкм) (рис. 4.7, а): серая фаза — корунд с содержанием А1 — 53,34% и Si — 0,12%; светлая фаза — карбид кремния с содержанием Si — 68,71% и А1- 2,75%. Области мелкозернистой двухфазной структуры составляют в общей массе продукта от 30 до 80%; до 10% составляют области крупных образований корунда и карбида кремния, в которых размер фаз колеблется от 50 до 200 мкм и более (рис. 4.7, б).
Микроструктура исследованных образцов неоднородна. Среди мелкои крупнодисперсных двухфазных систем карбида кремния и корунда (рис. 4.8) имеются участки различных включений.
Таблица 4.6.
Результаты рентгеноструктурного и химического анализов кусков продуктов синтеза, %
В печи. | Фазовый состав отмытой пробы. | Химический состав. | ||||||||
а-АБОз. | P-SiC. | SiCIl. | Si 111. | Alee. | сС8 | Si+SiO> | SiC. | ЛЬОз. | Сумма. | |
Верх-бок. | ; | ; | 2,23. | 22,0. | 37,37. | 9,82. | 25,11. | 96,52. | ||
Верх. | ; | 4,10. | 2,17. | 6,13. | 29,29. | 56,81. | 98,56. | |||
Бок. | ; | 5,08. | 2,48. | 2,54. | 30,39. | 67,30. | 107,79. | |||
Низ. | ; | ; | ; | ; | 1,32. | 3,02. | 43,27. | 14,24. | 29,89. | 96,74. |
Верх. | ; | ; | 0,82. | 4,92. | 5,36. | 41,15. | 48,95. | 101,20. | ||
Бок. | ; | ; | 8,89. | 0,99. | ; | 33,84. | 61,0. | 104,72. | ||
Верх-бок. | ; | ; | 12,41. | 1,24. | 1,42. | 59.31. | 13,80. | 88,18. | ||
Верх. | 3,66. | 1,10. | 0,88. | 32,76. | 62,50. | 100,90. | ||||
Верх-бок. | 19,70. | 0,49. | 1,63. | 42,96. | 40,54. | 105,20. | ||||
Бок (серый). | ; | ; | ; | ; | ; | ; | ; | ; | ||
Бок (шлаков). | ; | ; | ; | ; | ; | ; | ; | ; | ||
Бок (монолит). | ; | ; | ; | ; | ; | ; | ; | |||
Низ. | ; | 5,92. | 0,92. | 2,53. | 36,90. | 63,47. | 108,04. | |||
Низ. | ; | 6,35. | 0,27. | ; | 31.0. | 62,11. | 99,74. | |||
Верх. | ; | ; | 22,64. | 0,90. | 11.43. | 58.59. | 0,48. | 94,06. | ||
Низ. | ; | ; | ; | ; | ; | ; | ; | ; |

Рис. 4.7. Микроструктура продукта алюмотермического синтеза: 1 — корунд; 2 — карбид кремния.

Рис. 4.8. Микроструктура образцов с отпечатками пирамиды Виккерса при Р = 100 Н, 200х: а, б — двухфазная структура образцов композиционного материала на основе SiC и АЬОз; в — крупнозернистые двухфазные системы SiC и АЬОз; г — отпечаток пирамиды на корунде; д — отпечаток пирамиды на карбиде кремния На рис. 4.9 приведен график зависимости диагонали отпечатка и зоны хрупкой повреждаемости от нагрузки на индентор в логарифмических координатах для областей двухфазной системы карбида кремния и корунда.

Рис. 4.9. Зависимость диагонали отпечатка и зоны хрупкой повреждаемости от нагрузки на индентор: • - SiC; о — АЬСЬ; А — двухфазная структура образцов композиционного материала на основе SiC и а-АЬОз.
Из рис. 4.9 видно, что в исследованных образцах мелкодисперсная двухфазная структура по диагонали отпечатка индентора (микротвердости) близка к карбиду кремния и корунду, а по зоне хрупкой повреждаемости (миикропрочности) значительно отличается от них (за исключением отдельных участков поверхности) в сторону большой трещиностойкости. Поскольку характер этих зависимостей при всех нагрузках одинаковый, то сопоставление исследуемых образцов материала целесообразно производить при одной и той же нагрузке, например, ЮН.
Результаты такого сопоставления приведены в табл. 4.7.
Таблица 4.7.
Сравнительные микромеханические показатели исследованных образцов
Характеристика образцов. | Вид фазового состава. | М и кротвердоегь Н, ГПа. | Микропрочность а, ГПа. |
SiC. | 31,0. | 2,3. | |
АЬОз. | 22,000. | 2,0. | |
Композиционный материал. | Двухфазная структура. | 23,0 — 32,0. | 4,5−5,9. |
Светлая фаза. | 30,0. | 2,1. | |
Темная фаза. | 20,0. | 1,7. |
Таким образом, анализ результатов испытаний показывает, что двухфазные структуры, представляющие собой композиционный материал из карбида кремния и корунда, по микротвердости близки к SiC, а по микропрочности значительно превосходят карбид кремния и корунд. По всей видимости, эта двухфазная структура имеет большую пластичность и гасит трещины при их движении. Например, на некоторых образцах трещины в районе отпечатка индентора не образуются даже при нагрузке 10 Н. В то время как на большинстве высокотвердых материалов, в том числе и на алмазе, они появляются при нагрузках 0,20 — 0,40 Н. Более крупнозернистые двухфазные системы SiC и аАЬОз по сравнению с мелкозернистыми имели более низкую трещиностойкость.
Физико-механические характеристики продуктов плавок, выполненных с разным содержанием алюминия в шихте, исследовали также по пробам узких фракций, полученных рассевом измельченных продуктов (табл. 4.8).
Из табл. 4.8 видно, что большему содержанию алюминия в исследованных пределах соответствует получение более качественного шлифматериала.
Для оценки возможности изготовления абразивного инструмента из композиционного материала в лабораторных условиях изготавливали образцы-«восьмерки», на которых определяли прочность при разрыве и твердость; для оценки шлифующей способности инструмента из композиционного материала в сравнении с инструментом из карбида.
Л) прессованное тело, по форме напоминающее цифру «8» кремния и электрокорунда изготавливали шлифовальные круги ПП 250×20×76 и ПП 70×50×20 на керамических и бакелитовых связках.
Таблица 4.8.
Сравнительные микромеханические и эксплуатационные характеристики проб шлиф материала в, полученных из шихты с содержанием алюминия 33, 26, 18%
Содержание в шихте алюминия, %. | Микротвердость Н, ГПа. | Микропрочность а, ГПа. | Разрушаемость (хрупкость), %. | Прочность единичных зерен, Н. | Относительная режущая способность. |
23,0−27,0. | 2,3−4,8. | 31,5. | 48,0. | i, 6. | |
20,5 — 22,5. | 2,9 — 3,3. | 34,0. | 42,0. | 1,3. | |
22,4 — 29,0. | 2,0 — 3,3. | 39,0. | 40,0. | 1,0. |
Образцы-«восьмерки» и шлифовальные круги готовились параллельно из всех вышеперечисленных материалов.
Заформованные изделия подвергались термической обработке в лабораторной печи и бакелизаторе по режимам, принятым для обычных абразивных изделий.
После визуального контроля и отбраковки по внешнему виду негодных образцов и кругов проверяли прочность и твердость готовых изделий.
Прочность образцов-«восьмерок» при разрыве определяли на испытательной машине УММ-5 по общепринятой методике, прочность кругов на разрыв — на стенде АИП-400 согласно ГОСТ 12.3.026−82.
Твердость образцов и шлифкругов — на пескоструйном приборе модели 910 в соответствии с ГОСТ 18 118–79.
Рецептура изделий для композиционного материала была аналогичной серийному инструменту с учетом различия материалов по плотности.
Заданная структура — 6 и 7, содержание связки в массовых долях на 100 массовых долей зерна:
- — для связки К 5 — 9,5 и 17,5;
- — для связки К 10 — 24,5 и 34,0;
- — для связки К 3 — 30,0 и 17,0;
- — для бакелита 9,0 — 10,9 и 18,6 — 20,3.
Анализ полученных результатов показал, что образцы из исследуемого материала по своим свойствам ближе карбиду кремния, чем корунду.
Установлено следующее:
- — материал может применяться при изготовлении абразивных изделий на керамической и бакелитовой связках соответственно существующей технологии их изготовления;
- — по физико-механическим свойствам изделий на керамической связке материал сравним с карбидом кремния;
- — изготовление абразивных изделий из композиционного материала возможно по рецептуре для карбидкремниевых изделий на керамической связке К 10 и по рецептурам для карбидкремниевых и электрокорундовых изделий на бакелитовой связке при соответствующей корректировке их в связи с различием материалов по плотности;
- — проведены исследования эксплуатационных свойств шлифзерпа в абразивном инструменте ПП 250×20×76 и ПП 70×50×20 при обработке стали ШХ-15, чугуна и титановых сплавов. Установлено, что шлифующая способность кругов из полученного продукта на 30% выже, чем у аналогичных из карбида кремния и электрокорунда;
- — исследования выявили перспективность создания абразивного материала на основе корунда и карбида кремния. Дальнейшую работу следует проводить в направлении исследований зависимостей качества получаемого продукта от состава шихты, температурно-временных условий проведения процесса, выбора (создания) печного агрегата для реализации алюмокарбовосстановительного процесса с получением продукта стабильного состава, с широкой оценкой эксплуатационных свойств и экономической оценкой целесообразности разработки технологии производства.
В этом плане представляют большой интерес исследования возможности применения новых технологий физико-технической обработки при производстве абразивных материалов и шлифовального инструмента, в частности, микроволновой.