Сварка трением.
Технология сварочных работ
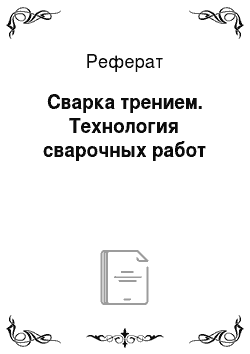
Вибрационная сварка — это сварка трением некруглых заготовок, при выполнении которой вместо вращения осуществляется возвратно-поступательное движение торца одной из свариваемых заготовок относительно другой. В процессе такого движения (с частотой около 60 Гц и амплитудой до 3 мм) торцы заготовок сжимаются до образования плотного контакта. При сварке вязкопластичные слои металлов заготовок… Читать ещё >
Сварка трением. Технология сварочных работ (реферат, курсовая, диплом, контрольная)
Сварка трением производится с применением давления, а нагрев осуществляется трением, вызываемым относительным перемещением свариваемых частей и инструмента.
Наиболее распространенной разновидностью сварки трением является ротационная сварка. Ее схема приведена на рис. 5.7. Две заготовки, подлежащие сварке, устанавливают соосно в зажимах машины. Одна из них неподвижна, а другая приводится во вращение вокруг их общей оси. На сопряженных торцовых поверхностях деталей, прижатых одна к другой осевым усилием Р, возникают силы трения.
Работа, затрачиваемая при вращении свариваемых заготовок относительно друг друга на преодоление сил трения, преобразуется в теплоту, которая выделяется на поверхностях трения и нагревает прилегающие к ним тонкие слои металла до температур, необходимых для образования сварного соединения (при сварке черных металлов температура в стыке достигает 1 000… 1 300°С). Таким образом, в стыке действует внутренний источник тепловой энергии, вызывающий быстрый локальный нагрев небольших объемов металла.

При трении пластичный металл стыка выдавливается в радиальных направлениях под воздействием осевого усилия и тангенциальных сил, возникающих в стыке при Рис. 5.7. Схема ротационной сварки трением: Р — осевое усилие вращении одной детали относительно другой. Выдавленный металл — грат — имеет характерную для сварки трением форму двух правильных колец, расположенных по обе стороны плоскости стыка.
При выдавливании пластичного металла из стыка в радиальных направлениях хрупкие оксидные пленки, покрывавшие торцовые поверхности соединяемых заготовок до начала сварки, разрушаются, а их обломки, продукты сгорания адсорбированных жировых пленок и другие инородные включения вместе с металлом удаляются из стыка в грат.
Нагрев прекращается путем быстрого (почти мгновенного) прекращения относительного движения заготовок. При этом в контакте находятся очищенные торцовые поверхности соединяемых деталей, металл которых достиг состояния повышенной пластичности. Для получения прочного соединения такой подготовленный к сварке металл достаточно подвергнуть сильному сжатию — проковать. Это достигается благодаря действию в течение еще некоторого времени осевого усилия.
Прочность образующегося сварного соединения непосредственно связана с величиной пластической деформации торцов свариваемых деталей и режимом проковки.
В свою очередь, степень пластической деформации и геометрические параметры зоны сварки зависят от количества теплоты и характера ее выделения при трении, теплопроводности материалов заготовок, распределения давления в контакте (с учетом изменения механических свойств материалов при нагреве) и длительности цикла сварки.
Тепловая мощность, выделяемая в кольцевом сечении шириной dr,.

где/ — коэффициент трения; р — нормальное давление в области контакта; п — частота вращения заготовки; г — внутренний радиус кольцевого сечения.
Суммарная мощность.
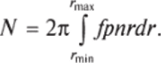
На периферии стыка нагрев металла более значителен, чем в зоне оси вращения. При сварке пластичных материалов происходит перераспределение давления. Оно концентрируется в центральной зоне (там, где линейная скорость и нагрев материала меньше). Обычно линейная скорость составляет 10…25 м/с. При скоростях менее 10 м/с необходимо увеличивать давление, что может привести к деформации заготовок. При сварке сталей рскомендуются следующие технологические давления: в фазе нагрева — 0,6 МПа, на стадии проковки — 1,5 МПа.
При нагреве происходит притирка поверхностей заготовок, удаляются оксидные пленки и загрязнения, что сопровождается уменьшением обшей длины изделия, но сравнению с суммарной длиной заготовок. После проковки общая длина изделия сокращается еще в большей степени. Если необходимо обеспечить точный осевой размер свариваемого изделия, то производят контроль изменения длины заготовок в процессе сварки. Управление процессом сварки на современных станках осуществляется с учетом данных о скорости изменения длины заготовок при нагреве и проковке.
К энергетическим и технологическим преимуществам сварки трением относятся:
- • высокий КПД процесса вследствие локального генерирования теплоты и малого объема нагреваемого металла;
- • более низкий (в 5 — 10 раз) расход энергии, чем при контактной стыковой сварке;
- • высокая производительность процесса (в зависимости от вида материала и размеров сечения заготовок продолжительность цикла их нагрева составляет 2…30 с);
- • при правильно выбранном режиме сварки наличие у металла сварного шва и прилегающих к нему зон таких же показателей прочности и пластичности, как у материала заготовок;
- • измельченная структура металла шва и зоны термического влияния в результате быстрого нагрева и охлаждения сварного шва при больших давлениях;
- • отсутствие зависимости качества сварного шва от чистоты поверхности торцов свариваемых заготовок;
- • возможность сварки как одноименных, так и разноименных металлов (например, алюминия со сталью, меди со сталью, титана с алюминием, меди с алюминием);
- • простота механизации и автоматизации процесса сварки (основные технологические параметры процесса легко программируются).
К недостаткам сварки трением можно отнести то, что она не является универсальным процессом. С ее помощью могут осуществляться соединения лишь таких заготовок, из которых хотя бы одна является телом вращения (круглый стержень или труба), ось которого совпадает с осью вращения. Другая заготовка может быть произвольной формы, но должна иметь плоскую поверхность, к которой приваривается первая заготовка. Этот недостаток, однако, несущественно ограничивает применимость сварки трением; так как в машиностроении число деталей круглого сечения составляет 50… 70% общего числа свариваемых деталей.
Из-за применения громоздкого оборудования процесс сварки не может быть мобильным. Он осуществим лишь при условии подачи заготовок, подлежащих сварке, к машине (сварка малых заготовок с массивными конструкциями при помощи переносных машин исключается).
Волокна текстуры проката вблизи стыка расположены радиально, выходят на наружную (боковую) поверхность готовой детали и изгибаются в направлении вращения заготовки. В деталях, противостоящих динамическим нагрузкам, стык с таким расположением волокон может оказаться очагом усталостного разрушения, а в деталях, работающих в агрессивных средах, — очагом коррозии.
Лучший способ предотвращения указанных дефектов — сохранение на детали грата. Однако необходимо снимать грат, когда его наличие по конструктивным соображениям недопустимо. На это затрачивается дополнительное время либо на сварочной машине, либо на отдельном рабочем месте.
Сварка трением широко применяется в автомобилестроении (изготовление деталей рулевого управления, карданных валов легковых и грузовых автомобилей, полуосей, картеров задних мостов, клапанов двигателей внутреннего сгорания, цилиндров гидравлических систем и др.), тракторостроении (производство деталей рулевого управления, планетарных передач, валов отбора мощности, катков, траков, роторов турбонагнетателей дизелей и др.), электропромышленности (создание деталей высоковольтной аппаратуры, выводов бумажно-масляных конденсаторов, кислотных аккумуляторов, анодов игнитронов, поршней пневматических цилиндров сварочных машин и др.) и инструментальном массовом производстве (изготовление концевого режущего инструмента — фрез, сверл, метчиков).
В принципе, сварку трением можно вести на любом металлорежущем станке (токарный, фрезерный, расточный, сверлильный и др.), имеющем на вращающемся шпинделе патрон для закрепления одной из свариваемых деталей и место для установки второй детали. Однако использование универсальных металлорежущих станков дтя сварки трением приводит к их быстрому изнашиванию. Универсальные станки не рассчитаны на режимы, свойственные сварке трением: выходят из строя подшипниковые группы станков, ломаются станины.
В серийном производстве сварку трением осуществляют с применением специальных машин, снабженных силовым (обычно гидравлическим) механизмом прижима заготовок и электромагнитным тормозом шпинделей, установленных в подшипниках повышенной мощности.
Различают несколько видов сварки трением.
Инерционная сварка отличается от обычного способа сварки трением лишь тем, что потребляемая из сети электроэнергия, преобразованная электродвигателем в механическую энергию, предварительно (в промежутки времени между циклами сварки) аккумулируется в маховике машины.
Процесс инерционной сварки начинается с того, что с помощью электродвигателя приводится во вращение маховик машины. Когда угловая скорость (т.е. накопленная энергия) достигает достаточной для сварки заготовок величины, маховик отключается от приводного двигателя и подсоединяется к шпинделю, на котором укреплена одна из заготовок. Если заготовки предварительно были прижаты осевым усилием одна к другой, то в стыке начинается процесс тепловыделения.
Продолжительность нагрева при инерционной сварке в несколько раз меньше, чем при обычной сварке трением. Кратковременный цикл нагрева — охлаждения позволяет с помощью инерционной сварки соединять такие разнородные материалы, как титан и алюминий, а также другие сочетания металлов, что при обычной сварке трением в ряде случаев невыполнимо. Однако при сварке, например, быстрорежущих сталей, склонных к образованию закалочных структур, с конструкционными быстротечность термического цикла приводит к образованию закалочных трещин.
Орбитальная сварка (рис. 5.8, а) отличается от обычного способа сварки трением тем, что позволяет осуществлять соединение заготовок не только с круглой, но и с любой произвольной формой сечения.
На начальном этапе заготовки устанавливают соосно и сообщают им вращательное движение с одинаковой угловой скоростью и одинаковым направлением вращения. Из-за отсутствия перемещения заготовок относительно друг друга сила трения между ними не возникает.
Если одну из заготовок сместить в радиальном направлении относительно другой, то в стыке возникнет трение и начнется тепловыделение. Процесс тепловыделения завершается принудительным совмещением осей вращающихся заготовок. Во время торможения обеих заготовок к их торцам прикладывается проковочное давление. К моменту остановки заготовок они оказываются сваренными.
Сварка двух заготовок с помощью третьего тела применяется для соединения длинных (или коротких, но массивных) заготовок. Во время сварки (рис. 5.8, б) они остаются неподвижными. Во вращение приводится только зажатое между ними тело (вставка). В качестве вставки может быть использован тонкий диск большего диаметра, чем у свариваемых заготовок, или относительно длинная в осевом направлении вставка, диаметр которой может быть таким же, как у соединяемых заготовок.
Одновременная сварка трех заготовок позволяет повысить производительность процесса. Средняя заготовка при сварке остается.
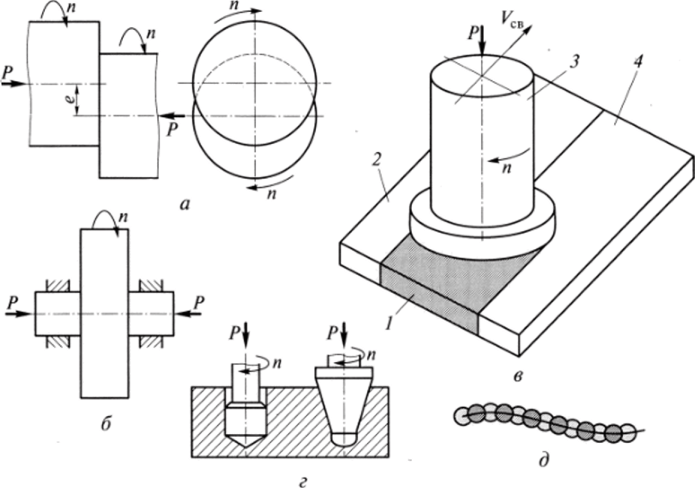
Рис. 5.8. Основные схемы сварки трением:
а — орбитальная; б — двух заготовок с помощью третьего тела; в — перемешивающая; г — штифтовая; д — внешний вид сваренной трещины; / — сварной шов; 2, 4 — заготовки; 3 — инструмент; Р — усилие прижима; п — частота вращения заготовок; Усш — скорость сварки; е — эксцентриситет неподвижной, а крайним сообщается вращение с помощью двух независимых шпинделей.
Вибрационная сварка — это сварка трением некруглых заготовок, при выполнении которой вместо вращения осуществляется возвратно-поступательное движение торца одной из свариваемых заготовок относительно другой. В процессе такого движения (с частотой около 60 Гц и амплитудой до 3 мм) торцы заготовок сжимаются до образования плотного контакта. При сварке вязкопластичные слои металлов заготовок перемещаются к границам свариваемой поверхности. При этом удаляются оксиды и загрязнения. Малая длительность процесса (до 20 с) обеспечивает минимальную зону термического влияния по сравнению с другими методами стыковой сварки.
Сварка целого или полого стержня с диском или пластиной является разновидностью ротационной сварки.
Перемешивающая сварка трением (ПСТ) выполняется торцом вращающегося инструмента J (pnc. 5.8, в), который перемещается в направлении сварки. Диаметр инструмента немного меньше глубины сварки. Пластифицированные тепловыделением металлы заготовок 2 и 4 за счет действия сил трения перемешиваются в процессе формирования сварного шва /. Деформация и перемешивание металлов заготовок в твердой фазе обеспечивают более прочную микроструктуру, чем у основного материала. Сварка может производиться в любом пространственном положении по любой заданной траектории. ПСТ используется для соединения листовых, цилиндрических и трубчатых заготовок толщиной.
1,6…30 мм из стали и сплавов цветных металлов.
Штифтовая сварка трением (рис. 5.8, г) осуществляется под водой для соединения конструкций, которые трудно сваривать обычным способом, а также в ремонтном производстве при устранении трещин. Предварительно сверлят отверстие, в которое вставляют цилиндрический или конический штифт из того же материала, что и материал свариваемых заготовок. Сварка начинается с момента касания штифта дна отверстия. В результате нагрева и пластической деформации поверхность трения перемещается вверх по отверстию, пока пластифицированный металл не заполнит его полностью. Длительность сварки составляет 5… 20 с. Далее сверлят новое отверстие (рис. 5.8, д), и процесс повторяют.