Литье без давления
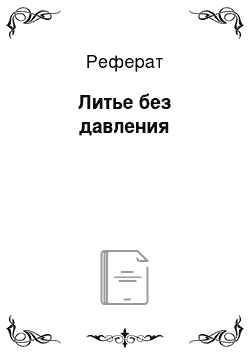
Объемная усадка е-капролактама и метилметакрилата при полимеризации составляет 19—20%, эпоксидных, полиэфирных и фурановых смол —5—10%. Усадка наполненных композиций уменьшается пропорционально объемной доле наполнителя. В процессе литья без давления изделий простой конфигурации без внутренних полостей усадку необходимо учитывать при расчете размеров форм. Если же изделие имеет внутренние… Читать ещё >
Литье без давления (реферат, курсовая, диплом, контрольная)
Процесс литья без давления позволяет изготавливать изделия непосредственно из мономеров или олигомеров, минуя промежуточную стадию получения полимера. Иногда этот процесс называют «свободным литьем», «заливкой», «химическим формованием».
Литье без давления объединяет в одном технологическом цикле синтез полимера и его переработку. Большинство мономеров в жидком (или расплавленном) состоянии обладает низкой вязкостью. Поэтому для осуществления процесса не требуется приложения значительного внешнего давления, а вполне достаточно давления порядка долей атмосферы или нескольких атмосфер, создаваемого перекачивающим оборудованием (насосами).
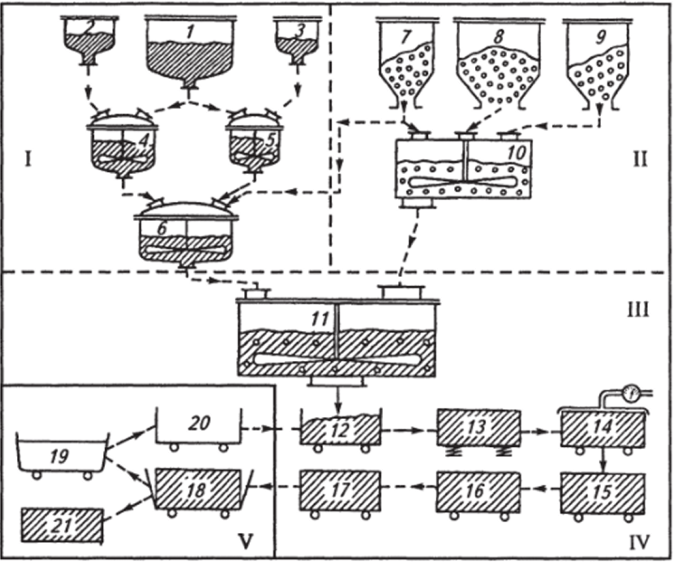
Рис. 6.20. Технологическая схема получения изделий методом литья без давления:
I — участок приготовления жидких компонентов смеси: 7 — емкость для мономера (смолы); 2—емкость для катализатора (инициатора, отвердителя); 3 — емкость для активатора (пластификатора, разбавителя); 4, 5— реакторы для предварительного смешения компонентов; 6 — реактор для приготовления форполимера (связующего); II — участок приготовления твердых компонентов смеси: 7—9—емкости для наполнителей, пигментов, модификаторов; 10— промежуточный смеситель для сыпучих компонентов; III — участок смешения, заливки и формования композиций: 11 — смешение композиций; 12— заливка композиции в форму; 13 — виброуплотнение композиции; 14 — вакуумирование композиции; IV — участок отверждения композиций: 15— подогрев форм; 16— выдержка форм до окончательного отверждения; 77- охлаждение форм; V —участок подготовки форм: 18— выемка изделия; 79—чистка и сборка форм; 20— смазка и подготовка форм; 21 — контроль готовых изделий Технологическая схема получения изделий методом литья без давления приведена на рис. 6.20.
Методом литья без давления можно перерабатывать как мономеры, дающие при полимеризации термопластичные продукты, так и термореактивные материалы, дающие при отверждении неплавкие и нерастворимые продукты с пространственным строением. Этим методом можно получать изделия из ненаполненных, наполненных и высоконаполненных композиций.
Типичными мономерами, дающими в процессе полимеризации термопластичные полимеры, являются жидкие акриловые мономеры (метилметакрилат и др.) или порошкообразный е-капролактам, полимеризация которого с получением капролона происходит в расплаве. Для осуществления полимеризации к жидкому Мономеру добавляют инициаторы или катализаторы, а также активаторы, ускоряющие их действие. Кроме этого в состав композиций могут входить наполнители (дисперсные или волокнистые), пластификаторы, пигменты и другие добавки или сомономеры (винилацетат, акрилонитрил, стирол и др.). Высокая прочность и химическая стойкость получаемых полиакрилатов и полиамидов, простота их переработки позволяют получать из этих материалов крупногабаритные изделия: детали судовых механизмов, работающие в узлах трения (шестерни, втулки, прокладки); электротехнические изделия (капролон); плоские и рельефные листы; коробчатые изделия; монолитные объемные детали; стержни, прутки; скульптурные и архитектурные элементы.
Методом литья без давления можно перерабатывать и композиции на основе реакционноспособных олигомеров. Для химического сшивания к олигомерам добавляют отвердители, инициаторы, катализаторы. В состав олигомерных композиций могут также входить наполнители, красители, пластификаторы и другие добавки.
Олигомерные литьевые смеси обычно применяются в наполненном состоянии [20—50%(об.)] для приготовления заливочных масс, скульптурных и архитектурных деталей (эпоксидные и полиэфирные смолы), ремонтных мастик и шпатлевок (фурановые, эпоксидные и полиэфирные смолы).
Для уменьшения тепловых эффектов, сопровождающих полимеризацию или отверждение мономерных или олигомерных композиций, а также для значительного снижения стоимости и полимероемкости изделий применяют наполнение композиций до 80— 90%(об.). Высоконаполненные материалы после отверждения обладают хорошими конструкционными свойствами. Их прочность при сжатии, например, близка к прочности гранита. Такие материалы называют полимербетонами. Для их получения применяют эпоксидные, полиэфирные, фурановые смолы, метилметакрилат и некоторые другие мономеры, а также минеральные (гранит, кварц, стекловолокно, керамика, каменная мука) и другие (графит, углеродное волокно) наполнители. Применяют полимербетоны для изготовления коррозионно-стойкого технологического оборудования и строительных конструкций (фурфуролацетоновые полимербетоны); деталей прецизионных станков, машин и приборов (эпоксидные и акрилатные полимербетоны); декоративных покрытий (полиэфирные полимербетоны) полов, покрытий мостов и для других ответственных сооружений. Примерный состав композиций, перерабатываемых методом литья без давления, приведен в табл. 6.4.
Таблица 6.4. Примерные составы композиций, перерабатываемых методом литья без давления
Основной мономер или смола. | Катализатор, инициатор или отвердителъ. | Активатор | Другие добавки. |
е-Капролактам (К). | Натрий металлический (0,1%). | Гексаметилентолуилендиизоцианаты (0,1%). | —. |
Метилметакри; | Пероксиды бенДиметиланилин,. | ПММА, ПВХ, ПС,. | |
лат (ММА). | зоила (0,1—1%), демитил-л-толуи; | ПВА, каучуки, ДБФ,. | |
циклогексанкардин (1—3%) боната (0,3—. 0,5%). | пигменты, наполнители (волокно)*. | ||
Эпоксидные Три-, тетраили. | —. | Разбавители, плас; | |
смолы (ЭС). | полиамиды (10−25%). | тификаторы, каучуки, пигменты, наполнители. | |
Ненасыщенные. | Пероксиды метил; | Нафтенат кобаль; | Разбавитель (сти; |
полиэфирные. | этил кетон а, бен; | та (2—5%), ани; | рол), пигменты, на; |
смолы (НПС). | зоила, гидропероксид кумола (1−3%). | лин (1—2%). | полнители**. |
ФурфуролацетоБензол сульфокисновый мономер лота (15—25%), (ФАМ) серная кислота, концентрат Перова. | Наполнители**. | ||
ФАЭД — смесь ЭС + ФАМ. | Полиэтиленполиамин (10—15%). | ". |
*ПММА —полиметилметакрилат; ПВХ — поливинилхлорид; ПС —полистирол; ПВА — поливинилацетат, ДБФ — дибутилфталат.
**В ненаполненном состоянии практически не применяется из-за сильного саморазогрева при отверждении.
Основной подготовительной операцией является тщательная сушка всех ингредиентов, в том числе минеральных наполнителей. Содержание влаги в них, например при полимеризации е-капролактама или полиэфирной смолы, не должно превышать 0,02%; при полимеризации фурфуролацетонового мономера или ЭС — 0,05−0,1%.
Стадия заливки композиций в форму требует точного выполнения всех заданных временных и температурных параметров, так как даже 2—3-минутная задержка при заливке или небольшой перегрев реакционной массы могут привести к частичной или полной потере текучести.
При смешении мономеров или олигомеров с большим количеством наполнителей для улучшения равномерности распределения небольших добавок катализаторов и инициаторов по всему объему смеси применяют последовательные 2—3-стадийные режимы смешения. На первой стадии смешивают мономерное или олигомерное связующее с наиболее мелкой фракцией наполнителя, катализаторами и активаторами отверждения. На второй, а в случае необходимости и на третьей стадии вводят остальной наполнитель пофракционно. Время смешения ненаполненных заливочных композиций обычно не превышает 1—2 мин, а время смешения наполненных и высоконаполненных композиций — 2—5 мин.
Повышению вязкости исходной композиции способствует снижение температуры заливочной массы. Для снижения вязкости повышают температуру, вводят добавки низковязких сомономеров (например, стирола в акрилатные и полиэфирные композиции), разбавителей и пластификаторов (в эпоксидные компаунды). Снижение вязкости особенно важно для смол, являющихся основой (связующим) для высоконаполненных композиций.
Полимеризация (отверждение) начинается сразу же после смешения мономера (смолы) с инициатором, катализатором или отвердителем и приводит к повышению вязкости композиции. Возрастание вязкости идет в две стадии: вначале медленно, а затем ускоренно. Виброформование возможно лишь на первой стадии роста вязкости.
Форполимеры и связующие получают в реакторах-смесителях с обогревом (охлаждением), с мешалкой и с возможностью вакуумирования реакционной смеси. Для приготовления смесей сыпучих ингредиентов применяют вибросмесители, лопастные мешалки, смесители типа «пьяная бочка». Для получения смесей жидких и сыпучих ингредиентов применяют смесители типа бетономешалок или тестосмесителей, а также установки непрерывного действия, представляющие собой одношнековые смесители в сочетании с емкостями и бункерами для хранения и подогрева ингредиентов (3—4 жидких и 5—6 сыпучих компонентов), оснащенные автоматической системой управления.
Формы для заливки компаундов и высоконаполненных композиций изготавливают из жестких (сталь, алюминий, дерево и т. п.) или гибких (пластмассы, стеклопластики, силиконовые полимеры, резина и т. п.) материалов. Жесткие формы являются разборными, а гибкие позволяют вынимать изделия, не разбирая формы. Гибкие (эластичные) формы применяют для тиражирования по моделям небольших по размеру предметов искусства. Для предотвращения прилипания изделий к формам на их внутреннюю поверхность наносят смазки (составы на основе воска, парафина, вазелина, силиконовых олигомеров и т. п.). Для придания блеска декоративным изделиям внутреннюю поверхность форм полируют. Жесткие формы применяют для изготовления массивных крупногабаритных изделий, гибкие — для мелких изделий. Формы для литья должны быть герметичными, чтобы не происходило вытекания низковязких мономеров при заливке.
Формовая оснастка играет важную роль в процессах литья без давления. Это обусловлено тем, что полимеризация реакционноспособных мономеров и смол сопровождается их значительной усадкой.
Объемная усадка е-капролактама и метилметакрилата при полимеризации составляет 19—20%, эпоксидных, полиэфирных и фурановых смол —5—10%. Усадка наполненных композиций уменьшается пропорционально объемной доле наполнителя. В процессе литья без давления изделий простой конфигурации без внутренних полостей усадку необходимо учитывать при расчете размеров форм. Если же изделие имеет внутренние полости, то усадка материала может приводить к раздавливанию внутренних сердечников или к растрескиванию изделий. Чтобы обеспечить свободную усадку отверждающегося материала, в форме в этих случаях внутренние сердечники должны уменьшаться в размерах в процессе отверждения. Это достигается за счет усложнения их конструкции путем применения клиновых или винтовых зажимов, прокладок, а также за счет применения легко деформирующихся или разрушающихся сердечников.
Для облегчения заполнения форм, удаления пузырьков воздуха, попавших в реакционную массу, и для ускорения процессов уплотнения наполненных и высоконаполненных композиций применяют вакуумирование или вибрацию. При получении труб также возможно применение центробежного или ротационного формования. Вакуумирование с разрежением 0,04—0,07 атм применяют обычно при формовании небольших по размеру изделий из жидких наполненных или ненаполненных мономеров. Для проведения вакуумирования требуются герметичные формы или специальные вакуумные камеры. Хорошие результаты дает вакуумирование реакционной смеси на стадии смешения.
Для уплотнения высоконаполненных композиций применение вибрации является необходимым, так как при этом не только облегчается выход воздуха, но и достигается наиболее плотная укладка частиц наполнителя. Источниками механических колебаний средней частоты (40—60 Гц), способствующих уплотнению, являются механические или электродинамические вибраторы, создающие колебания за счет вращения несбалансированных противовесов или за счет колебательного перемещения сердечника в электромагнитной катушке. Существуют также гидравлические вибрационные устройства. Амплитуда вибрации 0,1—0,5 мм. Возможно формование изделий за счет применения вибраторов, закрепленных прямо на литьевых формах или установленных на специальных площадках.
Применение вибрации для уплотнения заливочных композиций наиболее эффективно при переработке полимербетонов. Вибрация облегчает взаимное перемещение грубодисперсных частиц наполнителей (обычно неправильной формы) в смеси. Возрастание плотности композиции проходит в две стадии. Первая стадия связана с разрушением исходного случайного каркаса частиц в высоконаполненной смеси и с переукладкой частиц в более выгодные положения. Вторая, более медленная, стадия связана со сближением частиц и с выходом воздушных включений из уплотняемой смеси. Темп уплотнения высоконаполненных композиций определяется интенсивностью виброколебаний и концентрацией жидкой фазы в смеси.
Проведение процесса отверждения также требует тщательного соблюдения температурных (температура форм и камеры) и временных (время прогрева и выдержки) параметров. Для большинства термореактивных смол и мономеров саморазогрев при отверждении настолько значителен, что приводит к термическому разложению получаемых полимерных продуктов. Например, полимеризацию метилметакрилата даже при разбавлении его собственным полимером обычно проводят при интенсивном охлаждении форм водой. Наиболее целесообразным способом разработки рационального режима отверждения композиций является его математическое моделирование на базе системы дифференциальных уравнений теплопередачи, решаемых совместно с уравнениями, описывающими скорость выделения тепла мономером или олигомером. Математическое моделирование позволяет рассчитать наиболее мягкие режимы отверждения изделий (с учетом внешнего нагрева или охлаждения), не приводящие к ухудшению их эксплуатационных свойств.
Отверждение изделий, получаемых методом литья без давления, проводят при комнатной температуре в многоярусных полимеризационных камерах. При повышенных температурах отверждение изделий проводят в печах туннельного типа или в печах периодического действия, обогрев которых осуществляется горячим воздухом, с помощью электронагревателей или ИК-излучения. Весьма удобными в эксплуатации оказались печи аэродинамического подогрева, нагрев воздуха в которых осуществляется за счет вращения мощных вентиляторов с очень низким аэродинамическим качеством лопастей (переход механической работы в тепло). Эти печи выгодно отличают практически безынерционные нагрев и охлаждение, что позволяет осуществлять заданные скорости прогрева или охлаждения.
Основным параметром стадии охлаждения является скорость снижения температуры, которая обычно составляет 0,1—0,5 вС/мин. Превышение скорости охлаждения снижает прочностные показатели получаемых изделий за счет возникновения больших градиентов температур и высоких температурных напряжений или за счет нарушения оптимального режима кристаллизации полимера (в случае капролона).
Контрольные вопросы и задания
- 1. Какие методы формования изделий из стекловолокнистых материалов применяются на практике? Опишите области их применения.
- 2. На чем основан выбор метода формования при производстве изделий различного назначения из стекловолокнистых растворов?
- 3. На чем основан выбор растворителя при получении пленкообразующих растворов?
- 4. Каковы особенности изготовления триацетатных и полиимидных пленок?
- 5. Перечислите основные стадии процесса изготовления материалов методом промазки.
- 6. Приведите схемы нанесения покрытий на основу с помощью ракли.