Наночастицы и нанопорошки
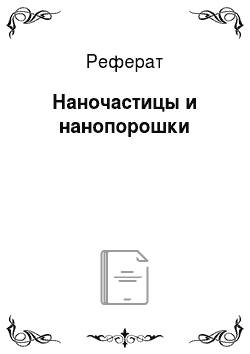
Можно получать порошки при помощи электрического взрыва проволочек. Известно, что при пропускании через относительно тонкие проволочки импульсов тока плотностью 104—106А/мм2 происходит взрывное испарение металла с конденсацией его паров в виде частиц различной дисперсности. В зависимости от состава среды, в которой протекает процесс, может происходить образование металлических частиц (инертные… Читать ещё >
Наночастицы и нанопорошки (реферат, курсовая, диплом, контрольная)
Мир наночастиц велик и разнообразен. Они могут быть изолированными или окруженными газообразной, жидкой или твердой средой; иметь равноосную форму, близкую к сфере или многограннику; форму чешуек, стержней, колец и различных комбинаций этих структур. Их находят в космосе, во льдах Гренландии, минералах, органических и биологических материалах и живых организмах. Они могут непреднамеренно создаваться человеком в результате производственной деятельности (при сжигании топлива, электродуговой и лазерной сварке, в химико-технологических и биотехнологических процессах и др.) или конструироваться и производиться специально.
Термин наночастща применяется для более крупных, чем кластеры агрегатов атомов, обычно при описании свойств металлов и углерода. Основу большинства наноматериалов составляют индивидуальные, изолированные наночастицы.
Перечислим и кратко охарактеризуем наиболее распространенные способы искусственного синтезирования и выделения наночастиц из нарабатываемого продукта. Вес их можно объединить в три группы: физические, химические и биохимические. Иногда используют и различные комбинации этих методов.
Наиболее просты и производительны методы распыления струи расплава жидкостью или газом. Реализовано множество схем с соосными потоками расплава и распыляющей среды, направленными иод углом друг к другу, с центробежным распылением вращающимися головками и электродами (рис. 3.2.1) и др. В качестве диспергирующих сред применяют малоаюгивные или инертные газы: азот, аргон и др. или жидкости: воду, спирты, ацетон и т. д.
Этими методами обычно получают порошки металлов и сплавов с размерами частиц -100 нм. При необходимости получения частиц с размерами в единицы — десятки нанометров используют метод двойного распыления, в котором.
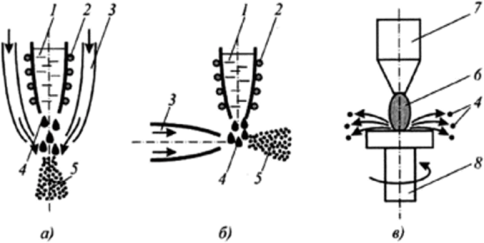
Рис. 3.2.1 Схемы получения нанопорошков методом распыления жидкого расплава: а — соосный потоком инертного газа; 6 — перпендикулярным потоком; в
- — в электрической дуге на вращающемся электроде; 1 — расплав; 2 — нагреватель; 3
- — инертный газ; 4 — капли расплава; 5 — диспергированный материей; 6 — электрическая дуга; 7 — неподвижный электрод; 8 — вращающийся электрод

Рис. 3.2.2 Схемы установок для получения нанопорошков методом испарения-конденсации: 1 — инертный газ; 2 — электропечь: 3 — нагреватель: 4 — сырье; 5 — поток пара; 6 — охлаждаемый вращающийся барабан: 7 — скребок; 8 — нанопорошок; 9 — контейнер; 10 — корпус: II — плазмотрон: 12 — струя птзмы; 13 — вращающаяся тарелка
расплав сначала насыщают иод высоким давлением растворимым газом, а затем разбрызгивают его и диспергируют нерастворимым. Быстрое охлаждение капелек приводит к взрывообразному выделению раствореннот газа и их разрушению на более мелкие частицы [3].
Другая часто используемая техника — испарение-конденсация материала (рис. 3.2.2).
Интенсивный нагрев и испарение могут обеспечиваться плазменной струей, лазерным пучком, электрической дугой, электрическим взрывом проводника. Охлаждение и конденсация пара с образованием наночастиц могут происходить в вакууме, среде инертного газа, а также на твердой или жидкой подложке. В зависимости от конкретной реализации и режимов можно получить порошки различных металлов и сплавов с размерами частиц 10… 100 нм.
Общими достоинствами перечисленных физических методов являются высокая производительность, широкий диапазон материалов, которые могут быть диспергированы, недостатками — загрязненность продукта (особенно кислородом), большой разброс размеров получаемых частиц, необходимость специального оборудования. Отчасти эти недостатки компенсируются в вакуум-сублимационной технологии, заключающейся в растворении обрабатываемого вещества в подходящем растворителе, замораживании раствора и последующей его возгонке в вакууме. В результате получаются гранулы из слабосвязанных наночастиц растворенного вещества.

Рис. 3.2.3 Схемы мельниц для тонкого механического измельчения сырья: а — вращающаяся шаровая мельница, размалывающая продукт падающими шарами: б — вибромельница, размалывающая продукт пульсирующими шарами: в — аттрактор, истирающий продукт вращающимися папьцами; г — струйная мельница, измельчающая продукт «во встречных пучках»: д — дезинтегратор, измельчающий продукт вращающимися навстречу друг другу' пальцами: 1 — мающие шары или пальцы; 2 — сырье.
Не менее распространены методы механическою измельчения твердых тел. Они осуществляются в мельницах различных типов: шаровых, планетарных, струйных, вихревых, вибрационных, дезинтеграторах, атгрикторах (рис. 3.2.3).
В современном машиностроении широко используются готовые изделия, полученные из мелкодисперсных порошков методом спекания (порошковая металлургия). По такой технологии изготавливают режущие пластины, сверла, метчики и другой режущий инструмент, а также функциональные изделия машин, например шатуны двигателей внутреннего сгорания. Методами порошковой металлургии изготавливают и сортовые стали и сплавы, из которых путем механической обработки, изготавливают готовые изделия. Такие технологии позволяют получить равномерную мелкозернистую структуру материала, что значительно повышает физико-механические и эксплуатационные свойства изделия. Под порошком при этом понимают совокупность находящихся в соприкосновении твердых частиц небольших размеров — от нескольких нанометров до тысячи микрометров.
При изготовлении наноматериалов используют ультрадисперсные порошки с размерами частиц не более 100 нм, которые подвергаются спеканию, горячему или холодному прессованию и др. с целью получить объемной изделие. При этом количество пор должно быть сокращено до минимума и сохранена наноструктура исходного порошка.
Методы получения порошков, которые можно разделить на химические и физические представлены в табл. 3.2.1.
Основные методы получения порошков для изготовления наноматериалов
Таблица 3.2.1
Метод. | Вариант метода. | Материалы. |
Фишческие методы | ||
Испарение и конденсация. | В вакууме или в инертном газе В реакционном газе. | Zn. Си, Ni. Al, Be. Sn. Pb. Mg. Ag. Cr. MgO. Al, 0, Y:0, ZiO, SiC. TiN. AIN. ZrN. NbN. Zr02,. A12Oj, TiO,. |
Высокоэнергстичсскос разрушение. | Измельчение Детонационная обработка Электрический взрыв. | Fe-Cr, Be. Al A". TiC, Si, N4, NiAl, TiAl, AIN. BN, SiC, TiC, Fe. алмаз Al, Cd, A1 >Oj, Ti02 |
Химические методы | ||
Синтез. | Плазмохимический Лазерный Термический Самораспространяющийся вмеокотемпературный Мсханохимический Электрохимический Растворный Криохимичсский. | TiC, TiN, Ti (C, N), VN, AIN, SiC, SijN4, BN. w. SiiN4. SiC. Si?N4-SiC. Fe. Cu. Ni. Mo. W. BN. TiC. WC-Co SiC. MoSi:, AIN. TaC. TiC, TiN, NiAl, TiB, Fc-Cu, W-Cu VC, CeO,. Zi02, WB4 Mo;C. BN. TiB;, SiC Ag. Pb. Mg. Cd. |
Термическое разложение. | Конденсированные прекурсоры Газообразные прекурсоры. | Fe, Ni, Co, SiC, SijN4, BN, AiN, ZrO>, NbN TiB2, ZrB2, BN. |
Разделение методов на химические и физические носит условный характер. Химические методы более универсальны и позволяют достигать большую производительность. При использовании физических методов легче осуществляется управление размерами, составом и формой частиц. Большинство методов были разработаны и благополучно использовались задолго до увлечения нанотехнологиями.
Следующим является конденсационный метод. Метод основан на испарении и конденсации атомов, которые осаждаются на холодную поверхность вращающегося цилиндра с образованием нанокристаллических частиц. Различают гомогенное и гетерогенное зарождение зародышей (кластеров). Процесс происходит в среде разряженного инертного газа, обычно гелия. Основные методы получения порошков для изготовления наномагериалов.
Широкую известность и популярность приобрел метод получения объемных наноматериалов, предложенный Глейзером и др. На Рис. 3.2.4 показана схема установки Глейтера. Конденсат с поверхности цилиндра снимается специальным скребком и попадает в коллектор. Затем инертный газ откачивают и при давлении порядка 1 ГПа осуществляют предварительное, а затем при давлении до 10 ГПа — окончательное прессование порошка. В результате получаются заготовки в виде дисков диаметром 5−15 мм и толщиной 0,2−3,0 мм с плотностью до 70−90% теоретической плотности соответствующего материала.
Для нанометаллов можно достичь 90−95% теоретической плотности, для нанокерамики — до 85%, при этом размеры наночастиц могут достигать от единиц до десятков нанометров.
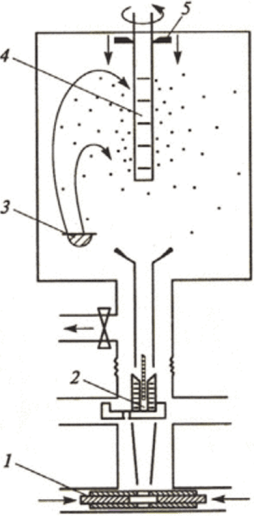
Рис. 3.2.4. Схема установки Глейтера:
- 1 —узел компактирования при высоком давлении;
- 2 —узел предварительного прессования; 3 — испаритель; 4 — вращающийся коллектор, охлаждаемый жидким азотом; 5 — скребок
При получении иаиокристалличсских оксидов и нитридов используют кислородно или азотсодержащую атмосферу. Изоляция процесса от влияния окружающей среды позволяет получать достаточно чистые наноматериалы.
Плотность наноматериалов может быть увеличена за счет повышения температуры прессования, но в этом случае может начаться рекристаллизация и размер частиц будет расти до десятков микрометров. Плотность также зависит от давления и времени прессования. Наиболее перспективно при этом динамическое прессование, которое осуществляется при высокочастотных колебаниях пуансона.
Изменяя пересыщение системы (увеличивая или снижая давление пара, например, варьируя температуру процесса), можно добиваться нужного размера частиц получаемых порошков. Наночастицы могут быть изготовлены и путем кристаллизации из эмульсий. Недостатком такого метода является образование крупных агрегатов. Во избежание агломерирования осаждение проводят в гетерогенных средах, используя стабилизацию поверхностноактивными веществами полимерного типа, с помощью которых удается, например, получать частицы Zr02 размером менее 10 им.
Производительность установки Глсйтсра ограничена невысокими скоростями испарения.
На рис. 3.2.5 показана схема установки для получения ультрадиспсрсных порошков оксидов, нитридов, карбидов методом конденсации с использованием в качестве исходных веществ металлоорганических соединений.
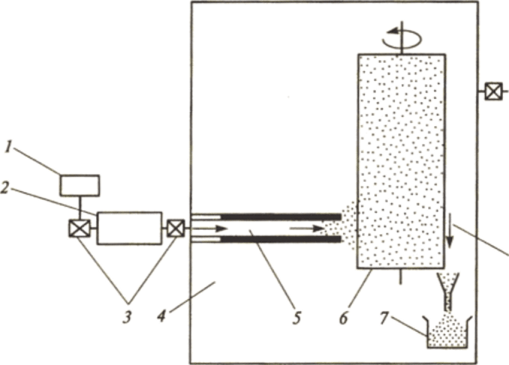
Рис. 3.2.5. Схема установки для получения ультрадисперсных порошков.
оксидов:
1 — подвод газа-носителя; 2 — источник прекурсора; 3 — регулирующие клапаны;4 — рабочая камера (давление газа 1 — 50 Па); 5 — нагреваемый трубчатый реактор; 6 — охлаждаемый вращающийся цилиндр; 7 — коллектор; 8 — скребок
В установке происходит разложение термически малопрочных металлоорганических соединений типа тетраизопропилтитана или тетра-третбутилциркония. Обогреваемый трубчатый реактор выполняет роль испарителя, в который подастся газовая смесь исходного вещества и нейтрального газа, в котором происходит гетерогенное образование наночастиц. Эта смесь из испарителя попадает в рабочую камеру и конденсируется на вращающемся охлаждаемом цилиндре, откуда счищается скребком в специальный коллектор. Установки такого типа используются в промышленном масштабе (например, американской фирмой «Nanophase Technologies Corporation» и др.) для получения ультрадисперсных порошков А120з, Ре2Оз, ТЮ2, СеС)2, Сг20з, ZnO, 1п2Оз, У2Оз и Zr02 с производительностью до 20 г/ч, которая зависит от требований, предъявляемым к размерам ультрадисперсных порошков.
Конденсационные методы позволяют получать ультрадисперсные порошки с размером частиц до нескольких нанометров, но производительность при этом очень низкая. Методы позволяют на поверхность порошка наносить тонкие полимерные пленки, предотвращающие агломерацию и коррозионное воздействие.
Рассмотрим метод высокоэнергетического измельчения, механохимический синтез. Измельчение является технологией типа «сверху-вниз», и осуществляется в мельницах, дезинтеграторах, аттриторах и других диспергирующих установках за счет разрушения крупных частиц на более мелкие. Механический размол является наиболее производительным способом получения порошков, в том числе и на наноуровне в больших количествах. Этому методу могут быть подвергнуты металлы и сплавы, композиты, керамика и другие материалы. Для размола применяют планетарные, шаровые, ротационные и вибрационные мельницы, которые позволяют получать порошки со средним размером частиц от 5 до 200 нм. На рис. 3.2.6 показаны схема аттритора. в котором за счет вращения измельчаемой шихты и шаров совмещаются ударное и истирающее воздействия, и схема вибрационной мельницы, конструкция которой обеспечивает достаточно высокую скорость движения и частоту соударения шаров.
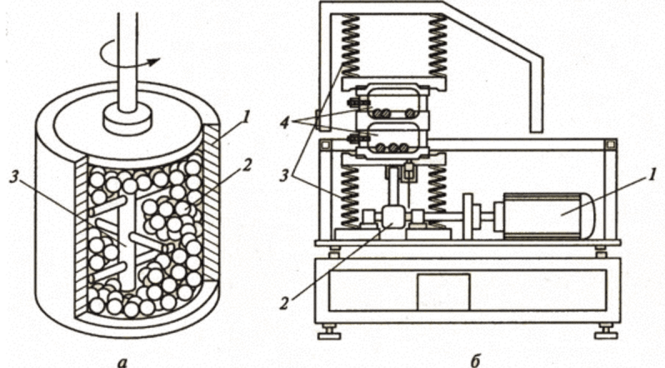
Рис. 3.2.6. Схема установок для измельчения:
a — аттритор (I— корпус, 2 — шары, 3 — вращающаяся крыльчатка); б — Вибрационная мельница (1 — двигатель, 2 — вибратор, 3 — пружины,
4 — барабаны с шарами и измельчаемой шихтой)
Для повышения производительности процесса измельчения в ряде случаев его осуществляют в условиях низких температур. Соотношение массы шаров и измельчаемой смеси обычно поддерживают в интервале от 5:1 до 40:1.
Явления агрегации частиц при измельчении и химические реакции часто осложняют диспергирование и делают его неоднозначным для прогнозирования.
Такие установки имеют определенный предел размельчения, что не позволяет получать очень тонкие порошки, поскольку наступает своеобразное равновесие между процессом разрушения частиц и их агломерацией. Даже при измельчении хрупких материалов трудно получить размер частиц ниже примерно 100 нм; частицы состоят из кристаллитов размером не менее 10 — 20 нм. Кроме того, в процессе измельчения всегда происходит загрязнение продукта материалом шаров и футеровки, а также кислородом. Мельницы, из-за наличия подвижных частей быстро изнашиваются и выходят из строя.
Для получения нанопорошков наиболее перспективными являются способы, основанные на истирании частиц между собой. Такие установки нс имеют подвижных частей, а следовательно и изнашиваемых элементов конструкции. Установка представляет собой камеру с хордально расположенными соплами для подачи энергоносителя, в качестве которого используется сжатый воздух под давлением 4−5 кг/см2. Вихревой вращающийся ноток энергоносителя создает внутри камеры локальные зоны акустических полей и осевую зону пониженного давления в которую из питателя подается исходный порошок. Готовый продукт движется по спиральным траекториям на периферию в приемники. Для создания акустических полей (ударных волн) используется генератор Гартмана — газоструйный излучатель звуковых и ультразвуковых волн. Генератор позволяет создавать акустические мощности в несколько десятков Ватт с частотами от 5 кГц до 120 кГц. Если использовать в качестве энергоносителя водород, то можно получить частоты до 500 кГц.
В результате механического истирания и механического сплавления может быть достигнута в твердом состоянии полная растворимость таких элементов, которые в обычных условиях несовместимы.
При получении наноматериалов такие установки могут быть использованы для механохимического синтеза, когда высокоэнергетическое диспергирование сочетается с образованием сплавов и соединений в результате химических реакций, которые протекают за счет взаимодействия исходных порошков, или в результате насыщения из газовой фазы. Возможны и различные смешанные варианты. Соединения и сплавы при механохимическом синтезе образуются в результате интенсивной генерации новых поверхностей и глубокого диффузионного перемешивания, а также и с разупорядочением кристаллической структуры реагентов. В результате может иметь место самопроизвольное развитие процессов.
Методом механохимического синтеза получают ультрадисперсные порошки тугоплавких соединений (TiN, TiC, TiB2, ZrN, NbC и др.) и композиционных составов типа АЬ03 + Fc (Ni, Сг), зафиксировано также образование пересыщенных твердых растворов в системах Fc — Си, Fc —Ni, Fc — Ti, Fc —Al, W— Си, Ni — A1 и др.
Высокоэнсргстичсскос измельчение и механохимический синтез имеют достаточно высокую производительность, но чистота получаемых ультрадисиерсных порошков не всегда бывает высокой и минимальный размер частиц (кристаллитов) также 01раничен.
Синтез в низкотемпературной плазме (плазмохимический синтез) производят при температурах до 6000 — 8000 К, что обеспечивает высокий уровень пересыщения, а также большие скорости реакций. Используются при этом дуговые плазмотроны, и высокои сверхвысокочастотные (СВЧ) генераторы плазмы. Дуговые аппараты обладают высокой производительностью и сравнительно недороги, но СВЧ-установки обеспечивают получение более тонких и более чистых порошков. Схема установки (изготовитель ЗАО «Наноматериалы» Черноголовка, Московская область) представлена на рис.
3.2.7. В качестве исходных материалов для плазмохимического синтеза используют хлориды металлов, металлические порошки, кремний — и металлоорганические соединения.
Плазмохимическая технология обеспечивает получение улырадисперсных порошков тугоплавких металлов (W, Мо), соединений (TiN, A1N, AI2O3, SiC, Si3N4, Ti (C, N) и др.), а также композиционных объектов типа SijN4 + SiC, TiB2 + TiN и др. в больших объемах. Из-за особенностей плазмохимического синтеза (неизотермичность процесса, возможность коагуляции частиц и др.) распределение получаемых частиц по размерам в большинстве случаев достаточно широкое.
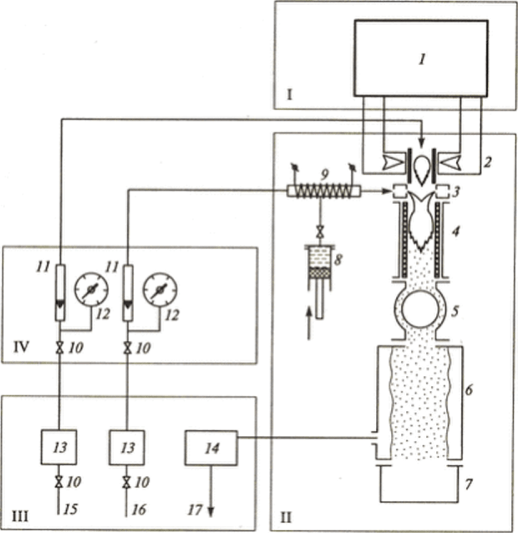
Рис. 3.2.7. Схема СВЧ-установки плазмохимического синтеза :
/ — силовое оборудование (1 —микроволновый генератор); II — основное технологическое оборудование (2— плазмотрон. 3—устройство ввода реагентов, 4 — реактор, 5 — теплообменник, б — фильтр, 7 — сборник порошка, 8 — дозатор реагентов, 9 — испаритель); III, IV — соответственно вспомогательное технологическое оборудование и блок управления (10 — вентили, 11—ротаметры. 12 — манометры, 13 — система очистки газов, 14 — скруббер, 15 — ввод плазмообразующего газа, 16— ввод газа-носителя,
17 — вывод газов)
В основе метода синтеза в условиях ультразвукового воздействия лежит эффект кавитации микроскопических пузырьков, при этом в небольшом объеме развиваются высокие давления порядка 50— 100 МН/м2 и температура 3000 К и выше, а также достигаются высокие скорости напева и охлаждения (до 1010 К/с). В условиях кавитации пузырек становится своеобразным нанореактором. Таким методом получено много нанокристалл ических (аморфных) металлов, сплавов и тугоплавких соединений (например, наночастицы Fe, Ni и Со и их сплавов из карбонилов, коллоиды золота и меди, нанооксид Zr и др.).
Можно получать порошки при помощи электрического взрыва проволочек. Известно, что при пропускании через относительно тонкие проволочки импульсов тока плотностью 104—106А/мм2 происходит взрывное испарение металла с конденсацией его паров в виде частиц различной дисперсности. В зависимости от состава среды, в которой протекает процесс, может происходить образование металлических частиц (инертные среды) или оксидных (нитридных) порошков (окислительные или азотные среды). Требуемый размер частиц и производительность процесса зависят от параметров разрядного контура и диаметра используемой проволоки. Форма наночастиц преимущественно сферическая, размеры частиц изменяются в широких пределах. Для наночастиц размером 50— 100 нм таких металлов, как Al, Си, Fe и Ni производительность установки составляет 50 — 200 г/ч при энергозатратах до 25 — 50 кВт ч/кг. Могут быть получены нанопорошки оксидов (А1203, ТЮ2, Zr02, MgAl204 и др.) с размером 20 — 30 нм.
Выбор того или иного метода получения нанопорошков зависит от предъявляемых к ним требований, свойств исходного материала, и экономического обоснования процесса.
Часто процесс тонкого помола сочетается с механохимическим синтезом нового материала из нескольких загружаемых компонентов. Процессы, происходящие при интенсивном размоле, нельзя считать чисто механическими, поскольку они сопровождаются электрическими явлениями, атомарным перемешиванием и химическими реакциями как внутри отдельных частичек, гак и между ними, а в ряде случаев — сильнейшей физико-химической модификацией свойств их поверхности — механоактивацией [3].
Поэтому зачастую ультратонкий помол многокомпонентных субстанций называют механическим сплавлением (mechanical alloying).
Этими методами можно получить порошки металлов с размерами частиц в десятки нанометров, их оксидов — с размерами в единицы нанометров, диспергировать полимеры, компоненты керамики и др.
Более комплексную и глубокую переработку сырья обеспечивают физико-химические методы, меняющие не только размеры и структуру частиц, но и их химический состав. В отличие от сухой механохимической технологии их проводят в жидком состоянии реагентов: растворах, гелях, коллоидах — или в газофазных реакциях.
Среди большого числа используемых методов этой группы отметим наиболее распространенные: золь-гель метод, методы осаждения из раствора, сублимационной сушки, методы восстановления оксидов металлов газами (Нг, СО), гидридами металлов, гидразином, формальдегидом, гипофосфитом и др. Ряд металлов и их оксидов можно получить методами гидролиза и термической диссоциации солей органических кислот при их нагреве до температуры 200…400 °С. Размеры частиц получаемых порошков могут варьироваться от единиц до многих десятков нанометров, хотя во многих из этих методов удается добиться очень узкого распределения частиц по размерам.
Методы высокотемпературного распыления и испарения в электрической дуге, пучке лазера, потоке плазмы, упоминавшиеся выше, часто дополняют проведением химических реакций и модификацией химического состава обрабатываемого сырья путем введения в зону нагрева нескольких компоцентов и различных газовых сред. При этом возможны синтез, разложение, окисление, восстановление продуктов.
Обратимся теперь к особенностям свойств наночастиц и наноиорошков. Высокая удельная поверхность (т.е. отношение площади свободной поверхности к массе), доходящая до Кг м2/г, предопределяет их высокую химическую и каталитическую активность. Поэтому помимо применения их как сырья для дальнейшего производства наноструктурных объемных материалов они часто используются в качестве высокоэффективных катализаторов и реагентов для химических реакций, компонентов косметических и фармакологических средств.
Наибольших объемов достигло производство нанопорошков для полирующих суспензий, лакокрасочных покрытий, солнцезащитных кремов и катализаторов. Другие важные сферы применения — автомобилестроение (катализаторы для очистки выхлопных газов, лакокрасочные композиции), медицина и фармацевтика (лекарственные средства в наноструктурном состоянии), электроника (нанопорошки для магнитных систем памяти, дисплеев и др.), смазочно-охлаждающие жидкости [3].