Скоростное гальваническое формование деталей из Ni-Co сплавов
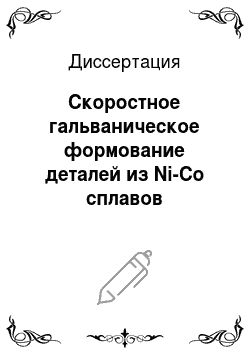
Диссертация
Технология получения матриц пресс-форм с использованием процессов электролитического катодного формования подробно изложена в работах П. М. Вячеславова, Г. А. Садакова, Г. А. Волянюк и других авторов. Этот метод применяется как в единичном, так и в крупносерийном производстве, используется для изготовления деталей сложной, в том числе уникальной формы. Для реализации процессов электролитического… Читать ещё >
Список литературы
- Абдулин B.C., Черненко В. И. Выход по току и механические свойства никеля, осаждаемого в импульсном режиме // Защита металлов. — 1982. — Т. 18. — № 6. — С.964−966.
- Антропов Л.И. Теоретическая электрохимия. М.: Высшая школа, 1975. -512 с.
- Акопян Э.М. Совместный разряд ионов при электроосаждении металлов импульсным током: Автореф. дис.канд. техн. наук. Иваново, 1970. 20 с.
- Артамонова Е.В., Левит М. Л., Цветков И. В. Применение метода электролитического катодного формования для изготовления вставок пресс-форм и других изделий из никеля и никель-кобальтового сплава. Обзор. М.: НИИМАШ, 1984. 50 с.
- Батков Г. С., Конопатова А. П., Сергеев Ю. С., Степанов В. Д. Прогрессивные методы формообразования в изготовлении деталей генераторных приборов // Электронная промышленность. 1985. — Т. 140.- № 2. -С. 76 — 79.
- Беккер М.Б., Заславский М. Л., Игнатенко Ю. Ф. и др. Литье под давлением. М: Машиностроение, 1990. -400 с.
- Белоконь В.И., Чернов Б. Б., Коварский Н. Я. Микрораспределение тока на катоде при электролизе пульсирующим током // Электрохимия. -1975.-Т.П.-№. 11.-С.1655 1659.
- Белоцерковский О.М., Давыдов Ю. М. Метод крупных частиц в газовой динамике. М.: Наука, 1982. 392 с.
- Беренфельд В.В., Бирин Б. В. Конструкционные и технологические особенности при изготовлении формообразующих деталей пресс-форм методом гальванопластики // Гальванопластика в промышленности: Матер, семинара. -МДНТП, 1976. -С. 12- 77.
- Богеншютц А.Ф., Георге У. Электролитическое покрытие сплавами. Методы анализа. М.: Металлургия, 1980.- 190 с.
- Бондарь В.В., Гринина В. В., Павлов В. Н. Электроосаждение двойных сплавов // Итоги науки и техники. Электрохимия. М.: ВИНИТИ.- 1980. -Т.16.-329 с.
- Брагинский В.А. Прессование. JL: Химия, 1979. 176 с.
- Брайман Б.М. Опыт и перспективы использования в отрасли гальванопластики для изготовления технологической оснастки //Обзор. М.: ЦНИИТЭИН легпишемаш, 1984. — 68 с.
- Бригадиров Г. В., Дунаев В. А. Численное моделирование внутрибал-листических процессов в теплоэнергетических установках.//Труды 21-го международного пиротехнического семинара. М.: АНРФД995. -С.88−96.
- Ваграмян А.Т., Жамагорцянц М. А. Электроосаждение металлов и ин-гибирующая адсорбция. М.: Наука, 1969. 199 с.
- Вансовская K.M., Волянюк Г. А. Промышленная гальванопластика. Л.: Машиностроение, 1986.-195 с.
- Вашуль X. Практическая металлография. Методы изготовления образцов. М.: Металлургия, 1988. 319 с.
- Волгин В.М. Модели эволюции обрабатываемой поверхности при ЭХО // Современная электротехнология в машиностроении: Сб. тр. Всероссийской науч. -техн. конф. Тула, 1997. — С. 27−40.
- Волков Ю.С., Лившиц А. Л. Введение в теорию размерного формообразования электрофизико-химическими методами. Киев: Вища школа, 1978.- 120 с.
- Волков Ю.С., Мороз И. И. Решение простейших стационарных задач электрохимической обработки металлов // Электронная обработка материалов. 1966. — №.4. С. 67 — 73.
- Вячеславов П.М. Новые электрохимические покрытия. Л.: Лениздат, 1972.-264 с.
- Вячеславов П.М., Волянюк Г. А. Электролитическое формование. Л.: Машиностроение, 1979.-198 с.
- Вячеславов П.М., Шмелева. Н. М. Методы испытаний электролитических покрытий. Л.: Машиностроение, 1977. 88 с.
- Гальванопластика в промышленности. М.: МДНТП, 1976. 148 с.
- Гальванопластика в промышленности. М.: МДНТП, 1979.-136 с.
- Гальванопластика в промышленности. М.: МДНТП, 1981.-118 с.
- Гальванопластика в промышленности. М.: МДНТП, 1985.- 148 с.
- Гамбург Ю.Д., Полукаров Ю. М. // Всесоюзн. конф. по электрохимии: Тез. докл. М.: 1982. Т.1. — С. 206.
- Геллер Ю.А. Инструментальные стали. М.: Металлургия, 1975.- 176 с.
- Герасименко A.A., Слотин Ю. С. О критерии равномерности распределения тока и металла по поверхности катода //Электрохимия. 1975. -№ 1. — С.110−111.
- Головчанская Р.Г., Свирщевская Г. Г., Коротаева Е. В., Хо Куанг Лам. Электроосаждение сплава железо-никель для изготовления гальванопластических копий и пресс-форм // Гальванотехника и обработка поверхности. 1993. — Т.2. — № 9. — С.46 — 49.
- Горюнов И.И. Пресс-формы для литья под давлением. Справочное пособие. Л. Машиностроение, 1973.-256 с.
- Гудин Н.В., Гильманшин Г. Г., Ярхунов В. Л. Определение выхода металла по току при нестационарных режимах осаждения // Защита металлов. 1985. — Т.21. — № 6. — С.970.
- Гурович Р.И., Кривцов А. К. Исследование кинетики разряда никеля при поляризации пульсирующими токами // Электрохимия. 1971. -№ 10.-С.1435 — 1439.
- Давыдов А.Д. Об измерениях потенциалов при исследовании процессов электрохимического растворения металлов с высокими плотностями тока // Электронная обработка материалов. 1975. — № 2. — С. 19 -23.
- Давыдов А.Д., Энгельгард Г. Р., Малофеева А. Н. и др. Скорость катодного выделения и анодного растворения металлов при больших градиентах концентрации раствора в диффузионном слое // Электрохимия. -1979.-Т15.-С. 1029- 1033.
- Давыдов А.Д., Козак Е. Высокоскоростное электрохимическое формообразование. М.: Наука, 1990. 272 с.
- Дамаскин Б. Б, Петрий O.A. Введение в электрохимическую кинетику. М.: Высшая школа, 1980. 400 с.
- Дамаскин Б.Б. Принципы современных методов изучения электрохимических реакций. М.: Изд-во Московского университета, 1965. 103 с.
- Деванатхан М.А., Гурусвами В. Исследование массопереноса в проточных электролитах. 1. Режим ламинарного течения. // Электрохимия. 1971.-Т.7.-№. 9.-С. 1175 — 1178.
- Деванатхан М.А., Гурусвами В. Исследование массопереноса в проточных электролитах. 2. Режим турбулентного течения. // Электрохимия. 1971. — Т.7. -№. 10. — 1203 — 1207.
- Делахей П. Новые приборы и методы в электрохимии. М.: Изд-во иностр. лит., 1959. 351 с.
- Дикусар А.И., Энгельгард Г. Р., Петренко В. И., Петров Ю. Н. Электродные процессы и процессы переноса при электрохимической размерной обработке металлов. Кишинев: Штиинца, 1983. 207 с.
- Дунаев В.А. Математическое моделирование течения вязкого теплопроводного газа в каналах сложной формы.//Конверсия, наука и образование: Тез. докл. международного конгресса Тула, 1993. — С.27.
- Дьяконов В.П. Справочник по алгоритмам и программам на языке БЕЙСИК для персональных ЭВМ: Справочник М.: Наука, 1987. -240с.
- Жамагорцянц М.А. К вопросу о влиянии величины рН раствора на процесс электроосаждения металлов группы железа в интервале температур 25 175 °С // Электрохимия. — 1980. — Т. 14. — № 1. — С. 34 — 38.
- Жамагорцянц М.А. О диффузионных ограничениях процесса электроосаждения никеля при высоких температурах // Электрохимия. 1975. — Т.9. — №.1. — С.78 — 93.
- Заблудовский В.А. Влияние импульсного тока на текстуру и свойства никелевых покрытий // Защита металлов. 1983. — Т.19. — № 5. — С.724 -728.
- Захидов Р.А. Применение струйной гальванопластики для получения гелиотехнических поверхностей. // Гальванопластика в промышленности. М.: МДНТП, — 1976. — С.143 — 145.
- Зенкевич О., Чанг И. Метод конечных элементов в теории сооружений и в механике сплошных сред. М.: Недра, 1974. 240 с.
- Иванов В.Т. Расчеты электрических полей в многоэлектродных электрохимических системах с биполярыми электродами// Электрохимия 1974- Т. 10.-№ 11.-С. 1657- 1662.
- Иванов В.Т., Гусев В. Г., Фокин А. Н. Оптимизация электрических полей, контроль и автоматизация гальванообработки. М.: Машиностроение, 1986.-211 с.
- Казначей Б.Я. Гальванопластика в промышленности. М.: Росгизмест-пром, 1955. 174 с.
- Казначей Б.Я. Гальванотехника в механической и магнитной записи электрических сигналов. М., 1964. 78 с.
- Калинчев Э.Л., Калинчева Е. И., Саковцева М. Б. Оборудование для литья пластмасс под давлением: Расчет и конструирование. М.: Машиностроение, 1985. — 256 с.
- Костин H.A. Влияние частоты импульсного тока на скорость осаждения, структуру и некоторые свойства осадков // Электрохимия. 1985. — Т.21. — № 4. — С.444 — 449.
- Костин H.A., Кравцов А. К., Абдулин B.C., Заблудовский B.C. О механизме блескообразования никелевых покрытий на импульсном токе // Электрохимия. 1982. — Т.8 — № 2. — С. 21 — 214.
- Костин H.A., Кублановский B.C., Заблудовский А.В Импульсный электролиз. Киев: Наук, думка, 1989.- 168 с.
- Костин H.A., Лабяк О. В. Математическое моделирование процессов импульсного осаждения сплавов // Электрохимия, 1995. Т.31.- № 5. -С. 510−516.
- Крылов B.C., Давыдов А. Д., Козак Е. Проблемы теории электрохимического формообразования и точности размерной электрохимической обработки//Электрохимия. 1975. — Т.11. — N.8. — С.1155 — 1179.
- Кудрявцев Н.Т. Электролитические покрытия металлами. М.: Химия, 1979. — 352 с.
- Кузнецов Д.П., Лясников A.B., Кудрявцев В. А. Технология формообразования холодным выдавливанием полостей деталей пресс-форм и штампов. М.: Машиностроение, 1975. 112 с.
- Лайнер В.И. Защитные покрытия металлов. М.: Металлургия, 1974. -559 с.
- Левич В.Г. Физико-химическая гидродинамика. М., 1952. — 538 с.
- Лобанов С.А. Практические советы гальванику. Л.: Машиностроение, Ленингр. отд-ние. 1983. 248 с.
- Лойцянский Л.Г. Механика жидкости и газа. М.: Наука, 1957. 840 с.
- Любимов В.В. Аддитивное формообразование // Электрофизические и электрохимические методы обработки материалов 1989. — С.5 — 12.
- Любимов В.В., Сундуков В. К., Новосёлов A.M. Скоростное электрохимическое формирование медных осадков // Электрохим. и электро-физ. методы обработки материалов. Тула, ТПИ, 1984. — С.27 — 33.
- Маки Я. Изготовление пресс-форм при помощи гальванопластики. Кикай то когу, 1975. Т. 19. — № 10. — С.115 — 120. МФ Пер.77/25 882.
- Мендельсон B.C., Рудман Л. И. Технология изготовления штампов и пресс-форм. М.: Машиностроение, 1982.-207 с.
- Мирзоев P.A., Давыдов А. Д. Влияние электродных процессов на некоторые технологические характеристики электрохимической размерной обработки // Электрофизические и электрохимические методы обработки. 1972. — N.9. — С.9 — 12.
- Мороз И. И, Алексеев Г. А., Водяницкий O.A. и др. Электрохимическая обработка металлов. М.: Машиностроение, 1969. 209 с.
- Мороз И.И. Электрохимическое формообразование, технология и оборудование. Обзор. М.: НИИМаш, 1978, — 79 с.
- Московиц М. Селективное электроосаждение покрытий натиранием //Гальванотехника и обработка поверхности. М.: 1993. Т.2. — № 9. -С.40 — 45.
- Никитенко Н.И. Исследование нестационарных процессов тепло- и массопереноса методом сеток. Киев: Наук, думка, 1971. 264 с.
- Ньюмен Дж. Электрохимические системы. М.: Мир, 1977.
- Оборудование для размерной электрохимической обработки деталей машин / Под ред. Ф.в. Седыкина. М.: Машиностроение, 1980. — 227 с.
- Озеров А.К., Кривцов А. К., Халиев В. А. и др. Нестационарный элекVтролиз. Волгоград, 1972. — 160 с.
- Палей М.М. Технология производства приспособлений, пресс-форм и штампов. М.: Машиностроение, 1979. — 293 с.
- Панченко И.И. Электролитическое осаждение сплавов: Конспект доклада. М.: МДНТП, 1959. — 20 с.
- Пат. 2 501 730 Франции. МКИ С25Д 5/04. Способ и устройство для электроосаждения сканирующим электродом. Опубл. 1982. БИ№ 8.
- Пат. 12 823, 12 824 Японии. /Иноуэ Киеси/, Кл.12А, 230. Изготовление медных электродов. Опубл. 1965.
- Пегловский В.Л., Костенко В. Д. Изготовление пресс-форм для пластмасс методом гальванопластики. Киев, 1969. 42 с.
- Переработка пластмасс / Спр. пособие под ред. В. А. Брагинского. Л.: Химия, 1985.-295 с.
- Попилов Л .Я. Гальванопластика. М. Л.: Машгиз, 1961. — 64 с.
- Полукаров Ю.М., Гринина В. В. Электроосаждение металлов с использованием периодических токов и одиночных импульсов // Итоги науки и техники. Сер. Электрохимия. 1985. — № 22 — С. 3 — 62.
- Поветкин В.В., Ковенский И. М., Устинщиков Ю. И. Структура и свойства электролитических сплавов М., Наука, 1992. 255 с.
- Рыбалко A.B.,. Дикусар А. И. Электрохимическая обработка импульсами микросекундного диапазона // Электрохимия, 1994. Т.ЗО. — № 4.-С.490 — 498.
- Садаков Г. А. Гальванопластика. М.: Машиностроение, 1987. 296 с.
- Садаков Г. А., Семенчук Р. В., Филимонов Ю. А. Технология гальванопластики: Справочное пособие. М.: Машиностроение, 1979.-160 с.
- Самарский A.A. Теория разностных схем М.: Наука, 1977. 656 с.
- Седыкин Ф.В. Размерная электрохимическая обработка деталей машин. М.: Машиностроение, 1978. — 176 с.
- Седыкин Ф.В., Дмитриев Л. Б., Иванов Н. И., Тимофеев Ю. С., Шляков В. Г. Оборудование для размерной электрохимической обработки деталей машин. М.: Машиностроение, 1980. 277 с.
- Серянов Ю.В., Аравина Л. В. Кинетика лазерно-стимулированного электроосаждения никеля на плоскую, цилиндрическую и сферическую поверхность меди. // Защита металлов, 1993. Т.29. — № 3. — С.521 -522.
- Скоминас В.Ю. Функциональные металлопокрытия в современной гальванотехнике // Гальванотехника и обработка поверхности. М.: 1993. Т. 2. — № 3. — С.22 — 25.
- Федосеева Т.А., Ваграмян А. Т. Электроосаждение железо-никелевого сплава импульсным током. // Электрохимия. 1972. — Т.8. — №.6. — С. 835 — 839.
- Федотов В.Е. Электроэрозионный способ обработки деталей технологической оснастки. Фрунзе, 1977. 68 с.
- ЮО.Федотьев Н. П., Бибиков H.H., Вячеславов П. М., Грилихес С. Я. Электролитические сплавы. М.: Машгиз, 1962. 312 с.
- Фотеев Н.К. Технология электроэрозионной обработки. М.: Машиностроение, 1980. 184 с.
- Хыбымяги А.И. Холодное выдавливание рельефных поверхностей технологической оснастки. М.: Машиностроение, 1981.- 79 с.
- Ahlhorn J., Lewisch I., Kreye H. // Galvanotechnik. 1992. — T.83. — № 11. -P.3712.
- Belt K.C., Grossley J.A., Watson S.A. // Trans. Insn. Metal Finish. 1970. -T.48. — №.4. — P. 133 — 138.
- Safranek W.H. // Plating and Surface Finishing. 1982. — №.69. — N.4. — P. 26−30.
- Schwabe H.U. // Industrie Anzeiger. — 1973. — T.95. — №.34. — P.703 — 706.
- Watson F.A., Worn D.K.//Met. and Meter Technol. 1981. — T. 13. — № 6. -P.46 — 50.
- Wearmmouth W.R.//Metalloberflache. 1977. — T.31. — № 11. — P. 89 — 94.
- Кошссии были представлеш на рассмотрение лабораторное .•¦. экспериментальное оборудование, результаты всследовакий, а заключительный отчет по теме # 46 106″
- Определены параметра процесса скоростной гальванопластики, позволяющие получать осадки с минимальными внутренними напряжениями.2. Выв о д, а ' 2Л. Содержание научно-технической продукции соответствует заданию согласно хоздэиовору 'й 46 106.
- Научно-техническая разработка выполнена на высоком научно-техническом уровне в установленные календарным планом сроки.
- Представленную научно-техническую продукцию считать принятой без замечаний.
- Договорная цена разработок, выполненных за прошедший период с I января 1991 г. по 31 декабря 1991 г., составляет 80 000 руб.
- Результаты’исследований вкедшть в серийное производство. ЦКБА.
- От ТуяПН Доцент каф. ШиА, к.т.н.к. Сундуков
- Акт выдан без предъявления финансовых претензий.
- Научный руководитель Главным Teß-i^jiorтемы 46 305 / уу! В. К. Сундуков АО ЦКБА. Булычев1. Научных сотрудник' /твах.1. ЛБЕРЛЩАЮ реактор АО ЦКВА1. Ю. Г. Нечепуренко2. 1994 г.1. АКТс внедрений результатов научно-исследовательской работы
- Акт выдан без предъявления финансовых претензии.
- Научный руководитель «-------- —-----—17 Оthe interrational congress .
- ВЫСОКОСКОРОСТНОЕ ГАЛЬВАНИЧЕСКОЕ- ОСАЖДЕНИЕ МЕТАЛЛОВ1. И СПЛАВОВ ¦
- Технология предназначена для получения сложнопрофильных формообразующих вставок пресс-форм для литья и прессования изделий из пластмасс, резины и стекла.
- Для реализации процесса разработано и изготовлено оригинальное оборудование: импульсный источник технологического тока: электролизер- центробежный насос из неметаллических материалов.
- Управление параметрами импульсного тока в ходе, электролиза позволяет получать осадки с заданными физико-механическими и геометрическими характеристиками.
- Внедрение технологии скоростного гальванического осаждения сплава никель-кобальт позволяет повысить производительность изготовления пресс-форм в 5. 10 раз по сравнению с существующими технологиями изготовления пресс-форм методом гальванопластики.
- ДСВ-2.Р- Ш марш О (ГОСТ 17 476 72) или ДГ-4 В (ГОСТ0437−89) изделия АТТ 01 в пресс-Форш АЕЩ 1335−4.153 й Ш’М 777 325 003 СБЛ’Ю-1 йзделш! G&-93.
- Игл/ниий пжгпппич>& пт, Т1 л ':<.» :г:г! -рдипглвлг