Получение карбида бора в куске
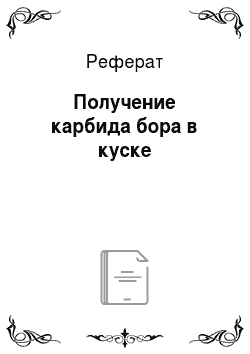
Рис. 3.12. Микроструктура зерна промышленного карбида бора (участки белого цвета) с порами разных размеров (вкрапления черного цвета в зернах В4С): а — плотные, однородные наиболее высококачественные зерна; б — крупные и мелкие поры в зерне повышенного качества; в — смесь крупных плотных зерен (А) и зерен с включениями графита (Б); г — зерна с эвтектическими включениями ровавшую шихту, сгребая… Читать ещё >
Получение карбида бора в куске (реферат, курсовая, диплом, контрольная)
Промышленное производство карбида бора в России осуществляется в дуговых электропечах способом «на блок». В качестве основных сырьевых материалов используются техническая борная кислота с массовой долей Н3В03, равной 99%, и нефтяной кокс. Кроме основных сырьевых компонентов при плавке карбида бора добавляют оборотный спек, отходы с копра (спек сортировки) и фракцию -0,4 мм, образующуюся при дроблении куска. Оборотный спек — это возвратный материал при плавке В4С, являющийся продуктом сплавления борной кислоты с нефтяным коксом. Рекомендуемое соотношение В203/С в оборотном спеке должно составлять величину, равную 1,89.
Отходы с копра представляют собой спек шихты, отобранный с поверхности блоков карбида бора при их очистке на разбивочной плите.
Для уменьшения пылеуноса, способствующего значительным потерям массы борсодержашего сырья, борную кислоту и нефтяной кокс смешивают перед загрузкой в печь и брикетируют, а затем загружают в печь вместе с обогащающими добавками.
Подробная технологическая схема подготовки сырьевых материалов и производства карбида бора показана на рис. 3.10.
Процесс плавки карбида бора ведется в трехфазной дуговой электропечи при активной мощности 600−900 кВт способом «на блок» с погруженными в шихту электродами диаметром 450 мм.
Образование карбида бора обычно описывают суммарной реакцией.
4Н3В03 + 4С = В4С + ЗС02 + 6Н20.
Контроль за процессом наращивания блока ведется по скорости подъема электродов и электрическому режиму.
Каждая кампания осуществляется в три этапа: розжиг печи, наращивание блока карбида бора, проплавление шихты на колошнике. Розжиг печи длится 10−15 мин при установленной мощности трансформатора 500 кВ А. При наплавлении блока необходимо правильно выбрать номинальную мощность, так как при низкой мощности печи снижаются скорость и полнота протекания реакций и, как следствие, производительность печи с одновременным увеличением расхода сырьевых материалов и электроэнергии, а при повышенной мощности наблюдается перегрев карбида бора и разложение его с выделением углерода, загрязняющего готовый продукт.
В процессе наплавления шихты (наращивания блока карбида бора) шихта подается в печь равномерно в период всей плавки по определенному, строго установленному графику. Процесс плавки ведется с закрытым колошником, позволяющим снизить тепловые потери. Загрузку шихты в печь прекращают за 30−40 мин до окончания плавки, а за 15−20 мин перед отключением печи снижают се мощность. Непосредственно процесс плавки заканчивается после полного проплавления шихты на колошнике.
Выплавленный блок остывает, очищается от спека и затем разбирается по сортности. Приваренная к поверхности блока корка спека (спек сортировки) возвращается снова в плавку, а разбракованный кусковой продукт дробят до получения кусков размером 20 мм, затаривают в специальную тару и направляют в цех производства шлифовальных материалов.
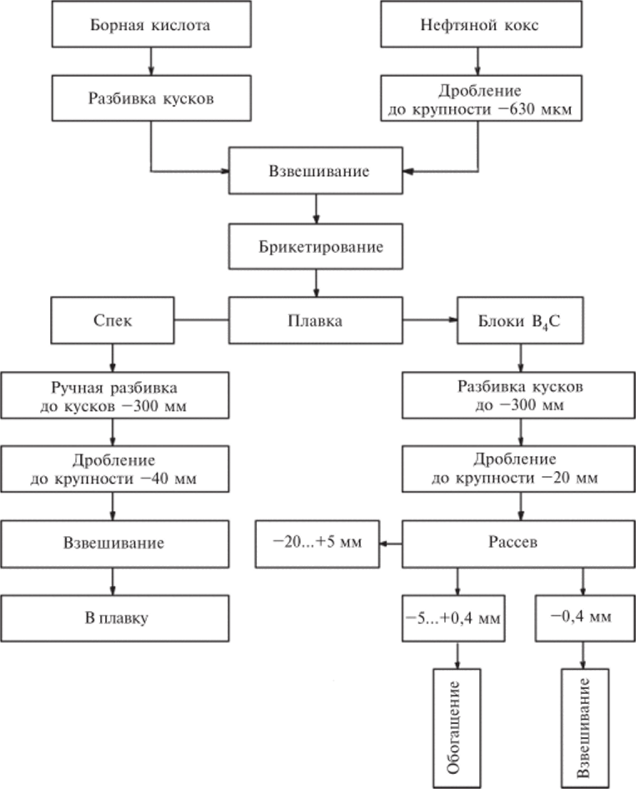
Рис. 3.10. Технологическая схема подготовки сырья и получения карбида бора.
Получаемый по такой технологии kvcok карбида бора содержит 69−71% •W 3−5% в203, 26−28% С*., 7−9% Ссвов, 86−90% В4С.
На 1 т производства карбида бора расходуется примерно 4,7 т борной кислоты и в среднем 18 675 кВт ч/т электроэнергии. При этом примерно 9% борной кислоты безвозвратно теряется во время плавки.
Высокие сырьевые и энергетические затраты при производстве карбида бора стимулировали дальнейший поиск в направлении совершенствования и удешевления этого процесса.
В конце 80-х голов XX века была разработана и внедрена новая технология производства карбида бора повышенного качества [7]. Новизна предложенной авторами |7| технологии заключается в том, что плавка карбида бора ведется в электропечи с двумя цилиндрическими стальными кожухами (рис. 3.11): наружный кожух диаметром и высотой, равными 2 м, и внутренний кожух диаметром 1,6 м и высотой 1,2 м. Наружный кожух устанавливается на тележку и перемещается по вертикали по ходу плавки с помощью специального механизма.
В электропечи такой конструкции шихту (смесь борной кислоты и углеродного восстановителя) загружают в кольцевой зазор между наружным и внутренним кожухами, где происходит дегидратация Н3В03 и плавление В203 за счет нагрева внутреннего кожуха в процессе плавки до температуры 600−700 °С. Поступление расплавленной шихты, состоящей из смеси В203 и углерода, в реакционную зону ванны печи регулируется подъемом внутреннего кожуха, при этом расплав протекает в зону электрических дуг, где происходят процессы образования карбида бора по реакции 2В203 + 7С = В4С + 6СОТ.
Использование внутреннего подвижного кожуха позволяет вывести процесс дегидратации борной кислоты из зоны интенсивного нагрева и высоких.
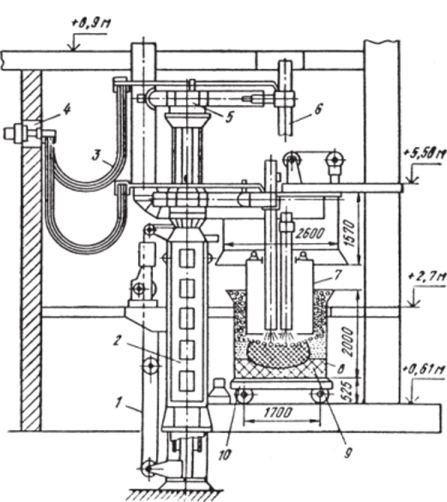
Рис. 3.11. Общий вид дуговой электропечи для выплавки карбида бора «на блок»:
1 — трос; 2 — стойка механизма перемещения электрода; 3 — гибкий кабель; 4 — проем; 5 — рукав элскгродсржателя; 6 — электрод; 7 — подвижный кожух; 8 — наружный кожух; 9 — подина; 10 — выкатная тележка температур и тем самым значительно снизить потери Н3В03 при плавке и повысить качество карбида бора.
Непосредственно процесс плавки в такой электропечи ведется с использованием графитовых электродов диаметром 300 мм, питание печи осуществляется от трехфазного трансформатора типа ЭТМК3200/10, имеющего 12 ступеней изменения напряжения. Номинальная мощность печного трансформатора 2 MB A, напряжение на высокой стороне трансформатора 10 кВ. На низкой стороне трансформатора напряжение может меняться от 145 до 69,6 В при токе 7,97 и 10 кА соответственно |7|.
После окончания плавки электроды и внутренний кожух поднимаются, печь выкатывается и остывает в течение 30 мин, а затем блок карбида бора специальным приспособлением приподнимается с помощью крана, и с его поверхности металлическими скребками удаляют расплавленную непрореаги;
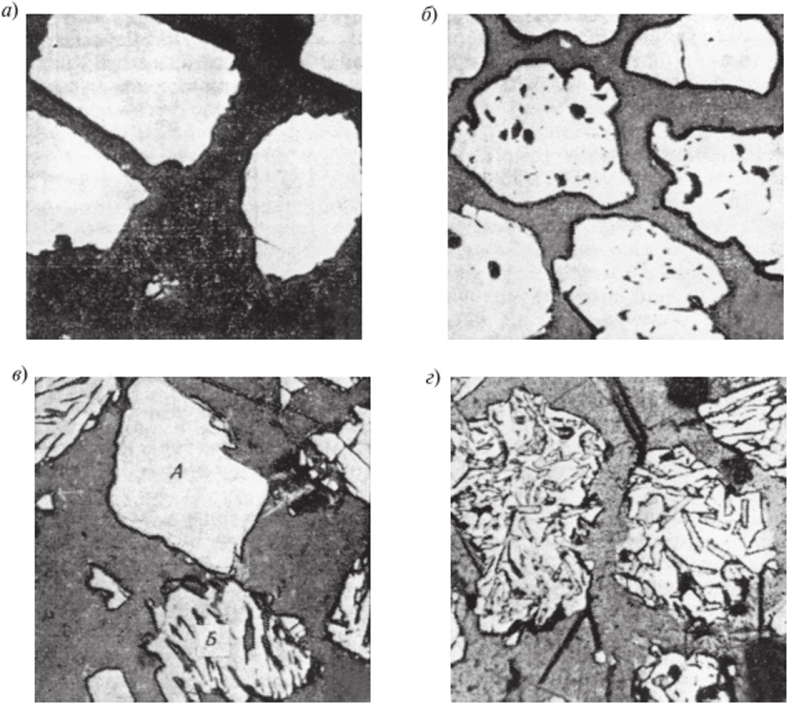
Рис. 3.12. Микроструктура зерна промышленного карбида бора (участки белого цвета) с порами разных размеров (вкрапления черного цвета в зернах В4С): а — плотные, однородные наиболее высококачественные зерна; б — крупные и мелкие поры в зерне повышенного качества; в — смесь крупных плотных зерен (А) и зерен с включениями графита (Б); г — зерна с эвтектическими включениями ровавшую шихту, сгребая се в печь. Затем очищенный блок карбида бора передается на эстакаду, где охлаждается на воздухе до температуры окружающей среды. Освобожденная от блока печь закатывается снова под электроды (см. рис. 3.11), и начинается новая плавка.
Выплавленный в печи новой конструкции кусок карбида бора имеет следующий состав, %: Вобш 75−77, В203 1−2, Собш 22−24, Ссвоб 1−3, В4С 95−98.
На рис. 3.12 показана структура промышленного зерна карбида бора N40 (кристаллы белого цвета) с мелкими и крупными порами (черного цвета вкрапления в кристаллах В4С).
Себестоимость сырьевых материалов вместе с электроэнергией составляет 75 % от обшей заводской стоимости 1 т кускового карбида бора.