Реконструкция дебутанизатора и изопентановой колонны на ГФУ с целью повышения эффективности процесса ректификации
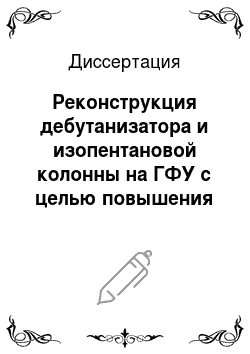
Диссертация
Изучено влияние состава ШФЛУ на значения темератур низа дебутанизатора и изопентановой колонны. Установлено, что изменение содержания в ШФЛУ углеводородов Сб и выше от 8,22 до 0,82 требует снижения температур низа дебутанизатора и изопентановой колонны на 6 °C. Показано также, что температурный режим колонн определяется не только содержанием углеводородов Сб и выше в ШФЛУ, но и относительным… Читать ещё >
Список литературы
- Григорян Л.Г., Шафранский Е. Л., Прохоренко Ф. Ф., Шевелев Ю. В., Логинов В. И. Проблемы и перспективы ректификации в нефтепереработке. В сб. тезисов докладов 6-ой Всесоюзной конференции по теории и практике ректификации, Северодонецк, 1991, с. 23−30.
- Кафаров В.В., Кулов H.H., Дорохов И. Н. Перспективы развития научных основ химической технологии. ТОХТ, 1990, т.24, № 1, с. 3 11.
- ГОСТ 9965–76. Нефть. Степень подготовки для нефтеперерабатывающих предприятий. М.: Издательство стандартов, 1976, с.З.
- Неяглов A.B. Состояние производства и переработки углеводородного сырья на предприятиях ВПО «Союзнефтеоргсинтез». В сб. «Совершенствование процессов сероочистки углеводородного сырья и газофракционирования», М.: ЦНИИТЭНефтехим, 1980, с.3−8.
- Саттаров У.Г., Ибрагимов М. Г., Зиляева Л. Н. Анализ способов стабилизации нефти на промыслах. В сб. «Совершенствование процессов сероочистки углеводородного сырья и газофракционирования», М.: ЦНИИТЭНефтехим, 1980, с. 20−27.
- Берлин М.А., Гореченков В. Г., Волков Н. П. Переработка нефтяных и природных газов. М.: Химия, 1981, 472 с.
- ТУ 38.101 490−89. Газовое углеводородное сырье. Технические условия.
- ГОСТ 10 679–76. Газы углеводородные сжиженные. Метод определения углеводородного состава.- 13 210. ГОСТ 20 448–90. Газы углеводородные сжиженные топливные для коммунально-бытового потребления. Технические условия.
- ГОСТ 27 578–87. Газы углеводородные сжиженные для автотранспорта. Технические условия.
- Moore J.R. How occidental conserves associated gas in North Sea. Oil and Gas Journal, 1979, v.77,№ 23,p. 110,115−116,118.
- Thompson Hohn, Kuchler Jim. Expander increases Sun gas plant efficiency. Oil and Gas Journal, 1978, v.76, № 43, p. 179−180.
- Minton Bill R. Recovering ethylene from refinery gas. Oil and Gas Journal, 1979, v.77, № 42, p. 62−63.
- Кафаров B.B., Перов B.M., Мешалкин В. П. Принципы математического моделирования химико-технологических систем. М.: Химия, 1974, 344 с.
- Свинухов А.Г. Основные закономерности системного анализа в химической технологии. Химическая промышленность, 1978, № 7, с.67−69.
- Motard R.L., Sahan M., Rosen E.M. Steady state Chemical Process Simulation. A.I.Ch.E. Journal, 1975, v.21, № 3, p. 417−436.
- Вольфсон И.С., Константинов E.H., Дубов A.B., Димитриев А. П., Тяпугина Л. А. Сравнение схем деэтанизации предельных газовых головок нанефтеперерабатывающих заводах. Нефтепереработка и нефтехимия, 1972, № 11, с. 26−29.
- Вольфсон И.С., Теляков Э. Ш. Сравнительный анализ схем газофракционирования на НПЗ и НХК. Химия и технол. топлив и масел, 1978, № 1, с.7−10.
- Теляков Э.Ш., Силкин Е. А., Тяпугина JI.A. О реконструкции типовых трехсекционных газофракционирующих установок (ГФУ). Химия и технол. топлив и масел, 1978, № 3, с.28−31.
- Александров H.A. Перегонка и ректификация в нефтепереработке. М.: Химия, 1981, 352 с.
- Брукс Г. Г. и др. Химия углеводородов нефти.: М.: Гостоптехиздат, т.1, 1958, 552 с.
- Богатых К.Ф., Кондратьев A.A., Миннуллин М. Н., Арсланов Ф. А. Расчет состава непрерывной смеси по экспериментальной кривой однократного испарения. Теор. основы, хим. технол. 1971, т.5, № 4, с.508−512.
- Кондратьев A.A., Богатых К. Ф., Зыков Д. Д. Теор. основы, хим. технол. 1969, т. З, № 5, с. 667.
- Богатых К.Ф., Кондратьев A.A., Зыков Д. Д. Теор. основы, хим. технол. 1969, т. З, № 6, с. 811.
- Платонов В.М., Берго Б. Г. Разделение многокомпонентных смесей. М.: Химия, 1965, 368 с.
- Кондратьев A.A. Схемы соединения простых ректификационных колонн в сложные колонны со связанными тепловыми потоками. В сб. тезисов докладов 4-ой Всесоюзной конференции по ректификации, Уфа, 1978, с. 271−274.
- Марушкин Б.К. О схемах колонн со связанными потоками. В сб. тезисов докладов 4-ой Всесоюзной конференции по ректификации, Уфа, 1978, с. 275−277.
- Кондратьев A.A., Умергалин Т. Г., Деменков В. Н. Ректификация нефтяных фракций в сложных колоннах. В сб. тезисов докладов 5-ой Всесоюзной конференции по теории и практике ректификации, Северодонецк, 1984, с. 267−268.
- Деменков В.Н., Кондратьев A.A. Новые схемы фракционирования нефти и мазута. В сб. Проблемы углубления переработки нефти. Тезисы докладов 6-ой Республиканской научно-технической конференции, Уфа, 1985, с. 134 141.
- Сидоров М.Г., Деменков В. Н., Кондратьев A.A. Фракционирование нефти в колонне со связанными тепловыми потоками. Нефтепереработка и нефтехимия, 1991, № 12, с. 15−17.
- Деменков В.Н. Схемы фракционирования нефтяных смесей в сложных колоннах. В сб. тезисов докладов Всероссийской научно-технической конференции «Проблемы нефтегазового комплекса России», Уфа, 1995, с. 167.
- Деменков В.Н., Сравнение схем разделения смеси на четыре продукта. В сб. тезисов докладов Республиканского семинара молодых ученых и специалистов «Актуальные проблемы нефтехимии», Уфа, 1982, с.82−83.
- Деменков В.Н. Новые технологические схемы фракционирования нефтяных смесей в сложных колоннах. Дисс. доктора технических наук, Уфа, 1996, 342 с.
- Деменков В.Н., Кондратьев Ю. А. Ввод бензина двумя потоками в стабилизационную колонну установок АВТ. В сб. тезисов докладов Республиканской научно-технической конференции «Химия, нефтехимия и нефтепереработка, Уфа, 1984, с. 61.
- Сидоров Г. М., Деменков В. Н., Мощенко Г.Г и др. Получение тяжелой фракции бензина сырья процесса риформинга в колоннах фракционирования нефти. Нефтепереработка и нефтехимия, 1993, № 12, с. 16−21.
- Баланич A.A., Сидоров Г. М., Деменков В. Н., и др. Разработка технологии выделения высокооктановой фракции из катализата риформинга. Нефтепереработка и нефтехимия, 1994, № 3, с. 13−18.
- Сидоров ГМ, Деменков В., Баланич A.A. Получение высоко-октанового компонента бензина на установке газофракционирования. В сб. тезисов докладов Всероссийской научно-технической конферен-ции «Проблемы нефтегазового комплекса России», Уфа, 1995, с. 166.
- Ибрагимов М.Г., Теляков Э. Ш., Сибгатуллина JI.A., Саттаров У. Г. Исследование процесса стабилизации нефти, Нефтяное хозяйство, № 2, 1980, с.48−50.
- Саттаров У.Г., Каштанов A.A., Шамсутдинов М. Г. Опыт эксплуата-ции блоков стабилизации установок комплексной подготовки нефти и пути их дальнейшего совершенствования, Нефтепромысловое дело, 1976, № 10, с 18−22.
- Петров Ф.К., Рачковский C.B., Теляков Э. Ш. Моделирование процесса разделения этаноламинов. В сб. материалов Всероссийской научной конференции «Теория и практика массообменных процессов химической технологии (Марушкинские чтения)», Уфа, 1996, с.90−91.
- Кондратьев A.A. Сложные колонны для ректификации многокомпонентных смесей. В сб. материалов Всероссийской научной конференции «Теория и практика массообменных процессов химической технологии (Марушкинские чтения)», Уфа, 1996, с.84−87.
- Холланд Ч.Д. Многокомпонентная ректификация. М.:Химия, 1069,351с.
- Peiser A.M. Better Computer Solution of Multicompopnent System. Chem. Eng., 1960, v.67, № 14, p.129−134.
- Петлюк Ф.Б., Серафимов JI.A. Многокомпонентная ректификация. Теория и расчет. М.: Химия, 1983, 304 с.-13 754. Багатуров С. А., Основы теории и расчета перегонки и ректификации. М.:1. Химия, 1974, 439 с.
- Fenske M.R., Fractionation of Straight. Rum Pennsylvania Gasoline. Industrial and Engineering Chemistry, 1932, v.24, № 5, p.482−485.
- Gilliland E.R. Minimum Reflux Ratio. Industrial and Engineering Chemistry, 1940, v.32, p.1101−1106.
- Gilliland E.R. Estitation of the Number of Theoretical Plates as a Function of the Reflux Ratio. Industrial and Engineering Chemistry, 1940, v.32, p.1220−1223.
- Михайловский Б.Н. Аналитический метод расчета процесса ректификации многокомпонентных и бинарных смесей. Химическая промышленность, 1954, № 4, с.237−241.
- Кафаров В.В., Ветохин В. Н., Бояринов А. И. Программирование и вычислительные методы в химии и химической технологии. М.: Химия, Наука, 1972, 487 с.
- Muller Werner, Verworner Marianne. Berechnung von Rektifikations und Absorptionsprozessen von Mehrstoffgemischen mit Hilfe von Matrizenverfahren. Chem. Techn, 1977, v.29,№ 11, s. 607−611.
- Peiser A.M. Better Computer Solution of Multicomponent System. Chem. Eng., 1960, v.67, № 14, p.129−134.
- Александров И.А. Массопередача при ректификации и абсорбции многокомпонентных смесей. JL: Химия, 1975, 320 с.
- Rose A., Sweeny R.F., Schrodt V.N. Continuous Distillation Calculations by Relaxation Method. Ind. Eng. Chem., 1958, v.50, № 5, p.737−740.
- Кондратьев A.A. Расчет ректификации непрерывной смеси в колонне с несколькими вводами питания и отборами. Теорет. основы хим. технол., 1972, т.6, № 3, с.477−479.
- Богданов B.C., Терехин В. П. Поэлементный метод расчета ректификационных колонн и их комплексов. В сб. тезисов докладов
- Всесоюзного совещания по теории и практике ректификации нефтяных смесей, Уфа, 1975, с.65−67.
- Марушкин Б.К. Расчет абсорбции углеводородных газов. Химия и технол. топлив и масел, 1966, № 9, с.14−18.
- Теляков Э.Ш., Сергеев А. Д., Матюшко Б. Н., Резванов В. Н. Исследование работы блока газоразделения установки каталитического риформинга. Известия ВУЗов, Нефть и газ, 1977, № 3, с.53−57.
- Константинов Е.Н., Кузнечиков В. А., Арнаутов Ю. А., Берлин М. А., Супрунов В. Т., Расчет тарельчатых колонных аппаратов и исследование процесса неадиабатической абсорбции на ГПЗ. Газовая промышленность, 1973, № 5, с. 43−46.
- Hanson D.W., Duffin S.H., Sommerviele G.T. Computation of multistage Separation Processes. N.Y., 1962, p.280.
- Ибрагимов М.Г., Теляков Э. Ш., Сибгатуллина C.A., Саттаров У. Г., Каштанов А. А., Шамсутдинов М. Г. Влияние содержания воды на эффективность работы нефтестабилизационной колонны. Нефтепромысловое дело, 1978, № 7, с.29−31.
- Кондратьев А.А., Фролова Л. Н., Серафимов Л. А. О некоторых особенностях ректификации неидеальных систем. В сб. Технология нефти и газа (вопросы фракционирования), Уфа, 1975, вып.26 (4), с. 17−25.
- Гатауллин Т.Т., Теляков Э. Ш., Шакирзянов Р. Г. Расчет разделения трехфазных систем. В сб. тезисов докладов 6-ой Всесоюзной конфер. по теории и практике ректификации, Северодонецк, 1991, с. 281−283.
- Тукманов Д.Г., Гималеев М. К., Теляков Э. Ш. Моделирование нестационарности массообменных процессов в нефтехимии. В сб. тезисов докладов 4-ой конференции по интенсификации нефтехимических процессов «Нефтехимия-96», Нижнекамск, 1996, с. 143.
- Van Winkle М. Distillanion. N.Y. McGraw-Hill Book Co., Inc., 1967, 684 p.- 13 975. H. Kehlen and M.T.Ratisch. Coraplex multicomponent distillation calculation bycontinuos thermodynamic. Chem. Eng. Sci., 1987, v.42, № 2, p.221−232.
- Зуб M.K., Ветохин В. Н. Модель равновесия жидкость пар для расчета процесса ректификации непрерывных смесей. В сб. тезисов докладов 6-ой Всесоюзной конференции по теории и практике ректификации, Северодонецк, 1991, с. 84−86.
- Кафаров В.В., Ветохин В. Н. Основы автоматизированного проектирования химических производств. М.: Наука, 1987, 624 с.
- Мазгаров А.М., Неяглов А. В., Теляков Э. Ш., Ахмадуллина А. Г., Матюшко Б. Н., Фомин В. А. Очистка широкой фракции легких углеводородов газового конденсата Оренбургского месторождения от сернистых соединений. Химия и технол. топлив и масел, 1976,№ 12, с.6−8.
- Шакирзянов Р.Г., Теляков Э. Ш., Ибрагимов М. Г., Серафимов JI.A. Равновесие жидкость пар в системе изопентан-этилмеркаптан- н.пентан-диметилсульфид. Ж. прикл. химии, 1981, т.54, № 5, с. 1021−1023.
- Шакирзянов Р.Г., Теляков Э. Ш., Серафимов JI.A. Равновесие жидкость -пар в системе пентаны-сернистые соединения при повышенных давлениях, Ж. прикл. химии, 1982, т.55, № 5, с. 1041−1044.
- Шакирзянов Р.Г., Вильданов А. Ф., Теляков Э. Ш. Исследование реализуемых вариантов выделения сернистых соединений из пентановых фракций. В сб. Массообменные процессы и аппараты химической технологии, вып. 6, Казань, 1979, с. 29−31.
- А.с. 891 603 (СССР). Способ выделения нормального пентана. // Э. Ш. Теляков, М. Г. Ибрагимов, Р. Г. Шакирзянов. Опубл. в Б.И., 1981, № 47.
- Рид Р., Шервуд Т. Свойства газов и жидкостей. JL: Химия, 1971, 704 с.
- Варгафтик Н.Б. Справочник по теплофизическим свойствам газов ижидкостей. М.: Наука, 1972, 720 с.
- Джонн Г. Перри. Справочник инженера-химика. Под общей редакцией Н. М. Жаворонкова и П. Г. Романкова. 1969, т.1, 640 с.- 14 086. Автоматизированная единая система теплофизического абонирования
- АВЕСТА), ВНИИПКНефтехим, Киев, 1978.
- Сверчинский Б.С. В сб. тезисов докладов 3-ей Всесоюзной конференции по теории и практике ректификации, Северодонецк, 4.1,1973, с. 164.
- Рамм В.М. Абсорбция газов. М.: Химия, 1971, 767 с.
- Кафаров В.В. Основы массопередачи. М.: Высшая школа, 1972,494 с.
- Соломаха Т.П. Массоперенос в газовой (паровой) фазе на барботажных тарелках // Труды МИХМ. 1975. — Вып. 61. — С.33−40.
- Соломаха Т.П. Уравнение массоотдачи в газовой фазе на колпачковых тарелках // Теор. основы хим. технол. 1970. Т. 4. — № 2. — С. 181−190.
- Плановский А.Н., Соломаха Г. П., Филатов JI.H. Влияние гидравлических параметров на массоотдачу в жидкой фазе // Изв. вузов. Нефть и газ. 1969.- № 6. С.65−71.
- Cho J.S., Wakao N. Determination of liquid-side and gas-side volumetric mass transfer coefficients in a bubble column // J. Chem. Eng. Jap. 1988. — V. 21. — № 6. — P.576−588.
- Соломаха Т.П., Реут В. И., Ващук В. И. и др. Массоотдача в газовой фазе на барботажных клапанных тарелках // Теор. основы хим. технол. 1979. Т. 13.- № 1. С.3−8.
- Scheffe R.D., Weilfiid R.H. Vass transfer characteristics of valve tays // Jng. and Eng. Chem. Res. 1986. — V. 26. — № 2. — P.228−236.
- Кафаров B.B., Шестопалов B.B., Комиссаров Ю. А. и др. Комбинированная математическая модель структуры потока жидкости на клапанной барботажной тарелке // Труды МИХМ. 1975. — Вып. 88. — С.118−120.
- Комиссаров Ю.А., Кафаров В. В., Амангалиев С., Те А.Ю. Структура парожидкостного потока на барботажных тарелках // Теор. основы хим. технол. -1981. Т. 15. № 6. — С.809−816.
- Комиссаров Ю.А., Кафаров В. В., Амангалиев С., Те А.Ю. Эффективность массопередачи с учетом реальной структуры потока жидкости набарботажных тарелках с переливом // Теор. основы хим. технол. 1983. Т. 17. -№ 1. — С.3−9.
- Комиссаров Ю.А., Те А.Ю., Федосеев Д. Ф. и др. Исследование структуры потока жидкости и массопередачи в аппаратах с прямотоком жидкости на смежных тарелках // Теор. основы хим. технол. 1985. Т. 19. — № 5. — С.591−596.
- Gualito J J., Cerino F.J., Cardenas J.C., Rocha J. A. Disign method for distillation columns filled with metallic, ceramic or plastic structured packing // Ind. Eng. Chem. Res. 1997,-v.36, N5, p. 1747−1757.
- Ingo Wagner, Johann Stichlmair and James R. Fair. Mass tri sfer in beds of modern, high-efficiency random packing // Ind. Eng. Chem. Res. 1997,-v.36, N1, p.227−237.
- Reinhard Billet. Packed towers in processing and environmental technology.-New York: VCH, 1995.
- Дьяконов С.Г., Елизаров В. И., Лаптев А. Г. Теоретические основы и моделирование процессов разделения веществ. Изд-во Казанского университета, Казань, 1993.
- Дьяконов С.Г., Елизаров В. И., Кафаров В. В. Сопряженное физическое и математическое моделирование в задачах проектирования промышленных аппаратов. Ж. прикл. химии, 1986, т.59, № 9, с. 1927−1933.
- Дьяконов С.Г., Елизаров В. И., Лаптев А. Г. Моделирование массотеплопереноса в промышленных аппаратах на основе исследования лабораторного макета. Теор. основы хим. технол. 1993, т.27, № 1, с.4−18.
- Дьяконов С.Г., Елизаров В. И., Лаптев А. Г. Моделирование процессов разделения на контактных устройствах промышленных колонн. Ж. прикл. химии, 1993, т.66, № 1, с. 92−103.
- Баглай В.Ф., Минеев Н. Г., Лаптев А. Г., Дьяконов Г. С., Фарахов М. И. Реконструкция установки получения моторных топлив. В сб. Массообменные процессы и аппараты хим. технол.: Межвузовский тематический сборник научных трудов, КГТУ, Казань, 1997, с. 13−20.
- Баглай В.Ф. Моделирование процесса разделения углеводородного сырья и реконструкция колонн установки получения моторных топлив. Дисс. канд. техн. наук, Казань, КГТУ, 1997,171 с.
- Hausen H. Zur Definition des Austauschgrades von Rektifizierboden bei Zwei-und Dreistoffgemischen. Chem. Eng. Techn., 1953, Bd.25, № ДО, s. 595−597.
- Марушкин Б.К., Теляшев Г. Г. Методы оценки эффективности (к.п.д.) тарелок при ректификации многокомпонентных смесей. В сб. Технология нефти и газа (вопросы фракционирования), вып. З, Уфа, Башкнигоиздат, 1975, с. 35−86.
- ПЗ.Попенова С. Г., Комиссаров Ю. А., Ветохин В. Н. Разработка нечеткого алгоритма синтеза схемы разделения многокомпонентных смесей. В сб. тезисов докладов 6-ой Всесоюзной конференции по теории и практике ректификации, Северодонецк, 1991, с. 325−327.
- Галиаскаров Ф.М., Быстрое А. И. Расчет системы простых и сложных ректификационных колонн. В сб. тезисов докладов 6-ой Всесоюзной конференции по теории и практике ректификации, Северодонецк, 1991, с. 272−273.
- Кузнечиков В.А., Теляков Э. Ш. Анализ работы действующих химико-технологических производств на основе системного анализа. Теор. основы хим. технол., 1984, т.18, № 5, с. 662−669.
- Петлюк Ф.Б., Киевский В. Я., Аветьян B.C., Иняева Г. В. АРМ процессов разделения на основе персональной ЭВМ. В сб. тезисов докладов 6-ой Всесоюзной конференции по теории и практике ректификации, Северодонецк, 1991, с. 263−265.
- Лебедев Ю.Н. Совершенствование колонной аппаратуры для нефтеперерабатывающей, нефтехимической и газовой промышленности. В сб. тезисов докладов 6-ой Всесоюзной конференции по теории и практике ректификации, Северодонецк, 1991, с.32−38.
- Питерских Т.Д., Карасев В. Е. Гидродинамические характеристики регулярной насадки ИОНХ. В сб. тезисов докладов 6-ой Всесоюзной конференции по теории и практике ректификации, Северодонецк, 1991, с.152−154.
- Богатых К.Ф., Мнушкин И. А. Изготовление пакетов регулярной насадки. Хим. и нефт. машиностроение, 1987, № 5, с. 29−31.
- Богатых К.Ф., Минуллин М. Н., Артемьев А. Ф. Массообменная эффективность сетчатых насадок при перекрестном токе фаз. Химия и технол. топлив и масел, 1987, № 9, с. 22−23.
- Боглаев Ю. П. Вычислительная математика и программирование: Учеб. пособие для студентов втузов.- М.: Высш. шк., 1990.-544 с.
- Nielsen К. L., Methods in Numerical Analysis, New York. Momillan Co., 1957, p. 199.
- Sokolnikoff I. S., Sokolnikoff E. S., Higher Mathematics of Engineers and Physicists, 2nd ed., New York, MacGrow-Hill Book Co., Inc., 1941, p. 101.
- Soave, G., Chem. Eng. Sci., 27, 1972, p. 1197.
- Рид P., Праусниц Дж., Шервуд Т. Свойства газов и жидкостей: Справочное пособие- Л.: Химия, 1982.- 592 с.
- West Е. W., Erbar J. Н. An evaluation of four methods of predicting the thermodynamic properties of light hydrocarbon systems, paper presented at 52d annu. Meet. NGPA, Dallas, Tex., March 26−28, 1973.
- Холпанов Л.П., Шкадов В. Я. Гидродинамика и тепломассообмен с поверхностью раздела. — М.: Наука, 1990.
- Дьяконов С. Г., Елизаров В. И. Решение инженерных задач химической технологии с помощью ЭВМ: Учеб. пособие.- Казань: КХТИ, 1987.
- Розен А. М., Мартюшин Е. И. и др. Масштабный переход в химической технологии: разработка промышленных аппаратов методамигидродинамического моделирования.- Под ред. А. М. Розена.- М.: Химия, 1980.
- Вертузаев Е. Д. Опыт масштабного перехода при разработке промышленных массообменных аппаратов// Химическая промышленность. 1990.- № 4.- с. 223−227.
- Расчеты основных процессов и аппаратов нефтепереработки: Справочник/ Рабинович Г. Г., Рябых П. М., Хохряков П. А. и др.- Под ред. Е. Н. Судакова.- М.: Химия. 1979.-568 с.
- Джон Г. Перри. Справочник инженера-химика, т. 2, Л.: Химия, 1969. с. 504.
- Drickamer H. G., Bradford J. R., Trans. Am. Ind. Chem. Eng., 39, 319, 1943.
- O’Connell H. E., Trans. Am. Inst. Chem. Eng., 42, 741, 1946.
- In Chin Chu e. a. J. Appl. Chem., 1951, v. 1, № 12, p. 529−531.
- Ясавеев Х.Н., Баглай В. Ф., Солодов П. А., Лаптев А. Г., Минеев Н. Г. Вариант реконструкции установки получения моторных топлив// Межвуз. сб. науч. тр., «Массообменные процессы и аппараты химической технологии», Казань: КГТУ, 1998.
- Ernest Е. Ludwig. Design for Chemical and Petrochemical Plants. Vol. 2. Gulf Publishing Co. 1989,310 p.- 146 144. Гленсдорф П., Пригожин И. Термодинамическая теория структуры, устойчивости и флуктуаций. М.: Мир, 1975.
- Шехтер Р. Вариационный метод в инженерных расчетах. М.: Мир, 1971.
- Ясавеев Х.Н., Лаптев А. Г., Данилов В. А., Фарахов М. И. Вариационный метод определения ВЭТТ для насадочных колонн при проведении процесса ректификации в нефтепереработке / Деп. в ВИНИТИ № 2870-Б98. 1998.
- Дьяконов С.Г., Лаптев А. Г., Данилов В. А., Ясавеев Х. Н. Определение ВЭТТ для насадочных колонн вариационным методом // Темат. сб. науч. тр. Вестника КГТУ «Тепломассообменные процессы и аппараты химической технологии», Казань: КГТУ, 1998, с. 10−17.
- Холпанов Л.П., Мочалова Н. С. Гидродинамика и тепломассообмен в осесимметричных течениях жидкости с учетом входного гидродинамического участка // ТОХТ. 1996. — Т.ЗО. — № 1. — С.14.
- Лаптев А.Г., Данилов В. А. Математическое моделирование процесса хемосорбции в насадочных колоннах // Хим. пром-ть. 1998. — № 1. — С.23−27.
- Лаптев А.Г., Дьяконов С. Г. Математическое моделирование процессов массо- и теплоотдачи в газовой фазе насадочных колоннах // Хим. пром-ть. 1993. -№ 6. — С.48−51.
- Ясавеев Х.Н., Мальковский П. А., Дияров И. Н. Процесс получения изопентановой фракции марки, А по ТУ 38.101 494 79 по газофракционирующей установке Сургутского завода стабилизации конденсата (СЗСК) // Изв. ВУЗ -ов. Нефть и газ. — 1997. — № 6. — С. 165.
- Нефть и газ. 1998. — № 2. — С. 101 -110.
- Ясавеев Х.Н., Мальковский П. А., Дияров И. Н. Проблемы реконструкции изопентановой колонны на Сургутском заводе стабилизации конденсата (СЗСК) // Химия и технология топлив и масел. 1998. — № 6. — С.
- Фарахов М.И., Ясавеев Х. С., Мальковский П. А., Афанасьев И. П., Дьяконов Г. С., Лаптев А. Г., Минеев Н. Г., Баглай В.Ф/СвидетельствоРФ на полезную модель «Насадка для тепло-массообменных процессов: положительное решение от 25.11.98, per. № 98 119 407.
- Глитч 82 года новаторства. Glitsch. 1996.
- Bolles W. L., Fair J. R. I. Chem. E. Symp. Ser. 56., p. 3.3/35, 1979.
- Kister H. Z., Gill D. R., Chem. Eng. Prog., 87(2), p.32, 1991.