Развитие пористости при гомогенизации
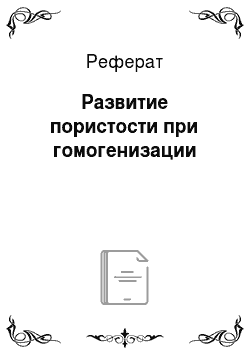
Режим гомогенизации перед закалкой, во-первых, определяет легированность твердого раствора (через полноту растворения неравновесных избыточных фаз), во-вторых, разные температуры и длительность выдержки перед закалкой приводят в промышленных сплавах к образованию разных по размерам и характеру распределения вторичных выделений алюминидов переходных металлов, на которых при старении, как… Читать ещё >
Развитие пористости при гомогенизации (реферат, курсовая, диплом, контрольная)
Еще один процесс, идущий при гомогенизационном отжиге (нагреве под закалку) литых сплавов, — это развитие пор (возникновение новых, рост этих новых и старых пор, образовавшихся при кристаллизации). Новые поры образуются на месте и вблизи растворяющихся включений избыточных фаз из-за разницы их удельного объема с матрицей и эффекта Киркендала. Рост пор при высокотемпературном отжиге происходит за счет стока вакансий.
Особенно сильно увеличивается пористость при высокотемпературной гомогенизации выше неравновесного солидуса (рис. 3.15). Предполагается, что в результате оплавления неравновесных эвтектик водород из пересыщенного (А1) диффундирует в эти микрообъемы расплава. После их рассасывания при отжиге остаются поры, заполненные газом под большим давлением. Отсюда боязнь высокотемпературной гомогенизации, связанной с частичным оплавлением отливки или слитка. Предотвратить такое оплавление можно путем медленного или ступенчатого нагрева, во время которого наиболее легкоплавкие составляющие успевают раствориться в (А1) еще при температурах ниже неравновесного солидуса.
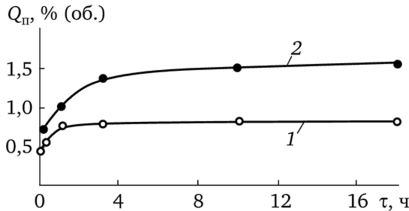
Рис. 3.15. Зависимость объемной доли пор Qn в слитке сплава Д16 от времени гомогенизации при 490 (7) и 515 °C (2).
Способы полного предотвращения развития вторичной пористости при гомогенизации пока не разработаны. Почти полного устранения пористости в отливках можно добиться отжигом в газостатах в условиях всестороннего газового давления, обеспечивающего «заварку» пор за счет пластической деформации микрообъемов сплава, окружающих несплошности. Однако для алюминиевых сплавов этот дорогостоящий способ применяется пока редко.
Старение после литья и закалки
Во время изотермической выдержки (гомогенизации) перед закалкой в (А1) активно идут процессы его распада с образованием вторичных выделений алюминидов переходных металлов. В слитках деформируемых сплавов, которые относительно медленно охлаждаются после гомогенизационного отжига, происходит частичный распад (А1) с выделением фаз, образуемых основными легирующими элементами, — подобно распаду в отливках по окончании кристаллизации.
Однако в фасонных отливках, которые после гомогенизации закаливают, этот распад обычно не идет. Большинство литейных алюминиевых сплавов после закалки, а иногда и без нее подвергают искусственному старению, в некоторых из них старение идет при комнатной температуре.
Отливки из алюминиевых сплавов подвергают старению в ряде случаев сразу после литья (режимы Т1 — Т2), а в основном — после закалки (режимы Т5 — Т7). Поэтому исходная (перед старением) структура может быть литой или полученной после гомогенизации и закалки.
Влияние литой структуры на распад алюминиевого твердого раствора с образованием основных фаз-упрочнителей при старении должно определяться в первую очередь характеристиками их внутрикристаллитной ликвации и субструктурой дендритных ячеек.
Общее количество выделений, их размеры и межчастичное расстояние, а также фазовый состав продуктов распада в отливке зависят от среднего состава алюминиевого раствора Cg перед старением. Средний состав в определенном сплаве есть функция объемной доли неравновесного избытка фаз кристаллизационного происхождения и вторичных выделений, образованных основными легирующими элементами. Следовательно, Cg определяется на практике скоростью охлаждения при кристаллизации и ниже солидуса. Кроме того, Cg зависит от состава сплава.
Чем больше легированность алюминиевого раствора, тем при оптимальном режиме старения дисперснее продукты распада, больше их число, меньше межчастичное расстояние и в результате выше должны быть прочностные свойства после старения. В общем случае при неоптимальном режиме старения (здесь имеется в виду режим, не обеспечивающий максимальную прочность) можно говорить лишь о том, что чем выше Cg, тем больше полнота распада алюминиевого раствора — больше объемная доля образующихся выделений. При этом они могут, например при перестаривании, быть и более грубыми, чем в отливках с меньшим Cg.
Из-за внутрикристаллитной ликвации легирующих элементов распределение продуктов распада после старения литых сплавов весьма неоднородно по сечению дендритных ячеек: полного распада всегда больше на их периферии, обогащенной основными легирующими элементами (Си, Mg, Zn, Si). Разная легированность алюминиевого раствора в середине и на периферии дендритных ячеек может при определенных режимах старения приводить к образованию разных по структуре выделений.
Дислокационная структура литых сплавов относительно слабо влияет на картину распада алюминиевого раствора при практически используемых режимах старения. Это объясняется гомогенностью зарождения частиц при низкотемпературном старении, а также относительно небольшой разницей характеристик дислокационной структуры разных по составу литых сплавов и разных отливок из сплава одного состава. Однако в ряде случаев, когда сравниваются сплавы, имеющие после литья существенно различающиеся дислокационные структуры, эффект упрочнения в результате старения заметно выше в сплавах с большей исходной плотностью дислокаций и субзеренной структурой.
Различия в структуре закаленных отливок, которые способны повлиять на картину распада алюминиевого раствора при последующем старении, могут быть обусловлены температурновременными режимами изотермической выдержки перед закалкой и разницей в исходной литой структуре.
Режим гомогенизации перед закалкой, во-первых, определяет легированность твердого раствора (через полноту растворения неравновесных избыточных фаз), во-вторых, разные температуры и длительность выдержки перед закалкой приводят в промышленных сплавах к образованию разных по размерам и характеру распределения вторичных выделений алюминидов переходных металлов, на которых при старении, как и во время медленного охлаждения гомогенизированных слитков, зарождаются частицы основных фаз-упрочнителей.
Устойчивость твердого раствора снижается тем эффективнее, чем дисперснее вторичные интерметаллиды. Переходные металлы, находящиеся в твердом растворе, также существенно снижают устойчивость твердого раствора, что необходимо учитывать при анализе старения как по режимам Т5 — Т7, так и по режимам Т1 — Т2 (в литом состоянии продукты распада алюминиевого раствора с образованием вторичных алюминидов переходных металлов обычно не наблюдаются).
Дисперсность большей части продуктов старения слабо зависит от размеров и распределения частиц вторичных алюминидов переходных металлов. Только непосредственно на этих частицах образуются более грубые выделения, а вокруг них — зоны, свободные от выделений.
В результате в сплавах с большим количеством относительно дисперсных частиц алюминидов переходных металлов общее количество основных фаз-упрочнителей может быть несколько уменьшено. Однако этот эффект, по-видимому, невелик, поскольку прирост прочности при старении после закалки по разным температурно-временным режимам почти не меняется, если время выдержки больше времени растворения избыточных фаз кристаллизационного происхождения.
Вторичные выделения дисперсоидов служат местами зарождения продуктов распада не только при искусственном, но и при естественном старении на ранних стадиях распада, сопровождающихся перераспределением атомов внутри твердого раствора.
Образование этих продуктов распада, видимо, связано с возникновением определенным образом ориентированных полей упругих напряжений в матрице вблизи межфазной границы на начальных стадиях распада.
Исходная структура слитков промышленных сплавов оказывает наследственное влияние на устойчивость алюминиевого раствора при старении после гомогенизации, деформации и закалки. Это объяснено увеличением пересыщенности алюминиевого раствора переходными металлами по мере ускорения кристаллизации и соответствующим увеличением числа вторичных интерметаллидов, образующихся в основном при гомогенизации и сохраняющихся в структуре при последующей обработке вплоть до конечного старения. Таким образом, изменение скорости охлаждения при кристаллизации влияет на устойчивость алюминиевого раствора и, вероятно, на дисперсность продуктов распада аналогично влиянию режима гомогенизации перед закалкой.
В сплавах, не содержащих добавок переходных металлов, была установлена неизменность плотности продуктов распада при старении отливок с разной исходной литой структурой после закалки по единому режиму.